Introduction: Daft Punk Thomas Bangalter Helmet!
Having the Guy Manuel helmet on hand, and looking at Volpin's amazing work, I began working on a Thomas Bangalter Helmet, why not have them both? ^-^
If you've seen my previous instructables, you will understand the process much easier, however, I encourage you to have a read at this instructable!
Step 1: Materials
As stated in the intro, if you've followed my previous build, then you will recognize most of the materials listed.
Here's a compiled list:
Cardstock paper
Hot glue
Bondo body filler
Bondo spot putty
Variety of sanding sponges/paper
Contour gauge
Expandable foam
PETG plastic sheet
VHT nightshades
Krylon primer paint
Duplicolor black paint
Red EL wire (15ft)
Rebound-25 silicone rubber
Smooth-cast 65D Urethane Resin
Tools used:
Dremel
Orbital sander
Scissors
Contour gauge
Skills required:
Patience
Step 2: Designing the Model and Bringing It to Life
First, the helmet started by being designed on a 3D model software (Autodesk Maya 2012)
There can't be much said about the actual 3D model since it will require a new instructable on how to use/design objects using 3D modeler software.
This file was later transfered onto a program called "Pepakura Designer 3".
It basically allowed the object to be turned from a 3D computer object be transformed/laid out on paper and later when printed and put together will bring the 3D computer model onto a 3D real life model.
The first picture is a screen cap of the object in the pepakura software ready to be printed.
The second picture is of the file put together.
This was easy, as the pepakura software prints number on the edges, symbolizing where the edges need to be glued together.
Step 3: Strengthening and Sculpting
Instead of my traditional method of reinforcing an object, I decided to reinforce the paper model with some urethane resin by slushing a small batch inside of the paper helmet.
From this point and on, it was time to use bondo body filler! How exciting! (for me it is! Don't judge!)
Now it just became a mundane task.
Fill, wait, sand. Fill, wait, sand. Fill, wait, sand. Fill, wait, sand. Fill, wait, sand. Fill, wait, sand. Fill, wait, sand. Fill, wait, sand. Fill, wait, sand.
Seriously, it was about 2-3 days before it started reaching that smooth-perfect surface.
Step 4: Testing and More Work!
Before I continued with the build, I had forgotten to do something very critical!
I hadn't tried the helmet on to check if it had the right fit I wanted!
Oh dear! Was I worried.. Luckily it fit perfectly how I desired it to! So I was very content ^-^
I primed the helmet and smoothed it down with sandpaper grits 180-1000.
It took about 2-3 hours, but at least I had a good surface now!
Step 5: Taking an Alternate Route (optional)
By now, I was getting kind of tired of muling this helmet/weight around, so I decided to split the helmet into 3 separate parts.
1 - The dome
2 - Upper face
3 - Lower face
I primed the dome with brown paint and I cut the visor area out and replaced it with a sheet of PETG plastic.
Step 6: Details!
As you know, the Thomas Bangalter helmet design has some type of "vents" and an indented mouth hole, so I went on ahead and defined these areas but using my dremel with a cutting bit and some files.
I was satisfied with how well the vent/mouth hole were shaped.
I also made it convenient for when the casts were pulled.
I didn't want to cut all the vent holes and mouth hole all over again, so I permanently indented these areas by shaping them inward with some bondo filler.
I also worked a bit more on the dome. Since this piece was cut out separate, it was a whole lot easier to really get a smooth surface.
The contour gauge really helped out when trying to make the dome perfectly symmetrical, so you should use yours too! ^-^
Step 7: Ensemble!
When I finished working on all the main components, I put them all together using epoxy glue and back filling it with some bondo filler to make sure it would stay put.
And I primed the whole helmet in order to check for imperfections.
Step 8: Molding! Almost There!
I didn't document my build of the ears but pretty much I tried out two methods.
1 - Using a lathe and spinning a wood block to make the ear puck
2 - Using some cans and bondo to make them accurate.
I ended up going with route 2 since it was faster and easier as well as being accurate, and though it was a small shortcut, it took up some work to get it just right.
With that being said, the molding began!
Rebound 25 can be harsh to work with at first, but eventually you get the hang of it ^-^
First coat is thin
Second coat is thickened
Third coat is thickened and registration keys are added
Fourth coat is thin to lock everything together.
Step 9: Shelling!
I call this process "shelling" now, because that's practically what is is!
It's originally called a "mothermold" but I think "shell" or "shell-in" fits better!
This shell-in was made from fiberglass resin and cloth.
This shell-in is hard in order to prevent the cast from deforming when replicating the mold.
Step 10: Casting!
So finally I grabbed my smooth-cast 65D, mixed up a couple of batches, poured them into the mold, slushed it around and voila!
I now had my first thomas cast!
I was so excited and proud when I pulled it from it's mold!
My friend, who is also a Daft Punk fan as I was, was over my house he was literally waiting for me to pull the cast out so he can wear it! Haha!
You can see his excitement in the pictures (not really, since he is wearing a helmet)
Step 11: Paint, EL Installation, Finished!
With my cast on hand, I gave it a couple' coats of paint.
I cut out another piece of PETG plastic which I tinted by spraying it with VHT nightshades.
I installed the visor by using epoxy glue.
The EL wire was installed using super glue and finally I was done!
I was able to take this with me to Megacon and a lot of people really liked it!
I met up with someone there who had bought a daft punk helmet.
She was amazed when I told her I made mine, haha!
So that's how I was able to turn 3D computer model design in to full scale 3D real time object, which is also wearable!
Hope you enjoyed reading my instructable!
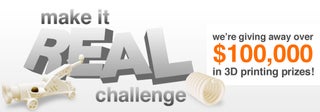
Participated in the
Make It Real Challenge
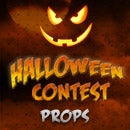
Participated in the
Halloween Props Contest