Introduction: Gears of War 3 - Hyper Realistic Digger Launcher Replica
In this Instructable I'm going to show you how I, in collaboration with my talented wife, went about building my very own real life Gears of War Digger Launcher Replica from start to finish. Fortunately it will not actually shoot little exploding creatures so you can sleep soundly at night knowing the children will be safe. Prop building has really taken off in the last few years and more and more people are starting to create there very own versions of digital objects. Everything from exotic guns to helmets to full blown armor. Working in the gaming industry, I like to keep the focus of what I build relevant to what I do during the day. Most of my projects are from various video games that I am a fan of. As a fair warning, A project like this one is very time consuming so be prepared to put in a lot of hours if you decide to undertake something along these lines. As with my last project, there will be a lot of information in here that has a lot of different applications so feel free to experiment.
Choosing a Gears of War gun was a risky choice and there are already several professional replicas on the market. A Replica company by the name ofTriforce has been making them for awhile now and have created 4 different guns from the Gears of War games. The quality of there work is extremely high and there props are very impressive. So the bar was already set very high before I started. My final product would inevitably be compared to their work. No pressure.
This instructible should be a great resource for anyone interested in attempting some replica or prop building projects and most of the methods used in here apply to a wide variety of builds. If you have any questions and would like me to expand on a specific area or idea, please feel free to contact me or leave a comment below.
So let's get started shall we?
Materials and Tools used are broken down for each section.
Step 1: Lets Get Started!!!!
Step 2: The Digital Version
The great thing about video game guns is that the concept artist can really go crazy with the design. Because its digital it is really easy to make changes and create things that would be impractical for a real weapon. The Digger Launcher definitely falls into this category and the design is pretty wild with a lot of external pieces. This will make creating a real version of this gun very interesting and probably very hard. The other real challenge is that video games have limits on the amount of detail that they can put into their weapons due to the limits of what the game engine can render. This results in weapons never having enough detail to work from and requires the builder to fill in the missing details. I do have one advantage.
Epic Games, the makers of Gears of War, were kind enough to provide me with the high res 3D model to work from for this project. I also went into the game and grabbed as many reference photos as I could so I would have as much source material to work from as possible for both the geometry and the textures. I can't stress enough how important good reference material is.
Here is a still image of the game model, pictures 1, 3 screen captures, pictures 2-4, and 3 images of the high res 3D model in 3D Studio Max that Epic provide me with, pictures 5-7. I'll add some more reference pictures pulled from the game later in the painting and finishing steps.
Step 3: Blueprints!
Having the high res 3D model to work from made my life about 1000 times easier, as trying to build this strictly from reference photos would have been 'difficult' to say the least. One thing I quickly realized in dissecting the digital model was that in its current state, it could not exist in the real world. There were more then a few floating pieces and several others that barely made any contact at all, certainly not enough to be structurally sound. So as the creation of the blueprints was underway, I had to make several small changes to the design in the blueprints so that it could be made real and the floating pieces could have points of attachment. None of these adjustments were anything you would notice once the gun was finished.
As with my last project, the blueprints for this were created by Tyler Garrison. His Illustrator skills are far beyond anything I can do, and he again knocked it out of the park. Blueprints make a project exponentially easier and they really help work out potential issues before you start building. Once these were far enough along I was ready to officially start building this beast of a weapon.
So Lets get started!!!
Materials and Tools Used for this Section
Tyler Garrison
Illustrator
3D Studio Max
Step 4: Construction - Main Body Parts and Handle
Let the project begin! One of my primary materials of choice for building props is MDF or medium density fiberboard. It is available at home depot in both 4 x 8 foot sheets, which is a little large for prop building, or 2 x 4 foot sheets. It comes in thicknesses of 1/8", 1/4", 1/2" and 3/4". I personally prefer this material as it is very easy to work with, easier then standard wood, and can be sanded smooth. It also has no grain to worry about. The only downside is that according to the sticker that comes on it here in California, the dust from it can cause cancer. So its important to use a mask when working with the stuff. This first step of construction will cover the main central core, upper core piece and the handle.
The Central Core
The one really nice thing about this gun is that it has this very distinct central core that all the other pieces attach too. This core is therefore the perfect piece to build first. I will then work my way out from this, adding on new pieces as I go. I printed out the top and side view from the blueprints to use as reference as I work. The first thing to do is to cut out the profile shape for the core, pictures 1 and 2. This was done in 2 layers of 1/4" MDF to create the inset piece in the center and the slot for the handles which will come into play later. After each side was completed, I then built up the width in picture 3. The box was then closed and the outer surface sanded smooth. I made sure to leave a gap in the bottom for the clip, which will come later. The edges of the core have a 45 degree bevel so I took the core over to the router and beveled all the sides. You can see this pretty clearly in picture 10. The inner depression was also beveled with Apoxie clay since it couldn't be done on the router. the whole thing was then sanded nice and smooth to make one solid piece. This box will also hold the battery pack and power switch, which I'll get to a little later.
Handle
The handle was a nice quick piece to make. I took 4 pieces of 1/2" MDF and cut out the shape shown in picture 4, making the handle (surprise!) 2 inches thick. These were then glued together and the edges sanded smooth. This also took a spin on the router table to bevel the edges. There is a small circular rise near the top of the handle on each side which was made from Styrene and Apoxie clay to blend the outer edge into the handle. This is visible in picture 10. The handle will get a cloth wrapping later on so there isn't any more detail to worry about. This will get attached to the upper part of the central core.
