Introduction: Folding Chair With a Twist
This is a neat chair that folds entirely flat, into what looks like a piece of plywood, only to become a really unique chair. The way it casts shadows often makes its structure hard to figure out and somewhat intriguing, and we really liked that. Also, it kind of looks like a modern art piece or something along those lines haha. Lastly, we made it in a single day. Took about ten hours.
This is not an original design. We got the idea from pictures of work done by Robert Van Embricqs. The tricky part was figuring out how he did it. You can look at his version and the rest of his impressive work here: http://www.robertvanembricqs.com/#!rising-chair/c1...
Tool List
Table saw
Mitre Saw (or a crosscut sled on you table saw) (or a strong arm, a lot of motivation, and a backsaw)
Drill and drill bits
Measuring tape
Carpenter square
Composite square
Pencil
A few dabs of glue
Supplies
8 pieces of 1x6, 6ft long or more (could also get the equivalent total width in 1x4s, 1x2s, or other, if that is cheaper in your area)
2 dowels of 5/8” in diameter and at least 36” long
26 1”x1” hinges and appropriate screws. Longer screws if possible
About 4” worth of 1/8” dowel
NOTE: we suggest trying this project with thicker pieces, starting with 2x4s instead. Although ours held up 200lbs men, we think it would be interesting to also try it in hardwood. If only we had the money to do so… Oh well, we got to have fun and still have a functional chair.
Step 1: Cut and Prepare Strips
Cut the 1x6s to be 64” long. Start by cutting off any cracked or undesirable ends, and then cut to length.
Cut 26 strips of 1-1/4” wide (a couple extra in case something goes wrong is a good idea). If your blade does not make a nice clean rip, then give yourself a little extra to bench plane it flat and smooth at a later time.
Make the strips nice by planning, jointing, sanding, or whatever other technique is necessary. For us, planning and sanding was all that was needed.
Step 2: The Ellipse
There are two approaches to this. Either cut down to the specific dimensions we detailed at the bottom here, or free hand draw a quarter of the ellipse and make the rest point symmetric to the first quarter.
Before beginning, label the end grain of each strip either alphabetically or numerically. Both ends! I.e. piece #1 should have #1 written on both ends. You will need to match the pieces together for the hinges, and then put them in the correct order during assembly. Because of all this matching and ordering, make sure they are clear and correct!
After laying out all the strips in order, we free hand drew the ellipse - we needed some friends to stand on it so it didn't move. We drew the centre line of the ellipse 25” from one end, so go ahead and draw a line across all the strips 25” from one end. On the middle piece (13th piece from an edge) we went up 9-1/2” from the centre line or 34-1/2” from the end you are measuring from. Starting there and sketching a smooth curve down to the centre line on the last strip. Keep your ellipse wide, staying nearly horizontal for a few pieces before arching down at the end.
Working with the strips that have an ellipse marked on them: Take a strip and mark a line 5/8” from either edge so that it intersects with the line of the ellipse. Take your composite square and draw a line that is square to both edges and cuts through that intersection. This should make three lines all intersecting at one point. The only line you will need is the perpendicular one you just drew. From now on, that is the one being referred to.
Draw all those perpendicular lines (the ones you just did) mirrored across the centre line you drew previously. Then draw all those lines on the other 13 pieces, mirrored along the 13th piece (the centre piece). Piece number 13 and 14 will be identical. This is normal and okay.
It gets a little tricky here. You need to alternate between pieces. So starting with piece #1, put an X on the line below the centre line. On piece #2 put an X on the line above the centre line and so on and so forth. If your first piece has the centre line as the cut line, that probably works, but it was not the case for us. You should not have any X’s side-by-side
[Our 13th and 14th pieces had X’s side-by-side, which was a mistake! As the dictum says: do as I say and not as I do J]
Cut along the straight line which does not have an X on it (or cut all the X’s only).
ALTERNATIVE: Simply use our dimensions of each cut. Starting at either side, and always measuring from the same bottom edge of each piece, the cut lines are:
25-1/2
21-1/8
28-1/4
19
30-1/8
17-3/8
31-1/4
16-1/4
31-3/4
15-5/8
31-3/4
15-1/4
32-7/8
Now the same thing starting from the other side
Step 3: Drilling
Drill a hole on both ends of each piece. The hole should
allow you to run a dowel across all the pieces on both ends. We placed the hole 5/8” from the end (but suggest going a full 1” instead) and used a 5/8” dowel – and therefore drilled a 5/8” hole. Make sure the hole is parallel to the end, or vertical if you place the piece on it’s side. If the holes are not true and square, they won’t line up properly and putting the dowel through will be hard, if not impossible. Using a press drill would make this a lot easier.
Step 4: Hinges
Place hinge on the unmarked end of a strip, leaving the
labeled ends visible so you can put it all back together – in order – when the time comes. Make sure that the hinge folds flat on the end, if there is a space, where the two sides of the hinge should meet, then put the other face of the hinge down flat on the end. The cylinder of the hinge must be able to hang off the edge. Now punch a hole for the screws, and then deepen and widen the whole by drilling a pilot hole, or using a larger punch. We found that one of our punches was the correct size for our screws. A pilot hole should have the diameter of the screw’s shaft WITHOUT the thread. The thread must be able to bite into the wood if you want it to hold tight. Screw in the screws.
Take the other piece of the same strip, remembering to use the unlabeled end, and line it up so that both pieces are perfectly parallel to one another and the cylinder of the hinge still hangs outside of both pieces. It is important that the pieces are parallel if you want your chair to fold flat in the end. Also important that the hinge’s cylinder does not get in the way of folding it up either.
Step 5: Run Dowel Through Pieces
Lay all your pieces down flat, and in the order, using the
labels you are now so glad you did correctly and clearly. Now run the dowel through the first piece at one end, and then run the second dowel through the other end of the same piece. Doing both ends at the same time is much easier, especially if you have a buddy around. Leave a little room between strips, this will make things easier too.
When all the pieces have a dowel running through them, you can put the strips tight against one another.
Put a second dowel with a little glue through one end of the dowel. Pull that up against it’s respective strip. Then repeat on the other end so that all the pieces hold up together nicely. Cut off excess dowel and let dry. Do NOT glue any of the strips to anything, they need to move freely.
Fold it up into a chair, and find that sweet spot where it doesn’t want to unfold, even when you sit in it. You could end the project here like we did, but later found and now suggest cutting a piece of rope with hooks on both ends so that the bottom of the chair can be tied together and prevent it from unfolding. So far, it has not unfolded on us, but on a slippery surface it might be more of an issue and suggest the rope.
Stain and seal if you so desire.
You’re done!!! We’d love to hear (and especially see) if you tried a differently sized ellipse and how that worked out for you.
Cheers!
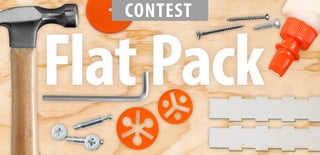
Runner Up in the
Flat Pack Contest