Introduction: Fitting Dupont Connectors
One of the things that you can do yourself (and pretty cheaply) is to make your own connecting wires.
Making your own connecting wires means that you are free of the tyranny of the length and colour of connectors/jumpers that you need to buy, it is MUCH cheaper and you are never going to be short of a connector/wire again (of course, you still need wire, the connectors and the connector housing).
The cost is pretty fair, when you tote it all up:
I've bought wire for as low as $8 for a 10m roll (stranded copper in pvc sheath)
The Dupont housing (2P F2.55mm pitch) for $4.75 for a packet of 200 ($0.05 each)
The Dupont connectors (Female gold plated 2.54mm) for $10 for a packet of 200, Male (not gold, 2.54mm) for $7.90 for a packet of 200 ($0.04 each)
Dupont housing (1P F2.54mm pitch) for $2.86 for a packet of 100 ($0.03 each)
You'll need some decent wire cutters (mine cost about $16) and crimping pliers for Dupont connectors (mine cost about $12)
The Dupont housing doesn't care if the connector is male or female ... so they are interchangeable!
I've made dozens of connector wires so far, for connecting a 9V snap to a PCB, connecting LED to a pin header, connecting sub-boards and for making USB power cables. Once you get the hang of it, you will find it easy and rewarding.
Step 1: Gather Your Tools
A decent pair of crimping pliers, a wire stripper and a pair of side-cutters. A scalpel comes in very handy too.
You will also need some solder and a soldering iron. A Third Hand tool is also very handy.
To make a 9V snap with female connector, you will also need:
1 x 2P Dupont Housing
2 x Dupont Female Connector
1 x 9V snap (mine cost me $1.55 on eBay for a packet of 20 ... so that's $0.08 each!)
Step 2: Prepare the Wire
Get your 9V snap and trim about 5mm from the end using your wire strippers.
It's very helpful to then bevel the plastic/PVC sheathing on the end of the wire so that, when you insert the Dupont connector into the housing, it fits easily.
To do this, I simply took my scalpel and cut away the PVC kinda like sharpening a pencil.
The wire was already tinned, so if you are making your own connector where the wire isn't tinned ... tin it.
Tinning does two really useful things:
- it keeps the strands together in a tight bundle; and
- when soldering, the solder flows much better onto a tinned surface.
Tinning (in this context) is just applying solder to the wire without making a connection.
The bevel on the wire should be about 2-3 mm long.
Step 3: Prepare the Dupont Connector and Solder
Cut two connectors from the strip, leaving them on the strip. It is much easier to manipulate and much easier to solder when you leave the connector strip on board.
With the connector in an alligator clip on your Third Hand (or stuck in some plasticine for stability). You need to tin the inside of the connector where the wire will go. That is, between the fold-over wings of the connector and down to the handy little line in the connector body.
Use a reasonable blob of solder (leaving a blob of about 3mm) so that soldering in the wire is EASY ... don't make your life difficult!
Next, position the wire inside the U channel of the Dupont connector so that the beveled PVC is between the fold-over wings.
Apply your soldering iron to the blob of solder that you soldered in earlier. When the solder is hot, it will flow up the wire by capillary action. You don't need to add any more solder to make the joint good.
Take the piece out of the alligator clip and carefully wiggle the strip back and forth to take it off. If you wiggle it forward and back, it will put a lot of stress on the thin connection between the connector and the strip, you want it to do this so that it comes away easily, without resorting to cutting it with the side-cutters.
Your wires should now look something like the last image.
Step 4: Crimp the Connector
The first thing that I do is to give the connector a quick and light nip in the crimper to close the housing a little. If you don't then the wings are splayed out somewhat and the crimp can bend the fold-over wings the wrong way.
Next, the connector is placed in the jaws of the crimper (20-22) with the wings facing up (in the above picture, I have no idea how you are holding your crimper, so refer to the orientation above). The back of the connector should be wholly inside the jaws of the crimper with the non-crushing part wholly outside of the jaws. Close the jaws completely to make sure that the crimp is good.
I then put the connector into the next smaller anvil (26-28) and give it a light squeeze. I do this to make sure that the crimp is as tight as I can make it. Be careful not to completely crush the connector, you only want a light squeeze. I then turn the connector 90 degrees and give it another light squeeze. Honestly, I do this because I'm a bit obsessive.
Once you are crimped, the connector should look something like the last image.
Step 5: Shrinky and Fit Into the Dupont Housing
Now's the time to slip the small shrinky tube over the connector and the wire. That's right, do it now because doing it before you soldered would have made your life a lot easier ... and I'm feeling mean :P
Honestly, I should have put the shrinky on before I soldered ... but my shrinky is big enough to fit.
The Dupont housing has a little triangle embossed on one side of the plastic. I use this to indicate positive and I always orient my wire so that red is positive, red is at the bottom. That way I know which is positive when I connect, and I get to be a little bit more obsessive.
Slide the connectors into the housing until you hear a tiny click. If it doesn't click there's a couple of things that may have happened.
- you didn't remove enough PVC from the wire so it is a very tight fit or it won't fit.
- if you use a pin, you can lever the plastic tongue up and remove the connector from the housing. Remove more of the PVC insulation and try again ... be careful, the plastic tongue doesn't like to be wiggled to much.
- you didn't push hard enough. Sometimes, all I need to do is to manually push the little tongue down so that it catches the square tab on the connector.
If you hold the housing and give the wire a light tug ... the connector shouldn't move very much at all.
Now that that is done, slide the shrinky tube up so that it is flush with the housing and shrink it by lightly rubbing the hot soldering iron over it (being careful not to burn the housing, the wire, the shrinky tube or yourself.
Step 6: Job Done!
Well aren't we clever!
If you total up the consumable materials that we used in this project (the tools are not consumables, they are "plant and equipment") you have spent less than $0.30 AUD and made your own custom 9V battery snap connector. That's pretty cheap, considering that I've seen them for much more than that (>$1.00).
All that remains is to connect a battery at one end, and a blinky at the other to see the fruits of our labour.
As I said in the intro, I've made loads of these now and I feel confident in my skills here. Give it a go yourself, it won't cost you much to get going and you can impress your friends and attract gorgeous person(s) of the desired gender with your higher than average skills of connection ... you are now a LEGEND!
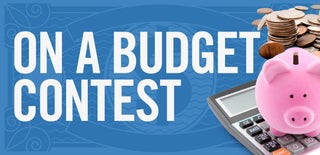
Participated in the
On a Budget Contest