Introduction: He-Man Power Sword Replica
The He-Man cartoon "MOTU" was my favorite as a kid. He-Man's sword, (Power Sword, or Sword of Power) played a huge part in the cartoon, without it, there would be no He-Man.
If you've ever secretly wanted to raise the Power Sword, and repeat the famous phrase, "I have the power", I can show you how to make your own high quality Power Sword. You'll need to be a patient person, and be ready for lots of detailed work!
Step 1: Template Creation
Proper Planning Prevents Poor Performance.
The beginning step will be one of the most important ones. A properly planned template will make way to a greater end result. Throughout this instructable, I will be referring to the He-Man Power Sword, but several of these techniques can be applied to any prop replica creation.
The first thing I do is find as many reference materials as I can to be comfortable with the layout of my project. For the Power Sword, I found some original artwork of the sword online, and traced it in Adobe Illustrator. If you don't have this program, try out Inkscape. This program is a professional vector graphics editor for Windows, Mac OS X and Linux. It's free and open source. The reason for using a vector based program is that once finished creating the template, it can be scaled to any size without any image distortion.
When tracing the template, the more complex the object, the more attention to detail should be kept. The Power Sword is very simple in design, so I made a quick tracing of the artwork to make my vector template. I wasn't as careful with some of the symmetry of the side view as I could of been, but I knew it wouldn't effect my end result.
Once I have my template traced, it has to be scaled to a proper proportion. I always use my own hands to determine a good size for a weapon. In some reference images of He-Man holding his sword, it appears that he could fit 1 1/2 of his hands on the sword handle. Using the sword handle of the image for scaling reference, I simply scaled my template to where 1 1/2 of my hands would fit it.
When my template is scaled properly, it's ready to print. Usually the object being replicated is bigger than a standard piece of paper. If possible, it's more accurate to have your template printed on a single sheet of paper from any business that offers printing services. If you're like me and too impatient to do this, the other option is to print the template out in portions on multiple sheets of paper, and then tape it all together. If you do the latter, be certain to take your time and properly line everything up. Also, print at least two copies of your template.
Step 2: Template Transfer
You've got a crisp, clean looking template. It won't stay that way for long. You're going to have to transfer your template onto your base work material (high impact polystyrene plastic, or HIPS, for this build). There are so many different ways to transfer your image. If your starting base material is a flat surface, you can just adhere your template to it. I've used this method with fine results, but the template needs to be well adhered to the base material so as to not peel off during the building process. The technique that I used for this sword build was to tape the template upside down to my base material. Next I "painted" 100% acetone (ACETONE MELTS POLYSTYRENE PLASTIC) over the image in small sections, and burnished the image onto the polystyrene. Acetone won't burn your skin, but it isn't the greatest thing to get on it, so wear gloves if you've got them.
With the template transferred onto the plastic, you can now cut it out of your material. Because I used thin plastic, I used scissors to do this.
Step 3: Symmetry Guides
The real building begins. For me, the best way to insure good symmetry is by using guides. These guides keep my filler material right where I want it.
Using the side view of the template, I measured how tall to make the "wall" and "spine" guides. These guides were cut from the same polystyrene plastic. Once they were all cut out, I stacked them onto each other and lightly sanded them all to the same height/shape/curve.
Using cyanoacrylate, I adhered all of the guides to their respective places, following the template pattern on the sword base. I glued pieces of MDF to support the "spine" guide.
Step 4: Fill Work
With the guides in place, it is now time to fill them in, and give the sword its body. This can be done with more than one type of filler material. I used Bondo body filler. Please wear a respirator, not a dust mask, when using automotive body filler; the fumes will damage your lungs. Also, wear gloves: nylon, latex, vinyl, nitrile, or anything similar.
My choice of using automotive body filler was because of its quick curing property. If you've never used it, it's very forgiving in the learning phase. Apply it in small batches though until you're comfortable with its physical properties. It's really sticky uncured, which is why you need to wear gloves. Despite it's stickiness, I've found that coating the polystyrene plastic first, especially the edges, with cyanoacrylate, will help prevent the body filler from pulling away from the plastic once cured.
