Introduction: Dueling Electric Chairs
Every year my wife and I throw a pumpkin carving party the weekend before Halloween. We use our unfinished basement for the event where we have friends over to carve pumpkins, eat food, watch movies, and participate in general Halloween mayhem. We have a tradition of doing a prop room in one area of the basement for the enjoyment of the guests and to help set the mood.
The past several years have had stationary props, almost like a life size dioramas. So to help take things to the next level I decided to make a pair of electric chairs. One chair would have an animated dummy that would jump around when a button was pressed. The other chair would be an interactive prop, where guests could sit in it and get a simulated shock.
Step 1: Chair Design
The first step is to build two wooden chairs. I spent some time doing internet searches for images of electric chairs. I created a chair design that was based upon several different chairs, taking aspects that I liked from each and combining them. I took a little extra time on the design so that I could make up for my lack of carpentry skills. I intended to do all my joinery with glue and wood screws.
I also created a drawing to help keep track of the lumber I would have to cut. The attached PDF lists the lumber required for a single chair. The first page has a bill of materials that I used for my master cut list. The last five pages show dimensions and angles for the parts that needed cuts that were more complicated that just square cross cuts.
Attachments
Step 2: Cut and Assemble the Lumber
Safety first! Please read all manuals for your tools, know how to use them and wear/use the appropriate safety equipment.
I wanted nice square edges so the chairs would look more realistic and not just something that was put together from dimensional lumber from the local big box store. To accomplish this I buy lumber one size bigger and rip it back down to the required size. For example if I need a 2x4, I buy a 2x6, and rip it to a width of 3.5". I cut about 1/4" off one side, then remainder of the material to be removed off the other side. Another advantage to this is once I rip the boards on the table saw I know I have nice square boards, so this requires less carpentry skills on my part, and things are more likely to fit together the way I designed them to.
Step 3: Finish It!
The finishing process for the chair went as follows; Distress, Paint, Sand, Stain
To get a finish on the chair that would look like it had seen some use, I took it outside and beat the snot out of it with a chain. Apparently Martha Stewart keeps a length of chain handy just for such occasions. This step was tough the first time, I had just spent all this time making a nice, square, and true chair. I then proceeded to abuse it with various metal implements like something out of a horror movie. The chain was pretty versatile, it could be used as a lash, like dental floss, or by sliding it up and down the length of the boards. Besides a chain, I found the edge of the head on hammer made nice groves in the wood. I would recommend doing twice as much distressing as you think is sufficient.
Next I painted the whole chair black. I used a general purpose flat black spray paint. The idea here is to add a dark used look. One coat was sufficient, I was only looking to have the paint stay in the cracks of the wood and the dents and scrapes from distressing.
Once the paint dried I got to work sanding it. I wanted to remove the bulk of the black paint but still leave some behind where it looked appropriate. I was picturing the sweat and body oils of countless convicts be release as they took their last breaths. I did most of my sanding with 100-150 grit sand paper so that it would leave a fairly smooth surface, but still leave the pores open to take the stain. I did run some 40 grit paper over the seat to give it some nice scratches for the stain to soak into. After sanding I blew the dust off and wiped the whole chair down with a microfiber cloth.
For the stain I chose a color called "Early American", it seamed appropriate somehow. I tried both the version that comes in a spray can and the stain in a can that you apply with a sponge/rag. The spray went on easy enough but for the second chair I used the stain in a can and spread it on by hand. I was much happier with how the wood took the stain in the hand application. Let the stain dry over night and you are all set.
Step 4: Build a Frame for the Dummy
For the chair that had the animated dummy in it I built a frame out of PVC pipe to act as a skeleton for victim. I decided to make the frame from the waist up, I didn't want the legs to move. The forearms of the dummy would be strapped into the chair so I didn't worry about incorporating them into the frame either. I made the frame in two sections, separating the dummy at the diaphragm. I did this so I would have a compound motion, hoping it wouldn't look like the dummy had a metal rod down his spine. I joined the two sections together with a block of wood I called the sternum. This is also the anchor point I used to transmit the motion from the actuator. I did a dry fit to make sure I had all the pipes to the correct size, then I used PVC cement to glue them all together. It wouldn't do to have them coming apart.
Step 5: Motion
Now that we have a frame put together, we need to make it dance. A friend donated his old jigsaw for the cause. This particular model had a slider switch for the speed, which was nice because you could set it to a specific speed and it would stay there. If you have a newer trigger model you could always use a pipe clamp or zip tie to compress the trigger. I wanted to have the jig saw always on and use a relay to turn it on and off. The jig saw also had a couple of threaded holes in the shoe, so I was able to use a couple of machine screws to mount it to the back of the chair through the board on the back. I had to cut a slot in the back board so that I could transmit the motion to the frame of the dummy.
