Introduction: Electric Coffee Maker
This instructable is for making an electric coffee maker. Nearly all components are from readymade diy parts & materials, so if any part ever breaks, you can repair or replace it. The parts from the casing were printed using Filabot filament, which is made out of recycled plastic. Other parts are made by casting local waste aluminum (such as cans, aluminum foil and chips from cnc milling aluminum). There is no glue used so you can always disassemble and reuse/recycle every part. So when I would ever get tired of coffee, I can send back my 3D-printed parts to Filabot (they have a recycling service) and I can remelt and reuse the aluminum for new projects. I tried using as much locally produced parts as possible and using as many components as possible which are not related to a specific model or product.
I made everything by learning from online tutorials, by using as much scrap material as possible and by utilizing the local fablab: Fablab Genk.
You will need a 3D-printer (I used the Makerbot Replicator 2X from Fablab Genk for the 3D-printed parts), a setup for casting aluminum and the right tools for assembling the internal components to each other and to the casing.
NOTE: This is a prototype, so some components or parts might have to be optimized. If there are any suggestions for improvement or any mistakes in my instructable, please let me know so I (or you) can adjust it.
Please keep all safety aspects in consideration. Electricity can be dangerous so double check everything before testing. I'm not responsible if anything goes wrong. Never leave the coffee maker running alone. Better be safe than sorry. :-)
(English is not my native language, so excuse me for any spelling mistakes or wrong use of certain words.)
Step 1: Order All Internal Parts
There's quit some internal parts you will need. I found all the parts on the internet, but you might check your local diystore if you can find some parts there.
These are the internal parts you will need:
- Funnel (top diameter around 100mm)
- Aluminum plate (for small parts, see next steps)
- Thermostat (KSD301 105°C)
- 4x M3 bolt length 6mm with Phillips or slotted head
- 4x M3 nut
- Temperature fuse
- 2x Parallel connector
- 1m flexible silicon wire 1,5mm
- Ring connector for 1,5mm wire (M3 hole)
- 1m Silicone hose 10mm inner diameter
- 1m Silicone hose 6mm inner diameter
- Heat resistant tube
- 7x M4 bolt length 12mm for embossing with Phillips or slotted head
- 2x M4 bolt length 6mm for embossing with Phillips or slotted head
- 2x M4 bolt length 30mm with Phillips or slotted head
- 13x M4 nut
- Rocker switch (minimum 6A)
- 4x Hose clamp 13,7mm to 15,3mm
- 2x Hose clamp 10.8mm to 12,3mm
- Grounded chord and plug for 220-250V
- 3x Faston angle connector 4.8 width
- 2x Faston connector straight (6mm width, depending on the connectors on your thermostat)
- Thermal paste (1 gram)
- Heat-shrink tubing 6mm to 2mm
- Heating element
- One way valve for water which fits the 10mm silicon hose
- Plastic cup (from paint gun, so make sure it's new and clean)
I ordered my parts from a German company called 'Conrad'. They supply many countries in Europe, so you can find the order number of most of the parts on this list:
https://www.conrad.be/ce/nl/ShoppingList.html?view...
On Conrad you can find everything except these:
-Heating element:
You will have to order this from a supplier for replacement components. I ordered mine from Servilux (order nr 141709)
If your order somewhere else you have to make sure it's similar to the one on the picture in order to complete the coffee maker.
- Plastic cup 600cc
This will serve as the water tank. Depending on where you order them they might have a different thread. So if possible order one with a thread where the hose fits around, otherwise you also need an adapter. This so you can make a transition from the thread of the cup to an outer diameter between 10mm and 13mm.
I ordered mine from nonpaintstore.nl (part nr 4213505). It's not cheap but it has the right fitting on it for the silicon hose.
Step 2: Print Parts for the Casing
Here you can find the link to all the 3D-printed parts. Because of the size of the object, they take quit some time to print. I printed all of them with standard print resolution from Makerware.
http://www.thingiverse.com/thing:348199
NOTE: These parts were made according to the dimensions of the components which I used. Different components might give problems with the dimensions of the 3Dprinted casing. In the future I might try to learn Openscad and make a parametric model out of it for dimension adjustments.
I ordered filabot filament, which is made out of recycled sources, to try out of it's possible to print with it. I first ordered a blue roll and when I tested it, it came out quit well. Only difference with normal filament was the inconsistency of the color. But that's what they also mention on their website and is because of the use of recycled sources that this might occur.
So I ordered two more colours: red & black. Red turned out to be more like salmon pink instead of red. Black was normal black. Both spools seemed to be pretty consistent in color. But printing with the black spool gave some problem, which is why I printed all parts in 'red'.
Step 3: Make Mold for Sandcasting Piece of Case in Aluminum
Making the mold was not easy and I had to try some stuff out before making the final shape. Basically you fill up the drag with sand, then place the 3D-printed model on top and fill in the gaps on the side. I then cut down the sand, so that the model can be taken out afterwards. After applying talk powder you fill up the cope.
