Introduction: Free Professional Wind Turbine Blade
Beware my friend, it's a loooong and detailed instructable since professional wind turbine have many parameters to take in account.
After that we'll jump, and backflip like ninjas with file formats to land in 123D Make and finally build this blade.
With all this you're (almost) ready to start manufacturing wind turbines :)
My goal is to show that a high tech industrial product can be made with a few tools, limited material and some knowledge (tricks?) and I hope to physically help make this kind of development in some parts of the world where you can't afford to buy such high end products but need them to generate green energy for local community development.
If you find this project green, worth a laser cutter, simply useful or beautiful, please vote for it by clicking on the "vote" button at the upper right corner of this page. It's really appreciated.
Materials needed:
Cardboard (or MDF) of the same thickness and in good condition (not pressed or compressed) 594x840mm minimum.
A wood stick of section 30x30mm and 600mm long minimum.
Laser cutter or brand new scalpel or knife, to cut properly and without compressing cardboard (or scroll saw for MDF).
Laser cutter or table saw for cutting wood stick (or jigsaw).
Non permanent spray adhesive (in DIY store).
Fiberglass: Roving 500g / m² and 200g / m², with carbon fiber if possible, or designed for wind turbines ideally
Epoxy Resin (laminating epoxy to prevent vapors from polyester and to master drying).
Printer and paper (or layer).
Calipers (just to measure some thickness).
If using a scalpel, a cutting mat to make precise and clean cut.
Software requirements (to be installed on your computer):
Heliciel (proprietary, http://heliciel.com)
jCAE 0.16 (open source, https://sourceforge.net/projects/jcae/files/jcae/0.16.0/)
Visorium (french, freeware, http://5axes.free.fr/Visorium3D.htm)
Autodesk 123D Make (freeware, http://www.123dapp.com/make)
Adobe Reader (version 10 minimum to print posters)
Step 1: Local Wind Data
A wind turbine is designed to operate at full capacity at a specific wind speed.
This designed speed, will define the shape of the blade helped by Heliciel (french software, now translated to english): a software that will help to understand and choose the right shape (even NACA profile) according to your location.
It is therefore important to know the exact wind speeds where you would install your wind turbine to get the modal wind speed (the most frequent, NOT the average) of your location.
Heliciel website is full of information and here's a link to some international weather data for different cities.
Just select your closest weather station, for instance: "Montpellier (LFMT)" in France.
Go to "Custom" tab and select a year. Unfortunately you can't select more than one year at a time (but you can copy paste afterward).
At the bottom of the page you can download you data in .csv
Step 2: Right Wind Speed
Just open it with OpenOffice Calc (or Excel).
Remove unused columns and roughly estimate the wind speed with a few statistical functions:
Average is a well known tool, median is little less known (as many days above as below this figure), and mode shows the most often speed (but we didn't split data in classes yet). The skewness (gamma 1) and kurtosis give an idea of the kind of curve of the sample without drawing it.
Here we can quickly see that it would be a sharp curve (following a logistic distribution not a normal) with a nice spread on the right (peak on the left, under the average).
So in this case the average is not the right tool to use (because of the spread) and even the median seems to be influenced by this heavy spread, only the mode can fit our need. In my case I round it to 3m/s. As you can see the choice of the right tool for you can be totally different depending on the wind speeds at your location.
Of course the generator power and its optimal rotation speed is also needed to determine the operating point of the wind turbine. Let's see it now in the next step.
Step 3: The Choice of a Generat...or
My generator is special, it's a hub motor for an electric bike, with permanent magnets, these motors have torque at low RPM, and operate with BMS controllers that make them work as generator when your bike is going down the hill. It's a 2in1 component.
An online tool helps evaluating the RPM needed to charge according to a defined motor and a specific battery.
Simply indicates a load (weight) of zero,and a 16" wheel just to have more values below zero NM (wheel diameter doesn't change values).
Here you can see that zero point is at 466 RPM.
The result is not visible right away on the curve but you can slide the dash line after the zero point you can read the (theoretical) generated power. Beyond the zero point this system will generate power, you can also see it in the small table in the lower left corner. This 500W motor will produce 500W at 513 RPM to charge a 48V-12Ah (576 Wh) battery.
Theoretically it can produces more but if it's sold as a 500W motor it's because of its wire gauge. This is why why some wind turbines are not turning fast when strong winds are blowing.
