Introduction: From 3d Printed Part to Metal, the Lost Pla/abs Method
Step 1: Spruing Up, or Building a Yoda Tree...
The first thing we need to do is to sprue up the parts and create a tree for casting. Here I am taking the printed parts and attaching them to wax rods to build the tree. The wax and the printed parts will be burned out later in the process.
Step 2: The Completed Tree
This is the completed tree. When attaching the parts to your tree you need to watch the way the parts are oriented. You do not want to attach the wax in a way that there will be an air pocket formed above the wax rod when the metal is poured. The wax rod should be the highest point of the printed part when casting.
Step 3: Mixing and Pouring the Investment
Once you have your tree all done it is time to mix your investment. There are several makers of the investment powder so it is best to follow thier instructions on mixing and burn out times. I am using americast by Ranson and Randolph. Once the investment has been mixed it is placed into a vaccum chamber for 2 minutes to remove the air bubbles. Its at this point a slite deviation is made from the traditional lost wax methods, generally the investment is poured into the flask and then vaccumed again but since the printed parts are hollow and contain small voids that could allow the investment to enter the part if placed under vaccum I instead place the flask on a vibrating table and the investment is slowly poured in. The vibration causes the air bubbles to rise to the surface and not stick to your printed parts.
Step 4: The Burn Out Process
It is now time to burn out you invested parts. Care must be taken during this step otherwise all your hard work will go right down the drain. The burn out takes a long time to do properly (again follow the investment mfg directions) I started my burn out at 200C and once that tempature was reached it was held for two hours, then the tempature was increased to 460C and again held for 2 hours. The final tempature was 740C and held for 4 hours before turning off the kiln and allowing it to cool slowly to 200C which is the flask casting tempature I decided on for this pour and choice of material to be cast.
Step 5: Melting and Pourning
I chose silicon bronze as the metal for this cast. It is very fluid when molten and very attractive when cast. The melting was done in my small propane fueled furnace. The melt time was about 20 minutes and at the end of the melt the surface was skimmed to remove any impurities and then quickly poured into the flask and allowed to cool before quenchig in water to cool and remove most of the investment. In the picture you can seeall the little ears on the yoda busts, a great sign of a succesful cast.
Step 6: The Finished Product and Video
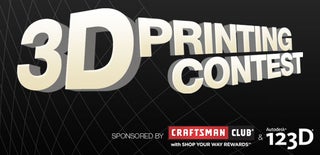
Participated in the
3D Printing Contest