Introduction: Hand Bowl
Here's a small bowl I made from interlocking layers of birch plywood. I designed it using Poser, Blender and Autodesk 123D Make, then used a laser cutter to precisely cut all 40 of the pieces.
The bowl stands at about a foot in height and, despite being very light, is sturdy and extremely well balanced so it won't topple over when filled.
You can now buy a kit for this bowl on the Instructables Store. We're making these ourselves at the Instructables Lab, so supply will be limited!
Step 1: Modeling the Hand
The first step was to model and pose a hand to act as the bowl's base. For this, I used a piece of software called Poser by Smith Micro. Poser is a 3D modeling package that specializes in modeling and animating human bodies. It comes with a library of basic figures that can be easily posed using a very intuitive and beginner-friendly interface. I used one of Poser's default hand models.
When posing the hand, I had a few things to bear in mind. Obviously I wanted all of the fingertips to touch the ground at the same level so that the bowl would stand upright. I also had to think carefully about the way I splayed out the fingers. The fingers needed to provide as broad a base as possible while also looking natural and comfortable (Poser does nothing to stop you contorting its models into grotesque and unnatural positions, so this is trickier than you might expect).
A more subtle issue was to do with how I knew the model would eventually be sliced when I exported it into 123D Make. I knew from the outset that I wanted this bowl to made of radial slices converging somewhere around the base of the palm. This meant that I had to position the fingers so that they all roughly pointed straight outward from the same spot (so that each finger would contain a slice of plywood). Any major misalignment would make slicing the model impossible. This is an excellent example of how crucial it can be to visualize the entire design process of a project before you even start modeling.
Step 2: Adding the Bowl
I exported the hand from Poser as an OBJ file, then imported it into Blender, a free and open source 3D modeling program. In Blender, I modeled a simple bowl by using basic Boolean operations between three spheres.
I positioned the bowl above the hand and connected the two by extruding a segmented stalk from the wrist, which I then manually posed before using the "Smooth Vertex" to achieve a smooth, flowing path between the parts.
I also used Blender to make sure that all of the fingertips were level, by slicing them all off with along the same plane. Nothing's more annoying than wobbly furniture.
Note again that I had to carefully consider how I planned to slice this up in the next step. For example, if the connecting stalk protruded too far to the rear, then it would become structurally weak as fewer radial slices of the model would reach all the way out to its extremities. Remember: if you're using radial slice of wood then the further from the center you go, the flimsier your structure will become.
Once I had everything positioned and joined, I exported the model as a single STL file.
Attachments
Step 3: Processing in 123D Make
I imported the STL file into 123D Make, a free app that lets you easily slice up 3D models into 2D vector files for laser cutting. I was actually using a preview version of 123D Make that isn't yet available to the public, so I was able to slice my model radially rather than just orthogonally. Don't worry, though! The public version of the software will be getting regular updates, so you should also be able to use these features in the coming months.
In 123D Make, I set the number of radial slices to 14, then fiddled with the radial center and rotational offset until I had the slices aligned with all of the fingers, so that each finger contained its own slice. I then tinkered with the number and position of the horizontal slices until I had something that looked sturdy and aesthetically pleasing and exported all of the components as EPS files.
On of the cool things about 123D is that it lets you readjust your material and object dimensions on the fly. This means that I could easily recreate this project in cardboard (which I actually did for several of my prototypes) or in thicker wood to make a much larger bowl. Heck, with enough plywood I could even make this thing into a chair!
I've included the EPS files necessary to make this bowl from 0.2" plywood or 0.157" cardboard.
Step 4: Lasering!
I used the Epilog laser cutter at the Instructables Lab to turn a big sheet of 0.2" plywood into a big sheet of 0.2" plywood with lots of oddly-shaped holes in it. I cannot stress just how much easier life is when you have a finely tuned laser that can cut through wood.
Step 5: Assembly
Once I had all of the pieces cut, it was just a matter of assembling the bowl. This is much like those wooden dinosaur skeleton kits that I'm sure we've all played with as children (and adults). 123D Make labels each piece for you, so it was much less of a frustrating jigsaw puzzle than you might expect; I just lined up each slot according to number and pushed them together.
The slight puzzle element appeared when I unthinkingly assembled 90% of the bowl and was then left with a few pieces that couldn't be added until I removed about 70% of what I'd already assembled. Ah well, you live and learn. This goes back to what I was saying earlier about trying to visualize a design in its entirety before you start manufacturing.
Step 6: Early Versions
- The bowl being off-balance, so that it tipped backward under its own weight
- The bowl being too low, so that it obscured the hand
- The hand not looking handy enough
- The bowl not looking bowly enough
- The stalk not looking creepy enough
- The bowl angle being too steep, so things would fall out
Step 7: The Final Bowl
And just like that, I had myself a handy little bowl, perfect for any desk, kitchen table or mad science laboratory.
Take a look at my Computer Assisted Gift Wrapping Instructable to find out how I made a presentation box for this bowl.
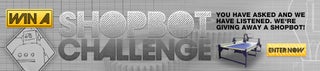
Participated in the
ShopBot Challenge
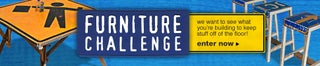
Participated in the
Furniture Challenge