Introduction: Fluorescent Tube Floor Lamp
This post modern vertical fluorescent lamp is a bold interpretation for a lighting solution, inspired by Gian Nicola's Gigante floor lamp (c.1981). Today, Nicola's lamps are a rare find, only sold at auction fetching anywhere from €900 to €1200. I decided to try making my own, with the additional challenge of only using parts found at my local home improvement and do-it-yourself store, The Home Depot.
I was able to recreate this lamp for $200 using off the shelf components. The most costly component was the chrome bars that made up the frame, if you have an alternative you can make this lamp for about half as much.
Ready to see how I built this vertical fluorescent lamp? Let's make!
Step 1: Supplies
Home Depot supplies:
| Tools:
|
Step 2: Mitre and Cut Boards
Mitre the top, front, and sides. The bottom and back will be butt joint and set inside the box.
To keep a clean look to the box I chose to make a mitre joints. A mtire joint is made by beveling the end parts to be joined at a 45° angle to form a corner. I wanted to show off the natural wood grain, and a mitre edge gives a nice clean edge, as opposed to a butt joint. If you're painting your box then a butt joint is much easier.
I started by ripping the boards to 7" wide, trimming off the edges. The table saw was set to 45° and one board was ripped to have a bevel on one side. Next, the mitred board was chopped into lengths; two longer pieces for the top and front of the box, and two shorter pieces for the box ends. Then the ends of each cut board was mitred.
2x 7"x24" board (one mitred long edge, one square edge, both ends mitred)
2x 7"x7" (two adjacent edges mitred)
These pieces will form the top, front, and ends of the box. The back and bottom pieces will not be visible and can be butt joints. The other board was used to create these pieces.
Step 3: Drill Upright Openings
In the top piece of wood a centreline was drawn lengthwise. A perpendicular line was drawn about 2" from each edge, this will be the location of the upright frame.
A hole saw was used to drill an opening. The heavy duty chrome pole is 1-5/16" in diameter, which is a weird dimension. I used a 1-1/4" hole saw, then widened the opening by hand with sandpaper. You want a tight fit.
Remove the chrome pole for now, we'll install it later.
Step 4: Create Box With Mitred Edges
After the top openings have been made the box can be assembled. Start by gluing the mitred sides to the top, ensuring squareness. After the glue has dried glue the mitred front to the mitred top, completing the front and top faces of the box. Finishing nails were used to secure the edges. Ensure squareness on all pieces assembled, then allow glue to dry completely.
The bottom of the box is not mitred, and will be hidden by the front and side pieces of the box. I measured the bottom piece dimension at 22"x6.5". This piece was cut from the other project board and glued into place. More finishing nails were used. The back piece will be cut an installed later.
Step 5: Stability Anchor for Uprights
For added stability for the chrome frame a dowel was added to the bottom piece of wood where the poles terminate inside the box. A 1-1/4" wood dowel fits perfectly inside the chrome pole used for the frame and will act as lateral support.
The poles were inserted inside the box and an outline was traced where they terminated on the bottom piece of wood inside the box. Next, the pole was removed 1" sections of wood dowel were cut and installed where the pole was traced.
Step 6: Openings for Wires in Box Top
After the box has been assembled openings can be drilled for the fluorescent connections on the top of the box. The distance between the chrome poles and divided by the number of lights I had. A small opening was drilled which will allow the wires to pass through, the fluorescent tube clips will be clipped on after.
Step 7: Sand Box
With all openings made and the box mostly assembled (aside from the back) the box can be sanded to give a nice smooth surface.
Starting with about a 200 grit sandpaper and moving to a 400 grit the box surfaces were sanded to a nice smooth finish.
Step 8: Fluorescent Strip Lights Break Down
With the box made we can turn our attention to tearing down the fluorescent lights.
There's really not much to fluorescent strip lights. The light cover is snapped into place and can be easily removed, inside there's an inductive ballast (used to limit the amount of current), and wires that run to the connecting ends for the tube bulb. The ballast is usually held in place by a clip or bolt and is easily removed, the connecting ends are also snapped into place and can be removed with little effort.
Step 9: Clip and Extend Fluorescent Wires
For this lamp we only need to extend one wire to be fed through the chrome pole and extend to the top horizontal frame. To reduce clutter inside the box the other wire was trimmed shorter.
The connector ends are slip-fit onto the wires and can be easily removed by twisting while pulling on the connectors while holding onto the wire.
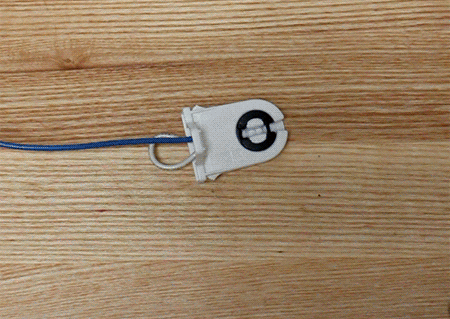
The stock wires that come with the strip light are about 2' long. I clipped one wire to be about 6" long, and used the trimmed wire to extent the other wire to about 3.5" long.