Upper Core and Vents
This upper piece was a little more complicated to make that the larger main section. It has a lot of curved surfaces and 2 vents that need to be built into it. Like the main core, I started with the profile view cut out 2 pieces of the shape. These are also visible in picture 1. Next was to fill in the width leaving space for the 2 vents. This was a process of filling in each section and then sanding the shapes down to match the profile view. You can see the progress in pictures 5 and 6. Again like the core this piece also had most of its edges beveled on the router. The whole surface was sanded smooth before I moved on. The vent covers were made from sheets of styrene that I painstakingly drilled hole after hole into using my drill press, picture 8. And in picture 9 you can see what the result is after it was finished. As a word of caution, Styrene drills really well until just before the bit exits the bottom. At that point the bit will grab the piece and subsequently spin it at the speed of light slamming it into the hand you "were" holding it with over and over. By the time I was done drilling the holes, the knuckle on my left thumb was beat up, bruised and in a few spots bleeding. Not cool styrene, not cool. Like the main core there are still several detail pieces that need to be added, but I'll get to them later on.
As you can see from picture 11, It is already starting to resemble the digger launch but there is still a very long way to go. So with that being said, let's move on to the next step.
Materials Used for This Section
MDF - Medium Density Fiberboard, various thicknesses
Lots of Wood Glue
Styrene Plastic
Apoxie Sculpt
Tools Used for This Section
Band Saw
Belt Sander
Drill Press
Router Table
Dremel
Clamps
Step 5: Construction - Gears
I find it appropriate that I have to make 2 large gears for a gun from Gears of War, even if they are purely aesthetic. The main bulk of these were made from 1/4" MDF. I really need to get a scroll saw so I can cut out enclosed shapes more easily. However all I currently have is my band saw and you have to make do with what you got. Unless you have unlimited funds, of which I do not.
I started by cutting out the main shape twice from 1/4" MDF for each gear. Picture 1 shows the 2 pieces glued together where the top pieces already have all of there inner cut outs done. I will fill in the cut marks on each end with Apoxie Sculpt later. The next step is to work on adding the inner detail. I cut out plastic disks to create the layering in the 3 circular depressions of each piece. A thinner piece of filler wood was also added to raise up the center cavity. See picture 2. This inner cavity has a textured surface on the model. I went to the local hobby store and picked up a piece of textured plastic from the model train section. The plastic was cut out to match the shape of the inner areas and glued in place. Apoxie Sculpt was again added to the circular areas to bevel the edges. The last thing to do was add the teeth to the outside of the gears. I used thick pieces of styrene sheet to make these teeth and glued them in place with super glue. You can see the result of this and the texture plastic in picture 3. There are still 2 additional detail pieces as well as the strapping for these that I will get to later on.
Materials Used for This Section
MDF
Wood Glue
Styrene Plastic
Apoxie Sculpt
Super Glue
Tools Used for This Section
Band Saw
Belt Sander
Drill Press
Dremel
Clamps
Step 6: Construction - Front Nose - Part 1
The front section of this particular gun is fairly complex and building it is going to involve more then a few different pieces. I'm going to break this down into a few steps so there isn't too much information on a single page. One of the details of this gun that I really like is the shape of the barrel. Unlike almost every gun ever made, the Digger barrel in not round. It is instead an oval shape, which I personally really like. You can see this if you go back and look at some of the still images of the ingame gun. The nose construction consists of two main pieces. I'll label them, front and back.
The trick to building complicated shapes like these is trying to break it down into as many smaller, less complex pieces as possible. I always find that it is much easier to build this way, and add on each new piece as you go. This has been working really well for me so far, and I recommend this as a good rule to follow.
Back Nose Core
I started with the back piece and traced out the pattern for half the barrel onto 1/2" MDF 'several' times, cut them all out, and glued them together. Picture 1 shows the left and right sides. The surfaces were sanded smooth on a belt sander. To make painting a little easier, I glued thin sheets of styrene onto the inside of each piece. By doing this, I won't have to apply several coats of primer, sanding between each coat to get a smooth surface. You can see that the inside of the barrel is white in picture 6. This piece is now the main core that all other pieces will attach too for the complete nose.
Front Nose
The next step was to create the front portion of the nose. Due to the grooves and beveled edges on this piece I decided to build only half of the nose and cast the 2 halves that I will glue together. I started in the same way by cutting out various pieces of wood at the different sizes needed according to the blueprints, picture 2, and then glued them all together, picture 3. I used Apoxie Sculpt to bevel the necessary edges. The Apoxie Sculpt is red in picture 4. Like the back part of the nose I also covered the inside of this piece with a thin sheet of styrene for the same reasons as before. Pictures 5 and 6 show this half aligned to the back piece. The next step was to coat it in layers of primer and sand it all smooth. I then made a quick mold of this piece and cast the 2 halves from Smoothcast 300. I glued these together with super glue, picture 10, and will smooth out the edges with bondo and sandpaper.
