Introduction: DeskTop Steam Boiler
The unit was built entirely in my apartment with a hand drill and a rotary tool. I used a small soup can for the boiler and some various hardware store fittings to plumb the system. If your looking to make a little, attractive looking boiler to steampunk up your place read on!
Step 1: Parts
The main parts you'll need for this build can be changed wildly depending on your available materials. I picked up most of my parts from my local hardware store and a couple items from a hobby shop. The main things you need are a soup can for the boiler body, some heat resistant tubing to carry the steam around (I used model airplane fuel line), and a little bit of sheet metal to form the boiler housing (I used brass sheet) and some 1/4" copper tube to make a few connection points and the heating coil. A torch and solder are also needed to make a few connections...the one pictured is massive and while it did work I used a small handheld one for most of the connections.
Note : The vinyl tubing picture DOES NOT work which I soon found out. Silicone is the way to go for the high heat resistance.
Step 2: Boiler-1
First you will need a small soup can and a drill bit just slightly smaller then the tubing you plan to use. In this step we will drill 2 holes into the soup can to empty its contents (pick a can of something like broth or tomato paste to make emptying easier). The 2 holes in the end of the can will serve to hold a small section of tubing which will act as our sight glass to see the water level in the tank. Make sure your tubing slides into these holes quite tightly as it needs to be airtight.
TIP - flushing hot water into one hole will help move the contents out a little easier...especially if its thick expired tomato paste like I used.
Step 3: Boiler-2
Once you have the contents of your can removed you will drill the 3rd hole to work as the filling hole. I chose to use a small brass fitting and matching plug to make opening and closing the boiler easy. Once you drill this 3rd hole you want to make sure the inside of the can is as clean as possible as this is the last time you will have easy access to the inside. After sizing my hole to my fitting I gave both the brass fitting and hole a light sanding to rough up the surface to make soldering easy. Screw the fitting into the can and apply a small amount of flux to keep the joint from oxidizing. Heat the thicker brass fitting and then the can until you can easily flow the solder into the seam. Once again all joints must be air tight so take your time and do a clean job.
Once the soldering is compete clean any remaining flux from the can. The only solder I had at the time was silver solder (expensive) and general electronics solder (60/40 mix). While the silver solder is nice I don't plan on drinking from this machine I used the leaded electronics solder which worked very well on this small job.
Step 4: Boiler-3
At this stage you can cut a small section of tubing and feed it into the sight glass holes. Clean up any remaining glue reside from the can as we will be starting the boiler housing in the next step. You can also check the boiler for its "air-tightness" buy installing the fill plug, putting one end of the fuel tubing into the sight glass hole, plugging the other with your finger and blowing into the free end of the tubing.
Step 5: Boiler Housing
Here I used the boiler can to slowly bend the brass sheet to form the main support. By working the metal slowly in your hands you should be able to form a nice smooth curve. Take note of the center of your metal sheet to keep both legs the same lenght. I eyeballed the lenght to lift the boiler high enough off the ground so I could slide my heat source underneath the can. The height will vary depending on your method of heating (tea light candles, container of liquid fuel...wood fire box???).
Using a straight edge and finger power you'll need to bend 90* feet at the base of the boiler support to fasten the unit to the wood base. This step is greatly simplified if you have access to a bench vice but since I was building this in my apartment I decided to go with the finger power approach.
I then marked out screw locations, drilled pilot holes into my wood base (Maple) and screwed the unit down.
Tip - Use gloves when working with the metal sheet...while the edges may not feel sharp a small slip of the hand can yield some pretty massive slices...once again speaking from experience.
Step 6: Drilling Fill and Exhaust Ports
I drilled a centered hole to allow my fill connector to pass thru the boiler housing. When working with thin brass like this its best to start with a small bit and slowly open the hole to the size you need. Since I didnt feel like drilling larger and larger holes I marked the hole location with a sharpie then slowly cut the metal away with a cuttoff wheel on my rotary tool until I was able to fit a small sanding drum into the hole to finish the edges nice and smooth.
The small 2nd hole will allow the steam exhaust port to clear the boiler housing. You can see how I slowly cut away the black sharpie mark until I was left with a smooth hole. I used a sanding drum to de-burr the holes on the inside to ready the housing for the boiler installation.
Step 7: Steam Output and Pressure Testing
Using the boiler housing as a guide mark the location for the steam output pipe. I used a short section of copper tube which fits VERY snuggly inside the airplane fuel tubing. Once again I sanded both the copper pipe and boiler body prior to soldering the connection.
After soldering the boiler body is complete. Since we are not using a blow-off valve to prevent the tank from rupturing under a closed valve situation I decided to see at what pressure the tubing would pop off (assuming it would). The safest way to carry out this task is by completely filling the boiler and connecting line with water then using a air pump to pressurize the system. By using a large volume of incompressible water we minimize the amount of compressed air inside the boiler which greatly reduces the concussive force if the can were to rupture before a line popped off.
