Introduction: Electric Furnace
Update: So after a few months the element did finally break, although it was partly my fault. After reading some of the comments and doing more research, a simple controller to cycle the element on and off is recommended as the element is more likely to reach critical temps otherwise. This configuration will work, but only if you've got an element with enough resistance to lower the current a bit and built well enough to handle the temps.
About a year ago I started playing with small furnaces to melt down aluminum, and like most people I went with a charcoal/wood burning furnace. However, after a while I decided there must be a better alternative to charcoal burning furnaces. In this instructable I will show you how to build a very simple electric furnace capable of melting down aluminum for casting.
Step 1: Why Electric?
The main reason I chose to convert to electric over any of the other alternatives that involved burning some sort of fuel is efficiency. Greater efficiency leads to lower operating costs and greater melting capability. Burning charcoal, wood, propane, or any other fuel sources require that many conditions be met before optimal efficiency can obtained. This is because burning is a chemical reaction and therefore requires that the optimal stoichiometric ratio be met in order to burn the fuel as efficiently as possible. This makes optimizing the furnace complicated and requires tools that most do not have access to. In addition, even when the optimum ratio is met, there are still bi products that are released that aren't heat. These bi products serve no purpose and therefore decrease efficiency. This brings us to another problem, expelling the exhaust gases. Because the bi products of combustion must be released in order to continue the process, we also wind up releasing heat in that process.
In comparison, an electric burner such as the one I use in this design creates heat simply by converting electrical energy into heat through friction. This leaves fewer sources for efficiency losses and makes for a much simpler design that is also easier to optimize. Also, since there is no chemical reaction, and therefore no bi products released other than heat, the system can be completely sealed, keeping in as much of the heat generated as possible.
Not only is electricity more efficient, but it is also easier to work with an electric furnace. Where as a charcoal furnace requires that you get the fire started, and keep the fire going, an electric furnace only requires you to plug it in.
Finally, there's the price. A bag of charcoal goes for about $6, and a tank of propane goes for about $15 for a refill. This furnace consumes about 2 kW/h of electricity, which will cost you anywhere between 16 and 40 cents per hour depending on where you live (http://www.eia.gov/electricity/monthly/epm_table_grapher.cfm?t=epmt_5_6_a), and usually doesn't need to run for more than two hours at a time.
Step 2: Materials/Tools
Disclaimer: This project requires working with high voltage, high temperatures, and molten metals. If you have little/no experience with electricity please have someone who is knowledgeable assist you. When operating, use proper safety equipment, including welder's gloves, safety glasses, and wear appropriate attire.
With that out of the way, here's what you'll need for this project:
- Stove top burner
- Two 120v power cables or One 240v power cable
- Chicken wire or similar steel wire
- Steel bucket (http://www.lowes.com/pd_89804-63872-1212GS_0__?productId=3728457&Ntt=bucket&pl=1¤tURL=%3FNtt%3Dbucket&facetInfo=)
- Plaster of Paris
- Sand
- High temp spray paint (http://shop.advanceautoparts.com/p/duplicolor-engine-enamel-gloss-black-12-oz.-aerosol-de1613/7140541-P?searchTerm=engine+paint&zoneAssigned=1&prefZC=34602)
- Duct tape
Tools:
- Bucket for mixing refractory
- Drill w/drill bits
- Masonry bits
- Multimeter
Step 3: Electrical System
After weeks of trial and error, I was able to come up with an electrical system that not only works, but is very simple and cheap to build. The system consists of a 28 ohm stove top burner connected to two 120v power cables. To calculate the expected output, we'll look at these two formulas: V=I*R and P=R*I^2, V=voltage, I=amperage, R=resistance, and P=Power. From our power equation we see that the greater our amperage, the greater the power output. According to Ohm's law, we can increase our amperage by reducing the resistance of our heating element. If we assume a constant voltage of 240, we can rearrange these formulas to give power output as a function of resistance: P=R*(V/R)^2.
If you decide to use two 120v plugs, you'll need to find two circuits in your house or garage that are 180 degrees out of phase (if you go to your breaker box, each breaker is for a different circuit). If done correctly, a hot wire from each power cable can be used to power the element. Note that if the outlets are not 180 degrees out of phase you won't see 240v. Once you've found two elements that are 180 degrees out of phase, you'll want to take a black lead from one power cable and the white from the other and check the voltage. The voltage will either be 0 (the sine waves are cancelling each other out) or 240 (the sine waves are adding together). Obviously we want the configuration that gives us 240v. Also take note, once the system is wired, make sure to plug each cord into the correct circuit. If you plug them into opposite circuits the voltage will be 0 and nothing will happen.
While you're doing this you'll want to make sure that the circuits you're plugging into have circuit breakers that are rated for at least 15 amps. This setup will pull 8.6 amps on average, but in the case that there's a change in the system or something else is plugged into the circuit you don't want the breaker to cut power in the middle of your melt.
While I didn't do this on my furnace, I would highly recommend connecting the ground wires (green wires) from each cord to the metal bucket, even if you're using the 240v cable. What this will do is, in the event that a wire comes into contact with the bucket, it will redirect the current to ground. During the earlier trials with this furnace I had a wire break due to the heat and short out against the bucket, and it was not a fun experience. Learn from my mistakes.