Back Nose Builtup
Moving back to the back portion of the nose. I needed to build the additional elements. Using the blueprints as a guide I cut out more pieces from MDF to build up the base of the larger curved surfaces, picture 9. Like before I glued them all together and sanded them smooth. Now I did something a little differently here than what I've done in the past. Once this nose is finished, it is going to have a lot of deep gashes and grooves cut into the surface, and to make it a little easier later on, I decided the best way for me to do this would be to cover these new pieces in thick styrene. I would then be able to take out chunks, hopefully with good results and minimal cleanup. My heat gun was the ideal tool for bending these pieces of plastic. So I cut down several pieces of styrene and glued them to the first side of the pieces. Using the heat gun I then slowly warmed up the plastic where it needed to be bent around the surface and glued them down as I went. As a word of caution, it is very easy to overheat the plastic or unevenly heat it and end up with an ugly crease right in the middle of your bend. I ended up doing a lot of tests before I found the sweet shot for bending these plastic pieces. Picture 10 shows these all covered in their styrene sheets with the front edge beveled. Next l added in the small details in picture 11 by drilling various sized holes in thinner sheets of styrene, and then layering them together to create the effect shown. I continued along this process until all of the pieces were constructed and in place.
Since the casting for this project is minimal I'm not going to go into detail on how to do it here. I buy all of my casting materials from Reynolds Advanced Materials. They have a location right near where I live, which is extremely convenient. Their website has a serious abundance of information on casting and mold making. If your interested in learning more about these subjects, I highly recommend you check them out. I also go into more detail about casting in my Portal Turret Instructable.
Materials Used for This Section
MDF
Wood Glue
Styrene Plastic
Apoxie Sculpt
Super Glue
Rebound 25
Smoothcast 300
Tools Used for This Section
Band Saw
Belt Sander
Drill Press
router
Dremel
Clamps
Step 7: Construction - Front Nose - Part 2
The focus of this step will be on the three external light bars that attach to the nose. There are a few details in the first picture that fall between this step and the last as well as the next step. You can see that I added a bunch of screws and the square groove along the top curved piece. The logo is also shown which is covered in the next step.
The light bars presented a unique challenge. I needed to keep in the back of my mind that I would have to run wiring through all of the pieces I build. It's important that the wires are not seen either. Each light bar consists of a bunch of little pieces, so there is a lot to build. Luckily each of the three light bars is identical with the exception of the shorter post on the center one. To make my life easier I decided it would be quicker to mold and cast a few of the more complicated pieces. These are visible as the white resin pieces in the top right of picture 2. I'll briefly break down the construction of each piece and how I went about building it.
Main Rails and Posts
These parts were the least complicated to make of all of the pieces for the light rigs. I started out by cutting out the 3 rail shapes on 1/2" MDF, as well as the posts. To create the beveled edges on the rails, I laid down some small L shaped pieces of styrene from the local hobby shop. Here is a list of the types of styrene pieces you can find at a hobby store. This stuff can be very useful for small details on props and I tend to use it a lot for various parts. I used some Apoxie Sculpt to create the bevel. This is the white edge around the rails in picture 1. The vertical posts also had some small pieces of styrene glued around their bases, and were beveled again with Apoxie Sculpt. You can see in picture 2 that posts and rails have holes drilled in them. These will be used for 2 purposes: so that everything is pegged together for strength, and to run the wires for the LEDs through them. Picture 1 shows these posts temporarily installed so I can see how they fit. There are a few more minor cosmetic details, like bolts, that will be added after the wires are run and the bars are permanently attached together. I don't have a picture of these but they are visible in later steps.
Light Housing and Lenses
The light housings consist of 3 different pieces. The main house, the lens, and the cap that holds the lens in place. I'll start with the housing, picture 3. The master for this was carved out of MDF meticulously using my band saw, belt sander, and Dremel. I tried to keep the walls of this piece as thin as possible so there would be plenty of room for the LED. After some meticulous work, I primed it and made a quick block mold of the piece. I used Smoothcast 300 and made 3 copies of it. You can see the original master, the mold, and a cast piece in picture 3. The cap was made to snugly fit inside this housing, but was made separately from the housing. The cap was made from 3 different pieces of styrene layered together to create the various lips. The inside edge got some Apoxie Sculpt, creating a 45 degree bevel. Just like the housing, it was primed, had a block mold made, and 3 copies were pulled with Smoothcast 300. You can see this in picture 4. The lens was made from the same clear textured plastic as the inner section of the large side gears on the body. However, they needed to be slightly bubbled, so there was a little more work to do than just cut them to the right size. You can see in picture 5 on the left side that I carved a quick bubble to fit inside the cap that represented the shape for the lens. I heated up the plastic with my heat gun and used the cap and the form to mold the lens to the new shape. It worked perfectly, and I was left with 3 bubbled textured lens. All I had to do was to trim down each lens to fit within the housing and cap.
Fork
These forks were a little more time consuming that I originally thought. The forks are the white curved pieces that attach to the back of the light housings. I started out by layering a few pieces of MDF together to build up the thickness of the piece. Using my Dremel with a very small sanding drum, I slowing carved away at the piece until it was very close to the proper shape. I used Apoxie Sculpt to fill in any areas that still needed some material. Like the light housings, I decided to make a mold of these, making them stronger. So I primed the part and sanded it smooth so I could make the mold. The piece is still a little rough but I'll clean up the casts. After the mold was done, I pulled 3 pieces and got to work on the clean up. I sanded all of the surfaces nice and smooth and used my
Dremel to add a small 45 bevel around all of the outer edges, creating a little detail. You can see the mold and a cast piece in picture 6. I somehow misplaced the original part before I took the picture. These will be both epoxied and screwed to the light housing for added strength after all the pieces are built.