Some wind turbine manufacturers indicate that the wind turbine lifespan is depending of its rotation speed.
That's where a gearbox is needed! So far, I'm not good at gearbox for wind turbine, so let's stick to reasonable figures like 1000-1250 RPM for the blades.
Of course the production doesn't follow the sharp curve given by the bike calculator, the tool here is just to indicate the motor power to move a weight and not a generator to produce power. But I didn't find other tools to test these systems that include both hub motors and battery packs (feel free to give yours).
Our wind turbine will have 3 blades for economical and equilibrium reasons.
Why? One is really hard to balance, two blades can bring cavitation, three is reasonably good, and more is expensive when you build them one by one. Molding can be a solution but you need to track the exact weight of fiber and resin to avoid unbalanced rotor.
We need to find the optimum radius according to our operating point: To do that, we'll get to the closest possible to Betz limit with our parameters, only changing the diameter (see next step).
Well, the diameter for a 3m/s is far too big to print it and build it in a simple instructable, so let's stick to 12m/s.
Step 4: Air Design!
Open Heliciel and start the design:
File> New project > Wind Turbine
If needed, you can precisely define air itself
Since the volumetric mass depends of altitude and air temperature (humidity is less significant) it influences the turbine ability to make the blades rotate. With the same wind speed and temperature, a wind turbine will generate more power near the shore than installed on a mountain.
You can define the operating point in tab 1:3 (see introduction to explain operating point).
Step 5: Blade Design :)
Then you switch to the Blade Geometry tab to choose its radius and width.
With Heliciel you can reverse engineer (retro-conception) an existing blade, so you can understand which wind speed and RPM your blades are designed for and if the profile is an optimized one.
Tab 2.2 helps you define the blade profile (here NACA 1408) and you can further define the profile in advanced option (tab 2.3), for instance depending on the material (as you can see some content is not translated to english yet).
Finally in tab 3, you can optimize design (RPM, blades) or start from maximum power of a blade by clicking on "Multi Analysis":
Step 6: Wind Turbine Tech Specs
In Multi Analysis, you can see how much the turbine will generate (theoretically) for various wind speeds.
This is the curve you'll find in any wind blade technical specification sheet.
Next tab shows alerts and design errors you may have (like theoretical limits of design).
In "Tool" tab you can change the security factor of your design.
Finally, you can build your computed wind turbine by visiting the 3D prototype tab (rebuild it by clicking the heliciel logo above the tabs)
Step 7: Spinning!
Our wind turbine is ready to generate!
Cannot embed the swf, please click "tourne.swf" file below to see the screencast.
You can see wasted energy in blue at the blade tips and wind in green as it pushes and transfer energy to the blades.
Finally you can export your work to really build a blade.
We'll choose .IGS format:
File > Export to IGS format (you must choose a name without any space or special character because Java won't like it). I included my export from heliciel: pale.igs (seems like Instructables doesn't like the igs file, but you'll get the PDF at the end)
Attachments
Step 8: IGS Import
This IGS file cannot be read by Autodesk 123D Make. You'll need to make several changes to make it work without modifying its shape or scale.
Let's start by exporting this IGS to UNV, then from UNV to STL to finally be able to get the PDF plans to build this blade.
In "My Documents": You need to create a new folder empty called "JCAEProject" respecting these caps.
In jCAE:
File > New project (choose the newly created folder)
File > Import geometry (select your igs file)
An information window pops up simply click OK.
If everything went fine, you have the name of your file in "Geometries".
(if not, export with a different axis in Héliciel and try again)
You'll need to right-click>"open" the file to see it.
Your file icon is now colored, you need to right-click>"view" it.
You can finally see your blade as splines (a type of vector design, IGS format and others, that compute surfaces by equations and not finite elements like mesh).
To turn, zoom and pan in this view: left mouse button + move = turn (orbit), right mouse button + move up/dowm = zoom, middle button + move = pan.
Step 9: Meshing
We need a file in .OBJ or .STL format ("mesh" type) and jCAE will convert it in mesh:
Windows > Output (to master the conversion).
right click on "Meshes">"Add Mesh"
Then right click on your geometry and select "Copy"
Finally another right-click on "new1" in Meshes (just newly created) and select "Compute"
jCAE computes with a green K2000ish bar in the lower right corner, output window fills up.
