Introduction: DIY Small Bench Power Supply
This is a small bench power supply that I made some time ago, and because I was very busy I couldn't do the instructable for it. I do apologise for taking so long, I hope it was worth the wait :).
After making my Mini Adjustable Power Supply I was very happy with it, but I was missing a more accurate control of the voltage and current. So I decided to make this slightly bigger (but still small) bench power supply.
The heart of the unit is basically the same as on the other power supply. It is based on the LM2596S. This IC can handle up to 3A with a good heat sink. I would use it only for 2A to be on the safe side.
There is a video of the unit working on the last step of this instructable.
Enough talking about it... let's make it...
Step 1: Materials and Tools
Here is a list of materials and tools I used for this project. Many of them can be replaced with other components that you may have already, but I would definitely use an aluminium enclosure, as I used it as a heat-sink as well. I have tried to find the cheapest components, but double check that the price has not changed, you may find it cheaper somewhere else.
MATERIALS
-Aluminium Enclosure (link)
-DC-DC Bulk Converter (LM2596S) (link)
-6 Pin Headers (link)
-10k Multi turn Potentiometer x2 (link)
-Potentiometer knobs(link)
-Volt, Amp Metter (link)
-Heat sink paste.
-Toggle Switch(link)
-Rocker Switch(link)
-Nail Polish.
-Nail Polish remover or Acetone.
-Power Panel Mount Connector (link) Check the power supply connector to get an appropriate connector.
-Banana sockets (link) (You may get cheaper ones, but I like the ones on the link because they are smaller)
-Banana test leads (You may have already one, I won't put a link as it may be worth getting a decent one)
OPTIONAL
The rest of the components are only necessary if you want to have LEDs to let you know if you limiting the current or the voltage, and to let you know if the output is set to on.
-attiny85 (link)
-2x Generic PNP transistors
-500R resistor x4 (or a close one)
-10k resistor x2
-100nf ceramic capacitor x2
-5V regulator L7805CV
-Heat-sink for the voltage regulator
-3mm Red LED x2
-5mm Two Colours LED and Panel mount for it.
-Etching Solution (Ferric Chloride) It is also used for PCB etching.
-Two containers for using the etching solution. One should fit inside the other and the inner one has to be big enough so the aluminium enclosure fits inside. (See step 2 for photos). They also need to be heat resistant.
TOOLS
-Dremel
-Cutting disk
-Drill and various drill bits
-Heat glue gun
-Solder and soldering iron
For the optional upgrade of warning LED's you will also need:
Household iron
Laser Printer
Step 2: Design and Etching the Enclosure
After taking measurements of the enclosure and all the components, I designed the layout of the front of the unit with Photoshop. I added the file so you can modify it to your needs. If you are designing it in another enclosure, just make sure you take into account what's inside the enclosure and fitting points.
Print the design on photo paper and with a good quality laser printer.
Place the front of the aluminium enclosure on top of the photo paper, printed side facing the aluminium. Use the iron to heat as evenly as you can the other side while applying pressure. Do this for about two minutes, or when you see the back looking like the one on the photo.
Wait for it to cool down, and peel the paper off. If everything when well your design will be left on the enclosure.
Inspect the printed area to see bright spots, and paint them with nail polish. Anything that is not covered will be etched.
Use tape to protect the rest of the front of the enclosure so you don't damage it with the etching solution.
Put some hot water in the bigger container and place the other one inside.
WARNING!! Wear gloves and eye protection when handling the etching solution. Use the solution only in a well ventilated area. The etching solution will stain yourself as well as pretty much everything it touches, and it will damage anything metal, especially be careful with the sink if is the metal type, when washing the enclosure.
Pour some of the etching solution in the smaller container and leave for a few minutes to warm up. Place the front of the box in there. Agitate for about two minutes and a half. (Time will depend on the temperature of the etching solution).
Once it has been etched, wash with cold water. I use some etchant neutraliser to stop the etchant reaction, but it is not necessary if you keep applying cold water for some time. Apply nail polish and let it dry. Carefully remove the excess to leave nail polish only on the etched area. This may take a few attempts, but I didn't want to sand the aluminium
Attachments
Step 3: Drilling and Fixing Components
I always cover the enclosures with decorators tape to protect it while drilling and cutting it. It also helps the marking procedure as it is a lot easier to mark on the tape than on the aluminium.
I measured all the components during the design process, so it was a matter of just drilling and cutting where the marks were. Just make sure your components will fit before this step.
I placed all the components on the aluminium where they will stay so I could access everything to solder the cables.
Step 4: Heat-sink for the DC-DC Converter
I decided to use an aluminium enclosure so I could use it also as a heat-sink. I cut a small piece of aluminium and after applying heat paste, I glued it to the back of the regulator. Then I applied heat paste on the back of the enclosure and hot glued the regulator to the back.
Step 5: Schematic and Diagrams
These schematics are self explanatory. The first one is without the LEDs, the second has the option of LEDs for the output and to let you know if you are limiting the voltage or the current.
The colours on the voltage and current meter may change on your model, so please check your wiring with the meter provider.
Step 6: LEDs On/Off and Limiting Warning (Optional)
For the CC/CV LEDs I used the dremel to sand a bit of the top of the LED to avoid it being too bright on that area. I drilled an opening on the top of the meter and placed both of the LEDs inside as per photo.
For the On/Off LED I used some heat shrink, but some tape will do.
Here is the code for the Attiny85, It is very simple, and I'm sure there are ways to do the same without a microcontroller, but I have a few of then around and I love to use them.
#include
#include
int LED = 1; //LED for CC
int LED2=2; //LED for VC
int Signal=0;
int SignalYN;
void setup() {
pinMode(LED, OUTPUT);
pinMode(LED2,OUTPUT);
pinMode(Signal,INPUT);
}
void loop() {
SignalYN=digitalRead(Signal);
if (SignalYN==HIGH){ // Limiting the Current
digitalWrite(LED,HIGH);
digitalWrite(LED2,LOW);
}else {
digitalWrite(LED2,HIGH); //Limiting the Voltage
digitalWrite(LED,LOW);
}
}
Attachments
Step 7: Testing
Here is a video of a test of the power supply. I hope you enjoy this instructable. I will be happy to answer any questions or help you out to build your own.
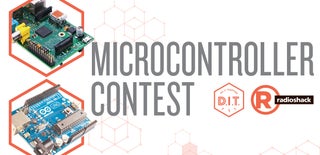
Second Prize in the
Microcontroller Contest
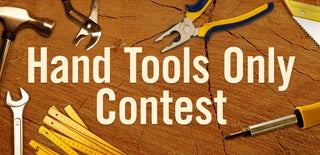
Participated in the
Hand Tools Only Contest