Lower Support
This piece is pretty straight forward. In picture 2, these are the U shaped pieces on the left. Building these was nice and easy. I traced the pattern for them from the blueprints 6 times onto 1/4" MDF and cut them out and sanded them smooth. With my Dremel I sanded a slight 45 degree bevel on the outside edges. Each set then had a 1/2" dowel added between them with the proper spacing for the lens housings. These will attach to the lens housings and be the primary piece that holds them in place. Nothing to it. You can see the profile view of these in picture 9 really well.
All that's left is to run the wiring and attach all the pieces. I started with the rails and posts, feeding the 2 wires through the drilled holes and then gluing the parts together. Next was the various parts for the front. Lower support, fork and lens housing, all glued together and the wiring run through the housing. The top bolts in picture 4 are cosmetic only, but the bottom bolts are holding everything in place. The LEDs will be tackled after the base paint in applied.
Materials Used for This Section
MDF
Styrene Plastic
Apoxie Sculpt
Wood Glue
Super Glue
Rebound 25
Smoothcast 300
Tools Used for This Section
Band Saw
Belt Sander
Drill Press
Dremel
Clamps
Heat Gun
Step 8: Construction - Front Nose - Part 3
Locust Logo
The logo on the front barrel of the gun is the only piece on the gun that I decided would be easier to have 3D printed rather then trying to make it by hand. The whole piece is only a little over an inch wide, has lots of angles and bevels, and I needed 2 of them... that helped me decide to get them printed. These pieces will also be illuminated as part of the lighting for the whole gun. The piece was quickly modeled up in Max, picture 1, referencing the high res model. It needed some adjustments to make it print ready, such as giving the walls thickness and a lip for the fogged acrylic piece, as well as a few other requirements from the printer. I decided to use Ponoko for printing simply because I have used them in the past for a few projects and have been happy with the results. There are quite a few options out there for 3D printing and laser cutting so I suggest doing some research and looking around. There might even be a place locally in your area that can do it. The only down side is that it can take a few weeks to get your pieces. Picture 2 shows my Ponoko order page. 3D printing can get expensive. These 2 small pieces came to $20.45. Picture 3 show the final printed piece after it has been test fitted on the side of the nose.
After the pieces finally arrived from Ponoko, I made a mold just to be on the safe side in case anything happened while I was working on them. That way I could cast a new one if necessary and not have to order a new one. I traced each piece onto the side of the barrel and with my Dremel started to bore out the cavity that will hold the LED. After some work, they were ready to go. I also drilled out a hole from the back of the nose to this cavity to run the wires. I will glue these in place after the nose has received its base coat of metallic paint, so I don't have to worry about trying to mask off such a small area.
I have included the .stl file below that is print ready if anyone feels the urge to try out Ponoko.
Materials Used for This Section
Rebound 25
Smoothcast 300
Tools Used for This Section
Ponoko
3D Studio Max
Dremel
Attachments
Step 9: Lathed Bits
One of the new tools I got recently was this central machinery lathe from Harbor Freight. I ended up getting it for just over $100 on sale, and I am so thrilled to have it in my shop. It really came in handy on this project. There are quite a few pieces on this prop that ended up coming off of the lathe. Since this was really the first time I have ever used a lathe, I spent about 2 days just playing around with it and various materials to get used to how it carved. There are countless resources out there for learning how to turn projects on a lathe, so if this is something you are interested in, I recommend doing some research on the subject. Here is a link to a YouTube account that has some good videos of turning projects.
I'm not going to go into too much detail here on using a lathe, as it is really only a small part of this overall project. During my tests, I decided to see what would happened if I used some of the Smoothcast resin I had instead of a block of wood. Turns out that it turns really really well... with one exception, which I will get to in a minute. The one thing I really like about turning resin is that it is almost perfectly smooth right off the lathe. Almost all of the pieces required minimal additional work and they painted extremely well. The only real downside that I noticed was that the resin would tend to flex a little once it started to get thin. Picture 1 is a good example of roughly where that point was. It was possible to get around this though by going really slowing and only taking away small amounts of material at a time. I ended up spending about a day making all of the pieces required for the Digger Launcher, which was about 15 pieces in total. You can see a good collection of them in picture 2 and picture 3, and a few of them in their final locations on the gun. The side gears each had 2 small pieces. The light assemblies on the front of the gun each had 2 pieces as well for a total of 6 on the front. There are 2 handles on the sides of the main body and the pieces in picture 2. The last lathed piece is on the back of the clip. All of these smaller detail parts really add to the overall gun. There is still a lot of work to go, so let's move onto the side panels!
Materials Used for This Section
Smoothcast 300
Super Glue
Tools Used for This Section
lathe
Dremel
sandpaper
Step 10: Construction - Side Panels
The two side panels presented a unique challenge for this project, being that the entire surface is curved both vertically and horizontally. Secondly, they are only about 1/2" thick, and thirdly, I need to make sure I can fit in LED's that will adequately light the 2 chambers. I decided the best solution for this problem would be to vacuform the shapes. Problem is I don't have a vacuform machine. Solution?... fake it. I managed to simulate the process using only an oven. I'll explain more about this in a moment. I first needed to build a form for the two sides.
