Introduction: Fish Bone - Knotless Gear Tie
I took this instructable to Kickstarter where it was well received. You can check it out here. Thank you everyone for your support. Brent
Step 1: Idea & Proof of Concept
I wanted to design this specifically for paracord. For starters I went to Sketchbook and doodled some ideas. I settled on a rod encircled by a spiral. I wasn’t even sure this was going to work but all I had to loose was a coat hanger.
Once I had my sketch made up from wire I began to figure out how it would work. After looking at it for a while I realized it looked like a fish. From here on my design was geared around a fish bone.
For anyone who’d like to try, the next couple steps show how the wire fish bone is made.
Step 2: Prototype, Basic Shape
Start by taking a coat hanger and cutting out the long bottom section. Bend it about 1/3rd of the way down over a the shaft of a screwdriver. Bend the longer end at 90 degrees. With the short end against the shaft, wrap the long end around both. See the pictures. Cut it to length so that 5 coils are left. File any sharp edges.
Step 3: Prototype, Key Features
The wire fish must be bent in two areas for it to work. The first is where the coil was cut. Use plies to reduce the diameter of the last coil. This helps hold the paracord in place and prevents the wire end from catching onto your gear when your pulling the tie tight.
The other important bend is at the head of the fish. The upper most coil must be bent toward the top. This gives the back of the head a hook shape for the paracord to tie around. See the pictures.
The tail is bent to complete the fish look. It also gives another place to tie off.
Step 4: Test Run
Take a section of paracord and point the free end toward the tail. Make sure it’s aligned along the spine as you wrap the cord around a few times. The more you pull the tighter it holds. To secure it to the head you wrap it around once. The cord's own pressure will hold it in place.
Step 5: Pencil and Paper
So now I know this thing works. Time to get to making it look legitimate. I placed the wire prototype on graph paper and sketched up a model. Here’s where I decided it was too long. It ended up as ½” x 2”. I also put in an eye and changed the tale. Though I had to figure this out by making a paper model.
Another idea was to incorporate a bottle opener but for now I’m sticking with the original purpose.
Step 6: Metal Model
The final model is made from aluminum flat bar. I traced the paper silhouette on and used an engraver to mark where to cut. Using various drill bits and a scroll saw I cut out the rough shape. I refined it with hobby files and my drill press as a makeshift grinder. Finally I polished it on a buffing wheel.
Step 7: Fish Bone in Use
Using the aluminum Fish is just like the wire version. Take a section of paracord and point the free end toward the tail. Make sure it’s aligned along the spine as you wrap the cord around a couple times. To secure it to the head wrap it around once. For a more secure hold run the free end through the eye.
Step 8: Going High Tech
To take this project to the next level I met with a professional mechanical engineer. Being able to pin point every curve with the knowledge of how forces travel through a structure really improved the design. I included a couple screen shots from our meeting.
He took the 3D image and broke it down on a molecular level based on the material. In this case 6061 T-6 aluminum. It then went through finite elemental analysis. Basically it means this. After runnign it through a super zoomy program it shows a heat map of where the stress is greatest while in use. It also determines the failure point in the structure and at how much force. How cool is modern technology! According to the results the design will strain at 75LBS and fail at 135LBS. I think that’s respectable given this little guy is smaller than 2 quarters placed side by side. Next step is production.
Conclusion: We are in a truly revolutionary time for makers. I began to doodle this idea on December 29th 2012 and posted this instructable three days later. One week after I began the crowdfunding campaign. Since then I’ve received an amazing amount of support and crossed paths with some amazing people. I have this site to thank. Being a member of Instructables has really had an impact on how I design and create. I call it my degree from Instructables University. It’s been a whirlwind. Thanks for reading. Brent
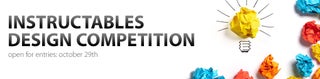
Second Prize in the
Instructables Design Competition

Grand Prize in the
Pocket Sized Contest
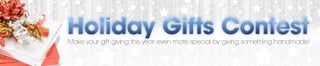
Participated in the
Holiday Gifts Contest