Introduction: DIY Powerful LED Panel - Video and Work Light
Today I am going to show you how to make a bright and cheap LED panel. I wanted a bright light for my working area, this panel comes with over 200 LEDs and I used just about 10 bucks to make it.
The panel is super bright and great to use as a video light, a grow light for plants, or whenever you need a lot of light while working!
We will be making the LED panel and 3D printing a tripod adapter. This means you have a vast amount of options for mounting the light. This also means the complete light takes virtually no space if you need to pack it. Perfect for tiny workspaces or traveling to a photo shoot.
If you like this project press the VOTE button in the upper right corner of this instructable!
Here we go!
Step 1: Parts and Tools
All right, to make this panel this is what you need:
Parts
- LED light strip$ 3.9
- These are long strips of tape with hundreds of leds on them
- LED dimmer$ 2.8
- This is optional but a nice feature. I chose a dimmer that comes with a remote.
- Power supply$ 2.2
- Needs to be 12 V where the max current supplied determines the number of LEDs you can power.
- Chose a power supply with the right plug for your area.
- DC Power Jack$ 0.8
- If your LED strip dosent come with one. Most strips have this presoldered
- Something to mount your LEDs on, this is the base of the panel $ 0.5
- I just used the lid of a small SAMLA box from IKEA
- After lightly sanding the lid I gave it a quick coat of spray paint
- Total: $ 10.2!
Tools
- Soldering iron
- Wire strippers
- Hook up wire
- Access to a 3D printer
- Definately optional, lets us make a nice tripod adapter for the LED base
Step 2: Choosing the Number of LEDs
So this is how the LED strip works. The strip is 5 meters (16.4 feet) long and has 300 LEDs. On every third LED there are markings where you can cut the strip. This tells us something about how the long strip is wired.
A regular white LED usually draws 3.3 V. On a segment of the strip, three of these LEDs are in series which means the voltage drop is aggregated in the circuit. Three LEDs that draws 3.3 V each means one segment of LEDs draws 9.9 V. The strip is powered by 12 V so that leaves 2.1 V.
If the segment only consisted of the three LEDs they would get more voltage than they dissipate. This is not good for the LEDs and can quickly damage them. This is why each segment also has a resistor in series with all three LEDs. This resistor is there to drop the remaining 2.1 V in the series junction.
So if each segment accounts for 12 V that means each of the segments are connected to each other in parallel. When circuits are connected in parallel they all get the same voltage and the current is aggregated. The current in a series connection is always the same.
A regular LED draws 20 mA in current. This means a segment, which is three LEDs and a resistor in series still will draw 20 mA. When we connect several segments in parallel, we add the current. If you cut six LEDs from the strip, you have two of these segments in parallel. Which means your total circuit still draws 12 V, but they draw 40 mA in current.
This is the basis for how the current rating of a power supply wil set the total of LEDs we can power.
Now, I did some quick math to find out how many LEDs I was going to use for this panel.
The whole roll of LED tape is 5 meters, 300 LEDs, and they draw a total of 2 Amps.
My power source could deliver 1.5 Amps which meant I could use a total of 225 LEDs. (300 LEDs / 2 A) * 1.5 A. I wanted a small safety margin so I ended up using 216 LEDs total. I also chose this number because the number of LEDs has to be divisable by three. Because you can only cut your light strip on every third LED.
These LEDs are distributed in 18 long strips with 12 LEDs on each strip. This fits nicely on my lid without too much dead space, which gives a clean and proffesional look.
Step 3: Cutting and Gluing the LEDs Onto the Base
When I knew the number of LEDs I was going to use, I started cutting all the strips. First I used a wire cutter, but I actually learned scissors are even greater for cutting the LED tape. The circuit where you cut the strip is as thin as paper, especially if you opted for the non-waterproof version. There are markings on the tape to cut it every three LEDs. These markings also indicate where we can connect the LED segment together again. There are solder pads on each side of the cutting mark.
According to my math I was going to cut 18 strips with each strip having 12 LEDs on them.
With all the LEDs ready, it is time to start gluing them to the base.
While gluing everything down the I alternated having the positive and negative poles upwards towards the top of the base. This makes it easy to connect half of the positive and negative leads with blobs of solder, which in turn means you only have to use half as many wires when you solder everything later on. Saves you a lot of wire stripping!
Step 4: Soldering
Okay, time to solder!
You need to connect all of the strips so they all share a common ground and a common positive voltage connection. When soldering all the tiny, cut LED strips and segments you want to connect the positive pole of one segment to the positive pole of another segment. The same applies for the negative poles on all the segments.
I started by connecting the ground leads. This can be done anywhere on the led strips and not only on the edges of the strips. I connected all the ground leads that were next to each other by laying down huge blobs of solder. And then I did the excat same thing for the positive leads.
After this I connected every other positive lead together, and every other ground lead to each other using short hookup wire.
And we're done soldering! This means the project is basically done. We just need a nice way to mount the panel and spread that nice light all around.
Step 5: 3D Printing an Adapter
To mount this panel on a tripod I designed and 3D-printed a real simple and really strong grip for the panel. This simply slides onto the panel and grips it firmly. Then all you have to do is screw the panel with the adapter onto whatever you have with a tripod screw, which is 1/4 inch.
This was printed with functional threads so you don't have to prepare the adapter in any way. Just remove from the printer and mount right on top a printer! To get the functional threads I printed this with a resolution of 0.1 mm and 5% infil. You can download the STL file here.
You're done! Connect the power source and the dimmer, and everything should right light up!
If you chose the LED dimmer with an RF remote I will later show you another instructable on how you can automate the whole LED panel.
Step 6: Watch the Video
Watch the video to see how I put together the project, and remember to press the VOTE button in the upper right corner! Click here to see the video.
Click here to see how I automated the panel with an Arduino.
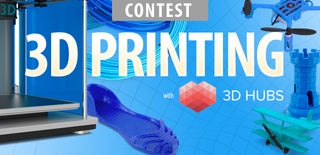
Participated in the
3D Printing Contest 2016