I used a shock pump which has a built in valve and can pump to extremely high pressures (200-300psi) very accurately to test the system. I placed the boiler in my kitchen sink, connected the pump and boiler with a section of tubing and started pumping. Out of the 3 tests I conducted the hose popped off at 50psi...a nice simple safety device.
Step 8: Boiler Supports
Now that we have a functioning air-tight boiler we need to support it inside the brass housing. I used small 1" wide sections of brass bent into rectangular cross sections. Metal this thin is easy to cut with scissors and bends easy with small flat nosed pliers and fingers. The bent supports will not sag under the load of the water filled boiler, especially once they become hot from the heat source. Your could simple use sections of threaded rod for boiler supports but I used what I had on hand (plus I have billions of those little brass screws and I like the looks of them).
To get the fuel line to slip over the copper pipe take a great deal of skill and dexterity. I found it easier to add a little water to both the tube and pipe to help them slide together smoothly. Also be sure to take any sharp edges off the tubing to keep from cutting the silicone.
Step 9: Shutoff Valve
As I also intend to use this boiler to run a small engine or turbine it was important that I could close off the steam supply to allow the main tank to build up pressure. I used the smallest 1/4" valve I could find at the hardware store and added to copper ends to it so I could attach the fuel lines to it.
Not much involved in this step, just make sure the screw together fittings are wrench tight. You want the brass couplers to compress slightly into the copper to ensure a good air-tight seal.
Step 10: Infuser Vessel
After searching around my house for a suitable container to wrap the copper heat exchanger pipes around I finally stumbled upon an old body spray can. Since it was nearly empty I depressed the trigger to clear out as much of the compressed gas as possible then using a small drill I made 2 holes in the top of the can to release any remaining pressure and allow for a way to flush out the rest of the contents. Since I planned on using a cutoff well to shorten the can I didn't want the alcohol in the can lighting from the cutting disk.
Once the can was cut to size I used a sanding drum to remove majority of the paint leaving a little here and there to add a little character. I finished off with some hand sanding to clean up some low spots and take any burrs off the edges.
The last and nearly most difficult set was bending the copper coil. If you try and bend the coil by hand (or around a form) you'll quickly see the tubing will kink. I tried filling the pipe with sand which works great but its quite hard to get the sand to pour back out considering its small ID. Finally I settled on filling the section of pipe with water and crimping the ends closed. I then carefully bent the pipe by hand to match the aluminum can and used the cuttoff wheel to trim the ends and remove the water. While this worked OK there has to be an easier way.
Step 11: Valve Mounting
As mentioned in my video I have decided to attach the valve to the base in a simple method that will easily let me remove the assembly later to try out different designs. I placed the valve on the base where I wanted it to sit and marked 4 hole locations. I then used a small drill bit to make thru holes and finally used a small end mill in my rotary tool to notch out the bottom. Through these holes I ran wire and basically twist tied the switch down.
I toyed with the idea of machining a nice channel for the valve to rest in with my CNC machine (also homemade) but came to the conclusion that not all people have a CNC machine in their apartment :) .
Note - If your interested in the CNC machine you can find my build thread (with DXF drawings of this machine) over here:
http://www.cnczone.com/forums/cnc_wood_router_project_log/118233-freeriders_table_top_mdf_machine.html
Step 12: Final Hookups
From here all the major work is complete. To fire my boiler I had planned on using tea light candles...after taking a look thru my cupboards I realized tea lights were scarce, there were none to be found. I did however have a couple copper end caps which I figured I could burn alcohol fuel with. I was going to devise a neat little wick system but decided to go with the KISS rule and simply sanded the oxidization off the end caps with some fine sandpaper and used it just like that.
Also mentioned in the video I connected the heating coil to the valve with a short section of fuel line. Initially I had the output from the coil routed to the side but I didnt like the fact that it would spit water onto my table from time to time so I ran a silicon tube back into the side of the "steamfuser" core. Not only did this solve my water problem is also helps carry the scent into the air much better...which I think is still trumped by the smell of burning alcohol, unless thats the smell your going for in the first place.
All in all I am very happy with the results of this build. I kept the cost low and functionality high. With the modular design of the steam output I can attach all sorts of little creations, now that I know the heat output of this little core I have the idea of using steam power to melt candle wax, to make candles, to heat water in the boiler. Its uses like that which make me smile. Devices built for the sole purpose of running themselves.
I hope that people take what they learned here and apply it to make the design better, smaller, sleeker or stronger. I've learned a lot from the many users of this community and thank all contributers for ideas and insight.
Happy tinkering!
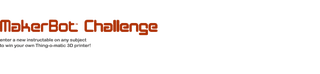
Finalist in the
MakerBot Challenge