Introduction: Double-sided PCBs With a Laser Cutter
With a little practice, you can make excellent double-sided PCBs by combining a laser cutter with chemical etching. The basic idea is: the laser cutter blasts away spray painted etch resist, then chemicals eat away the exposed copper. Once the copper is gone, the underlying board can be cut again with the laser to make through-holes. No drilling required! After some setup and practice, you should get reliable boards with 8-mil trace/space and hundreds of holes in about 2 hours. You can even cut internal routing and odd board-shapes!
You'd never want to make a bunch of boards this way, but if you want a same-day prototype of a new design it's perfect. I love this process because I don't have to wait 2 weeks for boards to come back from fab, so I can design aggressively and try new ideas. If you're in a research lab or shop you'll have no trouble finding the materials, but you should also be able to find everything you need at a hardware store and pharmacy.
This Instructable will go step-by-step through the process of making a double-sided board, with special attention paid to using software to generate a good laser path, and some neat tricks to help get good alignment between the top and bottom sides of the board. Drop me a note if you've got feedback or new ideas!
The steps are:
(1) Coat PCB stock with spray paint
(2) Laser cut a spring-form alignment jig
(3) Optimize your board layout for fabrication
(4) Generate vector art for the cutter
(5) Etch away black spray paint with the laser on both sides
(6) Chemically etch away exposed copper
(7) Laser cut through-holes in the exposed board
(8) Tricks and tips for soldering DIY boards
Stuff you'll need:
Access to a laser cutter
FR1 PCB blanks (try www.inventables.com)
Spray paint (McMaster #7719T9)
6"x6" of acrylic between 1/8" and 1/4" thick (3 mm - 6 mm) for making a jig
Drill press or rotary tool with small bit (optional, but helpful for alignment)
Gloves, goggles
Non-metallic dish, measuring device, and tools
Hydrogen peroxide (3%)
Hydrochloric acid (30-37%, also called muratic acid)
Paper towels
You'll also need some access to software:
A PCB design, exported to a format your graphics program can read (I use Eagle exporting to EPS)
A vector graphics program to edit the art in. I used Adobe Illustrator.
A brief note on safety and the environment:
If you have access to a laser cutter you should be familiar with the dangers involved with that. But these instructions also guide you through copper chloride etching, which you may not be familiar with. The chemicals used are dangerous. Hydrochloric acid can burn your skin, blind you, and generates poisonous fumes. The hydrogen peroxide is reactive with lots of stuff, and the heavy metals (copper) are poisonous. Always work outside (or in a chemical fume hood), in gloves and goggles. And make sure you have adult supervision if you're under the age of, say, 40.
Finally don't put your etch waste down the drain - it will poison both people and the environment. Store it safely in a labelled container, and dispose of it properly by contacting a hazardous waste disposal agency in your area.
Prior art:
Lots of people have previously documented parts of this process in some detail. I'm a huge fan of:
https://www.instructables.com/id/Stop-using-Ferric-...
https://www.instructables.com/id/Custom-PCB-Prototy...
https://www.instructables.com/id/Printed-Circuit-Bo...
You should check these out.
Alright. Let's get started!
Step 1: Coat PCB Stock With Spray Paint.
First, you'll need to acquire some PCB blanks. I've found that FR1 (a paper and resin based stock) laser cuts much more reliably (and without noxious fumes) than the conventional fiberglass FR4. This is critical if you want to generate through-holes or board edge routing. You can purchase FR1 copper-clad in both single- and double-sided flavors at http://www.inventables.com.
Next you'll need to coat the stock on both sides with spray paint. I've had good luck with Rustoleum Flat Black (McMaster #7719T9). Go for the thinnest coat you can get that reliably coats the whole board, and error on the side of not enough paint (you can do touch-ups with a Sharpie marker later). Thin paint is important because when you blast the paint off with the laser a thin film of it will resettle. The thinner the paint layer you blast away, the less there is to resettle. Keep the spray nozzle at least 18 inches from the boards to get a light and even coat.
(BTW, I've tried a few other spray coatings - one acrylic based, and one epoxy based - to find something that didn't leave an etch resisting mist. But the flat black seemed to work the best.)
Allow about 15 minutes for the top-side paint to dry before flipping the board. Try to keep the paint on the back-side the same thickness, or else the two sides of the board may etch at different rates.