To attach the jig saw to the frame, I picked up a metal strip with holes in it from the hardware section of the local home improvement store (sorry, I don't know the official name). I was able to notch out the end so that it would fit right in the blade chuck on the jig saw. I drilled smaller holes to use wood screws to attach the metal strip to the sternum block. I also bent the metal strip 90 degrees so that I could attach it to both the top and front of the sternum block to make it more robust.
At this point you should be able to power on the saw, please be careful as you will have thing moving under their own power. You can adjust the speed of the jig saw to see how the motion of the dummy will vary. There was definatley a sweet spot where I reched a natural frequency for the dummy that really got him jumping.
Step 6: Who's the Dummy Now?
The next step is to build up the dummy. I bought a convict costume from a Halloween store, and made some strategic cuts in it so it would fit around the frame. I used polyfill from the craft store to fill out the chest. The legs were made from rolled up cardboard. I had an old pair of boots for the feet. For the forearms and hands I have a favorite pair of severed arms I picked up from the Halloween stores that have a nice realistic look to them. For the head I picked up a styrofoam head from a beauty supply store for a nice price. I mounted some LED lights in the head so that the eyes would glow when he was being electrocuted. I covered the head with a burlap sack. This way I didn't have to fabricate a face. The burlap allowed the light from the LED to shine through with out being able to see the raw foam of the head.
Step 7: Restraints
Being that it is an electric chair, we will need to restrain our victims. For this I used some leather I had left over from a previous project. A trip to the local Tandy Leathercraft store supplied the required buckles and rivets. Each chair requires two wrist straps, two ankle straps, and a chest strap. Mulitply that by two chairs and you get a lot of leather cutting.
Electric chairs also have some sort of headset. I wasn't happy with the metal bowl look I got from using the shroud from a work light, so I decided to fabricate them from aluminum bar stock. A make shift anvil and some hammering later we had a couple of headsets. I used a panel mount conduit coupling to attach the headset to the conduit that was strapped to the back of the chairs.
Step 8: Dummy Controls
I took two videos showing the sequences, unfortuatley the phone I used to take the video didn't do well in the low light situations. So for the second video I added extra light, not as spooky, but that way you can see what is going on. For some added ambiance, I also built a pseudo fence to divide the room and make it look more like a prison. You can see the fence in the video.
Video Showing the sequence:
Video Showing the sequence with extra lights on so you can see what is happening better:
Step 9: Good Vibrations
For the second chair I wanted it to be interactive. I didn't want to actually electrocute anyone, so I figured I could use vibration to simulate the sensation of being shocked.
I made two handles for the user to hold, I made these out of copper pipes. I wanted the copper to have a little patina on it, so to give it a greenish tinge I placed the pipes in a plastic baggie with a couple of boiled eggs I smashed up. Apparently the sulfur in the eggs reacts with the copper to accelerate the oxidation process. Go chemistry! I bought some pager motors, but they didn't have enough vibration for my liking to be in the handles. So I bought some 9V 10,000 RPM DC motors and crimped lead fishing weights on the ends. I used hot glue to mount the motors in the pipes and then screwed the pipes into the arm rests.
On the underside of the arm rests I routed a 1/4" channel to hide a CAT6 cable. I used two of the leads to power the motors, and the rest I bundled and attached to the screw that attached the pipe to the handle. This way I could used the handle as a capacitive sensor on the input to the Arduino that was controlling the chair. One of the output pins on this chair's Arduino was tied to the input pins on the other Arduino so that when it was activated it would trigger the lights too.
Since I now had extra pager motors I decided to attach them to the head set. I cut up a pen, and used the pieces to mount the pager motors into. I glued these onto the sides of the headset and then covered them with leather. The leather gave the headset a nice old, creepy feeling. It also made it a little softer where people would have it against their skin.
On the under side of the seat I mounted a pair of old hair clippers. The hair clippers gave off a really nice hum, and they have a sharp crack when they are first fired up. I screwed the clippers directly to the under side of the seat boards using some pipe straps.
The control algorithm was once someone touched both handles simultaneously, the chair would start. Both the hand and the head vibrators would start out at a low power and then ramp up in an oscillatory fashion until they reached full power. Then there would be a random delay and the seat vibrator would go off. The random delay kept users from being able to guess when the last "kick in the pant" would come.
Step 10: Have a PAR-TAY!
I would like the thank Glen and Ira for their help in building this project. I would also like to thank my wife who put up with me sequestering myself in the basement for a couple of weeks during the fabrication. And I would like to thank everyone who attended our party, that is what really made it a success. Happy Halloween everyone!!!
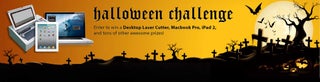
First Prize in the
Halloween Decorations Challenge
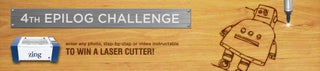
Participated in the
4th Epilog Challenge
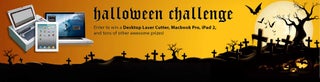
Participated in the
Halloween Props Challenge