Introduction: Steam Punk Themed Electrostatic Motor
Intro
Here is an electrostatic motor based on a Steampunk theme that's an easy build. The rotor was constructed by laminating a strip of aluminum foil between layers of plastic packaging tape and rolling it into a tube. The tube was mounted on an axle using cardboard end caps w/flat washers at the centers as bearings. Stationary electrodes or stators were made from a ring of nails suspended co-axially w/respect to the rotor and energized w/negative, high voltage DC. A framework made from drinking straws, tape and plastic covers of tin cans maintained the stators in proper alignment around the rotor.
The project provides an opportunity to learn about Coulomb's Law which describes electrostatic attraction/repulsion between charged points. Specifically, the rotor spins because negatively charged surface areas of the rotor are repelled after they contact the electrically hot stators. Each charged area then deposits excess electrons to the adjacent, grounded stator on the ring as the rotor turns. The charge-discharge cycle repeats as each neutralized area of the rotor approaches the next energized stator. I used re-purposed recyclables and some basic hardware for this project to reduce construction costs to a minimum.
Caution !
This project requires high voltage direct current (HVDC), so choose a power source that is appropriate for your level of experience.
Step 1: Parts & Tools
I've included a list of parts for the project; but improvise and substitute whenever necessary. Be sure to keep in mind the following points:
- Rotor must be light in weight.
- Rotor must be balanced.
- Stators must be well insulated from each other to prevent internal arcing.
Rotor Assembly
Axle (1) -- 15 cm x 0.3 cm dia coat hanger.
Axle Bearings (2) -- Stainless steel flat washers w/0.3 cm ID hole.
Axle Sleeves (2) -- 3 cm x 0.4 cm dia drinking straws (included w/small packages of soft drinks).
End Caps (2) -- approx 4.0 cm dia discs (use cardboard end cover from 3-ring binder).
Lining Strip (1) -- 2.5 cm x 15 cm strip of AL foil.
Stators (6) -- 5 cm length nails.
Stator Housing Assembly
Rims (2) -- Plastic flip lids from mixed nut containers.
Rim Supports (12) -- Std size drinking straws (1/4 inch dia).
Suspension Bands (2) -- Rubber bands.
Rotor Frame
Plastic Horseshoe (1) -- I found this hot pink horseshoe in the discard box at local schoolyard after community church fair; or, you can cut and then glue sheets of cardboard together to make the frame.
Project Base
Scrap Acrylic or Cardboard Sheet (1) -- Cut to appropriate size.
Spacer -- plastic bottle cap.
Power Source (1) -- Typical sources of HVDC in the low microamp range such as room air ionizers, Van de Graaffs and Whimshursts may be too weak to power this motor. Consider a high potential transformer. Simco's CH-30 Chargemaster is one of the "amp-kicking" bad boys of electrostatic generators. Sometimes these units are available through electronic auctions at large discounts by liquidation vendors who don't know what they can do!
Misc Items
Color-coded Wire Binding Posts (2)
Color-coded HV Wire (red & black)
Glues (Cyanoacrylate)
Packaging/Shipping Tape (5.0 cm wide)
Typical Connecting Hardware (small bolts, lock & flat washers, nuts)
Tools
Compass
Electric Drill
Handheld Hole Punch
Hobby File
Protractor
Ruler
Sanding Block
Sharp Pencil
Utility Scissors
Step 2: Make Rotor End Caps
Cut four 4-cm dia circles from cardboard. Drill a 4 mm hole through the centers. Chuck them in an electric drill and sand until round. Glue 2 discs together, then glue a flat washer over the center hole of each disc. Let dry. Ream out any hard glue w/a file.
Step 3: Roll Tape Around End Caps
Insert axle through bearings and carefully roll packaging tape around discs to from a tube. Discs surfaces must be parallel!
Step 4: Apply Foil Lining & Balance Rotor
Cut a 2.5 cm wide strip of foil which should be wrapped around the middle of the rotor. Secure in place w/a drop of glue. Apply several additional layers of tape to cover the strip.
Hand spin rotor on axle. Add pieces of tape as needed to balance rotor.
Step 5: Prepare Housing Rims
Build up housing by cutting about a 4 cm dia access hole in plastic lids to make 2 rims. Punch 12 holes 30 deg apart along edge of each rim. Cut 8 cm lengths of drinking straws to make 12 support tubes. Align holes in rims, then insert a straw into each hole. Construction Tip: Cut a 0.5 cm lengthwise slit in the tip of each straw to facilitate insertion.
Step 6: Complete Housing Frame
Work your way around the rim inserting straws as you go to form housing frame. Maintain a distance of approximately 5.0 cm between rims. Cut off excess straw length when frame is complete.
Step 7: Cover Frame
Roll 2 to 3 layers of packaging tape around frame. Trim excess tape around edges w/scissors.
Step 8: Install Stators
Drill 12 holes around circumfernce of housing that are just large enough to accept nails. Each hole must go through a straw at the midpoint so they can be pivoted at a slight angle as shown (angle will require further adjustments before energizing motor). Insert a rubber band through the straws located at 12 and 6 o'clock positions.
Step 9: Prepare Rotor Support, Attach Base & Posts
Any support that maintains rotor in a fixed position and allows it to spin freely is OK. I used this toy horseshoe. If you can't locate a horseshoe, just make one by layering several sheets of cardboard cut to appropriate size.
Carefully drill a hole for the rotor axle through the tip of each horseshoe heel. Next, drill a hole through the toe to accommodate bolt that attaches horseshoe to project base. Drill a hole through a bottle cap which will act as a spacer. Assemble components. Finally, drill holes in base for wire binding posts.
Step 10: Assemble Components
Slip rubber bands over horseshoe heels to suspend stator housing in place. Insert axle through a hole in heel, sliding spacers and rotor in place as shown. Pivot nails as needed so they are almost touching the rotor's surface.
Step 11: Connect Hot & Neutral Stators
Wire every other stator in series using insulated wire. Remaining stators are wired together using insulated wire of a different color. Connect one set of stators to the hot binding post; the other set goes to ground.
Step 12: Ramp Up the "Horsepower"
A 0.5 Watt power supply didn't even budge the rotor. However, the Chargemaster (see Parts & Tools) spun the rotor at 10 to 12 RPM. Optimum input was about 12 kV at 100 microamps before internal arcing between hot and grounded stators slowed down motor speed.
Step 13: Close-up of Spark
Here's a zoom shot showing a spark discharge to the rotor as it spins.
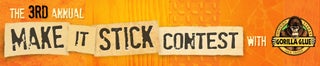
Second Prize in the
3rd Annual Make It Stick Contest
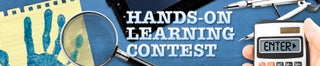
First Prize in the
Hands-on Learning Contest