Spray painting is messy, so either do it outside where nobody will mind the mess, or do it someplace where you won't get caught. I usually do a batch of 10 or so boards at a time and keep them in reserve. Be careful not to scratch the paint when you store them. (But if you do, you can touch it up later.)
Step 2: Laser Cut a Spring-form Alignment Jig
Repeatable alignment is critical for double-sided boards because you'll put the PCB in the laser cutter three times. (Top side pattern, bottom side pattern, and then again for through-holes after chemical etching.) If the top and bottom patterns don't line up then your through-holes won't line up either; this is suboptimal. (Holes that don't go all the way through something aren't holes, they're dents.)
I found that a simple laser-cut spring-form jig made alignment much easier. The provided pattern works for 2"x3" boards, but you could adapt it for larger stock. (I've included both DXF and Adobe Illustrator files - feel free to modify them.) 1/8" (3 mm) acrylic works fine for this, but you can go all the way up to 1/4" (6 mm) if that what you've got. Careful attention to the alignment of the jig can make sure the top of the PCB is in register with the cutter's coordinate system.
(1) Cut the outline out of acrylic stock (you'll need about a 6"x6" square) , then place the cut piece against the top left of the cutter's bed stops.
(2) Now cut the interior pattern. Align the top left of the pattern to [0.50",0.50"] in the laser's coordinates. This places the top left edge of the held PCB at [1.00",1.00"].
(3) Raster the text annotations on the top of the jig. (... if desired. These are only included in the Illustrator version of the files.)
Now you should be able to flex the springs in the jig to hold a board against the top left corner. Don't over-do it. Acrylic is very stiff, so you can snap it by over-flexing. But the attached design for 2"x3" boards includes stops that should prevent this. Also, don't try to mount a board in the jig while it's on top of a cutter's honeycomb bed - you'll scratch paint off the underside of the board as it scratches across the metal.
Attachments
Step 3: Optimize Your Board Layout for Fabrication
Creating good PCB layouts is a big topic and different boards have different requirements, but the DIY process imposes a few more constraints. Here are some suggestions for making your boards easy to build:
(1) Design trace and space conservatively. You can probably get 8/8 mil traces, but you'll need to watch the etch closely. So, make as many traces as you can wide and well-spaced. In the sample design pictured, the smallest traces are .016" wide, and lead to a 32-TQFP package in the center.
(2) Remember that through-holes won't be plated. So if a component has traces that lead to it on each side of the board, you'll need to solder it on each side. For some components that's easy, but others - particularly connectors with plastic flanges that sit flush against the the board - it's impossible. So, only run traces to components on the side of the board that you can solder. (You may also be able to get creative. For example, the pins in many 0.1" headers can slide through the plastic shroud. Hiking up the shroud can give you space to solder, and then you can slide the shroud back down.) This sample board is designed so connectors are only soldered on the top (red) side.
(3) Make your vias large and rare. Because through-holes aren't plated you'll need to insert a piece of wire in each one and solder it on both sides. (If you via under another part, make sure you solder the via first!) So make your vias big enough for the wire you use. A 25 mil hole on a 50 mil pad is convenient and robust.
(4) Your board won't have soldermask, so it will be harder to solder than a commercially fabbed PCB. Thus, be conservative running traces by pads, especially top-side pads where you need to solder around components. It's worthwhile to think through the order that you'll install components to make sure you can actually get an iron to all the places you need to.
(5) Add a couple of extra holes (or large unconnected vias) in unused areas. These are extremely useful for checking alignment.
(6) Your board also won't have a silkscreen legend. Usually you can get by ok if you have the design printed on paper nearby, but if your design is dense, repetitious, or convoluted it can get confusing. I usually add some unconnected copper features to act as markers. For example, in this design a small dot of copper marks the top right corner of the 32-TQFP package in the center.
(7) Once you've got a design you like you're ready to export your art. However for the holes, unlike a traditional process in which you would generate a drill file, you actually want an image of the holes. In Eagle, for example, you can generate this by choosing from the File menu: "Run ULP..." and selecting drill-aid.ulp. (Set the center-hole size to 0.) This produces an image of all though-holes in layer 116.
(8) You'll want to output several files (board outline, top copper, bottom copper, and holes) in a format that your graphics program can view. Eagle can generate EPS files, and the attached laserPCB.cam file is setup to pull the appropriate layers automatically. Choose from the File menu: "CAM Processor..." then choose "File > Open > Job" and open the supplied "laserPCB.cam" and click "Process Job" to generate the files.