The first thing I did was to cut out the shapes of these 2 sides from 1/4" MDF so I would have the proper shape to work with. The next step was to go into the 3D model and grab the cross sections of the curves. I did this every 2 inches or so and cut out the shapes to create a rib structure on the base plates. I then filled in the gaps with scrap wood and applied a coat of Bondo over the surface to fill in any low spots. After some time under my hand sander, I had a surface that looked like picture 1. You'll notice they are a mirror of each other and represent the shape of each side.
The next step is to shape the plastic sheets to these forms. I cut down 4 large pieces of styrene sheet plastic to about 3" larger than the form. I preheated the oven to 350 degrees. Since putting the plastic right on the rack would be a bad idea, I picked up a small panel of glass from IKEA for something like 5 dollars and put it in the oven. This piece of glass is slightly larger then the pieces of plastic I'll put on them. Once the glass was warmed up I tossed the first sheet of styrene in the oven. I keep a close eye on it, checking it every 15 seconds or so to see if it was soft. It probably took about a minute. Used a pair of thick work gloves, I pulled the sheet out and immediately started pressing it over the form for the first side panel. Once it cooled and the plastic hardened, I now had the curved surface. You can see what this looks like in picture 2. I repeated this process 3 more times to give me the main pieces needed.
Using the blueprints, I traced the patterns onto these pieces and cut them out using both my band saw and Dremel. I also cut out all of the inner holes and shapes. Picture 3 shows the result of this work. The vent covers also spent some quality time on the drill press drilling many many holes. Tedious. Next up is the spacers. I cut out a ton of small 1/2 inch blocks and glued them all around the edges and around the middle for support. The top piece was then glued to these and I had a good solid surface. These blocks also locked the shape, preventing the panels from being able to flex- important. Picture 4 shows a panel glued together and drying. The blue painters tape is there to hold the whole thing together while it dries. I had a roll of aluminum tape that I used to cover the light chamber, making it as reflective as possible. This worked great, as aluminum tape is incredibly thin and very reflective.You can see in picture 5 how shiny it is.
I unfortunately don't have a picture, but the 2 LEDs were also added at this stage. One on each side of the chamber, and the wires were joined to run through one of the supporting posts that will attach to the main core of the body. The last image, picture 7, shows one of the side panels temporarily attached to the core with the corresponding handle in place. It's starting to look pretty good.
The last step was to build up the rounded edges. I used Apoxie Sculpt fill in the edges, smoothing them out as much as possible. There is a picture of the clay in place during the texture gel step, so be sure to look for it.
Materials Used for This Section
MDF
Wood Glue
Styrene Plastic Sheets
Bondo
Aluminum Tape
Painters tape
Tools Used for This Section
Band Saw
Belt Sander
Hand sander
Drill Press
Sandpaper
Oven
Dremel
Thick pair of garden gloves
Step 11: Construction - Lower Clip
This gun has a BIG clip, but it does need to hold diggers, so it makes sense. This step will cover the three pieces that make up this part of the gun. The two side rails and the actual clip. Picture 1 shows what the end of the basic construction for these pieces will look like in place. There is still a lot of work to be done on the clip, but most of it is weathering and detail work. Let's start with the side rails.
Side Rails
One interesting thing I discovered when looking over this part of the design, was that the clip and rails are not perpendicular to the side of the core that they will attach too. If you look closely at picture 1 you will notice that the pieces are angled slightly towards the front of the gun, the left side of the screen. So the rails and clip with need to be trimmed to fit this angle. The two side rails look more complicated then they actually are and were fairly quick and easy to build. The main piece in them is a 1/4" piece of MDF with another 1/4" lip around the edge that was beveled on the router. Inside of that is just 2 pieces of styrene layered on top of each other, getting smaller with each one. I used Apoxie Sculpt again to created the 45 bevel between the layers. The bottom of each rail was notched to fit within the core. You can see this notching in picture 4. Like many other pieces there are a few more detail pieces, like screws that will be added.
Clip
I debated making the clip removable but decided it wasn't really necessary to do that since the gun isn't really meant to be handled all that much. So permanently attached clip it is. Step one was to build the angled side pieces of the clip. Picture 2. I took a piece of 1/2" and 1/4" MDF and glued them together, taking a trip on the router to bevel the edge. Inside of this piece is a smaller 1/2" clip that will hold the styrene sheet and wrap around the clip. A few support bars were added between the two sides to make one large piece. I then took a large piece of styrene and glued it to one full side of the clip. Using my heat gun I bend the styrene around the curve and glued it to the other side. Picture 3 shows the progress of gluing the styrene down. The base work for the clip is now finished but it still has a lot of detail work to go. It will get a bunch of bolts, leather straps, gashes, and texture on the surface. You'll see this progress in the coming steps.
Materials Used for This Section
MDF
Wood Glue
Styrene Plastic
Apoxie Sculpt
Super Glue
Tools Used for This Section
Band Saw
Belt Sander
router
Dremel
Clamps
Heat Gun
Step 12: Details - Cloth and Leather Straps
This Gun has two types of strapping in various places. The leather straps are part of the actually design of the weapon, and then there are cloth straps that have been added on by its user to the handles and gears. Lets start with the leather straps first.
