Introduction: Flex Shaft Mortise and Tenon Jig
I looked into purchasing a mortise and tenon machine. The one I really wanted utilized floating dominos (tenons). I believe the price for the complete package was close to $1,000. This is outside of my price range and so I decided to create a light weight option that I could clamp on to a board and carve both the mortise and the tenon. The design includes a detachable, reversable template for 3/4" wood. (I've only designed a 3/4" template as this is primarily the wood that I find at the local home store)
Items Used:
- Dremel tool
- Dremel Flex Shaft attachment
- Dremel 1/8" router bit
- 8x100mm rods - you need 6
- linear motion 8mm bearings- you need 6
- 8-32x1/2" Machine screws
- 3D Printer
- Small clear plexiglass plate Approx 5"x7" (Used to clamp jig to wood and see marking lines)
- Glue
Step 1: Designing Components
I used Fusion 360 to create the printed parts that hold the rails and flex shaft attachment together. The image above shows a rendering of the components assembled and how the jig secures the flex shaft end with the cutting bit perpendicular to the end/edge of the board.
Step 2: Template
The 3D printed tamplate is mounted into the jig and serves as a guide for a "Stylus" or "Follower" to trace around. The entire design is like a mini carving duplicator so is not much different except for the fact of the size, function, and is intended to use with a flex shaft. The template shown above is actually an additional template used to just produce floating tenons that you could fit into two mortise cuts if you are joining edge to edge and not end-edge or end-end.
Step 3: Diagram
I attempted to point out in the photo above to indicate a typical set-up configuration against a board. It may look more complicated than it is in real life since you would hang the dremel someplace and just use a wood working clamp to secure the jig to the board.
Step 4: Notes:
While I have been able to successfully cut the mortise and tenon joint. The fit is not as precise as I hoped for. I attribute some of this not to the design but to the materials used. I actually printed the plastic follower/stylus that you hold with your hand against the template and the follower has some flex to it. (Obvious bad choice for this component) so if someone had the means to be able to create out of metal. the rigidity would greatly improve the joint that you see in the first photo.
Step 5: Files
Here are the STL files I used. perhaps your version can improve on this idea!
Attachments
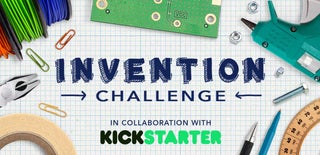
Participated in the
Invention Challenge 2017