Attachments
Step 4: Generate Vector Art for the Cutter
Now that you've got images of the copper and holes for your board, you'll need to import them into your graphics program for post-processing. I've written out these instructions for Adobe Illustrator, but you should be able to accomplish similar effects in other vector graphics programs. The goal of this process is to convert the art into continuous paths that outline the traces for the laser to follow, and also to offset the paths to account for the laser's beam width.
Why not just use the laser to raster away all the paint except on copper traces? Whenever the laser blasts away paint, it creates a fine mist which resettles (even on cleared areas) and resists etching. To fix this we try to remove as little paint as possible (so there's less mist) and make multiple passes. Using this "isolation etching" method is also more efficient when we chemically etch, because there's less copper to dissolve.
(1) Open all of the EPS files in Illustrator, and copy and paste their contents into separate layers of one document. (Using [Ctrl]-F to “Paste in Front” will ensure that the layers maintain their alignment.) Make sure that all of the board outlines are aligned so that your layer with the holes will remain in registration with the copper traces. You should now have separate layers for the board outline, top copper, bottom copper, and holes. (The CAM processor outputs separate files for top and bottom holes. The astute reader will recognize that holes, being holes, go through the top and bottom layers, so these files should be identical. Pick either one and use it!)
(2) Separately for the top copper, bottom copper, and holes layers do steps 2a-2d:
(2a) Select the traces (but not the board outline), and run Object > Path > Outline Stroke to create paths around the outside of each of your trace segments.
(2b) Now set the trace width to .001”, the trace color to Red, and the fill to unfilled. (This may vary depending on your cutter settings - choose the trace properties that generate a vector cut.)
(2c) Select all of the traces (but not the board outline). Now in the Pathfinder pallet, run “Unite” to merge overlapping paths to create one continuous outline of each copper trace. This will fill-in any ringed-in structures. It’s uncommon to have these, but if you do you’ll need to copy them into another layer before running this command. It will also remove the holes at the center of pads in the copper trace layers, but that’s ok, because we’ll put them back in from the “Holes” layer.
(2d) Now we’ll account for the laser beam width. Our laser's cuts are usually about .008" wide after etching - you'll get a sense of this after making a few boards. Select the traces and run Object > Path > Offset Path. For the offset value, enter half of the laser’s cut width (Our laser spot is .008" wide, so we enter .004" This value can be a little hard to predict, because it depends on laser power, and because the etching process also makes the cuts a little wider. You'll get a sense after making a few boards). If you want wider traces, increase this value. If you’re doing this for the holes layer, enter -.004”. This will make the insides of holes smaller to account for the width of the laser beam spot. Illustrator won't remove the old paths, so you'll need to cut and paste the new offset paths to a new layer. (The new offset paths will be the only ones selected after running Offset Path, so just [Ctrl]-X to cut them, make a new layer, and [Ctrl]-F to paste them.)
(3) If you want to laser cut a board outline or any internal routing, remember that you'll need to etch the copper away first in order for the laser to get through the board, so you'll need etch traces for those on both sides. Put them on a separate layer so you'll remember to do that.
(4) Set the board outline to be in a different color that won't generate cuts. You don't want to delete it, because it's often helpful for aligning the art to the cutter's coordinate system.
(5) We're isolating traces off of the background copper, but leaving that background copper in place. Consequently, if we accidentally short multiple traces to that background copper it results in connections we don't want. You can give yourself a margin of safety by breaking up the copper background by drawing a few etch lines across it. This makes it less likely that you'll accidentally short more than one signal to the copper background, and makes it much easier to diagnose if you do, since you only need to check the borders of a small region of copper. Just don't accidentally draw cuts across any of your traces!
Step 5: Etch Away Black Spray Paint With the Laser on Both Sides
Now we'll actually start lasing!
You'll want to make a few test etches before you do a whole board in order to figure out how much power to use. A few hints:
(a) Use the tightest focal spot lens you can find, and make sure you're precisely focused on the top surface of the board. A wide beam spot will make the separations between your traces too wide (and your traces narrower).
(b) Use enough power to get through the paint, but too much power will make the cuts wider.
(c) Run multiple passes. I've found 4 works great. The subsequent passes don't widen the cuts much, but remove the paint mist that has re-deposited in the cleared traces. After 4 passes the exposed copper should be brilliant and shiny, with no visible dull black residue.
