Introduction: High Quality (and Safe) Nickel Plating
Just like my popular copper plating instructable, the aim of this is to do high quality, low cost, and safe electroplating. We will also be making our own electrolyte from scratch instead of buying chemicals online.
If you've looked at my copper plating tutorial, note that the process here is different. The nickel will not dissolve very well if at all in the vinegar without special help and adding hydrogen peroxide will destroy your electrolyte.
Nickel plating can be used for a variety of different things.
- It creates a corrosion resistant coating that will protect the base metal from oxidizing and rusting. It is frequently used in food processing to prevent contamination with iron.
- It can increase the hardness and thus the durability of mechanical parts and tools.
- It can allow you to solder to difficult metals.
- It can create a variety of beautiful decorative finishes that range from a chrome-like gleam, to brushed stainless steel color, to a metallic black. It just so happens that black nickel plating is used frequently in aerospace applications
- In thicker platings, it can make the object magnetic.
To get different finishes and properties, you may need to add other chemicals and metals to your plating solution (see the Post Prep stage). These chemicals will change the way the atoms arrange themselves and/or add other metals to your plating. If you are looking for corrosion-resistance, do not add any other chemicals to your electrolyte as they may cause the end plating to stain or tarnish. I unfortunately haven't had the time to work out cool combinations, so feel free to experiment and report back!
For a copper plated finish, be sure to check out my copper plating instructable :)
https://www.instructables.com/id/High-Quality-Copper-Plating/
On another note, I LOVE your questions! I have noticed that a few folks are asking the same questions, so I've added a "Common Questions" step/slide/section/whatchamacallit at the end of this instructable. Take a look there to get quick answers to most of the questions you might have. If you have a new one, comment below and I'll be happy to answer it and add it to my step/slide/section/whatchamacallit :D
A quick disclaimer - nickel acetate, the chemical we will be making, is poisonous. The title "High Quality (and Safe) Nickel Plating" is referring more to the fact that you don't need to play with insanely powerful acids that will burn your skin or ask you to open batteries. In the concentrations we will be working with, the process is fairly safe. However, do NOT drink the solution and be sure to wash your hands after plating and properly wipe down any surfaces that come near or into contact with your plating solution. Always supervise kids. That said, enjoy!
Step 1: Materials
Nearly all of the supplies can be found at your local supermarket. Finding a pure source of nickel is a little trickier, but should not cost more than a couple dollars. To keep from draining your battery in later steps, I very highly suggest finding an AC/DC power supply around the house.
Materials you can find at your local supermarket:
>Distilled Vinegar - 5% acidity or higher (grocery)
>Salt (grocery)
>Mason jar (canning)
>6V Lantern Battery (camping)
>Alligator Leads (electrical)
>Nitrile gloves (pharmacy or DIY)
>Paper towels (paper products)
>Cameo Stainless Steel and Aluminum Cleaner (cleaning supplies)
Materials you will likely need to buy online, at a good hardware/welding supply store, or a music shop:
Pure Nickel - You can get this a few different ways. I bought my nickel in the form of two 4oz plates on eBay for ~$5, a good hardware store should carry nickel welding rods, and most music shops will carry Ernie Ball "Pure Nickel" guitar strings.
You can also try to remove the nickel windings from old guitar strings if you are strapped for cash. It takes a bit of time, wire cutters, and pliers, but it can be done. Note that most nickel-wound strings contain a steel core that will pollute your electrolyte (Ernie Ball "Pure Nickel" strings should be pure nickel).
You can also try to use solid nickel door knobs and the like. I would warn you to be careful when trying this because a good chunk of "nickel" decorative items are plated themselves.
Optional, but highly recommended materials (also at the supermarket or a local electronics store):
A higher voltage, DC power supply - I am using an old 13.5V laptop charger. You can use "wall warts" (the ugly black AC/DC power supplies that come with some consumer electronics) or an old ATX (computer) power supply. Just make sure that it does, in fact, output DC.
A fuse holder
A fuse that is rated slightly less than the max current rating on your power supply.
Step 2: Preparing Your DC Power Supply (Optional)
In the next step, we will make our electrolyte. In order to do this, we will need a significant amount of electricity. Instead of wasting a moderately expensive batteries, it is much cheaper to use an old wall wart, laptop charger, or computer supply (assuming they aren't already being used).
My version is crude, but effective.You could (and probably should) make a little project box with a DC barrel jack, internal fuse, and two terminals poking out to clip the alligator leads to.
Wall Warts (the ugly black things that come with some electronics)
Cut the barrel jack off of the end of your DC power supply. Pull the two wires apart and cut one of the wires two or three inches shorter than the other - this will help prevent you from accidentally shorting wires together later. Strip about a quarter inch from each wire. Solder in your fuse holder and pop in the fuse! You are done! (see polarity notes below).
