Introduction: Dragonfly 3D Fold-up
My metal direct class this year had the fantastic opportunity to visit a company called FedTech in MN. They were nice enough to help our school (St Olaf College) by printing a few small metal laser cut images.
I decided to sketch of a dragonfly in 2D using Graphite (http://www.ashlar.com/2d-3d-drafting/2d-3d-cad-graphite.html) and then I drew in fold-up tabs that would enable it to turn 3D.
After submitting the files, we went to their lab and watched the process as the giant laser cutter did its work. From here, I folded my dragonfly up along the perforations I had drawn in earlier.
The finished product didn't exactly turn out as nice as I wanted it to (the tail wasn't long enough) but the wings for sure turned out pretty gossamer, just like real dragonfly wings. I love the wings :)
Step 1: The Sketch
You can use whatever CAD software you want so long as it supports saving as a .DXF file. I used Graphite and it worked splendidly. It was my first time using it and I had my doubts at first, but I love it now :)
The dragonfly sketch is saved below. Feel free to do whatever you want with it!
You will notice that the entire dragonfly is at the top of the image and then halfway down it mirrors (kinda) so that the dragonfly can fold the belly underneath the top half so as to have a real 3D model.
Two corrections (possibly 3):
the legs don't quite work as drawn (the are directly flush with the wings and two short to reach the ground)
the bottom of the head doesn't quite line up with the body. I would make the body side flaps thinner to avoid this.
the tail is too long. I knew this going into the drawing since I was confined to a certain amount of space.
If you have any questions, post them either by messaging or in the comments below.
Attachments
Step 2: Laser Cutting
The drawings were cut at FedTech. Thank you FedTech! There is not much to say about this step except that I had to punch out the little hexagons that were a little stuck in the wings (they had been cut but didnt fall out).
Step 3: Fold It Up!
Carefully and forcefully bend each tab along the perforation (the dashed cut-outs). Using a couple of needlenose pliers or a regular pliers along with some assistance of a table clamp will be integral. Try and make them all 90 degree folds. The tiny folds between the tail segments were particularly difficult. Just try to fold the shape as accurately as you can. It is important to fold the smaller tabs first (the outermost tabs) and then work your way in (inner perforations) so that you can apply the force in the least awkward manner (AKA not squirming needlenose pliers through a mess of folded metal).
And thats it! Take a look at the images on the introduction step to see the final product! This project does not take too long and can be finished in a couple days. But you will need access to a laser cutter to do this as I did. For an interesting lead, google FABlab. The FABlabs around the world are brilliant places. USE THEM!!!!!! ibles and FABlab seem like a perfect partnership to me.
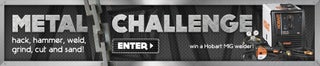
Participated in the
Metal Challenge
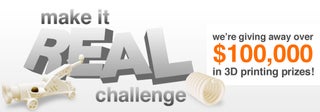
Participated in the
Make It Real Challenge