Leather Strapping
There are two places on this gun that will get leather strapping. The first is the 2 strips across the top on the central core of the gun. The second is around the clip. If you jump back to the one of the reference photos, you'll see these locations. I did a bunch of research into various types of leather remnants found on Ebay, but none of it really fit what I was looking for in the straps on the Digger. I finally decided that leather belts were going to be my best bet. I checked a couple of local thrift stores and was fortunate enough to find 2 matching belts that were just the right size and color, picture 1. I needed 2 belts because of the amount of leather strapping on the gun. I cut the belt down to the various sized pieces needed, and then started on weathering them. Can't have the leather straps looking all new-ish on a gun that is so beat up and dirty. Enter the sandpaper and rasps.
Aging leather is fairly easy to do. I started by taking a rough grit sandpaper and roughing up the edges of all pieces to make them look a little more worn. I then took a rasp and used its really sharp edges to add some small and some deep scratches into the surface of the leather. If you don't have rasps, you can use anything with a rough sharp edge to achieve the same look. I then did a second pass with the sandpaper to rough up the top surface of the leather a little, but not as harsh as the edges received. You can see the result of this process in picture 2.
Cloth Strapping
There is significantly more cloth strapping on this gun than leather strapping. I decided these straps needed to be made from scratch to make sure that they matched the prop as closely as possible. I went to a fabric store and found a really great course looking fabric in a sandy color. Using a sewing machine is something that my wife is much better at than I. So I managed to recruit her help in sewing up a bunch of straps for me. They came out perfect. She then tea stained them to make them look a little more dirty. You can see the three stages of these in pictures 3 and 4. After the weathering on the handles is finished, they will be permanently glued in place so they won't slide. Picture 5 shows how the gear pieces are wrapped. They are still way too clean looking though, so let's dirty them up a bit.
Dirt
Too add just a little bit of black dirt to the leather and cloth I decided to use some serious grime. I went out to my car, popped the hood, and rubbed my hands all over the engine until they were black with dirt. Do not attempt this if you have driven your car recently as your engine will more then likely be VERY HOT and you'll burn the hell out of your hands. I then rubbed this dirt into the handles and the leather straps to make them look like they have been well worn. On the cloth straps, a small amount of dark red paint was added to simulate some blood stains. The final result turned out exactly how I wanted it to, adding realistic grime to all the straps on the gun. Check out the straps in the final pictures to see what this looks like.
Materials Used for This Section
2 leather belts
Cloth of your choice
Actual engine dirt
acrylic paint
Tea
Epoxy
Tools Used for This Section
Sewing machine
Something to cut the leather straps
Rasps
Sandpaper
Step 13: Details - Texture Gels
In the past we have mostly faked the look of rust and peeling paint on my props. Usually by applying rust coloring over the metal paint. It looks good from a few feet back but close range, it doesn't hold up and seems very surface. I knew with this prop though, that I needed to get a little more complex. The surface was going to need some real depth. So I needed to come up with a solution for creating the underlying texture... to help sell the illusion. I originally thought about just adding sand to some primer and applying it with a brush, but I was put onto a better idea by my sister-in-law. Enter the world of Texture Gels. Texture gels primarily come into play in the fine art world to add texture to paintings. My sister-in-law had 3 different types that she wasn't using, so I did a test to see how each of them would look painted. You can see the result of this test in picture 2. The left one was just too course for what I wanted and the middle one just looked like little glass beads. I finally settled on the one on the right, the Black Lava Texture Gel. In my opinion this one created the best illusion of pitting and chipping on the surface, and applied properly to the prop could really create a nice effect.
Now the texture gel is somewhere that I could easily go overboard, so I thought it best to use it sparingly throughout the prop. I decided only to apply it to places where it would clearly add to the gun. I settled on three main areas. The front barrel, the side panels, and the clip.
I started with the front barrel and sparingly applied a coat of the gel, concentrating it on areas where I knew there would be heavy rust or peeling paint. Picture 1 shows the start of the application. I worked it in small sections until I started to feel comfortable with how it went on. The side panels and the clip received much thicker coats as the gels primary role on these pieces was to simulate the chipping paint. You can see in pictures 3 and 4 how much thicker the gel was applied. You'll see later on in the painting steps how well this idea worked as the painting details are added. I honestly couldn't be happier will how it turned out.
Materials Used for This Section
Liquitex - Black Lava Texture Gel
Step 14: Details - LED Lighting
There are a lot of great Instructables out there that cover working with LEDs. The lighting for this gun is about as simple as you can get, so I'm not going to spend too much time talking about it here. I figure if you really want to dive into LEDs my project isn't going to really teach you anything. I'll just briefly talk about what I did.
The entire gun consists of 9 LEDs, 9 resistors, a power switch and a AA battery holder. That's it. I debated with myself for awhile on what color lights I should use. In the single player campaign and all of the reference material I have, the lights are amber. But when you play multiplayer, they are either red or blue, depending on the side you are playing. I could add an additional switch to change the color from red to blue, if I wanted the gun to be from the multiplayer design. In the end though I decided to go with the amber lights and keep it true to the original design and single player style. Each of the lights on the nose have a single LED and the larger windows on the sides have two LEDs each. One on each side of the window pointing inward.
