Introduction: Handmade Knife and Sheath
A good quality knife is an invaluable piece of kit for camping, carving or any out doors activity. Wooden knives can a lovely and very individual object, due to the grain and method of construction. Depending on what its going to be used to do the design of a knife can change substantially, making them very personal objects.
What better way to make sure that you have an beautiful, individual and personal knife than to make one your self.
I'm in no way a blacksmith, though being able to forge your own blade would be amazing, so i bought my blade from here: Tamarck Outdoors
The Brass bloster and sheath leather also came from this shop. Everything else i either already had or got from someplace else.
Materials:
Blade
Brass bolster
Wooden block
Deer antler
Glue (something strong, i suggest Araldite or similar)
Leather (large square for sheath and extra for details)
Thick thread (I used waxed linen)
Warm water
Linseed oil
Tools:
Saw (for wood and metal)
Plane
Hammer
Clamp x2
Large file (flat)
Small file (flat and round)
Knife
Rasp
Sandpaper (P60-P240)
Cloth
Small bowl (for oil)
Large Bowl (for water)
Large sewing needle
Step 1: Preparing Your Materials
The very first thing that you need to do is see what materials you have at hand, this might inform the shape or design of the handle based on what you have. I looked about and found a few bits of wood. I chose a block of oak (from the leg of a table my gran was throwing out) and a piece of deer antler i had laying around.
After looking what you have decide on a design, i went for the oak handle with a deer antler piece on the butt. Shape wise i went for a curved grip that slightly widens out at the butt, so that it doesn't slip from the hand.
The first thing to do is to clean up the block of wood, you need to be certain that the edges are all smooth or the joints between your pieces will be wonky and you don't want gaps. Once the block is cleaned up it should be easy enough to draw your design onto the block. I traced round the brass bolster on to the top of the piece so that i would know where to drill my holes.
I also cleaned up and shaped the piece of antler that i was going to use.
Step 2: Shaping and Fitting the Tang
The tang is the part of a knife that fits inside the handle, the more room it takes up inside the handle the stronger the knife will be. That's why for the strongest knives we use tangs that run the full width of the handle (called a full tang knife), the blade that i have only has a narrow tang designed to be hidden by the handle.
The first thing to do is to take a drill bit and measure it against you tang. This is because you can only drill as far as the bit allows therefore the tang has to be that length too, using a hacksaw and file cut your tang to the length you will be able to drill into the wood.
The next step is to fit the brass bolster to the blade. The tang may be a little thicker than the slot on the bolster so carefully file down the tang. You want the bolster to be a tight fit but still have to get it up to the base of the blade without damaging it. The occasional tap with a hammer wont do it to much harm.
Now your going to drill the holes to fit the tang. This needs to be done very carefully or your handle will be a little wonky (this is what happened to mine). This step would be much easier with a drill press but i had to do without which is why the holes aren't quite lined up.
Now check your tang fits.
Does it? No? not a problem. Rather than just hammering it in (really tempting), use a small file to make the hole larger its worth having a bit of room round the sides for the glue to fill,
Better fit? Good, now you can remove the tang. Its time to get sticky.
For the glue i used a rapid setting resin. I've tried to use contact adhesive in the past and it simply isn't strong enough. The only problem with this is you have to be quick.
Mix your resin, pour some into the hole till its about 1/3 full, spread some on the tang and a little on the base of the bolster. Put the Tang back in to the hole, making sure that all available space is filled with resin, wipe away and excess that's dripped out of the sides.
Now you'll want to apply the clamps. Clamp them as tight as you can, make sure that they cant slip off (cable ties) and leave it for about 2 to 3 weeks to allow for the resin to totally set.
Step 3: Fitting the Antler
Once your handle is securely fitted to your blade you can release it from its clamps. A quick sanding of the bottom of the handle and the top of the piece of antler to make sure that they are totally flat and will sit flush is a good idea.
I now made a small hole in the bottom of the wooden handle and a corresponding hole in the center of the antler. Using a little resin i glued a small piece of wood into the based of the handle to act as a dowel between the two parts. Filling the hole in the antler with resin and covering both the base of the handle and the face of the antler i pressed them together and clamped them as before.
Your now ready to start shaping the handle.
Step 4: Shaping the Handle
The easiest way to shape the handle of your knife than with a knife, at least in the initial stages. I shaped mine to fit the curves of my right hand.
