Introduction: Electric Wooden Drink Dispenser
I've seen a lot of cardboard dispensers out there, so I felt inspired to make a drink dispenser myself using a bit more durable materials, because I want to use it at parties and barbeques in the future!
Supply list:
- Submersible pumps
- LED strips
- Momentary push buttons
- Power plug
- Shrink tubes
- Veneer
- Plastic tube
- 1cm plywood
- Aluminum roll
- Aluminum mesh
- Aluminum angles
- Acrylic glass
Tools used:
- Soldering iron
- Hot glue
- Heat gun
- Scoring knife
- Hacksaw
- Jigsaw
- Metal band saw
- Scroll saw
- Drill
Step 1: Planning the Project
I always start new projects with some sketching, trying to figure out all the components I need, which materials to use and so on. I also find it useful to draw a schematic beforehand, even though it usually ends up with some adjustments later, as well as taking the right measurements for every part. The original plan was to be able to connect a 1,5L bottle to the pump directly, but I'll show you why I didn't do that later.
Final schematic is for download as PDF.
Attachments
Step 2: Cutting Out the Plywood
The first step I did was create the entire box out of 1 cm thick plywood. I haven't worked with this type of wood before, but I really liked it, as it's easy to cut and quite sturdy. If you're interested in the measurements, you can find them on the sketches above.
I dealt with the side pieces first, just clamped them together and used a hand planer and a file to make them match perfectly. I prepared the other plywood pieces as well.
Step 3: Assembling the Box
With some tape I could keep the side pieces attached to the back while attaching the front pieces. I'm not going to attach the back piece, as this will be used as a swing door to access the drink containers. I secured the pieces properly with wood glue and nails.
Step 4: Making a Swing Door
The back door will be kept in place by two hinges. On the other side I simply used two hook and eye latches. I used two to make it more rigid, and because the wood was slightly warped, which fixed the problem.
Step 5: Covering Everything Up With Veneer
Now that the main shape was finished, I could cover it all up with this beautiful veneer. It's incredibly thin, so thin that I could cut it with a scissor. It was no issue attaching it. I just used contact glue, which you have to apply to both the pieces you're gluing and let it dry for 10 minutes before merging them. It made it much easier to flatten it out when I used a plastic squeegee, so I'd really recommend using one.
Step 6: Water Drain and Aluminum Mesh
I wanted to create a water drain, so in addition to having a plastic box that would collect all the spillage underneath the tubes, I wanted to cover that box up with this aluminum mesh. I marked the size of it, and tried to use cutter pliers at first, but that would take a lot of time. It's not impossible by any means, it's just a bit of work, so I decided to use a rotary tool instead.
Step 7: Covering the Bottom
I hadn't decided whether I wanted to use wood as the floor or a piece of aluminum, but I finally went for the plywood. Again, wood glue and nails. In retrospect, it might have been a good idea to cover the entire inside of the container room with metal, as this won't rot if there's any spillage. I'm not too worried about that, though.
Step 8: Adding Aluminum Details
I ordered this thin aluminum roll ages ago, and hadn't used it yet, so this was a perfect opportunity to test it out. It was thin enough to be cut by scissors too, which made it easy to cut and shape it like I wanted. Contact glue worked here too, again using the plastic squeegee to flatten it.
I noticed that the aluminum mesh bent slightly, and to fix that I added an aluminium angle underneath the inner edge to give it some support. It was easily cut with a hacksaw. Let's move on to the plastic water collector.
Step 9: Acrylic Water Collecting Box
As the front of it I used white opaque acrylic which I cut with a scroll saw. You can aslo use a scoring knife to make straight cuts like this, there's not really need for a saw. After cleaning it up a bit I drilled two holes so I could fasten the aluminum handle to it.
For the rest of the box I used regular acrylic and sealed it with hot glue. I think acrylic fuse glue could be a better option to seal it with, but I haven't experienced any leakage with the hot glue alone so I'm not worried about spillage.
I also used the remaining scraps of the aluminum rolls as decoration on the sides.
Step 10: Aluminum Label Holders
Because I want to be able to switch out the liquids for parties and everyday use, I have to change the labels every now and then, and these label holders will do the trick. I found some perfect aluminum angles that'll be able to fit the acrylic front piece as well as give some space for whatever label I want to put inside. I used a metal band sat to cut everything just because it was convenient, but it could definitely be done with a hacksaw.
By cutting 45 degree angles I could make some pretty good-looking squares that I could fit around some acrylic. They just had to be cleaned up a bit with a file first. Regular superglue was enough to fix the aluminum to the acrylic.