One coat of body filler will not do the job, and don't try to make one coat do the job. Apply multiple coats. With each coat, you will have time before full curing of the filler occurs. During this time, use coarse grit sand paper, or lightly use a rasp to remove unwanted material. With each coat, you will have less unwanted material to remove, and should use a higher coarse grit sandpaper to avoid deep scratches. The bondo will gum up your sand paper quickly. Once you are happy with the overall shape, let it set to allow the filler to reach its full cure/hardness.
Do not fill in the circular cross guard corners with body filler. That space will be filled in using something with more control.
Step 5: Cross Guard Corner Buttons
To continue continuity and symmetry, the button corners are not made using body filler. Using a hole saw appropriate to the size of my template, I cut eight disks out of some scrap wood. I wrapped them with a piece of polystyrene to hide the grain of the wood, and make them slightly thicker.
To make the rounded tops, I poured polyurethane resin into a paint palette and let it set. After they were cured, I adhered them to the disks using 5 minute two-part epoxy adhesive. I always use this type of adhesive when attaching pieces that might need moving around to achieve proper alignment.
Once that was set, I adhered a piece of polystyrene half round to the overhanging lip of the dome for a softer transition between the dome and the disc. I filled in any gaps with glazing putty.
Be sure to have all of the polystyrene plastic joints line up on the same side of the disk.
If you want to avoid these steps to create multiple pieces, you could just make one of these button corners, and make a mold of it. I ended up doing this at a later point. The mold has come in hand for other projects like this one.
Step 6: Crossguard
Adhere the cross guard button corners to the sword base two at a time, the top two at the same time, and the bottom two at the same time. Face the seam joints toward the inside, where they will be hidden by filler. I used 5 minute two part epoxy adhesive to make sure their placements would match symmetrically.
The next addition isn't original to the Power Sword design, but I thought it would add a pleasing aesthetic. I added polystyrene half round from button to button, down the center of each cross guard column, to create a small spine on each column.
With everything in place, the rest of the gaps can be filled in. I did not use body filler to do this, but instead, two part epoxy clay. I did this because it has far greater control than body filler does, and can be done with one application. Use water to help smooth it out once the clay is in place. This clay takes longer to cure than body filler does, and when cured you'll want to use a medium to fine grit sand paper to do the final shaping/smoothing out of the clay.
Step 7: Imperfections
Now that this area of the sword is all filled in, the imperfections need to be found. I applied a thin layer of spot putty/filler over everything that might have a scratch, ding, high, or low spot. When the putty is set, sand it with a very fine grit sandpaper.
Your sword now has multiple colors on it, and because of this, it is very hard to see ALL of the imperfections that may still be in the sword. Primer spray paint will give the sword one uniform color, and reveal anything left to touch up. I like to use a filler primer. I had to get used to using this type of primer because it has a thicker consistency. This not only reveals the imperfections, but because it's a filler primer, it fills in minor scratches. You can wet or dry sand this primer. It has to cure for 1 hour before dry sanding, so I prefer to wet sand it, which can be done as soon as the surface is dry. The objective in sanding the primer is not to take it back to the filler material, but to create a smooth surface in the primer, and reveal any lasting imperfections.
Once all of the primer has been sanded, carefully look over the whole piece and mark any spots that needs touching up. Once all of these spots are found, glaze over them with more spot putty. Lightly sand these spots and check to see if any of them need another glazing over. Once you're happy with your touch ups, prime over them again. I suggest using a non filler primer because you don't need a thick paint build up. Use a primer color close to the color of the filler primer you used.
Step 8: Handle
I made the handle for this sword in sections. I used a wood lathe for the first time with this build. Having no experience using a lathe, I thought it would be easier, and far quicker, to use a piece of PVC pipe for the main body of the handle to keep the thickness of it uniform throughout.
Using the lathe, I turned the top and bottom piece for the handle. I used a caliper to make sure these pieces matched the width of the PVC where they would join together. I used MDF because I have a bulk supply of it. I would not use it again though because of its composition. Being that is is made of compressed fibered materials, it does not turn well. Use a respirator when using a lathe, no matter the material you're turning, there will be dust/particles of the material floating in the air and you shouldn't breath them.