When the cope is filled with sand I open op the mold and get the model out. I also make a hole where the aluminum will be casted through. I know it's not according to the best aluminum casting technique, but it works. If there are any advices on how I can adjust the sand mold for a better casting with this shape, let me know. Or ideas for making a better cast-able shape are also welcome.
You need to cast part 1 two times as a left and right side. It's better if you sand the 3D printed model before making the mold, so the model loosens better from the sand. One of the 2 sides needs a 'bump' where we will fix the heating element later.
I made the bottom of the coffee maker out of aluminum so it has a heavy and stable base. It's also stronger for fixing the heating element. But there are ways to attach the heating element in a plastic 3D-printed model without having to use aluminum. The reason I chose to use aluminum was because this project was about searching for techniques for local producing and recycling. Casting aluminum & 3D printing with plastic from recycled sources came out as useful techniques, also because of the possibilities to share digital models.
I used oil based sand because I'm still learning how to cast and thought this was the safest method, instead of mixing my own sand with water like you can find on other tutorials.
Step 4: Melt Aluminum & Cast Piece
I made a furnace for melting aluminum out of an old fire extinguisher by checking out other instructables:
https://www.instructables.com/id/Oven/
I used scrap aluminum from the Fablab, old aluminum cans and trash aluminum foil to melt and cast into the mold.
Remember safety: read and learn enough about this before trying it out and use enough safety gear to protect you from any mistakes.
Step 5: Clean Up Casted Parts
Saw off the not wanted aluminum from the part and smooth down the model. The sides need to be straight because there are 3D-printed parts which will be attached onto them.
Step 6: Assemble Heating Element
The heating element is the essential part of the coffee maker. It warms up the water so it starts to boil. This is the way it works: The water goes through the heating element until it's leveled (communicating vessels). When the coffee maker is turned on the heating element starts to heat until the water starts to boil. Therefore the water wants to expand and will push upwards. In the side of the water reservoir there is a valve which makes sure the water doesn't go up on that side, therefore pushing it through the other side upwards.
Here is a more visual explanation video on youtube by Crazy Builders:
https://www.youtube.com/watch?v=COKlObhGt50
So, to make sure the element heats up to the right temperature you have to use a thermostat. This will interrupt the electric circuit when it reaches the stop temperature of the thermostat. I used a thermostat of 105°C, just above boiling point but I'm thinking a lower one (90°C for instance) might work as well, if not better.
The heating element I ordered has a small piece welded to it where you can fix the thermostat. I cut a piece of aluminum for this. On this piece it will later also be possible to connect the ground to for safety. To make sure the heat gets transferred well to the thermostat I used thermal paste between the connection of the aluminum parts, the heating element & the thermostat.
Step 7: Tap Holes in Aluminum Part and Fix Heat Element
Check the thickness of the 'bump' from the casted part. Take (at least) 1 mm less and tape off your drill to make sure you don't drill through the whole part. Tap an M4 thread inside the holes.
To fix the heating element to the part of the casing we need to cut some strips which we will use to clamp. By tightening the nuts, the heating element will get fixed. Make sure you put a piece heat resistant plastic between the aluminum strip and the heating element. This will make sure there is no way electricity can flow to the outside casing.
Since I don't have pictures from the fixing of the heating element, I made an exploded view to try to explain how it's fastened.
Step 8: Assemble Switch
Drill a hole to the size of the switch. I used the biggest size drill I could find and then rasped to the exact size. Make sure this is the side where the heating element is NOT fixed.
Step 9: Final Assembly
Connect all the parts in the right place. I made a scheme where you can see how everything is connected. Use as much silicon wires as possible since they can handle the heat better than normal wires. The wires from the chord can be protected with the silicon tube.
Make sure the valve is in the right direction otherwise the water can't get to the heating element.
I suggest leaving the coffee maker for a few hours before trying it out. Then make sure there isn't any water leaking through the sleeves in the bottom. Also check again to make sure the casing can't conduct any electricity with a multimeter.
Step 10: Make Coffee
Choose what flavor of coffee you like, how strong you want it to be, and how much you want. Press the button and start brewing. Enjoy!
Edit: I now also casted the dripping plate in aluminum. This because the 3D-printed part is not completely water sealing.
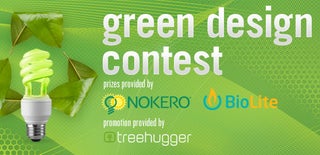
Third Prize in the
Green Design Contest
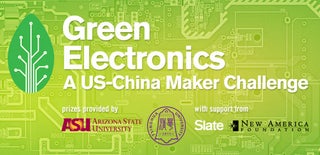
Participated in the
Green Electronics Challenge