Introduction: DIY High Resolution 3D DLP Printer (3D SLA Printer)
Hello World (skip the first two pages to go directly to the build)
Follow me on facebook to stay up to date about all my projects!
https://www.facebook.com/TristramBudelsworkshop
I have to admit that I have not been active on Instructables for quite a while now, this because we (yes it is we now :D) have been busy developing a 3D printer. A 3D dlp printer to be exact, an open source high resolution 3D DLP printer to be even more exact.
We have now finished version 1.0 and now it is time to share our learnings with the rest of the world.
Why did we work on a 3D printer?
Well as you all know the world needs more 3D printers, more platforms for creation, more freedom. More possible ways to show your epic awesomeness in creation. And most of all the freedom to design and fabricate exactly what you need, when you need it without any barriers. In short 3D printers are awesome, you can never have enough 3D printers.
Why did we work on a 3D Direct Light Processing printer (DLP)?
3D printers come in many shapes, sizes and varieties. There is Fused Deposition Modelling, FDM for short this is the category the RepRap community largely falls in to. Your Makerbots and Ultimakers that use a heated nozzle through which a filament is heated and deposited on the desired location. There are various powder bed 3D print techniques, where the powder particles are selectively fused together with a laser or glued together with a printed adhesive. And there is a variety of photo lithography 3D printing methods.
In lithography light is used to cure a resin to become a solid, the nice thing with this process is that where the light does not shine on the resin it stays liquid.
We found that there are two main DIY 3D printer routes out there that are easily accessible, FDM and photo lithography.
When googleing the WWW we found that there are absolute tons and tons of FDM 3D printers out there all working on roughly the same principles all producing roughly the same results.
Next to that stereo photo lithography has until now only been made really accessible to the community only by one guy, Michael Joyce from the B9 Creator. This is an awesome achievement! For us this also means that the world needs more and different kinds of these projects to become really open source. Photo lithography is an very precise method of manufacturing, in the past feature sizes of 100nm where obtained. No idea how big this is in inches (sorry people from the USA) but I estimate that if you squeeze your fingers together the space between your fingers is slightly less than 100nm.
If a mm is 1/1000 of a meter, a nano-meter is 1/1000 of 1/1000 of that or 10e-9 or one billionth of a meter . (courtesy of adamtimm1)
In other words amazingly small feature size. We would love to make very accurate 3d prints.
So we based our choice of what kind of printer to explore on the possible feature size, accessibility of materials, ease of manufacture and the fact that a relative few have walked this path before us.
Step 1: Basic Design Properties
I find that making lists like this before every new build really helps me and the people I am working with (it is "we" now) to come up with an effective design that really meets our expectations. This printer will be a prototype, we plan to build a cooler, better more advanced version in a later future. Hopefully to be completed at the end of 2013. And if all works out maybe we can even get to a kickstarter. (Dreaming freely here)
The printer must be,not in any specific order:
- Affordable.
- Open source
- Compact.
- High resolution.
- Compatible with a wide range of materials.
- Easy to use.
- Fast
The basic operating procedure:
This is how a Photo Lithographic 3D printer works. Photo Lithography is very simple, light illuminates the resin and the resin hardens.
To be more exact a quantity of light falls/shines onto the resin, if the energy quanta of that light is high enough it will induce photo polymerization of the resin.
First thing is to decide on a light source:
The key part in this is quantity of light energy or Dose, a therm that comes from the world of radiology.
The dose is divided in to three vectors as you will, namely photon energy, light intensity and duration of illumination, together giving the total energy dose. Usually in the UV curing of materials the dose is only measured for a specific part of the spectrum. The rest of the light will usually be reflected or absorbed and converted in to heat.
Only photons with a high enough energy will take part in the photo polymerization. This means that the resin that you will be using is the determining factor in the part of the light (electromagnetic) spectrum that we are interested in. Most photo curing resins will cure under the influence of UV light. Light with a wavelength of between 365nm and 420nm.
Some resins also allow for curing with longer wavelengths but these are usually rare and expensive.
1) One of the things to consider is that in order to be able to print with a wide range of resins we would like as much UV in our light as possible. I will explain this in depth when designing the basin, mirror and anti stick coating.
The other part is time of illumination and illumination intensity. The illumination intensity, or luminous flux is the amount of Photons per unit of time that is emitted by the light source. The longer you illuminate the resin the deeper the light penetrates and the harder and thicker your printed layer gets. This is a very unique feature of stereo lithography where the illumination time is another factor to consider as this determines the build layer thickness.
2) The light source must be of high intensity so the illumination time can be as short as possible allowing for a faster build.
3) An other thing to consider is that the light source needs to be very controllable in switching from illuminating the resin to not illuminating the resin.
In the principle of photo lithography, what gets illuminated polymerizes and what does not get illuminated stays liquid. This means that our resolution or minimum feature size is determined by the minimum spot size.
3) The third parameter for our light source is that it must have the possibility to illuminate a spot that is as small as possible.
Googleing we found that there are two viable light sources/systems that will meet these demands. A blue/UV laser with nice optics to produce a small spot size and a Galvo Head or A DLP projector. A Lasers are cool but to achieve a small accurate spot with a galvo system felt to us as going way over our heads. Since non of us has any experience in setting up a laser, laser optics and a galvo system. And having the guys from Form 1 as an example (patent issues), maybe one day we would like to offer the world a kit too. We decided to go for the DLP projector option.
There is a whole world of DLP projectors out there.
A light source passes through a rotating colour wheel and falls on a surface with actuated micro mirrors. These mirrors in synchronization with the colour wheel decide when to either reflect light through the lens or deflect it to somewhere else. Together many micro mirrors form the image.
As from our considerations in the above we can easily state what properties we want our projector to have:
- high UV content (determines if the projector works to cure the resin)
- high light intensity (shorter cure time)
- high contrast ratio (gives a higher resolution with less light contamination)
- high resolution (results in a smaller feature size)
Last but not least we only have 1000euro's to spend on a beamer. So there is a financial limit too. I realize this is not a small budget for a decent projector, but if the project fails I can always watch a movie on it.