Using a knife i got the handle to a very rough outline of how i wanted it, smoothing it down until i had the rough outline of what i wanted. The next step was to use a rasp to remove any lumps and give the edges a nice smooth round shape.
Finally a file was used to get an even surface over both the wood and antler parts. Once it was all smoothed over i was ready to start sanding.
Step 5: Sanding the Handle
As with most hand made wooden projects sanding is one of the most time consuming parts, though i find it to be rather therapeutic.
I started with a P60 grain paper and worked my way up to P250
Step 6: Oiling
Its important to preserve your knife so that it isn't damaged by water, and it also makes it look much nicer. One way to do this would be to use varnish; however a way that looks much nicer and brings out the grain of the wood much more clearly is to use oil. As the handle of your knife isn't going to come directly into contact with any food you can use an oil that will leave a taint or taste. The best oil to use for preserving wood is boiled linseed oil as it contains no water, although it does leave a taste and can be harmful if ingested. For a knife that will be used with food a lot i would suggest using sunflower oil or walnut oil (only if your not allergic to nuts, obviously).
Oil is really easy to apply to your handle. Simply rub it down with a clean rag to remove any excess sawdust, pour some oil into a dish and use the rag to generously rub it into the wood. Leave the knife for a few hours before applying some more oil. Keep this up until the oil is no longer soaking into the wood.
Give it a quick polish and your knife is ready. Now for the sheath.
Step 7: Sheath Design
I had a fairly good idea of what i wanted from the sheath before i started. I wanted it to be in the friction style sheath, I also wanted belt loop so i could keep it handy whilst i'm working. I drew out a few designs on paper to work out what i wanted exactly. I then broke this design down into the component pieces that i'd need to make it. I cut these out of the paper and made a practice sheath to check the fit and shape.
After a few alterations i felt i was happy with the design so drew the shapes onto the leather (with a little extra round the edges for stitching)
Step 8: Preparing the Sheath
Now i've got all my leather parts cut out i can start to assemble them. I figured it would be easiest to sew on the belt loop before i stitched the rest of the sheath into its final shape, this way i can properly secure it in (this didn't quite work out but we'll get to that later.
To save myself from buying a leather stitching awl i attached a nail to a bit of wood and used this, along with a hammer, to punch the holes through the leather to allow me to stitch it. For the thread i used a waxed cotton one, however this has become a little discolored with time so a synthetic thread might stand up better.
The next step is to wrap your knife in cling film and tape it up so that it's totally water tight. However try to make sure the wrapping sticks to the general shape of the knife.
Now go put the kettle on. Make yourself a cup of tea, you deserve it.
Relaxed? Good. You can pour the excess boiling water into a bowl big enough to fit your leather in. Soak your leather in the hot water for a good long while until it become supple and malleable.
Remove your leather from the water and start to wrap it around your now waterproofed knife. I used clamps and bulldog clips to hold the leather in place around the blade whilst it began to dry and take on the desired shape.
Using the same method as before i stitched the seam closed and then left it to dry for a few days.
Step 9: Refining the Sheath
If your happy with your sheath the way it is then grand, you're all finished. Have fun and try not to cut yourself.
For those of use who aren't as careful or haven't tried this sort of thing before it might be worth doing a few touch ups or refinements.
As i mentioned before the addition of my belt loop didn't work as expected. As the two pieces of leather began to dry they started to separate. This meant that the stitching came loose on the beltloop, making it feel less secure and look a little scruffy. My fix for this was to simply cut it off.
Another issue i found, possibly caused by flex in the cotton thread or my shoddy stitching was that the tip and mouth of the sheath started to expand a little bit along the seam. For the tip a simple cross stitch was enough to close the gap. For the mouth i glued a strip of thin leather over the expanded area to cover it and make the knife sit a little more snugly in the sheath. I also glued a band of this leather around the sheath to add a little decoration.
Through using the knife i've come to find how i prefer to carry it, and so now i have added a leather cord to the top of the sheath to allow me to attach it to my belt and have the sheath out of the way in my pocket.
Step 10: Update
Whilst kneeling down to take a shot on the range, with the knife in my pocket, the pressure of it pressing against my leg the antler piece popped of the end. The wooden dowl has now been replaced with a pit of M5 threaded bar and each hole tapped to fit it. This seems much a much stronger way of doing it.
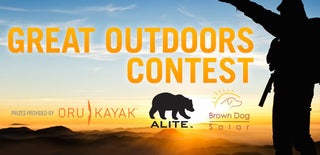
Participated in the
Great Outdoors Contest