Introduction: Harvesting Your Own Clay, Dirty But Delightful!
One of the many wonderful things about nature is that it provides so many wonderful opportunities to create with what is available to us.
Sand becomes glass, trees become homes, fallen leaves provide a winter blanket, everything serves more than one purpose. This Instructable will help guide you in finding and further creating works of art from what might otherwise be deemed a mere chunk of mud.
Put on your dirty duds, and follow me to the creek. Let's get digging!
Step 1: Tools and Materials Needed...
Processing your own clay, contrary to what some might say, is not an expensive proposition, nor does it necessarily call for arduous labor. A few supplies which may be taking up space at your residence are easy to come by, and just as easy to substitute.
- Buckets, containers, pails, or something in which to carry clay
- Hands. Two are helpful.
- Turkey baster, or suction hose
- Plastic tub or other container with a lid to store clay in while it soaks in water
- Shovel, hand trowel, or other digging device
- Approximately one yard of cotton cloth, or a large T-shirt for straining clay
- Glass jar or clear plastic container / jug for terra sig
- Fine sieve (40 mesh is good), colander, screen, or other material to strain debris
- A yard or so of Muslin fabric
- Stick, spoon, or other long-handled tool to mix the clay water. I use my hands and arms.
On occasion, I also use an all-purpose mixer, which attaches to a power drill for super-fast mixing of clay and water. If you do use a mixer, do so only after you have removed rocks and other debris from the clay water to avoid jamming the tool.
* Kiln (if you create a finished item you would like to keep)
If you would like to try your hand at a DIY kiln the primitive way, be sure to check out the fabulous Instructable by member Bigtoothcow, who created an excellent how-to entitled DIY PRIMITIVE POTTERY FIRING.
The purpose of this Instructable is to provide details for processing natural clay. While firing is the final stage of working with clay, consulting the instruction manual for your kiln would be best. My kiln instructions, for example, would likely differ greatly from more updated models, as it is a manually operated, 36 year old Evenheat. More firing information is available in the step titled 'Fire In The Hole'.
One of these days, Santa will stop here with a new one. ;-)
Step 2: Find a Source of Natural Clay...
Creeks, river banks, lakes, ponds, and other bodies of water such as a shore will often yield natural clay, which can be collected and processed for handwork and pottery. It may be in dried form if the water has receded, or in the case of a creek, run dry.
The above images show erosion in what is typically a flowing creek during the rainy season. As summer approaches, and the creek dries up, clay deposits are revealed. In our home state of Oklahoma, the clay is iron rich, which results in a deep orange, or red color. This red clay is often referred to as ultisol, which is one of twelve soil orders, according to United States Department of Agriculture and the National Cooperative Soil Survey
If you haven't visited the USDA link above, I highly recommend it for fascinating information.
If you look closely at the third image in this step, you can see the large cracks in the creek bank. A few good scrapes with a pocket knife indeed confirms the beautiful orange/red color of clay. Time to grab a few buckets and a shovel!
Step 3: Know What to Look For...
Depending on where you live, you may have encountered clay soil. Here on our property in Northeastern Oklahoma, one can hardly put a shovel into the soil without finding clay, which on one hand is a good thing, but not for the garden.
It would be helpful for you to contact your local county extension office with questions about clay soil in your area. Extension offices are notorious for having wonderful records, maps and other valuable resources to tell you all you need to know about where to look, if at all, for clay deposits.
At our home, we watch for little mounds that look like a compilation of spit-balls, created by crayfish, otherwise known in our state of Oklahoma as crawdads, based on the local lingo. Looking for clay in the rain is quite useful, as the dirt will often be washed away by the rainfall, while the clay remains. Our area is chock full of red and also dark grey clay.
Step 4: Sample Test and Terra Sigillata...
Unless you are familiar with natural clay, it would be a good idea to take a small sample. In a short period of time, you will be able to determine whether you have collected sand, mud, clay, or likely some of each. If your test yields a very low percentage of actual clay, you may need to examine your collected soil area for a better source.
Gather a good handful of what you are confident is clay, and process it in one of the following ways:
1.) Collect a chunk of clay, allow it to dry, smash it into small chunks, then soak.
See step #6 for detailed instructions.
2.) Toss the entire chunk into a bucket of water, stir on occasion to break up the clump
See step #5 for detailed instructions.
No matter which step you choose, only a sample is necessary. You don't want to gather a lot of material only to discover you've collected nothing more than mud.
In the photo shared in this step, you will see what looks like a glass of leftover iced coffee that sat out overnight.
- Note the layer at the very top, which is water.
- In the middle, a thin strip of valuable good stuff, called Terra Sigillata, which translates to 'sealed earth'.
For ease of reading, it will be abbreviated as terra sig or terra from here.
- Bottom layer - clay, sludge, and other sediment. This is the layer we will harvest for workable clay.
