Introduction: Fly Away to Sleep. Childs Bed.
This is a bed I made for my son. He loves planes. I love ridiculous projects that I don't have time for. It's a match made in heaven!
Step 1: Inspiration
This is the part where you drink beer and think about that awesome project that you might just have time for (like a week before starting a new job) and money to blow (having just spent four years at university with no income).
You need three things: beer, brainstorming, and Google Image search. These are some images I came across. There was another photo of the 'plane engine into bed', but it was a bit naughty. Still, I really like that style - one day I might have a crack at a circular bed.
My personal favourite is the green toy plane, but there are a lot of compound curves on that! The triplane is a bit too stubby for my taste - I prefer a more 'cartoony' look.
I like the concept of painting the back of the plane on the wall, but this house is a rental!
The toy biplane is looking nice... perhaps with round wings, reminiscent of a bumblebee.
Step 2: Planning!
This part is often overlooked. It is also my favourite part in many ways.
They key here is to get an overview, imagine how it all goes together and try to anticipate some of the issues you will have.
One issue I knew I would have is that I am not a very good woodworker, so there were definitely going to be mismatched joins, uneven surfaces, and unsquare corners. But I have learned through various hobbies that paint can cover a multitude of sins - all you need is filler, sandpaper and a good primer.
I digress. At this stage, you want to come up with a bit of a layout, a shopping list, and head off to the hardware store.
My materials list:
12mm 1200x2400 'CD' plywood - two sheets (the cheap stuff, I'm going to be painting it)
4mm 900x1200 'craft' plywood - for the canopy
1x replacement furniture leg (inspired in-store)
Wooden Dowel (12mm or a broom handle)
1/4 circle trim (about 1m should be enough)
String
Aluminium Angle
Nails, Screws, Sandpaper, Glue
Filler - sandable
Paint (undercoat + coloured top coat) - basically doubled the cost of the project
Optional: wheels or chocks to raise the bed a little higher
Tools:
Jigsaw
Battery Drill with twist bits and screwdriver bit
Sander of some type (I had a random orbit sander)
Pencil, straightedge (I used 3mmx20mmx1200mm bar aluminium), tape measure
Step 3: Marking Out
All those hours of tetris now pay off. I find it quite enjoyable to try to 'fit everything in'. Of course, you can never quite make your original dimensions fit, but with a few minor changes we got all the parts out of the two sheets of ply.
Unfortunately I don't have any photos of the exact layout we used - mainly because it was made up as we go along to try to fit everything in. The general design is as shown in the photo.
The things to remember that might not occur to you:
- make sure you have cutouts on the ribs so the outside of them will sit flush with the outside of the body
- mark and drill pilot holes for the wing uprights before attaching them to the body
- mark out the locations and drill pilot holes for the wings in the sides before assembly
Step 4: Cut and Cut...
This is actually one of the more enjoyable parts.
A jigsaw is not a tool to be trifled with. It does well for curves and odd shapes, but it can be very difficult to cut a straight line with it. Like a fighter jet it trades stability for manoeuvrability.
I'm sure you want to know what secrets I used to cut those wings out, but the honest truth is that is was all done freehand. None of the (ostensibly identical) shapes are very similar, but because there are so many curves and few parallel lines, you can't easily tell. I know of course, and it drives me crazy. But done beats perfect!
There are some tricks to using a jig saw that I have learned along the way:
- patience is key
- don't force it - if it is hard to push, you are probably bending the blade. Stop, look at the blade and the cut, back up and try again.
- bent blades are the result of trying to 'push' the heel of the iron back onto your cutting line. As much as you would like it to, a jigsaw simply cannot cut sideways at all (this is a major difference to cutting with a router). You need to strike a balance between keeping the blade at ninety degrees to the curve and following your carefully marked pencil line.
- good blades in a cheap machine will outperform okay blades in an expensive one. And jig saw blades are pretty cheap, so get a few of the good ones.