In the end we decided to use an Acer 7077365 Acer H6510BD DLP FHD 1080p, with 1920x1080pixels. Which we ordered at a local store.
Having the light source sorted we can now decide how to use our light source in our 3d printer:
Wait who ho ho stop, yes I know we are just designing a 3D printer but lets do a quick google on resins (photo curing resins). We found that these materials aint cheap. So this cancels the top down approach option. In common stereo lithography the light source illuminates a pool of resin from above. As consecutive layers form the build platform sinks down in to the vat of resin. This means your work piece can only be as high as your basin is deep. This also means that no matter what the size of your build, you must always have a full vat of resin. Meaning that if you want your largest object that you can print to be the size of a shoe, you will need a constant volume of about 3L of resin in your tank. At 80 Euros per litre, there are always 240euros sitting in the tank.
To us this is a bit much. So bottom up it will be.
There are two reasonable configurations when considering a bottom up 3D DLP printer. We can either project directly onto our build area or we can use a mirror to have our projector at an angle in respect to our build area.
We chose to put our projector at a 90 deg angle and use a single surface mirror to project a crisp image on to our build surface.
This because we are aiming for a true desktop machine, something that really fits on our desktop and is as compact as possible.
Step 2: Safety
Yes a whole page devoted to safety, be safe, take precautions, use your protection gear.
Please remember you have only one set of stereo vision sensors. Though you have two opposable thumbs I find this very handy and I bet you would prefer not to have to replace one of these with a big toe. So please use all safety gear and be sensible about it.
Gear:
Safety goggles and or face shield
Disposable gloves
Sturdy leather gloves
Earplugs and or earmuffs
Sunglasses
Please wear your face shield or goggles and appropriate gloves when cutting, filing, grinding, working with solvents and chemicals.
When performing operations that produce sound, forget about loud sound, just any sound wear your earmuffs or earplugs.
I say this because of my dear granpa, he is always telling me he does not need earmuffs because his disk grinder makes no loud noises. Sure you get it.
When staring at your Beamer light wear sunglasses.
I am not responsible for any of your injuries or damage you do to yourself or your surroundings, but I Will appreciate it if you are like me and try to set a good example. Your kids are watching and will do as you do.
Thank you so much for using your safety gear!
Step 3: Sizes and Dimensions
So first of we hit a small dilemma for starting the design, how big does it all need to be? Where does what go? Etc etc. ok it took us a day or two to figure our how to determine all off this. I mean the whole build is based on this so it's rather important.
Materials/tools:
Beamer
Computer
Ruler
Tape measure
Notepad
Pencil
Cardboard
Scissors
Tape
Plain white paper
Chair
First think about your X and Y, the size of your build area. We chose about 100x100mm to start with. The build area in the Z direction is of course dependent on the length of your linear slide.
First of you will need your Beamer and your computer to project an image. Place your Beamer on a chair facing the wall. And put the Beamer on maximum magnification. Move the Beamer to the wall until your image is 100x100 and measure the distance between the lens and the wall. This is your minimum projection distance.
Now put your Beamer on its minimum magnification and move it from the wall until again your image is 100x100mm this is your maximum projection distance. This means that in the build the distance between your bottom window of your basin and the lens of your Beamer must be between these two values as your Beamer will allow for any fine tuning in this area.
To work the mirror in to this equation you measure form the heart of the lens (do not scratch or touch it) to the basin with a 90 deg angle. So if you place the mirror very close to the lens the basin must be placed higher above the Beamer. But if you place the mirror further away the basin will be placed lower but further.
Once you have figured out where to place the mirror you can determine its size. We did this by fumbling together a 45deg slope out of some cardboard and tape with some white paper on top. Placing it in front of the mirror at the desired location and turning on the beamer. Then outlining the image on maximum magnification with our pencil. Definitely you need sunglasses for this wauw that thing is bright.
We added about 2cm to this outline then took the longest side as the measure for our square mirror.
In the lab I realized I have a stack of 152x152mm glass plates, these are a bit bigger than required and will thus do fine.
Step 4: Design
We decided to make a back bone for the machine out of aluminium profiles that we had lying around.
A simple compact design. Staring with two horizontal profiles which will make contact with the table to provide a steady base, two risers with a horizontal beam make a bridge over the beamer. To this bridge the building platform and Z-axis are attached.
We decided to use 2mm thick aluminium plate as a base to put the beamer on and an other 2mm thick sheet to hold the basin.
Because of the profiles we are using as the back bone, 45mm square aluminium profiles. We can really get away with this structure using no diagonal supports without losing rigidity. These profiles are really massive and a bit of an overkill for this type of machine.
What you cant see in the rendering here are all the corner pieces we used to bolt together the frame. I will put in some pictures later in the build.
Because we are going to use light sensitive materials in the end we will cover the printer with a box to keep out any light and dust.
3D design made by Chanil Budel.
Step 5: The Bones
Materials:
aluminum profiles 45x45mm total of about 2.5m
8 corner pcs
M6x15mm + washer 16pcs hex socket cap screws
M6 T-nuts that fit the profiles 16pcs
Tools:
Metal cutting bandsaw (a hand saw will do the trick but it might take a few days extra)
Allenkey
file
Cut the profiles to the following lengths:
2x 450mm
2x 280mm
2x 260mm
2x 200mm
make sure you cut nice 90deg angles and file off all sharp edges.
This is actually only the second time Inhave used these profiles and I am still amazed how easy it is to build something out of these profiles. Cut the profiles,screw them together and tada done. Using a band saw and a power screwdriver it took us about two hours to assemble the back bone.
I have added the construction plans for the back bone so you can but the profiles together accordingly.
Attachments
Step 6: Platforms
On the back bone we mounted three aluminum plates that will support the beamer, mirror setup,and the build tray.
Materials:
2mm thick aluminium sheet about half a square meter.
