Introduction: Floating Circular Concrete Staircase
This unique circular staircase at my casa in Mexico has no center support. It's 24 steps allow a 12' rise in a 10' diameter circular stairwell. I designed an built it with help from my son.
Circular stairs usually need a center support, but I wanted to have the center open, so I designed this one to cantilever from the wall, leaving a 3' open center.
To accurately form the wall and steps, I cut a dozen 5' -1/6's from 3/4"
Rotating same boards around the pipe gave us the riser forms to pour the actual steps onto the ramp.
Step 1: Sketchup Plan
Drawing it in sketch up made it possible to calculate step rise and run, rebar placement, and step placement.
Step 2:
The circular wall that holds up the stairs is made from 5" foam blocks that leave a 3" vertical and horizontal void for concrete and rebar. These styrofoam block forms are made in Mexico. I also used them for most of the walls in the house.
Bars to hold the steps had to be placed in this wall as it was built, so I needed to know exactly where to place them so each step would have a rebar in tension off the wall. By drawing this staircase in 3/d (sketchup) , I could place the bars exactly. The ramp/steps
We poured the ramp and steps 6 months after the wall was built.
Step 3: Landing and Circular Support Beam
Because the steps ran 360 degrees, the landing had to support both the staircase and the upstairs floor. We formed a circular 1/2beam on the floor and lifted it up to pour the complete circular beam.
Half the beam was in the wall, and the half you see supports the floor.
Step 4: Forming the Spiral Ramp
To accurately form the wall and stairs, I used a 20' 2" steel electric conduit pipe as a temporary center post.
I used a 2" u bolt fastened through the end of 6" wide plywood board to make sure the wall was round.
The same boards stacked and rotated to form the bottom support for a foam/fiberglass form we made by tweaking 1" beadboard to the needed warped shape, then fiberglassing it. We made two sections,glassed both sides with epoxy resin.
Step 5: Pouring Ramp
Rebar gets added to the bars coming out of the wall, and an inside form of 1/4" plywood added to the inside.
The ramp was poured in 3 sections, glued at the joints with latex concrete adhesive. This let us reuse the fiberglass and support forms, just by rotating the plywood boards and locking in place.
The concrete was very high strength, mixed on site using super plasticizer to reduce water content.
All the concrete was consolidated with a spud vibrator.
The ramp is 3 inches thick.
You can see the "U" bars sticking out. They give a physical lock to the steps poured next.
Step 6: Rule # 1 Celebrate Victories
On a big long project like this it is important to break it down into smaller parts, just like an instructable. You can then enjoy the successes that keep you going.
With only myself and my son Adam working on this part time, it took many weeks to complete, with many celebrations along the way.
Step 7: Steps
The ramp support forms get rotated to the top of the ramp and become riser forms.
Because the forms stack on each other at the main tube, all I had to do was level them and set them at my marks on the wall that came from the sketchup drawing a year earlier.
Step 8: Finish
A plaster finish on the wall and you have one solid staircase, with less than 1/8" deviation between step rise and run.
Someday we might cap the steps with tile or wood, but they look very sculptural as is.
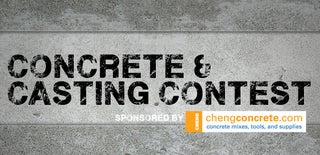
Grand Prize in the
Concrete and Casting Contest