Introduction: Hand+Ink Letterpress in Aluminum
I recently had some time to revisit my mini letterpress project. After using the earlier design for awhile, I wanted to redesign the press to eliminate all 3D printed parts and make it out of metal for increased strength. This press can be made out of MDF or Aluminum with a few quick dimension changes. The files attached are for 5mm thick aluminium sheet. Almost of of the parts can be cut with a laser cutter/waterjet/cnc, although I did use a lathe to make the wood handles and the top cross bar. All dimensions are in mm since I have recently moved to Sweden.
Materials:
For press:
320mm x 290mm x 5mm aluminum sheet
30 mm x 30mm x 300mm block of wood for turning handles
10 Cap nuts - (McMaster source)
1/4"-20 All thread rod
Thin MDF to make printing plates
To print:
Any type of thick paper or card stock, I prefer cotton paper
Printing ink, I tried aqua-LINOPRINT. It dried a bit too fast but was easy to clean up.
Brayer to roll the ink
Acrylic or glass plate to spread the ink
Tools:
Laser cutter
Waterjet/CNC
Lathe
1/4" Allen key
Step 1: Waterjet Files
Main parts:
Cut the attached DXF file using a water jet. I used 5mm aluminum. If you want to use a different material thickness adjust the inside squares width and height to your new thickness. Remember to space them out correctly to account for the thicker or thinner material.
Cutting aluminum on the water jet is not as accurate as laser cutting MDF. The nozzle shoots out a beam of high pressure water and cutting abrasive and as it hits the material the beam slows down. This creates a taper as the beam cuts through the material. The thicker the material, the more pronounced the taper. The 5mm aluminum had a noticeable taper that required a fair bit of filing and sanding to get the parts to fit together correctly.
The press worked well in MDF. I would suggest cutting out a few extra handle levers and stacking them together for extra strength.
Other parts:
Cut the all thread to roughly 50mm, you will need three of these.
If you have a lathe, turn a small handle that is 50.8mm long and 20mm in diameter. This will be the small front handle.
The larger handle is 160mm long and 28mm in diameter. I used a band saw to cut out the slot for the aluminum lever to fit into. I put the wood handle and aluminum lever together and drilled two holes. Dropped a rivet pin in both holes and peened the ends to hold the two parts together.
Step 2: Assemble
Once all of the parts are cut out and finished, assembling the press is straight forward. Build the lever system first and then build the frame around it. Tighten all of the cap screws using the appropriate allen key.
I ran into some issues with smooth movement with the aluminum version. It was resolved with a fair bit of sanding and some lubricating oil.
The MDF version should would quite well without much extra work.
Step 3: Lasercut Printing Plates
You can order professionally made polymer plates for high quality results.
I experimented with laser etching printing plates from MDF. The results were surprisingly good.
Illustrator:
Draw your printing plate design in illustrator. The max impression area is the size a of standard American business card: 2 x 3.5 inches.
Convert all text/strokes to outlines. Copy and paste your design to a new art board and mirror design. This is a very important step. If you forget to mirror your design, text will be backwards when you start printing.
Laser Etch:
The MDF plates were etched on an Epilog Zing 16 Laser. Find a local tech shop so that you can experiment with etching the plates; Luckily I had access to a laser through my university. I ran the raster engraving at 100% power and 60% speed. This was done three times to achieve a depth suitable for printing. I've attached a few sample printing plates you can engrave.
Print:
Use double sided tape to attach the printing plate to the removable aluminum platen - the piece with the small handle.
Attachments
Step 4: Print
The key to a good print is in the ink application. Too much ink and it will be heavy and uneven. Too little and it won't fill out.
The results from MDF printing plates were quite crisp. Not as good as a polymer plate but good enough for printing small things for fun. The spark plug card had details that were smaller than a millimeter and it performed well.
Step 5: Results
With the aluminum press I was able to achieve enough pressure to deboss the paper.
After using the MDF printing plates, pieces of the design fell off under the repeated pressure.
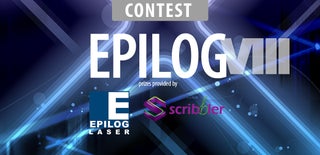
Runner Up in the
Epilog Contest 8
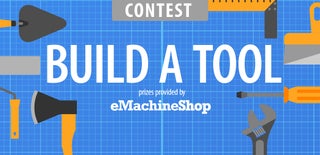
Participated in the
Build a Tool Contest 2017
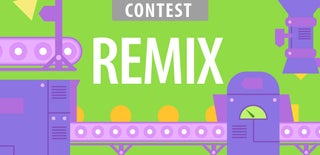
Participated in the
Remix Contest 2016