Introduction: Easy DIY Vacuum Former
I have always wanted to build a vacuum form machine and when I built my latest robot ( Click Here) I finally had a reason to. I needed to make a shell or top to my robot and I didn't want to mess around with fiberglass and all of the grinding and sanding. So here is my instructable on how to build an easy vacuum former with stuff you can buy locally. I have added some videos below. If you like my project please vote for me.
Step 1: Supplies Needed
These are the supplies that I used to build mine. You can certainly use whatever you have handy to build yours. I wont give many measurements for this because you can adjust everything to what suits you. And it is very simple to build. If you have any questions let me know.
- 1"X3" boards
- 1"X2" boards
- Plywood
- Pegboard
- Screws (I used drywall)
- 1/4" bolts, washers and nuts
- 1 1/4" Hole saw or drill bit
- Weather strip
- Big cardboard box
- Aluminum foil
- Caulk
- Garage Heater
- Shop Vac
- Plastic of your choice (ABS, Lexan, Polystyrene...)
Step 2: The Base
I first started out by cutting my 1X3 boards and making a frame. I pre-drilled the holes in the ends so the wood did not split. I ran 2 Screws in each end. I then drilled and screwed plywood to the bottom of the frame and caulked all of the inside edges. Then I drilled a 1 1/4" hole in the front for the vacuum to attach to later. Then I cut a piece of pegboard an placed it on top of the frame. I marked about every 3 holes, then pulled the pegboard back off and pre-drilled all of those marked holes in the frame. Then I caulked around the whole top of the frame and placed the pegboard back down and screwed it to the top of the frame. The caulk did squish out some but it wiped off easy. Once this drys you will have nice sealed box except where the peg holes are.
Step 3: Finish Base
To finish the base I took some 1X2 and attached it around the pegboard making sure to be flush with the pegboard and not to cover up the vacuum hole in the front. I attached this with screw through the face of the boards. Then I lined the top of the 1X2's with weather stripping. I used silicone since I know high temps will be involved. You need this strip to insure a good seal for the vacuum to give a nice forming detail. I used adhesive back strips.
Step 4: Material Frame
Now its time to build the frame that will hold your material to melt. I used 1X2's and laid them on their sides and screwed them together making a frame. You have to build 2 of these frames. Then I clamped both frames together (not shown) and drilled 1/4" holes on all 4 sides, I drilled 3 on the long sides and 2 on the short sides. As you can see in the 3rd picture that is the frame with just the holes drilled through it. The 4th picture shows the other frame with the 1/4" bolts sticking through it, and the last picture shows them together with no material in the center.
Step 5: Heater Box
My heater box is very low tech and you can make yours anyway you want but mine definitely gets the job done. I used a big cardboard box, big enough to hold my heater on the inside, and I lined the inside of the box with aluminum foil to keep it from burning it. I used a garage style Quartz heater for my heating source. I had to disable the "tip over" switch and the overheating switch to make it work. I laid the heater on its back and set the box on top of it. I had to cut a flap of the box out on one side so the heater could stick out because it was too big to fit. You have to play around with the height of the box because you don't want it to be too close to your plastic and melt it too fast but you don't want it too far away and never heat up. The last picture you can see that I just took a board that was laying around and put aluminum foil on one side for a lid. I don't know if this is necessary or not.
Step 6: Preperation
I have used Lexan, ABS, and Polystyrene and all of them work well. The Lexan is harder to melt though. In the first picture you can see that I cut the Polystyrene to fit between the 1/4" bolts in the material frame that I made. The next picture shows the two halves smashing the material between them by putting the washers and nuts on the frame. In the next picture you can see a mold that I made that I want to make a plastic shell from. You have to make sure it fits on top of your pegboard and does not overhang. I set my part to be molded on top of some thin boards to raise it up a little to allow air to flow under the part and suck the plastic under it. Then I placed the vacuum hose into the front of the base now ready to start molding. and the last picture is the final piece after it has been trimmed.
Step 7: Final Forming
I don't have any picture of when I was actually forming the material but you can watch my videos at the beginning of this. But I will walk you through the steps here. First turn on the heater and let it warm up for a while. Then place you material that is in the frame on top of the box. I then placed the lid over top of this but you might not deed this step. The plastic will start to warp, this will last about 15-20 minutes or so depending on your heater. The material will then start to sag in the center. You know when the material is ready when the edges and corners are pliable and stretchy. Sometimes I use a heat gun to speed up the heating of the corners. When you material is ready, turn on your vacuum, grab the material frame by the sides, pick it up and smash it down on top of your mold making sure it is limed up with the weather strip and push down hard so the weather strip will seal and let the vacuum do the magic. Keep it held down for a minute or so to let the plastic cool. Once it is cool, turn off the vacuum and pull your mold out of the plastic and you have your vacuum form mold.
If you have any questions please let me know. And if you liked this, please vote for me.
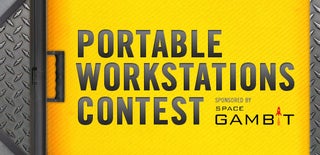
Participated in the
Portable Workstations Contest