Introduction: Hacking Drills- Cheap/Powerful Gearmotors for Robotic Applications
This Instructable will cover the process of how to modify a generic cordless drill for use in robotic applications by removing the chuck and disengaging the slip clutch. It will also cover mounting options for the motors.
Why use a drill motor instead of a purpose built gearbox/motor like a Banebots P60?
1. Cost. It's around $80 for a banebots gearbox/motor and about $30 or less for a cheap drill.
2. Drills are designed to be lightweight, durable and powerful. (isn't that we want in a motor?)
3. They are almost the same thing as a Banebots P60, but with more plastic. they have a similar final output speed*, and identical motors in most cases.
4. You get a battery and charger, which are always useful.
I use two of these in my top ranked combat robot Phoenix
* Banebots 26:1 gearbox with a 550 size motor outputs ~900rpm, which is about the same speed that most cheap drills spin at.
Step 1: What You Will Need
1. Cheap cordless drill such as the Harbor Freight 18v 900rpm drill but any single speed 500-900rpm drill with a 3/8" chuck will do.
2. V-Jaw Pliers
3. Snips
4. Cordless Drill (will not be disassembled)
5. 2 10-32 set screws and hex key for them
6. Philips and Flat Head Screw Drivers
7. 1/4" or larger hex key (it need to fit in the drill's chuck though)
Not Pictured
8. Steel pipe preferably about 2-3' long and 3/4" or smaller diameter
9. Table mounted vise
Step 2: Removing the Chuck Pt.1
Drills have a reverse threaded screw to hold the chuck on. The chuck is not reverse threaded. This is done so that the chuck can't unscrew itself in normal use.
In order to remove the chuck you have to take out the reverse thread screw...
How you do that is fairly simple.
1. Place the drill in your table vise. (like in the 2nd picture)
2. Open the chuck all the way
3. Grip the part of the chuck that you don't spin to open it (caption on 2nd picture)
4. Insert the your other drill with Phillips Head bit and extender attached into the chuck of the condemned drill. (3rd picture)
5. Hold the chuck with the V-Jaw pliers and unscrew the reverse threaded screw (set the non condemned drill to spin clockwise)
Do not lose the reverse thread screw. They are hard to buy and expensive and you might need it later to mount something to the output shaft of the gearbox.
Step 3: Removing the Chuck Pt.2
Warning Be Careful and Use Good Judgement With This Step Because Getting Hit With a Piece of Pipe Isn't Fun
Now that you've got the reverse thread screw out, you can remove the chuck
(With the drill still in the vise from the previous step)
1. Take the 1/4" or larger hex key, insert it in the chuck and then tighten the chuck.
2. Slide the piece of pipe over the hex key. (basically it's a cheater bar)
3. Insert the battery (if you already haven't) set the drill to counter clockwise, set the clutch to "drill", grab the pipe or let it push against your workbench and give the drill full power.
4. The chuck should unscrew itself, if it doesn't, try a bigger cheater bar.
Step 4: Removing the Clutch
Removing the clutch is easy. As in unscrewing two screws easy... Once you do that the clutch should fall apart. See the pictures for further instruction...
Once you remove everything you need to lock the gearbox in the "drill" setting. To do this you insert a setscrew in a hole where the ball bearings used to be and tighten it until it doesn't slip. I tend to put two screws in, (one on each side) for redundancy.
Step 5: Removing the Gearbox/Motor
At this point your drill should look something like the one pictured below.
You could keep your gearbox/motor inside the drill and use the drill to mount it but it's kind of large and bulky... I always take them out of the drill and mount them with other hardware which I'll cover on the next page.
Step 6: Mounting/Interfacing
The best mounts I've found are the kitbots drill motor mounts but hose clamps also work. I've also made my own mounts out of UHMW plastic but wood would work too. (See picture)
Interfacing typically requires use of a lathe or purchase of custom parts.
If you are making your own adapter, the shaft's thread is 3/8" -24 UNF
If you are planning to mount a 2-5" rubber wheel to the gearbox I recommend kitbots.com's hubs and colson caster wheels this combination is very common on combat robots.
Or your other option is to put the chuck back on and have it grip whatever you are planing to connect to it.
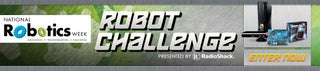
Participated in the
Robot Challenge