In this step, we will address the both the bottom layer, and also the middle layer, which is basically a wonderful suspension of the finest clay particles. This slippery liquid is very useful as a glaze, and depending on the clay body, can produce a glossy, or even a satin finish. If you are experimenting with harvesting your own clay, I highly recommend dabbling a bit in using your own terra sig, even if only for the experience. For a wealth of information regarding this wonderful by-product of harvesting your own clay, I highly recommend a visit to Ceramic Arts Daily
If you wish to collect a bit of Terra, use a turkey baster to suction the water from your test sample, which will expose the next layer of Terra. Use the turkey baster to gently suction only the Terra from the sample, and transfer it to a jar with a lid. Baby food jars are perfect for storing terra. Save until you are ready to glaze an item which has been previously fired in a kiln.
Once you determine if you like the finished look of an item glazed with sig, you can collect even more, as it stores well when kept sealed.
Once you have remove the first two layers, water and terra sig, the 'good stuff' is at the bottom. Put your fingers into the bottom layer, and you will be able to feel the thickness, compared to the previous two layers. If you do not feel anything thick that resists your fingers, you may need to go back to the collection site and try again.
Not up to trying to make your own? You can actually order TERRA SIGILLATA from The Ceramic Shop
Step 5: Going for Bulk - Collect and Soak the Clay in Water...
Once you have conducted a sample as explained in the previous step, and have determined there is in fact clay in your soil, you may now collect more, depending on your quantity needs. A truckload is not necessary at this time, but once you realize how much fun this process is, you might want to gather that much.
In a container that will hold a large amount of soil and water, such as a plastic storage tub with a lid, place the chunks of soil, and add enough water to cover the soil by several inches. It is best to have a lid for your container, to keep falling leaves, mosquito larvae, and other debris from falling into your soaking clay. (*)
In a few hours, reach into the mixture to see if it has softened, squeezing the clumps of mud. This process will likely take several days. As you mix the mud with your hands, remove any rocks, chunks, and other large debris. We will fine tune later, so don't worry about the small stuff at this stage.
As the soil soaks, it will begin to separate into layers.
This method is often referred to as the 'water extraction method'.
Step 6: Optional Processing...
*NOTE* Another way to hasten the process is to allow the chunks of soil to completely dry out, then smash them into smaller pieces before soaking. However, allowing dry time takes up time as well, and is not the best method for me, due to sensitive lungs, so this is why I prefer to simply soak and walk away.
- Scoop the quantity of clay desired, and smash into smaller bits.
- Pour the clay into a shallow dish.
- Add a bit of water, a bit at a time, mixing as you go.
- Once the clay has reached a thick and pasty consistency, mix well.
- Pour onto a flat surface, and allow to dry until pliable.
Step 7: Settling and Sediment...
This step is similar to the glass test conducted in earlier steps, but on a larger scale.
Once the soil has softened enough to thoroughly mix with your hands, you can allow it to settle.
This is done by simply walking away for several hours, or even better, an entire day.
The next day, you will notice the contents of your tub have separated into multiple layers, which include clay, water, soil, debris and such.
Step 8: Begin Removing Clear Water From the Top...
After the clay and soil has soaked for a few hours, or even better, a day, you can begin to remove the excess water from the top of the buckets. Be careful not to disturb the layer beneath the water.
A suction hose or a turkey baster is great for removing that last inch or two of water, but don't worry if you can't get every bit of it, as it will evaporate once we begin straining the clay through cotton cloth.
Step 9: Testing, Testing, One, Two, Three...
Once you have removed the larger particles of debris, and your big bucket of muck has been soaking and is settled, you can reach into the bucket with your hands to get a good idea of how much clay vs. other materials you've collected. Your hand can discern the sand from the clay, as the clay will resist, and cling together.
Slowly insert your fingers into the mixture. You should feel water, of course, then, if you're lucky, a silky-smooth layer of very light clay water known as Terra Sigillata (see below). As you press your fingers further in, you should begin to feel the clay. Imagine stepping into this with bare feet. If you feel as though you could get stuck in the muck, you've likely processed a good batch of clay. This is a good thing!
If the clay is very silky, very slippery, and smooth to the touch instead of clumping, you may have Terra Sigillata, which can be used as glaze instead of clay. Imagine putting your fingers into a bowl of chocolate pudding that is soft set. That's the feel of terra sig.
Step 10: Strain the Clay Through a Cotton Cloth...
Using a piece of cotton sheet, or even better, a discarded cotton T-shirt, drape the fabric over a five gallon bucket, and secure the fabric so that it won't fall through when you add the clay and water mixture.
Note - unless you want a T-shirt that is permanently stained, as shown in image #4 of this step, use an old shirt you aren't worried about. Otherwise, it makes a neat conversation piece.
