Introduction: Still Parrot
So I was getting annoyed with not knowing the content of what was coming out of the still until I put it in a testing tube and put in my spirit hydrometer.
I knew about people who have made parrots and liked the idea of seeing the proof coming out in a more real time way than the way that I was doing it. I have been planning to make a parrot but most of them seemed very plain to me until I saw one on one of the facebook feeds I had subscribed to, I don't recall which one, may have been copper porn. anyway I figured I could make that and it looked kinda cool.
the basic princeable of a parrot is that you have a tube with your hydrometer in it, and new spirit comes in the bottom of the tube and the older stuff over spills the top of the tube and is caught by a funnel which then carries it away in a little tube and you can catch this with your jars or jugs. but because its always flowing through the main tube you can see more accurately what is coming out of the still proof / percentage wise.
Step 1: Stuff You Will Need
heres a list of what you will need
materials
22mm Copper pipe
6mm copper pipe
a small piece of 8mm copper pipe
125mm x 125mm copper plate 0.5mm thick
22mm copper end cap
35mm to 22mm copper reducer
45mm to 15mm reducer
15mm to 8mm reducer
tools
Blow torch
lead free solder
solder flux
heat proof mat
pipe cutters for the 22mm, 8mm and 6mm pipes.
a clamp
a small vice
a drill with a 6mm metal drill bit
for cleaning
dish soap
cheap vinegar
hot water
some alcohol spirit, foreshots are fine from a previous run.
metal polish and 2 lint free rags
Step 2: Making the Intake
the intake will basically be a funnel leading down to a 6mm pipe which will go in to the bottom of the main tube, for this I had to use a couple of reducers chained together as I couldn't get a direct reducer to 6mm.
Making sure you flux each part before you heat it up, this will prevent oxidization of the surfaces and allow the solder to stick to the metal better.
Also you have to make sure the top of the intake will sit well above the top of the main tube, otherwise it will just over flow the intake and you will have spirit all over the floor, so bare that in mind when you are cutting your tubes.
Solder the 15mm to 8mm reducer in to the 45mm to 15mm reducer.
then Solder the 8mm piece of pipe in to the reducer.
then you will be able to cut a piece of 6mm pipe and shape it roughly to what you need and push that into the 8mm pipe and solder that in place too.
making sure you do all this on the heat proof mat, well I say heat proof its more heat resistant so when you do this make sure you are on a work bench as you are likely to scorch the surface you are working on.
if you have never soldered before then you should be aware that you don't want to heat the joint you are working on directly, you want to heat near it but not on it, the heat will travel through the piece, when the flux starts to bubble give it a couple more seconds and then try and touch the solder on it, if it melts then use it sparingly you don't want big blobs of solder all over the piece.
Step 3: Making the Main Body
the main body will be a piece of 22mm copper pipe cut to about 26cm long, long enough that my hydrometer will sit in it all the way to the bottom but leave enough to me to grab the top of it should I need to remove it.
i'm going to use the 35mm to 22mm reducer to form a cup around the top so when the 22mm pipe over flows it flows in to the cup around it. but these couplers have a little bump inside to stop the pipe slipping all the way through, which normally in a central heating system you dont want to do that, but in this case I do.
Using a file or a dremmel you need to remove this bump so the 22mm pipe can slide right through.
now i need a 6mm hole at the base of the cup to attach out out flow pipe, I do this on the angled part of the reducer. using a center punch I put a small dent in there to stop the drill bit slipping, I could have put the piece in a vice but I chose to hold it with my hand wearing a welding glove. remove any bits of metal left around the hole using a file.
push the reducer on to the 22mm pipe, not forgetting to flux the pipe, and then using a table top or flat surface you want to make sure the top of the reducer and the pipe are at the same level, then solder the reducer in place.
at this point I made a small mistake and drilled a hole in the bottom of the pipe for inlet, later on this would prove to be the wrong thing to do.