- A good stance will make the cut straighter and cleaner
- just cut it! Confidence will yield a better result. And in this project, the worst case is having to buy another sheet of cheap ply. Cutting is almost the most fun part, and marking out a second time will take much less time than the first.
You need to cut:
Rectangular base (this is a solid panel, and takes a lot of material)
Two sides
One front panel (split in two sections in this case, but I wouldn't suggest you do it that way)
Four wings
One rear 'arch' panel
Two 'ribs'
Four nosebox panels
Front nose panel
Phew!
(there is more cutting later, but that will utilise the scrap)
Step 5: Assemble the Body
The design is very simple, using screws and glue. Nothing fancy, just butt joins. It's very satisfying to see it come together (and quite quickly too).
12mm ply is definitely thick enough to put an 18G screw into the side. If you are a purist of some sort, you might prefer pocket screws (I don't have a jig, and I'm sure this would significantly add to the construction time). The joins are glued using 'construction adhesive' - this has the added benefit of filling small gaps caused by inferior workmanship! In this circumstance, the screws are really acting as clamps to hold the glued joint together.
There was a huge void in one of the sheets of ply - but a bit of glue and a clamp keeps everything together.
The key to a project like this (as with many things in life) is to realise your limitations and work around them. Make as much use as possible of the pre-cut edges, which are generally straight and square (unlike my cuts). Hide wonky edges on the bottom. Use the fact that the sheet is an even thickness to help line everything up. And you can leave a little extra (a little) and sand back your joins for a flush finish.
My view on this stage is that this is the 'armature' of a final sculpture. It doesn't have to look too nice, just be structurally sound. And I can assure you that the screws and glue are very sound - the three year old loves to stand on the wings, and they barely dip. The box made from the sides and baseboard is very strong.
If I was building this again, I don't think I would make the nose box the same. I don't particularly like the length and angles it makes. I might just try for a round nose, but that might look funny with a square front. Probably the best thing is to leave it off all together and put the propeller straight onto the front panel of the bed. Making the box was a fun activity in geometry and problem solving though.
I started by attaching the sides to the base and the front and back to the base. This gave me a 'box' to work on. Next time I might attach the wings to the sides before attaching to the base, depending on how I feel on the day.
The ribs go on next - space them evenly and just screw them into the insides of the box. You need to have cutouts so the outside top of the ribs lines up with the outside of the box.
Next up, the canopy. We used a few screws to hold it roughly in place, then a bunch of nails to conform it nicely to the ribs. Note that it goes from floor to floor (it sits on top of the sides). Even though there were many flats and wonky parts on the ribs, and they were far from identical, it all went on pretty nicely. There are voids, but they are hardly noticeable.
Step 6: Add the Wings
This is the trickiest part to line up (I didn't line it up all that well, but fixed it later). Measure and mark using some scrap to get the location of the wings. Then screw your aluminium angle into the side so that it will line up with the bottom of the wings.
On the top wing, I put some heavy twine/light rope under the bracket - this forms the 'cross brace' of the bottom wing. Before you attach the wings, make sure you have marked out and drilled a pilot hole where you want the uprights to go. It's a pain to do it after they are attached (don't ask me how I know). Then screws and glue to attach the wings to the sides, and screws to attach the uprights (they are screwed through the wing into the middle of the dowel, where there is a waiting pilot hole).
Step 7: The Nose Box
This step is rather optional, as I don't think I would make it this way again.
If you have worked out your angles (using a paper prototype), then it will 'sit' together quite nicely. The fun starts when you want to start actually joining the sides.
A few beers into it, and this was towards the end of the day, so the attitude was 'stuff it - just screw it in from the sides, and use a bunch of screws'. So it was glued and screwed. The screws do stick out a bit, since they are placed at an angle to the surface, but it holds together okay.
