Introduction: Electric Brewery Control Panel on the Cheap
If you are into home brewing then you have likely heard of "The Electric Brewery" created and run by a fellow named Kal. If you haven't then get over there and read up. This is the best homebrew setup out there, well thought out, well designed and effectively open source. It uses electric hot water heater elements, a three-kettle two-pump setup, and a process control panel to bring your home brewing to a new level of awesome and easy. Kal has designed a top-notch, no-compromises system that is safe, enjoyable and easy to use. However, it is expensive. Also, Kal is an engineer by training, and as a fellow engineer I cannot possibly leave well enough alone and must change his design. This is job security which is bred into all engineering types. You can substitute fittings and pots and pumps to reduce system cost, but the heart of the "Electric Brewery" system and one of the costliest is the control panel. Here I will show you how I redesigned Kal's control panel with cost in mind, bringing the cost down from around $1500 to $250 without compromising safety and with only a few compromises in function. I can attest to the fact that this control panel works and makes great beer. If that sounds good to you, then read on!
Step 1: Bill of Materials
The key to designing this kind of control system on the cheap is flexibility and availability. If you stick to the recipe strictly you may find that you cannot source the specified part locally or economically. Also, depending on your system you may be able to substitute a lower cost lesser performing part safely. So here I am going to present the parts that I used and you can use them as a guide for sourcing your own. In some cases the parts are from the internet and anyone can get them while others are local surplus and you might need to sub. I'll go into detail on what you should look for when choosing parts as needed. So without further ado:
Electronics:
3x DPST-NO 30A 120VAC relay (PN# G2290127 at www.zoro.com/)
3x REX-C700 PIDs (www.dealextreme.com)
2x 60A SSR (www.lightobject.com)
2x 60A SSR heatsink (www.lightobject.com)
2x 30A 250VAC locking 3-wire receptacle (www.homedepot.com)
1x 15A 120VAC two outlet receptacle (www.homedepot.com)
1x 30A 240VAC 6 foot 4-wire dryer cord (www.homedepot.com)
1x Keyswitch (local suplus but this one should work: www.amazon.com)
3x XLR 3-pin male socket (local suplus but this one should work: www.amazon.com)
1x 3/4" cable clamp = $1 (home depot)
2x On-off toggle switches (local suplus but this one should work: www.amazon.com)
1x On-off-on toggle switch (local suplus but this one should work: www.amazon.com)
2x 240V lamps (local suplus but this one should work: www.amazon.com)
Misc spade and ring lugs
Terminal strips for wiring buses (local surplus but similar to: www.amazon.com)
Enclosure:
1/8" Birch plywood (approx. 6 square feet)
Scrap 1/2" plywood or solid strips for frame and back and sides
Titebond III wood glue
Screws for mounting components and securing sides to enclosure
Step 2: Design Changes
A number of features are eliminated from the control panel presented here as compared to the one designed on the Electric Brewery. The purpose being to simplify the design and reduce cost. The cheap design eliminates the safe start interlock, the alarm buzzer, the alarm light, the alarm reset button, the power on light, the voltage panel meter, the current panel meter, the process timer, the alarm selectors, the pump lights, and the metal enclosure. None of these changes significantly impact system safety but substantially reduce component count and wiring complexity.
That said, a number of additional system changes could be made to further reduce cost. For example, in actual operation, the only temperature of consequence is the HLT (hot liquor tank) temperature. Similarly, this is the only temperature that requires control. As a result we can eliminate the temperature probes, the XLR sockets, the PID controllers for the mash tun and boil kettle. The boil kettle will still need some control to allow increasing or decreasing heat input. This can be accomplished with a basic PWM (pulse width modulation) circuit that is adjustable in duty cycle via a simple potentiometer. This would directly drive the boil SSR.