M6x15mm hex socket kap screws 12pcs
M6 washers 12pcs
M6 T-nuts 12pcs
Tools
Allen wrench
Nibbeling shears and or jigsaw
Step tapered drill
Drill press
Waterproof fine tipped permanent marker
Ruler
Pencel out the parts on the aluminium sheet according to the designs. Cut out the outlines of the pieces. The next step is to drill all the holes. For the plate that will hold the Basin drill a hole in each corner to make cutting out the large square easier. Drilling all the holes before taking out larger areas will make the drilling easier. Taking out material weakens the structure a bit so drilling first gives you nice sturdy material to drill in.
Step 7: Mirror Cradle
The mirror cradle is made out of the same material as the platforms, 2mm aluminum sheet. The cradle is made out of a square piece of sheet material and a strip. The strip has a hole in the end for a bolt and is bent in a U shape, hence cradle. Each of the bolts is slotted in the head to fit the square plate. A hole is drilled in the side op the bolt and threaded with M3 tread and fitted with an M3 grub screw to fix the mirror plate ( the aluminum square).
Fitting the slotted bolts through the holes in the U provides a pivoting point for the mirror plate. Putting nuts on the bolts makes that the angle of the mirror can be fixed and secured. Putting slots in the bottom of the U gives the option of sideways adjusting the position of the mirror. The slots put in the bottom mount plate provide adjusting capabilities back and forth. So the mirror can be adjusted in the X and Y direction, I'm trying to name things properly. The combination of these slots also allows for some rotational adjusting.
Materials:
M8x15 bolts 2pcs
M8 nuts 2pcs
2mm thick aluminum sheet
Tools:
Jigsaw and or nibbling shears
File
Dremel grinding tool
Hacksaw
Ruler
Fine permanent marker
Stepped taper drill
Drill press
Machine vice
2.5mm drill
M3 drill tap
Cutting oil
Draw all the parts on the aluminum sheet. Next drill all the holes and holes at the beginnings and ends of the slots. Depending on the size of your aluminum sheet you might want to cut out a manageable piece. Mine came as a 1x2 meter sheet and putting a corner of this sheet under the drill press is an instructable on its own.
Cut out all the slots with the shears or jigsaw. Proceed to cut out all the outlines, keeping this order gives you a nice solid workpiece.
File all the sharp edges using a file or Dremel tool. I found that the Dremel really works on the slots but I prefer a hand file for all the other edges, it's a bit less aggressive.
Clamp in the bolts in the machine vice (in the picture I actually use a drill clamp) and drill a 2.5mm diam hole through the head of each bolt. Next thread the nuts using the M3 drill tap and some cutting oil. Now for some more serious manual labour. Reclamp the Bolts upright in the vice and use the hack saw to cut a slot in the head of the screw.
Step 8: Z-axis: Spindle and Anti Back Lash Nut
Why use such expensive gear? Well this is what basically determines the accuracy you get out of your Z axis. Even fancier and more expensive, a lot more expensive, would be to use ball spindles and a ball spindle nut. Just wanted to drop the terms to set you on the track of the uber accurate.
Any normal nut and tread end will have ginormous play. This is because the thread in common nuts is just a bit bigger than the thread on common threaded wire. This ensures your nuts screw easy on the thread, even when a bit dirty. This could give a play of several tenths of a millimeter. Of course you can compensate for the jiggle in your software. But in the real world this still means your nut is jiggling around your thread.
This jiggle room is referred to as "back lash", which is most clearly detectable when your axis changes direction.
The anti back lash nut consists out of two parts and a locking screw. Both have the same thread on the inside as the spindle, on the parts where they screw together they have a different thread either coarser or finer than the spindle.
Screw both parts all the way together, then screw in the finished spindle until you encounter resistance. Carefully unscrew the parts until you can screw in the spindle all the way through. Screw the spindle through the nut until the nut is about half way through.
Here is where it gets a bit trickey and you might want to make sure you can reach the locking screw even in the finished printer.
Now you need to unscrew the parts of the anti back lash nut a bit more until you feel some resistance in unscrewing. Make sure you don't use too much force you should still be able to move the spindle inside the nut by hand. Once you are happy with your setting screw in and tighten the locking screw. We replaced the original screw with an M3 grub screw so it does not stick out. This makes it a bit easier to mount the anti back lash nut on the carriage.
We ordered our trapezium spindle from Damencnc.com together with two grove ball bearings 6000ZZ 10x26x8mm.
They offer the service of finishing your spindle for you in case you don't have a lathe
Attachments
Step 9: Z Axis
Our Z axis consists out of a dove tail slide, carriage, two leadscrew mounts, a motor mount, stepper motor, motor mount and a bunch of screws.
Materials:
10mm thick aluminum stock
20mm thick aluminum stock
3mm aluminum sheet
20mm round aluminum stock (or buy a shaft coupler)
15x50 brass stock
3mm brass sheet
M5x20 hex socket cap screws 4pcs
M6x6 grub screws 2pcs
Tools:
(CNC) mill or a friend who has one.
M5 tap set
M6 tap set
We made our linear slide from some materials we had laying around the shop so please feel free to alter the design and use different materials. I believe you could just as wel 3D print the spindle supports, motor mount and probably even the shaft coupler and the carriage. But for accuracy you will want to mill out your main dove tail linear guide.
You can use our plans to make the nessecary parts.
Step 10: Spindle Nut Housing and Build Platform Support Arms
To bridge the gap between the build platform which will be in the center of the tank and the Z-axis we will need some more parts.
One part, the spindle nut housing to connect the sled (the thingy that slides over the linear guide). A smart connection system so we can easily remove the build platform from the Z-axis. And some angular parts that will reach over the walls of the tank so we can place the build platform on the bottom of the tank when we start printing.
Now put all these parts together and presto (presto took us about two weeks) one Z-axis with sled, lead screw, bearings all complete.
Step 11: Build Platform and Research
Before you can build your build platform you need to have some 3D resin. I got some from different suppliers. It's quite an expensive ordeal but I have yet to figure out which suits my purposes best. The easiest to get is from Spot-A materials, they have a few.