Picture 1 shows the control panel for the gun, which I placed just under the handle. You can see the switch and the battery slot. Picture 2 shows the back side of the panel before all the wires have been connected. The front nose of the gun has all of its wiring meet up inside, and has a single set of wires leading back to the switch. Once the gun was assembled, everything was wired together and closed up. And just like that we have pretty amber lights. Be sure to check out the beautiful color these put out in some of the final images.
Step 15: Details - Steel Buckles and Acid
The buckles are just one more detail piece that needs to be handled. It is getting its own step, because of the unique situation required to make them look right. There are 3 of these steel buckles on the gun. The two smaller ones go on either side of the clip, and the larger buckle goes on the top of the gun just above the handle. I picked these up from the local Army Surplus store. They should work really well- with one exception. They are WAY to shiny and new looking, picture 1. This is a problem as they really need to be rusty and old looking. So I did a little research online and came across this link. He talks about how he artificially rusts and ages steel. A word of caution: as this step uses strong acids that WILL cause serious burns if used improperly, please be careful and use all the proper safety equipment! I would also recommend doing plenty of research into working with acids before attempting this, purely so you know what you're getting yourself into and be as safe as possible about it.
For the most part I just followed the process outlined in the link above. I started out by picking up a bottle of Muriatic Acid, picture 2, which is available at most hardware stores. You shouldn't have too much trouble finding it as it is used to clean concrete driveways and pools. Just so you know, Muriatic acid Is hydrochloric acid so it is dangerous. I started out by pouring about an inch of the acid into the plastic container and adding the copper wire to it, any copper will do, even pennies. I put the bucket into a safe place outside with plenty of ventilation where people and animals wouldn't be able to access. It is important NOT to put on the lid completely, as the acid eating away at the copper generates gas, and if the lid is on tight the bucket could explode. I left the solution for about a day giving plenty of time for the copper to dissolve. You'll notice in picture 3 that the normally clear acid has now turned green.
You can now remove the copper wire from the acid. As a first step to help eat away the coating on the steel buckles, I put the steel straight into the acid for about 2 days. The result is what you see in picture 4. The shiny coating is completely gone and the bare steel is now exposed. Now we are ready for the magic to happen. Since I'm not a chemist, I'm not sure why this next step works as well as it does, but this is what seems to work really well for MetalGeek in the link above. Watering down the acid solution will create a much better effect, somewhere in the neighborhood of 20/1 to 100/1 of water to acid/copper solution should work well. I dipped the buckles into this new solution and let them sit overnight. MetalGeek seems to get results within about a half an hour. I left them over night as I wanted a really strong effect. You can see in picture 5 that the buckles are now nice and rusty. Perfect to match the rest of the Digger Launcher.
Again I can't stress enough how important it is to use all the proper safety gear when working with acids. The risk of losing your vision if it splashes in your eye or burning your skin just isn't worth it. Be safe.
Materials Used for This Section
Steel Buckles
Copper Wire
Muriatic Acid
Tools Used for This Section
Rubber Gloves
Protective Eyeware
Mask - the fumes are awful
Acid save plastic bucket
Step 16: Finishing - Primer and Base Coating
Well I've done a lot of work up to this point but everything still looks like wood and plastic. It's time to get this looking more like metallic parts. Everything needs to be primed before it can be painted. There are several different colors of Primers out there to choose from. The common ones are black, white, light grey, and dark red. My rule of thumb is to choose a primer color that is close to the color of the spray paint I will use. So for metallic paint, I use the light grey primer. If its going to be a darker color, I usually go with the dark red primary. The only advantage to this is that it might take a little less paint to fully cover the primer. For this gun I exclusively used the light grey primer. since it is almost all metallic.
I started on the main large pieces of the gun and gave them their first coat of primer. It's going to take several coats to fully prep all of the surfaces before they are ready for the metallic paint. Picture 2 shows the top core piece with its first coat. You'll notice how it still pretty much looks like wood that is now grey. That means it's time to bust out the sand paper. When your working on priming a surface, it usually take several coats with a lot of sanding between each coat to get it smooth. Most of these pieces got something like 4 coats. This helps to insure that each surface is completely smooth and there is no visible reference to the material it is constructed from. While I am sanding between coats, I also add Bondo to any places where there might be cracks or seems or low spots that just need to be filled. You can actually see in picture 3 that most of the edges of the main core have a coat of Bondo that has already been sanded. The same goes for picture 4. The Bondo is the pinkish colored spots in these pictures. I worked my way through all of the parts of the Digger priming, sanding filling gaps over and over until finally all the pieces were ready for the metallic paint.
I've used a few different methods in the past to achieve my metallic look. There are a lot of different spray paints right off the shelf that get the job done. I recommend just picking one that you personally like. It was fairly easy to go through all of the pieces are apply the paint. Each piece took 2 coats to fully cover them. Pictures 6-9, 11, 12, 14-18 show the metallic paint. I think its looking pretty good so far.
The 2 geared pieces just need a kick pass of black spray paint and then its on to weathering. I meticulously masked off the areas of the gears that I didn't want black with painters tape and then applied a quick coat of black. Picture 10. The 2 side panels with get a large coat of red. It just it will not come from a spray can. It will be covered in the detail stage. You'll see why during that step. that about covers the primer and base paint. Let's move on.
Materials Used for This Section
Primer
Metallic Spray Paint
Sand Paper
Painters Tape
Bondo
Step 17: Finishing - Weathering Metal and Painting the Handle
From this step forward, my wife and partner in crime, will be explaining how to add authenticity from the game model through painting and weathering details. Take it away, Dena!