Step 3: PID Modifications
The selected PID controllers are quite inexpensive but they do not have the correct output to drive the SSR. As purchased the PID will have a relay output meaning that a signal generated by the PID will energize the coil on a 120VAC relay while we want to activate the SSR with a DC voltage. The good news is that the signal generated by the PID to energize the relay coil is a 12VDC signal and we can simply route that 12VDC signal out of the PID to directly drive the SSR. See the attached photos for details.
The first step is to open the case which is fairly easy, the front bezel and PCBs slide out once you depress the locking tab. Next locate the output relay using the connection diagram printed on the outside of the case or the user manual. Then desolder the 120VAC relay. Lastly we shunt the 12VDC trace to the output lugs so that we can access this signal outside of the housing. We then wire the output terminals on the PID to the SSR as if the PID was always SSR compatible.
One final note is that you will need to configure the PID controller to reduce the cycle time to around 2 seconds which is often the minimum on relay output PIDs since rapid cycling of the mechanical relay will quickly cause it to fail. Having removed the mechanical relay and now driving an SSR with no moving parts we want the system to respond more rapidly.
If you select an alternate PID, you need to ensure your can drive the SSR or modify the controller to drive the SSR. Go!
Step 4: Component Substitutions
The following are guidelines when selecting components:
Burner Lights: The burner lights illuminate when the SSR and contacting relay are active. Meaning that the burner select switch is enabled to either the HLT or Boil and the PID controller is energizing the SSR. When this happens, the lights will have 240VAC across them so you need a light rated for 240VAC and they will illuminate. A 120VAC light will draw twice its design current and burn out quickly. Neon, incandescent, and LED lights for this duty are available. I recommend you head to your nearest electronics surplus store or pull from salvage equipment. Nothing fancy is needed. You could eliminate these but since it is handy to know when the big heaters are being made hot the lights are a nice to have. Keep them.
Keyswitch: A keyed switch isn't really needed, but it adds a cool factor especially if you need to turn two keys in unison to arm the system. Also a keyed switch will keep random passers-by from firing up your brewery, as long as you hide the keys somewhere. If you hide the keys somewhere you are sure to forget where you put them because hey, we're brewing beer here and you can't brew beer without making room in kegs for that beer by drinking beer. Make sure you have a second key made. Any keyswitch rated for 120VAC will work. No real current handling capacity is needed since the keyswitch just enables the main relay.
Burner enable switch: The important spec on this switch is that it have an off and two separate on states and be rated for 120VAC. An on-off-on toggle is a good cheap choice and is what I used.
Heater element receptacles: You will need to be sure that the plugs on the end of your heater element wires are compatible with the receptacles you have on your control panel but as long as everything is rated for 240VAC and 30A you can choose what you like. I went with locking receptacles to prevent pull out, but those are a little pricey. As you can see from the pictures I used 4-wire plugs and receptacles but only 3-wire is needed (2 hots and a ground). However I had the 4-wire parts lying around so...
PIDs: Go for it. You can do it. If you find a cheaper PID or have some sitting around you can likely mod them to work. SSR output preferred. The specifics will be up to you, feel the burn.
Pump Switch: All you need is on-off and capable of handling the voltage and current of the pumps. The pumps are not a big load nominally but since they are motors their start up current can be large. So oversize the switches here. Rate them the same as your pump receptacles for peace of mind. 120VAC and 15A on-off toggles are not that expensive.
Pump outlet receptacles: Just use whatever household 120VAC 15A double outlet you have sitting around. Failing that, buy the cheapest at your local big box store. Nothing fancy here.
Temperature probe sockets: Use a socket that matches the cables on your temperature probes. Anything will work, no current capacity or special voltage requirements needed. XLR is used here to match the probes specified by Kal at The Electric Brewery.
Step 5: Designing the Enclosure
The pictured control panel uses laser-cut 1/8" plywood as the primary construction material. Holes for the PID controllers, the switches, lights, plugs, receptacles, and other penetrations are also cut with the laser. The laser-cut pieces comprise the front, top and bottom of the housing, with scrap plywood screwed to an internal frame to form the sides and back. The sides and back are thicker wood and are screwed together such that they form one U-shaped piece and the frame with laser-cut panels form the main piece that slides into the sides and back. See the exploded CAD view. Screws hold the two halves together and allow the box to be disassembled in the event that additional changes, repairs or work needs to be performed on the electronics within.