Laptop Charger
Cut the barrel jack off of the end of the DC power supply. Use a razor blade with light pressure to remove the outer jacket - you do not want to cut through to the inner core. Most chargers will have one insulated wire that is wrapped in many other bare copper wires. Twist the bare copper wires together to form a single wire. This should be your negative. Solder your fuse holder here. Strip about a quarter inch from the insulated wire and tie it back with a zip tie or electrical tape so it cannot short with your bare wire. Pop in a fuse. You are done! (see polarity notes below)
ATX/Computer Power Supply
These are a tad bit more complicated to turn into a useable benchtop power supply. Google (or search instructables for) "DIY benchtop power supply" or "ATX benchtop power supply". You should find a few different tutorials that will explain everything well :)
Lab Benchtop Power Supply
If you are super fancy and have the money, a standard adjustable power supply (which is what you would find in a lab) will work just as well. Just make sure you set aside your banana plugs for electroplating only.
Notes on Polarity
You will need to know which wire is positive, and which side is negative. If you are a pro with a multimeter, this should be pretty easy. If you don't know how to use a multimeter or don't have one, you can do this: Mix a pinch of salt into a little bit of water in your jar. Connect one alligator lead to the fuse and drop it into the water. Connect the other alligator lead to the non-fused wire and drop that in the water. The alligator lead that starts to bubble is your negative.
Step 3: Make Your Electrolyte
It is definitely possible to buy different nickel salts online, but where is the fun in that? Here, I'll show you to make your own nickel acetate solution for a lot cheaper than buying chemicals online.
Fill your mason jar with distilled vinegar leaving about an inch from the top. Dissolve a pinch or so of salt into the vinegar. The amount of salt is not all that important as long as you don't go crazy with it. The purpose of the salt is to increase the electrical conductivity of the vinegar. The more current that flows through it, the faster we can dissolve the nickel. Be careful though, too much current will lead to an over saturated solution which will lead to poor plating results. Use sparingly.
Unlike in the copper plating instructable I've done, the nickel will not dissolve into the solution just by letting it sit for a while. We need to electro-dissolve the nickel.
Place two pieces of pure nickel into the vinegar and salt solution such that part of both stick out and into the air and that they don't touch. Connect an alligator lead from the positive terminal of your battery (or a DC power supply) to on of the nickel electrodes. Do the same from the negative terminal to the other electrode. Make sure that the alligator clips don't touch the vinegar so they don't contaminate the final product.
The nickel source connected to the negative lead should start to create hydrogen bubbles and the positive lead should make oxygen bubbles. Truth be told, a very minute amount of chlorine gas (from the salt) will also form on the positive lead, but unless you put in huge amount of salt or are using a lot of voltage, the chlorine will just dissolve into the water like what you find in a swimming pool. The minute amounts of sodium, in case you are wondering, will react with the water to create sodium hydroxide.
For this step, I very highly suggest using a DC power supply that plugs into the wall (see the previous step). Dissolving the nickel will take a while and you don't want to drain your battery more than you need to - DC power supplies are reusable, most batteries are not.
After a little while (mine took about two hours), you'll notice the solution has turned a light green. This is your nickel acetate solution! Woot! If you get blues, reds, yellows, or any other color, it means that your nickel source wasn't pure. The end product should be a clear green - if cloudy, your have an impure nickel source.
The solution and nickel sources may become warm during this process - this is normal. If they get hot to the touch, you should disconnect your circuit, let it cool for an hour, and repeat as necessary. It is possible that you added too much salt, which increases the current, which increases the power dissipated as heat.
Step 4: Preparing Your Object to Be Plated
NOTE: Some materials, such as stainless steel, will not accept direct nickel plating. You will need to copper plate them first. See my copper plating instructable to learn how to copper plate: https://www.instructables.com/id/High-Quality-Copper-Plating/
The cleaner your conductive object, the better it will plate. You don't want any grease, oxidation (rust, tarnish, patina, ect), or general grime on your surface. Even if your surface looks clean, I can almost guarantee there is a fair amount of oxidation that needs to be removed.
Remove general grime and dirt with a little bit of dish soap and elbow grease.
Remove the oxidation and tougher grime with an acid-based abrasive such as Cameo. Don nitritle gloves and just mix the powder with a few drops of water on your glove and go to town!
You can further clean your object by reverse electroplating (ie "electrocleaning") it for a few seconds. Hook your object up to a positive voltage, a wire to the negative voltage, and drop them both in a vinegar salt solution for 10-30 seconds. This will remove any remaining oxidation.
For larger surfaces, try scrubbing them with fine steel wool and vinegar.
Step 5: Time to Electroplate!
For this step, you want to use your 6V battery. Even lower voltages (down to around 1V) will give you a better, shinier, smoother finish. You can use a higher voltage DC power supply for electroplating, but you won't get good results.
