Introduction: Guitar to AV Receiver Interface
Article Features:
- Simple two transistor stage pre-amplifier circuit, with a high impedance input stage suitable for musical instruments with passive pick-ups and an output stage with enough signal level to feed AV equipment.
- A brief description of the processes I used to fabricate the clear acrylic case I made.
Step 1: Make the Circuit
The input stage of this amplifier circuit is a Common Collector amplifier which has high input impedance, low output impedance, and high current gain. The output stage is a Common Emitter amplifier which has medium input and output impedance, and high power gain. The input and output is decoupled from the 3V DC supply power by C1, C2 & C3, R1 & R3 control the base current of Q1 & Q2, and R2 & R4 control the output current of each transistor stage respectively.
I used point-to-point construction for this circuit, however it could be built on a PC board if desired. I used aluminum duct tape to form power rails on the inside of the acrylic case. Since the tape can't be soldered I used small pieces of tape to fasten the connection points to the components. It was challenging to make reliable connections with this method. Alternatively copper tape, or wire could be used.
Parts List:
- Q1, Q2 = 2N3904 (most general purpose transistors could be substituted)
- R1, R2, R3 = 10K
- R4 = 22ohm
- C1, C2, C3 = 35v 10uf
- 1/4" Mono Input Jack
- 2 RCA Phono Plugs (I cut the thread on back shell to form nuts for panel mounting)
- 2 AAA Battery Holder
- Project Box (this is an alternative to the custom case I made)
I used male RCA plugs as the output termination because I wanted a compact inline connection, alternatively female RCA jacks could be used with patch cables. I connected the RCA output plugs in parallel to feed both the left and right channels of the AV receiver.
AV RCA phono plug on center spacing on my receiver is 13mm with a 10mm panel mount hole.
Step 2: Custom Acrylic Battery Holder
I didn't have a 2 AAA battery holder so I made one using the same 2mm thick clear acrylic sheet scraps that I made the case out of. The method that I came up with to form spring terminals for the AAA cells is my favorite part of the project. As you can see in the close up image I soldered zinc plated springs to 8-32 zinc plated hex nuts to form the terminals which were then through bolted to the acrylic tray with 8-32 X 1/4" SS undercut flat-head screws. These were all parts that I happened to have on hand. I used strips of aluminum duct tape as conductors.
Step 3: Custom Acrylic Case
I worked for a marine products manufacturer for 9 years and learned much, including thermoplastics fabricating techniques. I had some 2mm thick scrap acrylic sheet on hand and decided it would be put to good use for this project.
One Piece 5 Sided Tray From Formable Sheet Stock
Designing
The technique used to design a 5 sided tray from one blank of acrylic is similar to the technique used for sheet metal forming. First determine the inside length and width dimensions desired, then determine the desired inside height. Multiply the inside height by 2 and add it to the inside length and width, this will give you your overall blank size. If you want the outside corners of the height dimension to be flush when formed you have to multiply the material thickness by 2 and add it to either the length, or width when doing the layout to cut the blank into a cross forming the tabs that will be folded forming the sides. I designed the case to fit over the battery holder forming a complete enclosure, and allowing easy access.
Cutting
Since I don't have access to a laser cutter I used hand tools. Acrylic can be cut with woodworking tools such as saws and routers. Thin sheet plastics typically can be cut with a score-and-snap technique, which I used for some of the cuts. I just used a sharp razor knife to score the cut lines several passes, then I held the score line against the corner of a table and with a quick but careful application of force snapped off the piece. For some cuts I used a hacksaw with a fine toothed blade.
Bending
I used the homemade small strip heating fixture seen in the image to heat the blank along the bend lines until the plastic is soft enough to bend. For critical tolerances a bending fixture can be built to ensure that the bends are precise. For this application I just did it by eye. You'll notice in the images for the blank that there are holes drilled at the corners of the bend intersections. These are relief holes to remove material that would interfere with forming the compound corner and eliminate a sharp point. A nice feature of this bending technique is that the formed corners are radiused.
Step 4: Final Thoughts
This was a fun and useful project. The pre-amp works quite well interfacing my guitar with my AV receiver. The pre-amp has enough gain that guitars with "Hot" pick-ups may overdrive the pre-amp into some distortion at high guitar volume.
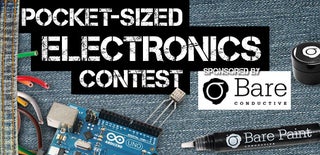
Second Prize in the
Pocket Sized Electronics
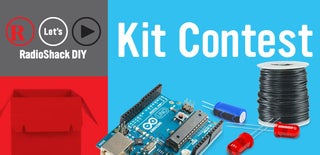
Grand Prize in the
Kit Contest
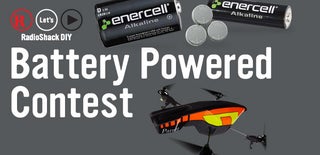
Participated in the
Battery Powered Contest
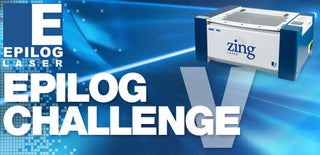
Participated in the
Epilog Challenge V