Before taking the pieces off of the lathe, I primed them to make sure there weren't any imperfections, and more importantly, to seal the MDF. If MDF gets wet, it will expand like a sponge, ruining the piece you've worked on, another reason to avoid using it.
The bottom piece of MDF had the same "paint palette polyurethane" piece as the button corners added to it, to round it off. The MDF pieces were adhered to the PVC with 5 minute two part epoxy adhesive. Once they were set, I hid the joint between the pieces with filler spot putty.
Once everything was filled in, I went through the process of finding the imperfections through priming, wet sanding, and repeating these steps until I was happy with the look of the handle.
Step 9: Molds
I did not repeat building, filling in, and touching up to create the other side of the sword. I instead made a block mold of the work I had already done. This is an expensive step that doesn't have to be done; I did it because I knew that I would be making more than one of these swords. I also made a block mold of the handle because of this. If you use your PVC handle as is, it will be hollow and unable to support the weight of the blade. Fill it in with a solid and sturdy material, as it needs to be strong enough to support the weight of the sword. I will not be going through the molding process in this instructable as there are already many instructables explaining this process.
Step 10: Final Construction
If you didn't mold your sword, skip this paragraph. With the two identical copies of the one side of the sword, I adhered them together with 5 minute two part epoxy adhesive. Don't mix a big batch of adhesive and then try to spread it over the joining faces of the sword, instead, dispense parts A and B side by side wherever you want the adhesive, and then mix the two parts together. Join the two sword pieces together and once the adhesive is set, the seam in the middle of the sword will need to be hid. I first used two part epoxy clay to fill in the seam. Once that cured, I lightly sanded it with both medium and fine grit sandpapers, then smoothed the rest of it with spot putty. When I was happy with the hidden seam, I primed the whole sword again to find and fix imperfections.
The handle needs to be able to support the weight of the sword. There isn't any glue that I know of that is strong enough to do this. To achieve the support I wanted, I cut a piece of 1/4" rebar long enough to reach the middle of the handle, and extend about 7" out of the handle. Using a 1/2" spade bit, through the top of the handle, I drilled a hole half way into it. I set the rebar in the hole, and poured enough polyurethane resin into the hole to fill it up. I made sure the rebar was plumb with the handle until the polyurethane set. The polyurethane bonds to the inside of the handle, and the ridges in the rebar lock it into place in the polyurethane.
The same procedure is now done to the sword. A 1/2" wide hole is drilled far enough into the sword for the rebar to fit, and then filled with polyurethane. The rebar handle is put into the hole and properly lined up with the sword before the polyurethane sets.
If you aren't making casts of the the sword parts, you won't need a large amount of polyurethane. You can get small quantities of it here to accomplish this step.
Step 11: "I Have the Power"!
With a change of color, and addition of "stones", the Power Sword design was used for three different characters in MOTU. So, which character do you want to be?
There are many different finishes you can achieve, and so many different ways to accomplish it, that I'm not going to go into detail concerning this area.
The basic treatment:
Before you paint your sword, prime it (grey), if you haven't already, and let the primer cure as recommended. Next decide what look you want, and select the colors you need to achieve it. Using an airbrush, I paint in several layers starting with the lightest color first (silver). With each layer, I add colors to the silver to add depth and realism to the sword. I wet sand between layers with very fine grit sandpaper for a naturally worn look. Let the paint dry well, half a day to a full day depending on the current temperature of where you are, and then clear coat the sword. If you are using aerosol paints, check application times for re-coating and clear coating. I apply a minimum of 3 coats of clear coat. It will be really hard, but let the clear coat cure for at least a full day before you start swinging the sword around.
Once you get the swinging around of your sword out of your system, hang it on a wall to show off to all of your friends. You've got the power!
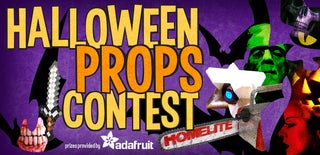
Fourth Prize in the
Halloween Props Contest 2015
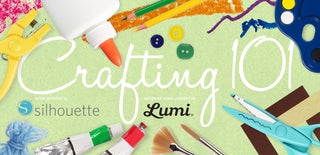
Participated in the
Crafting 101