But here is where we ran in to some serious problems.
Every resin adheres differently to the build platform material. You want the the cured resin to adhere to the platform nicely but not so nice that you will never be able to peel your workpiece off. So the idea is to find a material to which the resin adheres well too, but let's go when you try to pry it off.
There is only one way to really find out which works best. Yes the empirical method, trail and error, to try and try again.
Get a bunch of different materials, put a few drops of resin on top and cure the resin. Now try to peel the resin of your substrate.
Materials:
some thick sheets of different materials, PMMA, polycarbonate, aluminum, PVC, PE etc etc.
3D resin
Tools:
Pasteur pipet 1ml
Scalpel
UV lamp (small blacklight does the trick)
bottle cap
Marker
Jigsaw
Drill press
CNC mill if you have
Ok you really need to wear gloves for this one, 3D resins in liquid form do not nessecarely promote your health.
Put one drop of 3D resin on the substrate ( the material you wish to test) and harden it with the UV lamp. To make this experiment a bit more exact you can use your bottle cap as a measure. To ensure the contact area between your substrate and the resin is of equal area for each substrate. I used a marker to outline the bottle cap on the substrates and filled that area with resin.
Which I then cured. I found that it is even better to cure a few layers of resin on top of each other, this gives you a bit more sturdy object to pull of your substrate.
Once you have put a defined area of cured resin on each substrate you can now carefully peel the resin of the substrates. I used a scalpel as a prying aid. If you do this right you should be able to feel to which substrate the resin adheres best but still peals off.
Now that you have determined which material works best with your resin you can cut out your build platform according to our plans.
Attachments
Step 12: Resin Basin
The resin basin is basically a tank that holds your resin. Since we build bottom up, the bottom of the build tank needs some special attention. The light will pass through the bottom of the tank and the anti sticking layer before it gets to the cure the resin. Unfortunately most materials absorb our precious UV light. So when selecting the material for the bottom we must take in to account that it must be as UV transparent as possible.
After some googling we found that the best and most UV transparent anti sticking coating is sylgard 184. This can simply be bought from eBay or amazon. Just take care you buy the real stuff from Dow Corning and not some Chinese ripoff. Being a chemist I am always a bit cautious with bringing plastics in to contact with solvents. I am of course referring to using Plexiglass to build the basin out off as I observe many people do online. Yes it looks great but please take the following in to account. Plastics may contain plasticizers and other solvents and chemistry that may leach out off the plastic when brought in to contact with organic solvents. Your 3D resin might just be a very good organic solvent. This means you change the composition of your resin which might give the cured product very different properties than the resin should have. It can even happen that it will not cure at all, becomes waxy, get rubbery etc etc.
So we will build our basin out of mostly inert materials.
We also wanted to build the basin in such a way that it is modular. Which led if I may say so to our very elegant basin design.
The basin consists out of a base plate made in our case out of aluminum. This is what holds the entire basin together and needs to be a stiff structure. I milled some slots in to the base plate to fit in the walls of the basin. I recommend you use glass for the walls of the basin, 2mm ordinary window glass will do. I sacrificed a large picture frame with a 2mm glass window for this purpose.
Glue the walls of your basin on to the base plate with some silicone sealent.
It is important that you use the right type of sealent here, the one that is clear, colorless and used to build aquaria. Over the past few months we have tried a few different types, silicone = silicone right? Wrong! Different types of silicone have different compositions and we found that over time most silicones give under our abuse. They for some reason can not handle the mechanical stress. Or do not adhere to the aluminum properly, or the glass when exposed to our 3D resin.
Leave your walls and base plate dry for at least a day before you glue on the bottom.
The bottom is a bit of my special baby. I am not 100% happy with its performance yet but I'll dive in to that in the review of our machine.
For the bottom plate you will need a 0.7mm borosilicate window of 150x150mm. This is a very special item and I have no idea where you could get yours from. I have some friends at Phillips Pins, that is The Phillips research facility on the High Tech Campus in The Netherlands. So in the spirit of DIY I consider this a bit of a cheat, but these guys are awesome! They do O-LEDs, coffee machines, TVs and all sorts. If there is a large interest I maybe able to poke them for a stack of them but I expect these windows to be like at least 150€ each.
Why borosilicate? Well that's because it is highly UV transparent I believe all the way down to wavelengths of 200nm. So this really helps preserve our precious far blue and UV part of the emitted light of our Beamer.
Also borosilicate is a lot stronger than normal glass. This leads me to the second option normal glass, you could use normal glass of about 1 or 2 mm thick. Please don't use transparent plastics, they are filled with UV blockers or not UV stable. That means that your cure time will be much longer then necessary or that your basin will become brittle over time.
Your bottom window need a anti stick coating, known as a conformal coating in some industries. Most of the DLP folks out there use sylgard 184 by Dow Corning.
I have found that it is suggested that you build a basin and pour in some thing like 250 grams of PDMS (you know the silicone elastomer sylgard 184). That is a little expensive for my taste, 500 grams of PDMS go's for about 80€. And I read that this coating is to be considered a disposable. Meaning that you will have to apply a new coating every few builds or your object will stick to the bottom. So we will apply a better coating with 5mm of PDMS and make my jar of sylgard 184 last 50 times longer.
We will use a method known as tape casting or doctor blading. It works a bit like squeegeeing your windows.
Materials:
Silicone kit/chalk the aquarium transparent type
2mm glass
Borosilicate 150x150 window or a normal glass window.