Now how to attach this big heavy box to the front of the plane? Best not to screw and glue it, because you will never get the plane inside the house. I used 'lift off' hinges, one on each side. I intended to use two on each side, but lining up two hinges was hard enough! Trying to get the second set in was nigh impossible, so I gave up. Its pretty sound and a good tight fit though.
Step 8: The Propeller
This is one of my favourite parts of this build.
I got to use one of my favourite tools - the router - for a purpose it was made for! With some care I was able to rout four grooves for the blades to fit into. These fit quite nicely, with only a few voids and chips from carelessness.
Then it simply pushed and glued together.
A nut to match the already mounted thread was found, and a second nut used to lock against the first and allow for rotation of the assembly.
One issue was the length of the propeller blades. They are a 'nice' length, and use bits of scrap. But they are too long for the propeller to rotate without some chocks or wheels under the bed. So if you are going to sit it flat, make sure the blades are a bit shorter.
Step 9: Safety First!
Around this time, the whole thing is taking shape, and you can finally see how all the dimensions look in real life.
You can also show your significant other the results of your handiwork. Of course, the first thing she will say will be 'won't it be too hot to sleep in'. Followed by 'what are you going to do about all those edges?'.
Beer down. Back to work.
I used some 'quarter round' trim from the hardware store to make those 'straight jutty ribs' into 'curved smooth ribs'.
I went over the whole thing with the sander, took off all the edges and corners.
Finally, I said 'it won't be too hot!' and did nothing about the size of the canopy. I don't think it is too hot, and we have lived in some pretty hot places!
Step 10: Fill, Sand, Prime
Here is where you cover up all those mistakes. Or as I call them, 'joins'.
You bought the whole bucket of sandable filler didn't you? You won't need as much as you think, but use it freely. Fill, sand, fill, sand, etc. until you have the surface you want.
Then prime, and fill and sand again, because there will be bits you missed.
Where the canopy is overlapping the sides, blend in with filler. Having the canopy overlap the side was an intentional decision to see how it would look having the 4mm step blended in. It looks great! You would struggle to find the line on the finished product.
Remember that filler is rather brittle, so it will tend to chip on the sides. but that is okay - just put some more on! It doesn't take long.
Step 11: Painting and Finishing
This part took the longest chronologically (about a month) compared to the rest (about three days), mainly because I became obsessed over having a perfect finish.
Don't be like me. Just put your undercoat/primer/sealer on. Then lightly sand, possibly undercoat again, and paint. Lightly sand one more time and put a second coat on. Then stop!
I spent most of that month sanding, painting, sanding, painting the tops of the wings, hoping to reach some kind of finish nirvana. All that effort, and it looks no better than the nose box which was just finished with undercoat and topcoat.
Having said that, the finish is rather tough and has held up very well. It really looks great! Paint is bloody expensive though, this part costs as much as all the rest put together.
Step 12: Install
Trickier than it looks, but it was designed to fit through a 'standard' door. It might take some creative moves to get it in place, but I got it there in the end.
This is where it is important to have the nose box removable. It just won't fit any other way.
Also, the tail fin won't fit - that has to be installed after it is in place. It seems like such a small thing, but it will definitely not fit through a door with it attached. Trust me.
Step 13: Enjoy
You have created something with your own two hands that your child can use every day. That doesn't happen very often.
This bed has now lived in two houses (ask me how we got it up the internal stairs in our new micro-house) and has done quite well in the move.
The split in the front panel is causing some grief, but I will fix that any day now...
At the end of the day, I like to think of it as functional art. A bed is used so often, and the kids beds are often just images on a plain rectangular bed. This bed might be plane, but it's not rectangular!
(Sorry, little Dad joke at the end there)
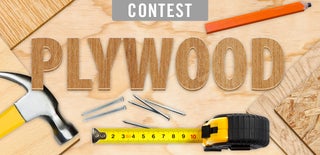
Second Prize in the
Plywood Contest