After a few seconds or minutes, you'll get something like:
99922 [INFO] org.jcae.mesh.xmldata.MeshToMMesh3DConvert- Total number of nodes: 111390
99922 [INFO] org.jcae.mesh.xmldata.MeshToMMesh3DConvert- Total number of triangles: 221801
99922 [INFO] org.jcae.mesh.Mesher- End mesh
you got a new "group" in "Meshes" sub folder.
(If you don't get this result but something like:
Error occurred during initialization of VM
Could not reserve enough space for object heap
Could not create the Java virtual machine.
You need to reduce memory allocated in jCAE options:
Windows > Options, jCAE/Mesher Settings > Maximum Memory)
Step 10: 3 Nurb Surfaces = 221 801 Triangles
Now to finally view your mesh result:
Right click on "new1" to select "View".
Zoom in to see the 221 801 newly created triangles!
In the attached screencast you can see two blades, one as nurb in blue, and the same as mesh in pink and green.
Unfortunately jCAE cannot export in STL or OBJ, but you can import a UNL format into Visorium, it's pretty fast:
In jCAE :
Right-click on "new1", select "Export to UNV". Think to keep "millimeters" before saving the file.
IGS file was 204kB, we get a 42MB .UNV file for the same shape but not the same thing.
Attachments
Step 11: STL Finally (71MB)
In Visorium (sorry only french version for now):
Fichier > Ouvrir Format Maillage
Select ".unv" in drop down menu and your UNV file. It takes a few seconds to get something like in the image.
You can directly save in STL:
Fichier > Enregistrer STL
Bang!, now STL file is 71MB.
Step 12: 123D Import
At last, we're on the workshop prototype stage:
In Autodesk 123D Make :
Import (without using the drop down menu) and select your .stl file.
Select the construction technique in the new menu showing below "import", in my case "Interlocked slices", it makes an unused cut and we'll modify it immediately.
First we need to precise the thickness of the cardboard we have and the size of the paper sheet we "ideally" need to have all the pieces altogether (this paper size is different from legal or A4 format), click on the pencil button.
I find it easier to keep the ISO system (A4, A3, A2, A1, A0). Since paper surface is doubled each time (A2=2xA3=4xA4) it's more effective to print a A2 on 4 A4 for instance. Later on, we'll see how to print this huge format to small A4 sheets. (Please someone explain how to do it with legal or other paper?)
Clicking on the pencil opens a window where we'll had a new type of material by clicking on "+" in the lower left corner, then clicking on the name to rename it, for instance "carton A2" (in this case 59.4cm is need to contain the guide).
Error margin of thickness is not important in this case because the guide will prevent errors to accumulate (this would be the case if you'd chosen "stacked slices" as technique).
"Thickness" is the cardboard thickness you've chosen for this project (get a caliper and measure your cardboard plus a glued paper sheet thickness). "Slot Offset" and "Tool Diameter" can be zeroed, because our scalpel cuts without removing matter. But if you use a CNC you'll have to take it in account.
Result should be something like the last image.
Step 13: Size the Blade!
It's time to give the good dimensions of our object in "Object Size" :
Units : mm
Click on "Original Size". Lenght is 547.229mm which is close to the original lenght of the design in Heliciel, the difference is just because the blade doesn't reach the center of the rotor but goes around the rotor shape.
Sometimes when you open a file, the axis orientation is incorrect. To re-orient the slices cut and the guide just click "Slice Direction".
You move the orange dot to be in this axis of the blade and the blue cone to be on top at 90°. This cone is the "1st Axis" and the orange is the "2nd Axis" in the Slice Distribution.
Step 14: 99 45 50?
Now let's focus on the guide and the slices of cardboard:
You have to make a choice: Either you want to stick to theory and cut 99 slices to have a "real" profile, but also take the risk to break the guide when you'll cut it or you cut less slices but loose precision and an important detail at the blade tip since it always start by a half space for the slice to hold in the guide.
99 slices is shown in the first image and 45 in the second.
In "Slice Distribution", we'll go for 50 slices for this tutorial:
Method = By count
1st Axis = 1
2nd Axis = 50
Step 15: Adjusting
The guide isn't perfectly positioned (gravity center is closer to the edge), click on it (its edges turn to white) to move it lower to get something like in the image.
Some slices are blue to indicate they are not bounded to the guide, we just need to keep it in mind for the rotor design (hexagonal or triangle shape). Additionally you can extend the guide to correctly position the blades in the rotor :)
If some slices are red there is a problem (usually when they cannot fit altogether in the chosen paper size).