Scotch tape
Piece of aluminum 200x200x10mm will do
Disposable cups
Disposable stirrers
Kitchen paper rolls and rolls of it
Soap
Water
Ethanol
Tools:
Glass cutter
Drill press (or CNC mill)
Jig saw (or CNC mill)
Silicone sealent gun
File
Carbide sanding paper 240 grit
4 microscope slides
Digital scale that reads single grams or smaller
Pasteur pipet
Scalpel
First use our designs to make the base plate. If your doing this by hand use your drill press to drill all the holes and drill our the four corners of the middle square. Next use the jigsaw to cut out the window in the aluminium assuming you have drilled your holes on the corners of this window large enough for your saw blade to fit through. Make sure all your cutting and drilling stays within the outlines of the window. There is not much room for an oops. When your window hole is done cut the aluminium to size with your jigsaw. Again if you are doing this by hand you might get away with using thinner aluminium say 5mm but 10mm is what we used. Don't forget to facet all the edges with your file to remove any sharp burs.
Cut your glass to size with your glass cutter the proper dimensions. We used glass walls that are 50mm high. Use some carbide sanding paper to sand the edges of your glass to remove the razor sharp edges. Best use a bit of water as lubricant here.
Glue the glass in place on top of the four spacers (see picture) with the silicone chauk and leave dry for at least a day.
Prepare the bottom window.
Ok here we go, it is really necessary to walk on your toes here as your future build quality depends on it. Wear gloves!
Wash the 150x150 window under the tap using your fingers (with your gloves on) to gently rub ever square mm of the glass. Next put some dish soap on your glass and again use your fingers to rub every square mm. Rinse and rub your window under running water at least three times to remove every last bit of soap residue. Rinse off your glass window three times with clean ethanol. And place your window in a standing position some where dust free and dry to dry. It is clean now, it should have no spots speckles and look absolutely clean. If you see any spots, speckles repeat the cleaning process from the beginning. Since it is so clean now it is of the at most importance that you do not touch it with your bare skin or bring it in to contact with anything that is less clean than your window. This for me means I only touch it with fresh clean gloves and maybe kitchen paper. But kitchen paper produces a lot of dust.
Prepare a squeegee:
cut a length strip of glass of about 20cm long. Make sure that it has one edge that has been cut by a professional that means absolutely straight. Wash this strip like you did with the bottom window.
Prepare your PDMS
Use a disposable cup. Put the cup on your scale and tare. Measure an appropriate amount of resin. If your scale only reeds grams measure 10 grams if it measures 0.1grams or smaller measure half that. You will really only need 5ml of resin, but it is very important to get the ratios right or the end product will not cure properly. Use your pipet to ad 1gram of catalyst, again use half that if you can measure sub gram units. Homogenize thoroughly (means put in great effort of stirring). Stir for 5 minutes be sure to mix all the materials from the walls and bottom of the cup.
Optional; place the mixture in an dessicator for 15mins at 20mBar. This will remove all air and micro air bubbles form the mixture.
If you do not have a dessicator at your disposal just leave it sit for 30min.
Continue preparing your bottom window:
Place your window in the center of a square of kitchen paper (lint free paper is much better). Apply a single layer of scotch tape on the entire outer 5mm edge of your bottom window. Put one extra layer of tape on the left and right edge.
Get your PDMS and pour it in a single bead just against your front edge of the window on the glass. Just against the tape is fine. Now use your squeegee to squeegee the bead of PDMS over the glass. Because the tape provides an even spacer between your squeegee and glass you should now have a homogenous layer of PDMS on your glass which has the thickness of two layers of tape.
Set this aside and leave cure overnight.
If you want to cure it quicker place it in the oven at 80 deg C for about an hour.
Use a scalpel to trace the edges of the tape in the silicone coating. Now peal of the tape and your bottom window is done.
Note that the PDMS is not glued to your glass and if you remove the tape without tracing it with your scalpel you will also peal of your coating.
Now take your base and walls which have been fully cured and apply a thick bead of silicone glue around the edge on the bottom of base plate. Note you're sticking your window under the base plate (see pictures if unclear). Place your window on the bead of glue in the right orientation. Make sure that if your base and walls are bottom up on your table the window goes on with the coating facing the table.
Slide your microscope slides between the corners of your window and the base plate. We use these as spacers. Make sure they are just at the corners and are not in the actual future build area. Now gently press on the window untill it touches the spacers. Leave it dry for about two hours then pull out the microscope slides and fill up any gaps with silicone kit as needed.
As I told you the basin is modular, because the window is kitted to the bottom with spacers you can always cut it loose and stick on a new window. Or get the old window, clean it, apply a new coating and kit it back on the base. All without starting all over.
We expect this will help us greatly once we start trying out different coatings, but that's a next instructable.
Attachments
Step 13: The Mirror
If your printer is designed so that the Beamer is directly under your basin you don't need a mirror. But we chose to put our Beamer at a ninety degree angle with the aim of making a more compact printer. So we need a mirror to bend our light around the corner. Ideally you want to use a single surface mirror for this. Because this is one of the build quality determining factors a high quality mirror would do best. I did not manage to find any reasonable priced suppliers of 150x150mm single surface mirrors so far. Still looking all suggestions are welcome. I asked some friends of mine at the Phillips labs if I can have a few hours access to their thermal evaporator.
Why not use a normal mirror? Well normal house hold and general purpose mirrors have the reflective layer coated on the back. If you are doing your hair this is no problem. But this type of mirror with a secondary reflector reflects the light twice. Once from the front surface of the glass and once from the metallic layer on the back. So this would mean when you use a normal mirror you would print double or in the best case see this as a loss of resolution.
I suggest you do the same as I did, most universities with a physics lab have a thermal evaporator or sputter tool just give them a call and say you are working on a 3D printer. I am sure you can find a student/undergrad or teacher that is willing to help.
A layer of silver is good but aluminum will be best. Apply at least 500nm of silver or aluminum to your glass. Make sure you have a transport box or something because touching your pristine metal surface will do it no good.
Thermal evaporator s are cool pieces of tech. Here is how it works.