Once you've got settings you like, you're ready to start etching the board.
(1) Place the board in the jig, and the jig against the stops. You can keep the metal bed honeycomb from scratching the board by putting a spare sheet of acrylic underneath the board and jig. (You won't burn through the board on this step, so it won't be harmed.) This should put the top left corner of the board at [1.00",1.00"] in the laser's coordinates. When you move the red sighting beam to [1.00", 1.00"] you should see it scatter off the corner of the PCB.
(2) Align your art so the top left of the board outline is at [1.00",1.00"].
(3) Now have the laser etch both the traces and the holes; do 4 passes sequentially. We need to etch paint away from the hole outlines to clear the copper off of them so we can laser cut the through holes in a later step.
(4) Remove the board from the jig. The jig helps with alignment, but if the PCB stock size isn't exactly 2"x3" this will still result in misalignment when you flip the board to do the bottom side. To check for this, pick one of your through-holes or vias outlined by the etching and use a drill press to drill a through hole through to the other side. (Most common through-holes are .040".) Using the extra unconnected holes you've added to your design makes this much easier, because you don't have to worry about missing and accidentally drilling through a pad. Centering a drill on a small pad can be hard. If your hole is a little off-center don't sweat it. Just use the drilled hole as a reference to make sure that the pattern is mis-aligned the same on both sides.
(5) Now flip the board over and place it in the jig. I've found that flipping up-down gives better alignment than flipping left-right, maybe because the 2" board dimension is more precise. Remember to also reflect your art about this axis, either in Illustrator or your cutter driver, to account for the fact you flipped the board!
(6) Pick out the path for the through-hole you drilled for alignment, place it on a separate layer, and try etching just this hole. If your alignment is off and the etching isn't concentric with the drilled hole, add some offset to the laser's coordinates and try again until you get a good match.
(7) Now etch the bottom-side traces and hole outlines using the same process you did for the top traces. (Again, do 4 passes.)
Step 6: Chemically Etch Away Exposed Copper
Now that you've exposed some copper on both sides of the board it's time to etch it away. You can use store-bought ferric-chloride etchant from your neighborhood hobby-electronics store, but that stuff is pretty gross, and I've had good experiences with a copper chloride process. Because both of these processes use acids and heavy metals they are potentially dangerous both to you and the environment: wear gloves and goggles, and do this outside or in a chemical fume hood. Don't pour the chemicals down the drain - store them in a non-metallic closed container and take them to a hazardous waste disposal facility.
You'll need:
Gloves, goggles, and old clothes (or a lab coat)
3% Hydrogen peroxide (standard from the drug store)
37% Hydrochloric acid (also called Muratic acid, sold for swimming pools)
Paint thinner (turpentine or acetone)
Non-metallic (glass or plastic) container and measuring cups. (The etch will dissolve metals. That's the point.)
Plastic forceps, plastic tongs, toothpicks, transfer pipettes, or feathers.
Paper towels.
Before you start, closely inspect the board to make sure all the areas you don't want etched are still covered by black paint. If you've got some missing coverage (sometimes the laser cutter's honeycomb bed can scrape away paint) clean it up with a Sharpie marker.
(0) Glove and goggle up! Safety first. Helmet optional.
(1) Pour 2 parts hydrogen peroxide in a non-metallic (plastic or glass!) container. About a half-cup (or 100 mL) is a reasonable starting volume.
(2) Slowly add 1 part HCl (probably 1/4 cup, or 50 mL). This will give off some heat. Do it slowly, and add the acid to the water, not the other way around, and avoid splatters.
(3) Place the board in the etch, wetting both sides.
(4) Gently shake the container to move the fluid and board around. Using plastic tools or toothpicks can help position the board. A transfer pipette or eye dropper is useful for squirting away bubbles that form. A feather can do the same job.
(5) After a few minutes you'll notice the etch starting to turn green as copper is dissolved. Every few minutes flip the board and continue to agitate.
(6) After a few minutes pull the board out, dunk it in tap water, and check out the traces under a magnifying glass or microscope. You should see some areas where the reddish copper has been etched away to expose the underlying tan or grey substrate. Place it back in the etch, making sure both sides are wetted.