White slices are OK.
The "notch Factor" and "notch Angle" are not useful if you cut with a scalpel on cardboard.
Please note that this guide is roughly added to our design and we'll need to sand the corners before gluing. See the corners to remove outside the red lines.
Step 16: Print
See attached screencast for assembly animation.
Just print and start to cut cardboard (laser cut is the best if you have a laser cutter, look at the guide!).
In the "Get plans" section you can save your plans in PDF then click on export.
I linked my PDF result so you can print this blade.
Note the bevels on the edges to help mounting the slices on the guide (in case you make it in MDF).
By playing on printer settings of Adobe Reader you can print a A2 Poster on A4 as stated below (for more details see http://helpx.adobe.com/acrobat/kb/print-posters-banners-acrobat-reader.html), here I print a PDF file (with doPDF, free) to check the result before final printing.
Attachments
Step 17: Heat the Glue
(Unfortunately I can't make beyond this step for now since I live in an apartment and don't have the tools and workshop. I give you these indications but if you find them inaccurate or incomplete I'll be glad to hear from you)
That's it, now you can print, if possible on layers, cut and glue sheets on cardboard then cut the shapes in the cardboard.
If possible make the guide of wood with a laser cutter (or scroll saw).
As explained, you can extend the guide to help position it in the rotor (or even have a variable pitch) but also to hold while resin is curing. Remove the sheets or layers and note the numbers directly on cardboard then carefully assemble the slices on the guide.
Draw on the guide the corners to remove. Remove the slices, sand the guide and re-mount the slices.
Now you have a real wind turbine blade ready to make solid.
Step 18: Epoxy and Conclusion
Spray glue (or go with resin and pencil) on the Us of the slices and the guide and mount them permanently.
Cut your 500g/m² fiber glass so it can turn around the profile (like the guide is an axis). Position it and verify that everything is covered. Cut corners to allow covering when resin is applied. Weight your fiberglass (see why below).
Spray glue on fiber glass and position it around the cardboard blade, cover the corners.
Finally, mix resin (weight equal to fiberglass weight) and apply gently with a paint roller following the slice shapes from the leading edge to the trailing edge until fiber is transparent and cardboard gets wet.
Resin in the cardboard will strengthened the blade but be careful not to overcharge. Position the blade flat to cure for 24 hours
2nd layer with 200g/m² fiberglass and resin to get more rigidity and laminate (it's a prototype and the over thickness is not detailed but 123D Make can deal with it if you know the thickness of your fiber and resin). Position the blade vertically (hold by the guide extension) for 7 days (resin mechanical strength is acquired with time depending on room temperature and type of resin used).
Remove everything that's outside the final shape with a grinder and sand papers (120 on sanded details, 220 everywhere except delicate details, 400 everywhere, eventually 600 then 1000 (water based)), may be some resin paste to fill holes and sanding again.
If possible: primer and spray car paint to avoid sun and rain to delaminate resin and fiberglass.
If you made a blade following this hard tutorial until the end you're a heck of a craftsman. Enjoy the satisfaction of making unique things useful for many!
Conclusion
I hope this detailed tutorial helped you to understand wind turbine blades, its specific design according to the location and the stages to get a prototype. Molding and production is another story.
If you find this project green, worth a laser cutter, simply useful or beautiful, please vote for it by clicking on the "vote" button at the upper right corner of this page. It's really appreciated.
Bibliography :
http://www.heliciel.com
http://lesvents.free.fr/Mythologie/La_vitesse_du_vent/la_vitesse_du_vent.html
http://eolienne.f4jr.org/eolienne_etude_theorique
http://en.wikipedia.org/wiki/Freeform_surface_modelling
http://5axes.free.fr/IGES_to_STL.htm
http://www.guzzitek.org/documents/divers/Resine.pdf
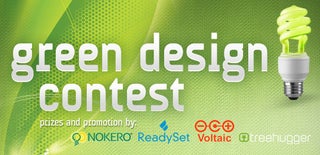
First Prize in the
Instructables Green Design Contest
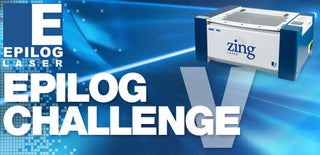
Participated in the
Epilog Challenge V