You place your clean substrate in the mounting tool facing down. Usually this tool rotates to ensure a homogenous coating. Then you load some material, silver or aluminum in a small tungsten boat. They call them boats don't know why. You close the chamber and turn on the vacuum. First a pre pump to get the pressure down to about 10^-3 bars and then the turbo kicks in to bring it down to 1*10^-6 bars of pressure. The turbo pump will literally kick out all the air molecules one by one until there are no more molecules left to kick out. Now you can turn on the power. Electrical current is used purely by resistance to heat up the tungsten boat. This causes the metal in the boat to melt and then boil. Because there is nothing in the chamber to provide any resistance to the metal atoms that fly of the boiling pool. They shoot out in a straight line from the pool and condense on anything they hit to form a fresh layer of metal.
And thus our mirror is born.
If you get the opportunity to have an aluminum mirror ask if they can give it an oxygen treatment, a quick exposure just a minute or two to a oxygen enriched atmosphere. Or blow a stream of pure oxygen over your mirror for a short time. This will cause the aluminum to form a very thin but very dense aluminum oxide layer. Better known as Safire this will make your mirror last through the ages. Remember that your metal coating is 500nm thick. Squeeze your index finger and thumb together, the space that is in between that's the thickness of your coating. So though it has a oxide passivation it is by no means scratch proof.
Use 4 small pieces of double sided tape to stick your mirror to the backplate of your cradle. Remember to stick the glass side to the backplate or your could have just bought a normal mirror. (Good that I got to make two, yes I really made that mistake)
Step 14: Electronics
This is the easy part. We went online and found reprapworld.com.
All electronic parts can be found here.
We ordered:
Some headers (male and female)
Thermal glue
Nema 17 stepper motor (set of 4 for future projects, we only need 1 here)
Opto end stop
Ramps 1.4 basic kit, comes completely assembled with the arduino MEGA.
Some other things that are handy:
Soldering iron
Solder
Fine cutting pliers
Small screwdriver
Multimeter
Now you only need a 12V 24W power supply
A 12v computer fan
And an USB cable to connect the arduino to your computer.
Now carefully check that the ramps board fits on top of the arduino board, all the pins must align. When we got ours we needed to realign a few. After aligning all the pins the Ramps board should fit neatly on top of the arduino.
Glue a heat sink to the chip of the motor driver. Up on testing we found that the thermal mass of the heat sinks that come with the ramps kit are not nearly large enough. So we replaced this with a block of layabout aluminium.
Solder a female header to each of the leads of your stepper motor.
and connect them to the ramps board (see picture for colour coding)
Also solder some female headers to the leads of your opto end stop. You can use a mechanical switch here, but we found a light port switch a bit more elegant. Again see picture for how to connect the Opto to the ramps board.
Because of the lousy capacity of the motor driver we needed a lot of extra cooling. So we set up an 80mm computer fan directly on the motor driver.
The arduino MEGA will be powered via the USB port but the rest of the system needs a seperate power source.
To power the rest (ramps, fan and box fan) we build our own diy power train out of a strip of screw terminals. See picture.
Step 15: Software
There are some pretty nice software packages out there. In the end we decided on Pacmanfan's software. His name is Steve Hernandez and he is a really cool guy.
Install his firmware on the arduino
And his software on your Windows
And you are now good to go.
Here you will find all the info you will need as well as the firmware and software:
http://forums.reprap.org/read.php?156,187848,1878...
http://reprap.org/wiki/Creation_Workshop
Step 16: Measure and Set Up.
Ok it is best to remove any fragile parts for this step.
You will need:
The 3D printer without the basin
Computer
Beamer
Dial gauge
Calipers
piece of paper
Machine clamp (something heavy)
First think you want to do once you have installed the software and firmware is check for life. Make it move just a little bit, check if the opto swtich works etc.
First step:
Put in the correct parameters in creation workshop. You will need to tell how many steps the stepper motor has to make in order to rotate 360 deg. If you are using micro stepping the general formula is (micro steps)x(stepper steps) in our case 32x200.
You will also need to put in the pitch of your lead screw. One rotation of the lead screw will move the sled 1 pitch up. 5mm in our case.
Now the program should know that our lead screw moves 5mm every 6400 steps, or 0.00078125mm per step.
Yeah uber accuracy, well not really you can not really count on a micro step to be absolute. Check out this Link to learn more about micro stepper behaviour.
Now make it move. First start by giving it a command to move 1mm. Then one more mm. Small steps easy does it. Once you feel more confident move 10mm, all the take making sure you will not crash in to the ends of your lead screw.
Once you feel really confident set up a move of 50mm but this time be read to put your piece of paper in the gap of the Opto switch.
Press go and while your lead screw is moving put the paper in the Opto. Your lead screw should stop immediately. Repeat this process until you feel confident that it really works.
Once your happy it is time to verify the performance of your Z axis.
Attach your micro gauge to a machine clamp, something heavy and immovable. Set the tip of the gauge on your sled.
Now move the sled 1mm towards the gauge. Verify with the gauge that when you give the command to move 1mm the sled really moves 1mm. repeat this measurement until you are confident that when you want your sled to move a specified distance, it really moves this distance. You can also verify larger distances using your callipers.
As a result we measured a repeatability of about 0.01mm plus minus 0.003mm so I am confident to say that we have a Z axis accurate to 0.01mm
Once you are happy you can put back together the entire printer.
Now it is time to set the height of the home position, this is also the start position for every print.
Lower the build platform down in to the basin, with your piece of printing paper between your build window and build platform.
Be very care full this is a very critical step.
Move the stage down while wiggling the paper until you feel the paper catches between the platform and the build window. Now this is your ideal home position.
Do not forget to make sure that every thing moves in the right direction.
The thing we did here is we attached the Opto to a strip of aluminium which we then attached to the z-pillar.
The nice thing about these aluminium profiles is that you can simply slide in a T nut and move it up and down to set the correct position.
On the sled/stage we mounted an other strip of aluminium as a sort of finger.
With some manual bending we made sure the finger passes down the middle of the Opto.
Now when the opto is open it lights up green (there is a green indicator LED on it), when it is blocked the LED is turned off.
When the stage is in the ideal home position move the Opto up until the LED just turns off. In our case it dimmed but did not turn off completely.
Better safe than sorry.