(7) Keep checking the board every few minutes to see if it's done. Error on the side of under-etching. Usually there will be a few stubborn spots that resist etching; cleaning those up with a razor blade is a lot easier than trying to ensure continuity in a bunch of moth-eaten traces that were over-etched.
(8) Once you're satisfied with the etch, immediately rinse the board in running tap water for 30 seconds, then immediately remove all the paint with paint thinner and paper towels. If you don't immediately strip the paint, acid that's been absorbed into it will continue to slowly etch the underlying copper, and you'll wind up over-etched.
(9) You can usually get several uses out of your etchant but it will need to be recharged once it's a deep emerald color. Remember to dispose of the waste in a safe and environmentally responsible manner. If you're going to store it, make sure it's in a sturdy non-metallic container, clearly labelled, and marked as poison.
Step 7: Laser Cut Through-holes in the Exposed Board
Now that you've etched away the copper around your through-holes the laser cutter can cut through the exposed FR1 substrate. Put the board back in the springy jig, and again align your image of the holes layer to the cutter's coordinate system. Again, it's often helpful to check your alignment and laser power by trying to cut a single test hole. Since the exposed copper largely reflects the laser, you can tolerate a moderate amount of misalignment at this step - only the exposed FR1 will cut through. However, you can get enough charring to crumble the substrate under pads, so you want to set the laser power so that it gets through the board on a single pass, but doesn't char the hole edges more than necessary.
Once you're satisfied with your test hole, go ahead and cut them all. You can also cut any routing or board-outline shape you've made, provided you've already etched the copper off of it. If you're aligned well you should get clean holes through the whole board, and won't need to re-cut the holes from the backside of the board. If you've got some misalignment then sometimes a second pass (perhaps from the back-side of the board) can help the cuts from each side get deep enough to meet, but at the risk of potentially burning the substrate supporting some of the pads.
The hole plugs may not fall out cleanly by themselves. Poking with solid-core wire should pop them right out.
Laser cutting the holes is really helpful for boards with a ton of holes that would take a lot of work to do manually on a drill press, or many-pinned parts that misalignment of a few pins might make difficult to insert. It's also great for odd-sized holes that you might not have a bit for, or for doing routing to cut the board to a new shape.
Step 8: Tips and Tricks for Soldering DIY Boards
Now that you're done making the board, a few tips and tricks for actually stuffing and soldering them. Since these require soldering on both the top and bottom and don't have any soldermask they're a little tougher than a commercial board, but not impossible.
(1) Visibility is the name of the game: you can solder whatever you can see. Even small pitch pads are easy to solder with a fine tip, as long as you can see them. So take some time to set up a magnifying glass (on a holder) or find an old dissecting microscope.
(2) You can use solder paste and a reflow oven (or hot plate) for fine surface mount parts, but I've found it's more trouble than it's worth. You really can solder tiny parts quite easily with good visibility. But if you do try to reflow, consider laser cutting a mylar solder paste stencil - they work great.
(3) Check trace continuity and isolation with a multimeter before you solder components. It's way easier to use a razorblade to separate a few areas of incomplete etch (or a bit of solder to clean up a wispy over-etched trace) before there are components in the way.
(4) Consider tinning your pads before you try to solder to them. It's really quick to use a hot iron to melt a little solder on each pad, and it'll make soldering components far easier if the pad already has solder wetting it. This is especially true for surface mount pads.
(5) Solder the vias before stuffing any other components. Use stripped solid core wire, solder it on both sides, then use clippers to clip it flush.
(6) Be careful that you don't lift pads when inserting leads. If you cut a misaligned hole then you might lift the edge of the copper off of charred substrate. Just go easy. When this happens the pads then to fold rather than break, so you can usually bend them back into shape with forceps or a well-placed fingernail.
(7) Be strategic about what parts you place first. I usually start in the center of the board and work my way toward the outside so tall parts (TO220 packages are big culprits) don't block the soldering iron's access.
(8) Have some solder wick handy for cleaning up inadvertent bridges. However, bridges can often be cleared just by running a hot iron tip down the groove between traces.
(9) These boards are really for prototyping, but if you need something rugged, consider coating it (after all the components are soldered) with a hard insulating epoxy spray.
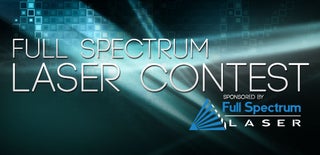
Participated in the
Full Spectrum Laser Contest