Step 4: The Outtake Pipe
I could have just put a short straight piece of 6mm pipe in but I wanted something that supported the intake pipe, and lets face it the coiled look well it looks awesome.
to make the coil i wrapped the 6mm pipe around a wine bottle, it took a little force but I managed it.
I put the fluxed end in to the cup on the top of the main tube and clamped it to the table, I had to wedge an off cut of 8mm pipe that I flattened with a hammer under it to hold it in place while I soldered it.
Step 5: Making the Base
for the base i was originally going to use the copper place and solder the pipe directly to it, but unfortunately I didn't have any clamps big enough to hold the two while I soldered them. so I improvised and used a 22mm Copper end cap.
I had to do some measuring to make sure the new hole i drilled in the cap lined up with the one I already drilled in the pipe, if you are doing to use a cap like me it would pay to drill the hole in the cap first then put it on the pipe and drill the pipe so they match.
to drill the cap I put it in the vice and using a center punch put a small dent in to stop the drill bit slipping and drilled a 6mm hole.
then I got an off cut of 22mm pipe and put it in the cap, this would allow me space to use the blow torch later.
on the plate using a pencil I marked the middle and measured out to where the cap should sit so I would know I had it in the center.
I clamped the cap and pipe to the plate, making sure the plate was on the heat mat and that I had fluxed the cap first, then soldered the 2 in place.
I had to wait for the whole lot to cool before I could remove the pipe as the copper expands and locks the cap and the pipe together until it has cooled.
also worth noting, make sure your mat is clean, i didn't and ended up with solder on the bottom of the plate which I had to remove with a file.
Step 6: Putting It All Together
so now all I have to do is put all my parts together.
I soldered the main tube in to the cap, making sure I aligned the holes first.
then I slid in the intake tube but before I soldered it I soldered it at the top where it met the coil, this allowed me to then turn the piece on its side to solder the pipe in to the bottom of the main tube and also make the piece much more ridged.
Step 7: Leak Checking and Cleaning
at this point I checked the part for leaks, I dont want to clean it and go to use it only to find it leaks. to do this I carefully wiped all the flux away with tissue and filled it with water being careful not to spill any on the piece. This way any water on the piece is a leak, and sure enough I had one right on the intake, so I had to go back and re solder the joint to make it water tight.
cleaning the piece is easy when its cooled down, put it in a builders bucket with a drop of dish soap and fill it with boiling hot water, this should help to bring the greases off the piece and they will float to the top, then carefully pour the water way.
next I took a couple of bottles of cheap vinegar, think they cost 23 pence (GBP) each in aldi, I poured them in to the piece filling it and allowing it to overflow in to the bucket, then filled the bucket up to the top with hot water. Made sure the piece was fully submerged and then left it for a few hours, I went out to the cinema and just watched the new Robocop film, was very disappointed in it, not a patch on the original films.
By the time I got back the vinegar had done its work and removed most of the oxidation from blow torching.
I removed and rinsed the piece in clean water and dried it.
using 2 clean lint free cloths, one to apply the polish and one to remove the polish, i polished it to as shiny as I could be bothered to make it.
Step 8: Testing It Out
ok so its basically complete now but I wanted to test it out and because I didn't have a run ready I just put some foreshots through that I had kicking around and put a coffee cup under it to catch the flow.
I'm very pleased with how the hydrometer sits in it, and it looks awesome, makes me want to build a 100% copper still now to go with it.
to use this I would put the intake funnel under the output of my still, the spirit will flow in to the funnel and fill the main tube and float the hydrometer telling me what the percentage is that is coming out of the still. this over flows the pipe and is caught in the cup and is channeled away through the coil and I can then catch the output in jars or jugs.
Now I can see the percentage in real time it should make things easier when I am distilling to make the cuts on the spirit.
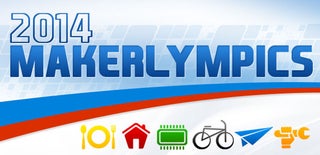
Participated in the
Makerlympics Contest