Move the stage up until you can remove the basin.
Remove the basin and give the command for home. The stage should now move in the direction of the home position and stop the moment the finger is about half way in the Opto.
Once you are satisfied reinstall the basin and repeat the test.
If all worked out well you are now ready to print as soon as you provide some light shelter.
Step 17: The Box
Having build the printer we still need to protect it from all ambient light. Especially day light is no friend to the inners of our printer. But Also dust, pet hair etc. is to be kept far away from the workings of our printer. This means we need to put the printer in an enclosure.
we chose to have a very simple enclosure, a wooden box with a door and a window to peep through.
Materials:
Wood sheet 12mm thick (I had some left over chipboard)
Two small hinges
8 12mm long wood screws
1 small doorknob
80mm computer fan 12V
Glue sticks
Mat black spray paint
White paint (this is a great project to spend those left over cans with paint on)
Red acrylic window.
Lead wire black and red
Tools:
Pencil
Tape measure
Ruler
Jigsaw
Hot glue gun
Brush
Square clamps (a few)
Drill
This is really intended as a 4 hour build, not the nicest thing I have ever made but ffunctionality. It is very important to keep in mind that the primary function of the box is to keep ambient light out. The printer works by curing the resin with light lets say of below a wavelength of 500nm. So we want to keep the entire spectrum from yellow down to UV out of our box. This greatly limits the choice of windows that you could put in.
Ours came from "Kunststofshop" this is a Dutch site but I'm sure they are happy to ship to where ever. We used Fluor red it's just a material that looks awesome on anything. Another plus for fluorescent materials is that they are highly UV absorbent. This is because the fluorescent dye absorbs short wavelength light and converts it into light of a longer wavelength.
Assembly:
Cut all materials to size with the jigsaw (see drawings). Take care when cutting out the hole for the window if you use chipboard. I would always advice to drill and cut as many of the large holes before cutting the contours. This so you can count on the strength of the bulk material.
Glue the box together with the hot glue gun, the most used saying on Flitetest "apply a bead of glue"
Once the glue has cooled you can paint the box and the door in a color of your choosing. Do not forget to test fit the door before doing the vigorous painting.
While the paint dries you can make the two light traps. One that traps light that could come in via the fan and one that traps light that could in from the air exit hole. It is very important to paint the insides of both light traps black. This will cause light that goes in to be absorbed rather than reflected thus effectively trapping the light.
I painted the whole box white, the outsides of the light traps white and the insides of the light traps mat black. Glossy black reflects a bit more light due to its shiny surface. After all the paint dried I glued the ventilator in the large light trap and then glued the light traps in to place.
Next I glued the acrylic window to the inside of the door with a generous amount of hot glue. My door has a nice tight fit in the doorway. So I placed the door in the doorway measured 1cm from the top and bottom and directly screwed on the hinges. I completely forgot about the doorknob which I realized after screwing on the hinges. This meant that I had to use some serious nail power to pry open my door. I used the drill to poke a 5mm hole through the door where the doorknob was supposed to go and screwed the doorknob in to place.
I would advice you to put some long leads, one black and one red on your fan before you glue it in. With my enormous enthusiasm I found this out when I wanted to connect the fan to the power supply. Meaning I had to dive in the box and connect the leads in a very confined space.
Step 18: 3d Resins
Starting this project I knew nothing about 3d resins, but soon I found that it is a world on its own.
So for now I will do the subject the injustice of trying to put my findings so far in a single page. I hope to write a more detailed instructable about this in the upcoming weeks. Here are just some basics and findings.
As far as I have understood so far is that any resin used to make plastic like materials could be used as an UV curing resin. This includes, acrylics, epoxies, urethanes, polyesters, silicones, etc etc. The easiest of these to access are the acrylics.
Many of these resins have volatile components, referred to as volatile organic components or VOCs. You need to circumvent using the VOC rich resins or use them only in we'll ventilated areas. It is important not to expose you or your family to these quite often harmful chemicals. Unless you of course ventilate your system to the outside or install adequate carbon filters.
For us this simply meant that we will try not to use any polyesters.
The aim for us for now is to find some ABS like material when fully cured. We started by ordering some materials form Spot-A materials. These guys are located in Spain. Since we are in Holland this is easier than ordering some form across the pond. At about 80€ per liter they are fairly priced and they even claim to have developed their materials on the B9 creator.
We for now used:
Spot general purpose ( GP)
Spot hard and tough (HT)
Spot general purposes:
We chose this as our first test material. Also because we chose the sub type already mixed with a dye. Wen the jar arrived we found that at Spot-A they use pigments. Personally I am not overly fond of pigments for these types of applications. Since the resin has a low viscosity the pigment starts to aggregate and precipitate on the bottom of the jar. Shake before use, as it says on the jar. Shaking causes foaming of the resin, so shake for 5min and leave the foam dissipate for half an hour. This also means you can not really leave the resin in your tray overnight.
The colorant controls the polymerization rate of the resin by absorbing the light in a controlled way. This means you need your pigment in there homogeneously distributed throughout your resin to controll your layer formation.
The curing of this material is nice and quick, we used 4sec for a 0.1mm thick layer resulting in a build speed of 50mm per hour, give or take. So awesome speed making our printer almost twice as fast as any other.
This resin also has a low viscosity, that's good. For your resin a lower viscosity is better this means that the resin can flow easier around your work and between the build platform and the window of your basin. Having a low viscosity will make releasing easier. When your workpiece releases from your basin window the uncured resin will be sucked in the void that is created by pulling your workpiece up.
I would say this resin shrinks a lot. So far I have little to compare it with but I will continue researching resins.
These cure times you can now put in Creation Workshop.
Resin suppliers:
Http://www.spotamaterials.com Very reasonably priced, good service (ordered some a few days ago).
Http://bucktownpolymers.com Very large assortment of photo curing resins, also reasonably priced, but unwilling to ship me less than a gallon.