Once you've removed a majority of the water from the tub the clay soaked in, pour it into the T-shirt drape.
Allow the clay to drip for several days, if possible, keeping it covered to avoid falling leaves, bugs and such.
Step 11: Allow the Clay Mixture to Drain, Check Each Day...
After a few days, lift the fabric and the clay. If it feels too soupy, allow it to keep dripping a few more days. Otherwise, if it feels as though it is beginning to stick together in one lump, you may either leave it be for a few more days, or remove the cloth, secure the top, and hang it for a little longer.
I always use a sharp knife to cut away part of the clay to inspect the middle, to make certain I didn't collect a mud sandwich, as explained in the next step.
Step 12: The Unwanted Mud Sandwich - Avoid.
The sandwich shown in this step is an example of a bucket that was in the process of settling when another sample was accidentally added on top. As a result, the orange-colored clay must be scraped off, to avoid the darker sludge in the middle. It would be best to simply soak, stir, and start over if this is the end result.
Step 13: Making the Cheese Wheel...
Uncovering the blob of clay after it has been cleaned and dripping through cloth for a few days always reminds me of making cheese. Once you can remove a wheel shape from the five gallon bucket, it should be in, and stay in, a round, flat shape. Flop the clay on a flat surface, and cut into the clay. If you cleaned and strained the clay and water mixture as detailed in previous steps, you should see a beautiful solid chunk of clay throughout the shape.
Step 14: Tempering Test, and Plasticity...
As all clay, depending on its composition, handling and firing, behaves differently, it is important to know that not all clay can simply be dug, worked, and fired to success. The batch I acquired during the creation of this Instructable just happened to be, well, absolutely wonderful, and required no additional materials or clay.
Sometimes, the clay lacks plasticity, which is the ability of the clay to remain in the state in which you form it. If you form a sample snake and the clay cracks, it may be too dry. If the clay is loose and refuses to keep its manipulated shape, it may be too wet. See the image on this step as an example. The clay was rolled, then the edges intentionally curled up. They stayed. This is a good thing, a good sign!
Temper, also referred to as grog, is an additional material with silica and alumina, added to clay to assist with shrinkage and thermal shock. Think of it as the chocolate chips in a cookie, or nuts in oatmeal. A binding material, so to speak. If you are hand-building, or using a pottery wheel to form a vase, for example, you would want to add a smoother grog with a smaller grit, so as not to rough up your hands. Many potters agree that a clay body with about 20% temper should suffice.
You may use a number of added materials as temper, including, but not limited to sand, gravel, marble powder, pebbles, even aquarium gravel, if crushed into smaller pieces.
To test whether your clay body will behave better with grog, roll out a flat disc without any additional material.
Roll out a few more discs, adding a higher percentage of grog to each. Allow to thoroughly dry, and then inspect for cracks. The one that looks the best should be selected as the clay for your project.
If your clay lacks plasticity, you could easily add a bit of bentonite to the mix, preferably activated sodium bentonite. Research and testing are very important. You don't want to ruin your project, or your kiln. No matter what you decide to use, always practice safety and use common sense.
Step 15: Test Rolling...
Remove a small handful of clay, and roll it between your hands. If you are familiar with Oklahoma Red Clay, you will immediately notice the staining of your hands during this step, but don't worry, it will wash off your body. Your clothes, however, not so much, so be sure to wear clothing you don't mind staining.
If the clay is too sticky to roll into a snake shape, it may need to dry a day or two longer. Otherwise, roll a length of clay into a snake shape. Bring one end of the snake to the other end, and attach the clay to itself. The clay you are looking for will create a smooth snake without any cracks. Today's harvest gave us clay with wonderful plasticity, which is the ability of a clay body to keep its shape when formed, dried and fired.
Try a few different shapes, such as a shape that should stand up an inch or two. Try a flat disc. Maybe a round ball. At this point, you are only trying to determine whether the clay will hold together, and remain solid during the drying process, instead of cracking. Cover your samples with a piece of plastic, such as a dry cleaner's bag. Check back every other day, noting the color changes, which indicate dryness. Don't try to hurry the drying process.
Step 16: Make the Pieces You Wish to Keep...
What will you do with your clay? Will you make a bowl? A mug? Refrigerator magnets?
The possibilities are endless, though you should consider starting with a small project, so as not to be disappointed should something go awry. Try to steer clear of larger items, and items that require internal reinforcement, until you are familiar with the way your newfound clay will behave.
I like to use a thin sheet of plastic to cut items with a particular flat shape, as it produces a smooth edge. Any additional smoothing can be done before the clay reaches a dried stage.
Step 17: Allow the Project to Dry Completely...
In the image on this step, you will notice the difference in the color of two samples.
One is still in its raw, or greenware stage, while the other piece is lighter, having dried for a few days.