Howdy!
As Ryan completed construction of the Digger Launcher, he began passing individual pieces onto me for the weathering and detail work! Pictures 1 and 2 show the materials I used and the basic paint colors for everything from the first dirt washes over pristine metal paint, to the rust details, and blood marks on the cloth strapping.
Because this prop required so much more painting detail than previous projects we've done, I really learned a lot about the best ways to achieve certain effects! I believe there are a ton of ways to get to the end result, and I'll try my best to create an image for how I got to the final photos of the Digger Launcher. So here we go!
Each section was primed and spray painted a base metallic color, so I started by giving everything a coat of "grime," pictures 3-6. This is a wash of Bone Black acrylic paint and water. As I progressed with each portion of the gun, I would add more of this grime wash into areas where I knew it would settle: between each main body piece around the connection points. The amount of water depends on exactly how nasty I wanted the metal to look. Less water is more nast! Sometimes certain areas would call for a little Transparent Burnt Umber (darker brown) or Burnt Sienna (lighter orange brown) in a wash. This meant watering down the paint even more and keeping a rag handy, as to avoid brush marks on larger surfaces. The reason I would layer brown tones with black, was to create an overall warmer feel for the gun. There would be dirt, and it would make the final gun feel more complex overall. You can see this looking at the detail of the top vents in picture 5. The same effect was applied to the side panel vents, which you will see in the final photos.
The color of the handle was something we changed our minds on, after it had already been built. So rather than remake it in solid wood, and delay the rest of the project, I took the "metal" handle and sparingly spray painted it with a red primer. I left the primer light, because I wanted the metallic underneath to shine through, and add an extra dimension to the faux wood I was about to paint on top. You can see the beginning stages of wood grain painted in photos 7 and 8. I mixed a palette of transparent browns, and used a 1" brush that would leave lines as I glazed over the surface of the handle. I then used the 2" brush to glaze. I didn't create a typical wood grain, because I knew that most of the handle would later be covered with cloth strapping and more dirt.
The last part of this general wear was in pulling back out the brighter metal tones, along edges where it would rub or scratch off. You get a taste of this in photo 5, but you'll really see it in photo 9. I just took a small piece of a medium grit sandpaper, and went to town.
Materials Used for The Finishing Sections
Acrylic Paint
Glass for Water
Spray Bottle
Rags
Brushes in Various Sizes (Round and Flat)
Sandpaper
Step 18: Finishing - Chipping Paint Details
This was my favorite part of weathering, because no other prop we've made has had specific color paint detailing. I am referring to the dirty white on the clip, top and front nose piece, as well as the multiple colors seen across the side panels. I'm so prone to incorporating tons of color into my personal work, that when Ryan said we were making a gun with color other than grime, I was all about it!
As you can see in photos 4-5, this started with a batch of Titanium White layered with Parchment White acrylic. Because of Ryan's experimentation with Textured Gel Medium prior to the final pass of metal spray paint, I was able to choose where I left the white and where I left metal. By adding quite a bit of thick paint to my brush, I would dab and glide the side of my brush across whatever section I was painting, paying attention to the reference photos pulled from multiplayer gameplay. After this would dry, I would go back and apply the same dirt washes to these white areas as I did to the metal, in order to achieve that overall look, photo 1.
The same technique of thick paint was applied in making the side panels a faded red. I started with a deep crimson, and worked up to the lighter variations you see in the completed Digger Launcher photos.
Step 19: Final Details - Rust and More Dirt
This is where I couldn't stop working... and Ryan literally had to wait for me to "polish" rust and dirt in all the details he'd so meticulously built. I was going to make this thing look real! You can see the final passes of paint on the clip, and where the leather belt turned strapping was attached using superglue. I also continued to sand the leather to age it with the rest of the gun.
Photos 5-7 show how I worked during the final stages. Following the previously mentioned steps, I would make a pass on all 13 pieces (including the main body), building rust until I was able to achieve that ultimate worn and torn look. I focused on the areas where screws or bolts wouldn't be detached after original construction of the weapon, or anywhere that the Textured Gel Medium had been built up (front of metal grip.) When painting rust, I keep a few soft round brushes in my hand, each for a different step and color of the rust. Typically I begin with a cool toned dark brown and work lighter, brighter, and warmer, ending with a bright burnt red-orange. This is best seen on the main body under the side gears and panels.
Photos 8 and 9 show the previously sewn and tea stained cloth straps, hot glued into permanent position on a rusty gun. Ryan then pulled grease and dirt off of his car's engine to get the best effect, and you can see the final product in the last section!
Step 20: Finished Product!!!!!
Here's the finished product, and for higher resolution pics head over to our Flickr pages! Be sure to check out both, as you'll find some differences.
CitizenSnips - My Flickr
Ratherbein100acrewood - Dena's Flickr
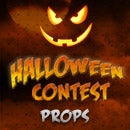
Second Prize in the
Halloween Props Contest
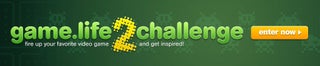
First Prize in the
Game.Life 2 Challenge
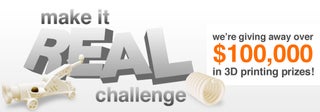
Participated in the
Make It Real Challenge