Place a nickel source into your green nickel acetate solution and connect it to the positive lead of your battery with an alligator clip. Clip the other alligator clip to the object to be plated and connect it to the negative lead of your battery.
Drop the object to be plated into the solution and wait for around 30 seconds. Take it out, rotate 180 degrees, and drop it back into the solution for another 30 seconds. Repeat as needed. You should move the alligator clip a new location after a couple dips so that the entire surface gets plated. Unlike in copper plating, the alligator clip shouldn't leave "burn" marks, just prevent the spot underneath from plating well.
The plating process should create enough bubbles that you won't need to agitate or swirl your object in the electroplating solution. For larger objects and containers, you may want to include a small aquarium pump (~$15) to circulate the solution.
Step 6: Post Prep
Now for post prep....Generally speaking, NONE! Nickel doesn't oxidize at room temperature and shouldn't tarnish. You can polish your end product with a light polish to get a bright gleam.
If your nickel plating is not as shiny as you'd like, polish it up with a light polish that doesn't leave waxes or oils behind, and then electroplate it again.
Adding small amounts of other metals such as tin during the initial electroplating will change the color of the plating (tin will give you a white colored metal like silver). Many metals can be electrically dissolved into vinegar just like nickel. The two main metals that cannot be electrically dissolved into vinegar are gold and silver (trust me, I've tried). Since I had some copper plating solution left, I mixed in a little bit of it with my nickel plating solution. The result is a matte, dark grey, very hard finish that feels like a chalk board (it squeaks like one too if you scratch it ). See the picture.
Unless you are an experienced chemist or have a friend who is, I would be very careful when adding random chemicals to your electroplating bath - you may just end up creating some toxic gas that isn't good for you, kids, or fido.
Step 7: Common Questions
Can I plate [insert your metal here] with nickel?
It depends. Certain metals play nice together, others do not. The ones that do not are called "dissimilar metals". In the picture, you'll find a table I borrowed from RFI. The table is designed to let you know when a galvanic reaction might occur causing corrosion. For our purposes, it also tells us which metals are compatible and which are not. The lower the magnitude of the number (aka the absolute value), the more compatible (ie similar) the metals will be. If you are trying to plate a metal that is not compatible, you may need to plate with copper or another metal first. You can find my copper plating instructable here: https://www.instructables.com/id/High-Quality-Copper-Plating/
How do I plate non-conductive objects?
First, you need to make them conductive. You can do this with conductive paints, conductive glues, and even metal leaf (think gold leaf) as long as whatever you are coating your surface with is not water soluble. I haven't experimented much with this myself which means you will have to. Send me a message with your results and I'll post them here for others to reference.
How much voltage/current do I need?
As little as possible. The lower the voltage and current, the better results you will get. You need a minimum of 0.5V DC to plate with copper. A C or D cell battery will give you pretty decent results. If you don't have access to lower voltages, you can put the electrolyte into a big container and move your electrodes as far away from another as you can - the increase in distance will also increase the resistance of the circuit and decrease the current.
Can I use other acids other than acetic acid (vinegar)?
Yes.....but be careful... This instructable was written for average Joes and Jolenes, not chemists. Other acids can be significantly dangerous as well as release some very nasty, very toxic chemicals into the air. Unless you are an experience chemist (ie you have an actual degree, not just AP Chem in high school or Chem 111 in college), I would not recommend playing with other chemicals.
Is plating coins illegal?
The first thing I want to point out is that I'm only using coins because they are everywhere and cheap by definition. The copper and nickel content make them ideal for small experiments. This isn't a "how to plate coins" instructable, they are just handy and recognizable. For those of you who took high school chem lab, you probably used quarters, dimes, and pennies for a couple different classroom experiments.
As far as the legality of plating coins, to my understanding, it is legal as long as you 1) Aren't removing metal from the coins with intent to sell that metal, 2) Are not trying to pass them as something they are not (ie a copper plated dime is worth 10 cents, nothing more), and 3) Aren't defacing the coins for malicious intent. As a personal disclaimer, this is MY understanding - take it with a grain of salt. If this is incorrect, I would welcome a friendly email or message from the US Treasury or other qualified persons.
Can I plate Aluminum?
I would avoid it. Aluminum is just one of those metals that don't plate well. If you are looking for a corrosion-resistant finish, you can anodize the aluminum to create a clear oxide layer that is extremely corrosion resistant. If you are looking for a colored finish, you can get dyes that absorb into the oxide layer and stain it whatever color you want (this is actually what Apple and other companies do to make different colored iPods).
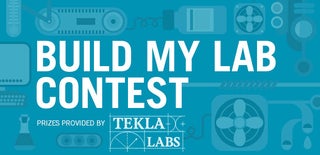
Participated in the
Build My Lab Contest