Http://www.buy3dink.com Sells the monomer from Spot-A materials.
www.solarez.com (thanks Orngrimm)
www.makerjuice.com (thanks Dizingof & Andersonta)
I also found a supplier of resin that has a large renewable content.
www.dragoncraft.com
Step 19: 3D Printing
Print, Print, Print
After weeks of building, measuring, adjusting, building, adjusting and measuring. Finally time to print something.
We started small with a mini Tardis (from Doctor Who) to printing small vases and the Eiffel tour. The Eiffel tour, being the most spectacular or at least recognizable got manhandled by a bunch of people and now looks horrible.
Every body will want to touch your prints, be warned.
You will need:
Gloves
Ethanol
Paper towels
Here is how it works.
Find a model on thingiverse or grabcad and download the STL model.
Load the model in to Creation workshop, scale, centre and put on the build platform.
It is that easy (Steve if your reading this, you are awesome!)
Slice and print.
Once you are done printing, move the stage a bit more up until your masterpiece is clear of the resin and above the walls of the printer. Remove the build platform and rinse your work piece with some clean ethanol. Once clean, put it in the sun to fully cure, 10 minutes is plenty.
Thank you for reading, I hope you enjoyed this Instructable and now feel inspired to build your own 3D printer.
Step 20: Acknowledgements & FAQ
I would like to thank every body for helping out.
I would like to thank the world and google for giving out all this information for free, the web community is awsome.
I would like to thank Chanil Budel for all the designs and endless CAD hours.
I would like to thank Steve Hernandez for the software.
I would like to thank Asahi Chemicals, Dow Corning and Dupond for helping out with the glass and coatings
I would like to thank the guys from Phillips to lend me access to some of their cool materials.
And I would like to thank my girlfriend for letting us turn the living room into a workshop for months, babe you are awsome too!!
I have entered this instructable for the Epilog contest because we could really user a laser engraver. We would make cool signs and labels, cut acrylics, do laser folding, make better parts out of plastic sheet, upgrade our 3D printer, make cookie cutters. The options are simply endless. And of course we would make endless amounts of Instructables!
Please vote for us!
I decided to put in a small FAQ since there are some questions that keep on returing
FAQ
How much did the printer cost?
About 1750 euro's in materials.
How about a BOM?
Sorry no Bill Of Materials for this project. That is because for example I got the profiles a long time ago from a colleague of mine. No idea how much these cost so we made an estimate in the total cost. Same goes for the chip board, this came from the packaging material from our lathe. The glass windows I got from a friend that works at Phillips research lab. Aluminium sheet, we had some from an old project and got some more from a friend. Next to that we messed up a few times and used quite a bit more material than would be strictly necessary. On top of that the printer is not done yet, functional yes, perfect not yet. So the best I can do for you for now is estimate how much this build would cost.
How long did it take you to build it?
Somewhere between 1000 and 1500 hrs.
How much did the resin cost?
Check spot A materials for the latest prices, we spend about 90 euro's/L including shipping and handling.
I ordered 1 liter of maker juice, I got a really nice discount but normally it would be 45usd plus shipping and handling.
Is the project finished?
Nope not by far, we will keep on going until we have a product that is ready for every day home use.
Where can I stay up to date of all progress?
For now we use facebook as our central hub.
Where are the movies of the printer in action, I have been waiting for a week now?
I am working on it, I am working on it. I am really sorry to keep you all waiting. I am working on it. Actually I have been working on new coatings for the basin to later write an instructable about. This is a lot of trial and error and puts the printer out of commision for serious printing. So far I have tested a spray on PTFE coating (didn't work very nice), a PTFE laminate (awesome but does come of rather quickly and is a pain to apply), two types of silicone (both cool but after 3builds it sticks to the resin) and some other things.
I hope to be able to post a movie some where next week (today is 21-July-2013).
How skilled do I need to be to build this?
On a scale from 1 to 10, 1 being you have trouble replacing a light bulb, 10 being you have sent something in to space. I would say 8.
if you read this Instructable very carefully maybe a skill level 7.
Step 21: Movie
My first timelapse of a printing session.
Once I have managed to make a nicer video I will put it on the first page.
Step 22: Updates Last Entry Feb 10, 2017
We spend a long time making up our minds, developing the printer to the next level. It took us years to refine and move on to the next step.
There was blood, tears, pain... We decided to see if we could make a business out of the 3D printer.
In April 2016, we went from a kitchen table invention that had the basic functionality to a full out company. We have spend a lot of time and effort optimizing the machine, updating the designs, software and firmware. Very cool, we have now reached a point where we have a professional product and are ready to start production. Right now we are even working on the financial backing to get this thing flying.
Check out Atum3D
May 2016, We are letting opensource go. I know this is painfull, trust me I feel your pain. But we had to take some measures. There are even some Chinese companies that have commercialized our instructables designs even though this is against the licence. We love the open source community, we love all the students that are building their own DLP system, we don't like Chinese manufacturers missusing our content.
Everything we have placed online we will leave online, but this hurts a bit.
I promise that if you are a student or hobbist and you contact me, I will be more than happy to help you out.
July 2016, new directions
We are now aiming for the professional market, we want to do better, we want to make more perfect and even better products. We have developed the technology to a point where it is very easy to supply a small business with components produced on our printers. This is the direction we want to persue.
Nov 2016, we presented ourselves on the FormNext in germany the worlds largest 3D printing event, atleast that is what the brocure says. We had a ton of interest and we are definately moving forward.
Feb 2017, Still moving forward.
We are now about to introduce the world to some engineering grade materials!
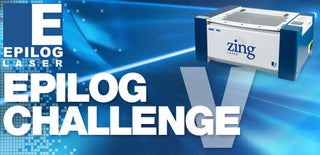
First Prize in the
Epilog Challenge V
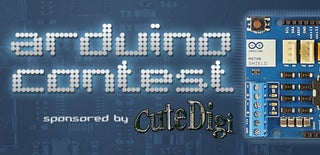
Grand Prize in the
Arduino Contest

Participated in the
Craft Contest