While the clay is typically fired after it has dried, it is not too late to sculpt, sand, or smooth any flaws that may have appeared.
Step 18: Fire in the Hole!
As mentioned in a previous step, my own kiln is a 36 year old Evenheat model, a far cry from today's modern, computerized kilns with fancy electronic controllers. (Starlight, star bright, first star I see tonight...)
It is always safest to assume that any clay you find and dig yourself should be fired as a low fire clay.
Firing at extreme temperatures may cause the clay to actually melt, and create a disastrous mess in your kiln.
Let us assume that 1300 degrees should be the maximum temperature for test firing.
My current kiln is rather large, and as a result, in order to utilize the amount of space, many pieces, although not necessarily required for firing, are preferred. Otherwise, it is complete overkill. There are many different kilns of varied size on the market today. Whether you are looking to fire large loads, or just a small item at a time, the kiln of your dreams is out there.
If you think dabbling in ceramics might be right up your alley, a wonderful starter kiln would be perfect. Larger kilns require special wiring, more room, and more often than not, permanent installation. The FireBox 8x6 LT Multimedia Kiln by Skutt is not only portable, but it can be simply plugged into any common household outlet and fired in a hurry. Better yet, you can fire glass in addition to ceramics, making this little box a powerhouse of productivity. Be sure to put this one on your wish list, and forget the hassles of manual controls and guessing games.
But wait, there's more! For only $9.99, no, wait. Wrong page. Instructables is currently hosting a CLAY CONTEST, so hurry up and post your own Instructable, one that fits the guidelines outlined in the contest description, entered in time for the deadline of October 17, 2016.
Don't wait for the last minute, as your tutorial will need approval before it is submitted to the contest.
You could win one of many exciting prizes, including a FireBox kiln, an assortment of beautiful glazes, ceramic tools, Laguna Clay and more! Not everyone lives near a creek or river bank, so finding your own clay isn't always possible. What could be easier than ordering online?
Also, if you already have an existing, clay-related Instructable created no sooner than August 22, 2016, you can enter that Instructable in the contest.
No kiln? Not to worry. You can still create little things that, although unable to contain liquids, can be carefully utilized. A dainty dish, perhaps a little figurine to set on a shelf.
Step 19: Clay for Another Day!
Now that you have a good amount of workable clay, be sure to wrap the remainder of it in a nice, tight plastic bag, or other airtight container to keep it fresh and pliable. It should keep for a very long time.
However, in the event you should discover your clay has been exposed to air and dried out, have no fear. Provided it has not been fired, it can be soaked and saved all over again. If it is still somewhat pliable, but very stiff, you can also put a very moist washcloth into a new plastic bag with the clay, and give it a few days to absorb the moisture.
Step 20: Let Your Creativity Flow...
Now what? Oh, there are so many things you can do, so much to make!
Will you glaze the item?
Have a peek at some of the wonderful glazes in a rainbow of wonderful colors and textures there are to choose from!
Will you allow your piece to be natural?
Will you use material, cookie cutters and other items to accentuate the piece?
Check out all the amazing things you can use to decorate the surface of your items.
Deciding is the hardest part. :-)
Step 21: Working on My Next Instructable...
This tutorial has given me the inspiration to create something new, beyond just the collection of clay.
I hope you'll stay tuned to see what I do with the pieces I've made while creating this Instructable. :-)
Instructables has been kind enough to offer a CLAY CONTEST, with many wonderful prizes.
If you have enjoyed this Instructable, I would greatly appreciate your vote in the contest.
If you decide to enter your own Instructable in the contest, be sure to check all the rules and regulations about entering, and pay close attention to the entry dates.
Deadline. The Contest begins at 12:00 a.m. Pacific Standard Time (PT)/8:00 a.m. GMT on August 22, 2016 (the "Start Date"). Entries for the Contest must be received by Sponsor by no later than 11:59 p.m. PT on October 17, 2016 /7:59am GMT on October 17, 2016 (the "Deadline"). Convert to Local Time
Perhaps you have entertained the thought of attempting to harvest your own clay. If you do, please return to share your experiences with the community. I hope you are inspired to try your hand at clay collection.
Many thanks, and happy mudding!
Step 22: A Very Grateful THANK YOU!
Today, I was notified that this Instructable had won the Grand Prize in a special contest.
I cannot tell you how very excited I am, and so very thankful for all the views, considerations, wonderful compliments and comments, and votes for this tutorial. No question, the competition was fierce, with fabulous projects, each and every one. Congratulations to everyone in the contest.
My heart is still skipping beats.
Thank you!
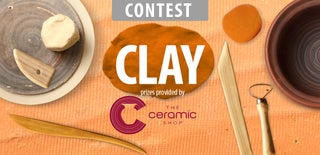
Grand Prize in the
Clay Contest 2016