The thicker sides and back are cut slightly larger than the laser-cut panels and frame to allow overhang to somewhat protect the thinner wood panels from damage.
You will need to modify the attached laser cut files (PDFs) to match the components you choose. Particularly, the cutouts for the lights, switches, and receptacles may need to be changed.
Step 6: Wiring
The final step is to wire everything up. This is where attention to detail, a steady hand, and a ready supply of curse words can come in handy. Make sure everything is unpowered when you are wiring, be safe, and understand what you are doing. Releasing the magic smoke from inside electronic components is not a good way to reduce system cost.
A lot of the wire in the control panel is heavy duty to carry large currents and is thus hard to work with. When using terminal strips you may find that it helps to tin the stripped ends of the wires. Crimping on ring and spade lugs will be required so pick up a crimp tool when you buy your lugs. The attached pseudo-schematic gives you an idea of what you want to do. In the schematic, thick fat wires are heavy duty 10 gauge for the 30A heaters. The rest are drawn with thin lines and can use smaller wire like 20 or 22 gauge since no appreciable current will be carried. However, the wires for the pump switches and outlets are drawn in medium weight because they should be 14 gauge since the outlets are rated to 15A and you may be plugging things into these outlets such as pumps, fans or the occasional vacuum cleaner that may draw a significant current.
The terminal strips were converted into "Bus" strips by using short sections of solid copper wire that short the terminals together as you can see in the photo of the interior wiring. Be sure to use a heavy duty wire, in this case 10 gauge for the hot bus and might as well use 10 for the neutral bus.
Another method to cut down on the number of wires running around your enclosure is to use the ring or spade terminals to accept more than one wire to allow you to avoid running a single wire for each need. In the case of the PID controllers you can see in the wiring photo that I've daisy chained the hot and neutral wires at the spade lugs to cut down on wires.
Be sure to have a good single point ground for the heaters and the outlets. If your enclosure is metal, ground it too. Also grounding the housings of metal components such as the key switch or the toggle switches is a good idea. Bring these grounds to a single point, which in my case was a bolt that I put all the ground ring terminals on and tightened them together. You can see this bolt in the lower right of the interior photo.
Step 7: Final Thoughts
One additional detail that is different than the Electric Brewery is that the pictured setup uses a GFCI outlet rather than a copier cord with built in GFCI capability. More accurately, the pictured setup uses a 240VAC 30A GFCI breaker installed at the service panel to make the 4-wire dryer outlet that the control panel dryer cord plugs into GFCI safe. This GFCI breaker is an expensive item but vital to making the whole brewery safe. Do not skimp on this!
Be sure to double check all your wiring before powering up the system. When everything is checked and double checked, you should leave the control panel unplugged from the wall but plug all the components such as the heaters and pumps and temperature probes into the control panel and check to be sure that your kettles and other items are not accidentally shorted to the hot or neutral leads with a multimeter. With that checked, you can arm the system and do some testing and then some brewing. Good luck.
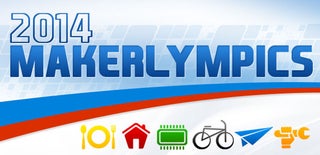
Participated in the
Makerlympics Contest
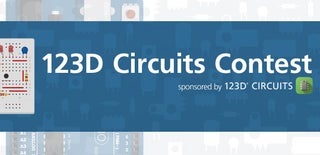
Participated in the
123D Circuits Contest
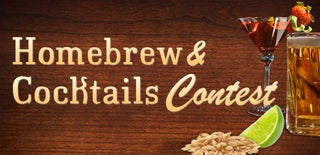
Participated in the
Homebrew & Cocktails Contest