In this model of fluorescent strip light there is an additional connection point for connecting lights in series. Since we're connecting these lights in parallel we can ignore this wire, or (like me) you can trim that wire down.
Repeat for all 3 ballasts.
Step 10: Group Ballasts
After all the fluorescent strip lights have been broken down and the wires shortened/lengthened the ballasts can be mounted together on a thin sacrificial piece of plywood for easier management.
Ballasts were aligned and screwed to the sacrificial plywood using the original mounting brackets.
The ballast assembly was then glued to the bottom piece of the box using wood glue. The ballast assembly was positioned between the pole anchors.
Step 11: Trim Connectors + Make Shrouds
To hide the light connectors a shroud was made from a small slice of 1-1/2" ABS pipe - the fluorescent light connectors almost fit perfectly.
When the light connectors come out of the fluorescent lights they have attachment clips on them, we'll need to trim these off to have them fit inside the ABS shrouds. Using wire snippers the plastic clips on each light connector was trimmed until it could fit inside the ABS pipe.
1/2" rings were cut from the ABS pipe, these rings will act as shrouds for the light connectors. Because the connectors fit inside there needs to be a way to pass the bulb prongs through the shroud a small slit is cut into the shroud ring.
After, each ring was sanded with 1500 grit sandpaper, then buffed to a high gloss finish.
Step 12: Feed Wires Through Box
With the light connectors removed, feed the shortened electrical wires from inside the box through the small openings drilled earlier. I used epoxy to attached the light connectors to the top of the box, just above the drilled wire openings, with the wire connectors facing the drilled openings.
Once the epoxy has cured the wires can be inserted back into the light connectors.
Before we finished the electrical we need to work on the chrome frame to support the lights.
Step 13: Cut Upright Frame
I used heavy-duty chrome closet rods as the structure to support the fluorescent lights, without it the bulbs would easily be crushed and broken. Getting the exact height for the upright frame can be tricky, especially with the 90° bend accounting for some of the height between bulb connection points. I made a stand-in reference bulb from a scrap piece of dowel that was the same length as one of the 4' bulbs I was using.
The chrome poles were inserted into the box, the wooden dowel bulb stand in was placed on top of the wooden box to determine how tall the chrome poles would be. Leaving myself some room for error, I undercut the poles. Small, incremental cuts could then be made later to shorten the chrome uprights to the correct length. The trimming from one of the cuts was used as the horizontal cross piece which will later hold the light connecting the horizontal and vertical members will account for some of the measurements. For now, we'll leave the chrome poles as it until we refine the elbows.
Step 14: Cut Frame Elbow
Chrome plated plumbing J-bend (quarter bend) pipe had a tight radius and fit neatly around the chrome closet poles I was using. The J-bends needed to be modified slightly to
were too long to use off the shelf, so I trimmed the flange from the connecting end and trimmed the tail end to be shorter, creating a small 90 degree bend. The edges of the cut ends were deburred using a deburring tool, alternatively you can use emery cloth or sandpaper to smooth the edges.
With the elbows finishing the frame structure the elbows were then placed onto the upright chrome pipes and horizontal piece to determine the correct lengths. The chrome poles were then trimmed again to the correct length.
Step 15: Tape Frame Ends to Create Secure Connection
After the chrome pipe has been cut to length we can focus on the connection points between the 1-5/16" chrome closet rod and the 1-1/4" J-bend, a 0.06" difference. I used a few winds of fabric gaffer tape to build up the chrome pipe and fit snugly inside the J-bend. The tape was hidden inside the J-bend, and any exposed tape was easily cut off using a sharp utility knife.
Install the J-bends to the uprights chrome poles only, the horizontal connection pole will be installed after the wiring has been brought up from the ballasts inside the box.
Step 16: Top Wires Inside Frame Upright
With the ballast short wires already installed to the box top the elongated wire connectors were labeled to the corresponding ballasts. These wires were threaded through a small opening created near the base of one of the chrome rods which would be hidden inside the box.
With the connectors removed, the wires were fed into the chrome pole opening and upwards through the pipe and out the 90° bend. There should be able wire length to complete the electrical connection for the lights.
Step 17: Horizontal Frame Openings
Openings need to be made in the horizontal chrome frame piece that match the electrical openings in the box.
Because a portion of the horizontal pipe will be hidden inside the elbow J-bends, the measurements we made for the openings on the box don't exactly match. I found the easiest way to ensure the light bulb electrical openings line up is to find the center of the pipe lengthwise and making a mark using a permanent marker. The horizontal bar was then laid on top of the box, with the center marks aligned, and the electrical openings on other side on the box were transferred to the horizontal pipe.