Step 4: Refractory
This section will a little bit more sparse as I have yet to find a refractory that I can say I feel confident in, but I will provide information on my trials. For those who don't know, refractory refers to the insulation that lines the furnace. Your refractory should be a material that will withstand high temperatures (preferably up to 2000 F) and won't crack under cyclic heating and cooling. My first furnace was lined with Quicrete concrete. It's by far the cheapest option and it worked well for my charcoal furnace. However, I tried using it for my first electric furnace in conjunction with a large flower pot and it cracked itself to pieces within about three uses. I believe this was due to the use of a flower pot which couldn't expand or contract readily enough as well as improper mixing of the concrete as I accidentally made the mixture far too watery. I believe a concrete refractory with a metal container, such as first furnace, would work just fine, but I can not say for certain. My current refractory is a 50/50 mix of Plaster of Paris and store bought play sand. I've seen this used several times, and again believe it is a fine refractory, but again was let down by my own faults. I failed to make a center form for casting the body of the furnace, resulting in the odd appearance. So again, learn from my mistakes, and save yourself a lot of swearing and just make a center form. I've found in the past a piece of poster board works well if lined with aluminum foil (to keep the moisture from collapsing the form) and would also recommend reinforcing the inside with paper plates or something similar. You'll also want something to shape the holes for the power wires. The more time you spend making a good form the less you'll have to spend drilling and chipping away at your refractory once it dries.
Before you cast the refractory, don't forget to drill two holes in the bucket for the power wires to go through as well as make any ground connections if you decide to do so.
The lid is fairly straight forward and the easiest part to cast. To start, you'll want to reinforce the structure with some sort of makeshift rebar. I used chicken as I had it on hand, however I've seen screws, nails, and many other materials used. This step is important, without it the refractory in the lid will crack and fall out. You can see in the pictures that the refractory in my lid has cracked, but it has been this way for a while and has yet to fail. Without the rebar it lasted only about three uses. I used the same Plaster of Paris and sand mixture in the lid as I did in the body.
One last piece of advice, when you cast the refractory, BE PATIENT! Give the refractory a good week to cure before use. Heating the furnace to high temperatures before your refractory has set will destroy the refractory, and replacing refractory can get expensive very quick.
Step 5: Putting It All Together
Once you've poured your refractory and allowed it to cure, you're ready to start putting your furnace together. Start by checking to see that your burner fits snug inside the furnace and make modifications as needed. Once that's done you'll want to start preparing the electrical system. Take you're chicken wire, or similar steel wire, and cut two pieces long enough to wrap around the burner's contacts, come out of the furnace at least about 6", and connect to the power wires. With your burner out of the furnace, use pliers to wrap the wire around the leads coming off the burner. Put the burner back in the furnace, feeding the wires through the holes. For extra insulation and to keep the wires from moving, pack sand or dirt into the holes from the top and side. With the wires sticking outside the furnace bend the ends away from each other, wrap the power wires around their respective steel wires, and loop the steel wire around the power wire as you did for the burner connection. For extra security a bead of solder can be placed on the connections.
High temp spray paint will be used to help insulate the wires and the bucket to prevent short circuits. Apply to the area around the holes and any exposed wire that is not making contact with the power wires or the burner. For added protection I used duct tape around the holes as shown in the picture above. A painted square on the outside surface is useful for temperature measurements if using an infrared thermometer. The paint I used is good for 500 F, if the outside of your furnace is reaching higher temps than that your refractory should be redone and possibly made thicker.
Step 6: Ready for Testing
With your furnace fully assembled there are just a few things left to do before turning it on. First, use your multimeter to check for continuity between the power wires and the bucket. If continuity is made check for direct contact between the wires and the holes and insulate as needed. Continue to recheck until no continuity is established. Next, make sure your furnace is in a well ventilated location, away from any flammable substances, preferably outside. Welding gloves are recommended when plugging and unplugging the furnace, in case of accidental arcing.
With everything ready go ahead and plug in your furnace! Once on, check to make sure that the burning is warming up. NEVER touch the burning while power is on. Not only can you be severely burned, but in rare instances the insulation inside the burner may be damaged or missing and allow current to pass through the outer housing. Placing a hand over the opening is all that is necessary to tell if it is functioning.
For the first run keep the furnace on for about 20 minutes and then turn it off. Allow it to cool completely and then let it go for another 40 minutes, followed by another cooling. This is done to allow any remaining moisture to escape the refractory without causing excessive pressure inside the refractory. Keep an eye out for excessive moisture or large cracks. Once the refractory is dried out and cleared of any signs of damage your furnace is ready to go!
Step 7: Results
These are just some of the things you can cast with your new furnace (I may post casting techniques at a later date). The possibilities are truly endless. Good luck and I hope you enjoyed my latest instructable!
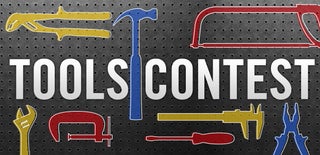
Participated in the
Tools Contest
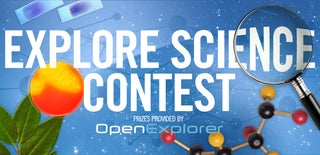
Participated in the
Explore Science Contest