Step 11: More Details, Finishing Up the Outside
Before gluing anything on, I applied some finishing oil to the wood, and that looks awesome. Next I'll cut some aluminum angles that I could add to the design, just for aesthetical reasons. Again, making 45 degree angles wherever needed and cleaning it up with filing.
I tried to be as accurate as possible when adding those label holders, marking just the right distance between them, and the top and the bottom, else it won't look very nice in the end.
Step 12: The Trigger Mechanism
I could've gone with a simple button as the trigger mechanism to make the liquid pour, but I really wanted to just be able to push a glass onto it and trigger it that way. I still had some scrap opaque acrylic I could use, and I cut 4 narrow rectangles with the scroll saw. In case I had to adjust the position of it later, I drilled a hole at the top so I could insert an elastic that could pull it backwards. It'll be more clear later.
Marking the same height on all of them, I could glue a short metal tube to all of them, and this will help keeping them in position.
Step 13: Drilling Holes for Tubes, Buttons and Power Plug
It might've been smarter to drill these holes before building it, but at the same time, it might not have been positioned as well as they are now. There are 4 holes for the plastic tubes that the liquids will flow through, and 4 holes for the acrylic hands that will be pushed in. While I was at it, I drilled a hole for the power plug too.
Step 14: The Electronic Components
Time to deal with the electronics. Check out the schematic above for details on how they should be connected.
The reason why I chose to use these submersible pumps instead of a vacuum pump is that they're cheaper and the liquid flow is a lot faster. For my use and design, they're perfect. I've had some concerns about food safety rating though, but as long as I make sure to clean them properly after every use I don't think it should be an issue. Anyway, they'll be easy to replace, and I might look into getting vacuum pumps sometime in the future.
The pumps will be connected directly to four LED strips of different colors, and the LED strips will in turn be connected to the momentary switch button and the power supply. That way, the LEDs and the pump will only be turned on when the button is being pushed in, and that's what the acrylic hands are for. They'll be held in place by some small plywood squares.
The containers I found were perfect. 4 of them fits snuggly besides each other inside the dispenser, and they're made of hard plastic. Each one can hold a bit more than 1,5L. The main reason I chose not to use plastic bottles is that with these I'm able to put ice cubes inside. A small detail, but an important one to me, at least.
Step 15: Wiring It Up!
First, I glued the switch button to one of the plywood bits. Then I connected a short wire to the normally open pin and protected it with shrink tube. I needed to drill two holes in the lid; one smaller to fit the cables for the pump, and one larger for the plastic tube.
I thread the wires through the hole, and then I could finally connect the rest of the electronics. Again, I'm soldering the pump directly to the LED strip, and onto the switch button.
Step 16: Adding the Plastic Tube
Time to push the tube through the hole, the lid and connect it to the pump!
Step 17: Soldering the Components to the Power Cable
Ok, so the first picture is the wire from the power cable, and that has to be hooked up with the common ground on the LED strip, and the positive wire on the switch button. It's easy to see on the schematic.
Now comes the tricky part, which was to position the acrylic hand correctly. I fit it inside the hole, and adjusted the plywood bits back and forth until the push on the button felt nice, and then glued them on with hot glue. Finally I could glue the LED strip around the tube.
Step 18: Pour the Drinks!
This is what it looks like on the inside after cleaning everything up. I had to use elastics on two of the hands, so good thing that I added those holes. Now all that's left is to fill those containers and test it out!
It's quite easy to slip the pump in there, and the lid is very well sealed. If I wanna switch to a different drink in one container, I make sure to wash the container first and pump some water through the tube so there's no residue left. If I put soda in there, I can just use the label from the bottle to mark the right tube!
Also, it's really easy to refill it. Quite practical at parties, for example.
Step 19: Final Thoughts
The pumps removes a lot of the carbonation from the sodas because the liquid has to pass through the motor, but it doesn't matter to me as I'll use it for non-carbonated drinks mostly. If you're more of a soda-drinker a vacuum pump might be a better option for you. I'm currently looking into switching the pumps myself, purely for cleaning purposes. The design will fit either pump.
Final tip; if possible, try to get hold of food grade tubes and pumps!
Hope you enjoyed the build, and thanks for reading!
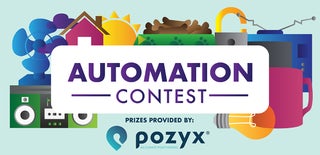
Second Prize in the
Automation Contest 2017
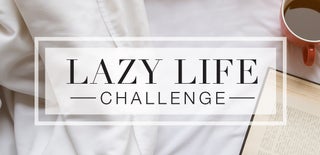
Runner Up in the
Lazy Life Challenge