Introduction: Dandelion Wind Turbine
We were given a project to design a wind turbine with an aim to generate as much power as possible (with 24W motor). In this instructables page we will show you a step by step process to build our turbine.
Step 1: Materials
Materials Needed:
-3mm sheet thermoplastic
-MDF, various sizes
-Sheet Aluminium
- 1 x Steel Block (50 mm diameter x 50 mm height)
- 1 x M8 threaded poles (0.6 m long)
- 2 x bearings ( 6mm inner bore, 22mm outer diamter)
- 2 x M5 bolts and nuts
- 4 x M8 nuts
- Various screws
- 2 x Gears (inner bore diamter 3mm)
- 1 x Bucket (approx 30cm diameter or wider at opening)
Tools and manufacturing process:
-laser cutter (alternative to hand drawing)
-band saw
-hot air gun
-lathe
-chemical adhesive
-glue and painting
-solidworks
Step 2: Making Blades
There are two options for making the blades:
1. Take the illustrator files and using a laser cutter, print them out in 3mm plastic (or draw the design onto the plastic and cut out manually
2. Spray paint the sheet aluminium, then using a laser cutter etch the blade patterns into the aluminium and cut out the design by hands.
The results should be similar to the pictures attached. (all blades should have the slots, this eases bending)
You should make either 3 or 6 blades.
Step 3: Bending Blades
The fan blades must now be twisted.
If made of sheet aluminium, grab the tip of the blade and spin clockwise, twisting the shape of the blade. The aluminium is malleable enough to withstand this.
If the blades are made of plastic, a hot air gun must be used. Heat a plastic blade and again twist by hand (remembering to wear safety gloves!). When the desired shape dip into cool water to re-harden. Do this one at a time.
When twisted the the blades should look like the image.
Step 4: Joining Blades
If the blades are made of plastic, align the blades into a circular pattern with the bore holes lining up.
Now that you can see where they should line up, using a plastic adhesive join the blades together. (the order is irrelevant as long as the bores match)
Step 5: Nose Cone and Coupling
Using the PDF provided, create the pieces using blocks of steel.
In the PDF there is two separates plans, the upper 2 drawings is the coupling and the bottom 3 is the nose cone.
The nose cone should be produced using a metal lathe.
The bore diameters given are diameters of threaded holes, you must compensate for this if when drilling.
Attachments
Step 6: Base, Nozzle and Stand
Cut a base of MDF 345 by 460 by 20 mm. This will be the platform for all other parts to join on to.
Take the bucket and draw a line approximately 40 mm from the open end. Saw through this line so you are left with a tapered band of plastic.
Take another board of MDF. (approx 440 x 400 x 20 mm). On this you want to remove a circle (Do not throw away)). The circle should have a diameter just slightly bigger than the smaller side of the bucket. (so it can be glued inside the circle edge)
Nail this support into the base. On the edge with length 460mm.
Glue the plastic band inside the circle, creating a nozzle.
To stop the stand falling over, Using the removed wood, create a block of 65 x 150 mm. Separate this block into two triangles by cutting a diagonal. nail the triangular supports into the stand and base.
Step 7: Shaft Support
Cut a piece of MDF 60 x 28 x 245 mm thick. This will have the shaft threaded through.
Using a drill, on the 60 x 245 mm face (the 245 is vertical) make a 8 mm hole all the way through. The hole is centered horizontally and is 20 mm from the top edge.
Now centering on this bore, use the drill to make two holes of 6mm depth and 21mm diameter (one hole each side)
These holes are for the bearings, sand out the hole so the bearing will fit into the slot tightly.
(Optional) To provide extra support for this stand. Cut two small triangular blocks of MDF. Using wood glue, attach these triangles to the lower half of one face with bearings.
Using PVA glue, attach the shaft stand and its supports onto the base, they should be centred, bearings and triangular supports facing the nozzle. The back of the stand should be 88 mm from the opposite edge (back) of the base.
Screws should also be put through the bottom of the base into the stand to provide maximum stability
Step 8: Shaft (needs Sizes + Pic)
To make the shaft, cut a piece of metal rod (127 mm long) . In order to have the shaft at 3 different diameter's (the biggest to go through the nose cone, then the ball bearings and the smallest through the gear), it must be lathed.
All of the dimensions are shown in the image.
The next step is to thread (M8) the largest diameter 16mm long.
Finally, the shaft can be connected to the blades and nose cone.
The shaft goes through and screws into the centre hole on all of the pieces.
To tighten it, fix all pieces together with M5 bolts into the two offset holes and screw with nuts.
Now the shaft should be fed through the two ball bearings (and the stand). Once through the first (biggest) gear can be attached to the free end of the shaft and tightened using a grub screw.
Step 9: Motor Housing
Cut two perspex blocks 45 x 60 x 140 dimensions, using a band saw.
Cut the remainder of the M8 screw thread into two pieces each of length 290mm
Take one of the blocks and remove a circular section (through the 140 60 face) this is for the motor to sit inside. Again cut slighter smaller and sand for a tight fit.
The next step is to drill two holes on both perspex blocks. They should be on the 140 x 45 face. They should be 8mm diameter and located 30mm from either 45mm edge. (centered in the other direction) and all the way through.
Step 10: Attaching Perspex Block to Main Board
Drill two other holes into the base MDF located 40 mm from the centre (centre line taken from middle of nozzle and stand) and 22.5 mm from the back of the board in order to fit the threaded rods through.
Put both threaded rods through the holes and attach using super glue. (make sure they are vertical)
Next, put the first perspex block (without the motor hole) onto the threaded rods and secure to the board using double sided tape or alternatively use super glue for a more secure hold.
Put two nuts onto the threaded rod x mm up from the bottom perspex block.
Then put the second perspex block onto the threaded rods, this will sit at the level of the nuts.
Finally, secure with two more nuts and put the motor through the bigger hole in the second block. This should fit securely
The height of the upper perspex block can be adjusted. This allows (when the motor is inserted) for alignment of gears
Step 11:
Finally attach the smaller gear to the motor, securing with a grub screw.
Move the shaft (with the bigger gear ratio) back onto the smaller gear ratio and adjust height of the perspex block if need be.
Attach wire connections from the motor to a load.
Lubricate gears and finally test your wind turbine!
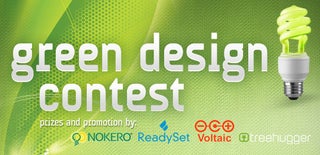
Third Prize in the
Instructables Green Design Contest