Ensure all marks for the electrical openings on the horizontal bar are along the same plane.
Using the same drill bit used to make the electrical openings in the box, carefully drill the openings in the horizontal chrome bar.
Step 18: Horizontal Frame Connector Shroud
Just like the shrouds on the wood box hiding the bulb connectors, there needs to be some at the top. The challenge here is that the shrouds need to fix to the rounded horizontal bar.
To accomplish this a 1-1/4" hole saw was lined up on the end of the ABS pipe and used to cut a crescent shape through the pipe. The pipe was then cut below the valley of the crescent to complete the shroud shape. The crescent side fits around the horizontal pipe, and the flat side will surround the bulb connector.
Just like with the box shrouds, small slits were cut into one side to allow the prongs for the fluorescent bulb to pass through and be installed into the fixture. The shrouds were epoxy glued in place.
Step 19: Horizontal Frame Wiring
Thread the wires from the top of the chrome uprights through the horizontal pipe with one wire exiting through the drilled openings. The wires were labelled so that they could be matched with the corresponding ballast and connection point in the box.
I found an easy way to get the wires through the pipe and out the openings is to make a kink in the end of each wire and allow it to hook onto the opening edge, then use pliers to grab the wire and pull it through the opening. The bulb connectors were then attached to the wire ends and the excess wire pushed back into the horizontal pipe. The connectors were then epoxied into the shrouds.
The horizontal pole was then fit into the J-bends, completing the frame assembly.
Step 20: Add Sockets for Vertical Frame
The pole sockets usually used to mount the chrome closet poles were slid onto the upright
Step 21: Extension Cord Wiring
Most times fluorescent lamps are wired in the ceiling and you don't see how they are connected to the light switch. This lamp is on the floor and will need power running to it by way of a power cord. A medium-duty power cord was used, you'll probably want a long length so you can move it around without being tethered too close to a wall outlet.
These lights are wired in parallel. The positive wires from the ballasts were twisted together, then the negatives wires together. The end of a power cord was stripped to expose the wires, then twisted to the corresponding ballasts wires. Twist-on connectors were used to make the connection between the power cord and the fluorescent ballasts.
Step 22: Back of Box
With the majority of the box complete we focus on finishing the back of the box enclosure.
To compliment the clean and modern look of the rest of the box I didn't want to use any visible fasteners to attach the back panel, and I also wanted to allow the box to be opened for any repairs or inspections. I chose to go for a slip fit piece of wood with a simple finger hole to allow it to be removed.
I measured the back opening dimension and cut a panel from the remainder of the project boards left over from the box creation. Remember to drill your finger hole before you start fitting the panel into the back of the box, otherwise you run the risk of getting the panel perfectly fit inside the box and unable to get it back out again. Since this panel relies on a tight fit to hold it in place there are no mitre cuts. I recommend cutting this piece slightly larger than the opening and sand the edges until it fits. To accommodate the power cord a notch was drilled into one corner to allow the panel to slip into place flush without pinching the cord.
To prevent the back panel from traveling too far into the box when closing I added small wooden cleats to keep the panel at the right level. Checking the thickness of the board, a line was drawn in pencil of the board thickness. Six small cleats from a scrap wood and glued in place along the offset of the board thickness. Once the glue was dried the back panel could be installed and the back of the box sanded to ensure a flush and even connection between teh panel and the rest of the box.
Step 23: Finish Wood
I love the look of natural wood grain. With mitred edges and no mechanical fasteners, I spent a lot of time and effort to showcase the wood grain of the box.
To seal and protect the wood box I used Danish oil, a hard-wearing matte finish. Wearing protective gloves and working in a well ventilated area Danish oil is put onto a rag and worked into the wood. Excess oil is wiped off after application.
Danish oil has a small potential risk of spontaneously combusting, so make sure you dry them flat before disposing.
Step 24: Add Bulbs
With the Danish Oil finish dried all that's left is to move the lamp into place and install the bulbs. Just like regular overhead fluorescent lamps, bulbs are inserted through the slit in the connectors and turned a quarter turn which both locks them in place and completes the electrical connection.
Step 25: Plug in Remote Switch
There no switch like with normal overhead lights, so we need to account for operation. I originally thought about doing a foot operated switch, but instead found a remote switch for about the same price as a foot switch.
The electrical cord was plugged into the remote switch box, then the box plugged into the wall outlet.
Step 26: Vertical Fluorescent Lamp
This project was a great way to learn and practice new skills, and was a lot of fun to build. This striking design goes well in any room and is sure to be a focus of visual attention, and the centre of conversation.
While the mitred box was difficult to build the results of the extra care to create mitred edges really stands out, and the natural wood grain combined with the industrial chrome is a great look.