Introduction: Hollow Wooden Surfboard - My Magic Carpet
Welcome to my first instructable. I've made a few wooden surfboards so thought I would share my favourite. It's 7'6 x 21" x 2"3/4 magic carpet design, a mellow cruiser good for lazy days and lazy waves.
Plans link:
Step 1: Glue the Pattern to the Plywood
So, there are places online where you can buy the plans, or you can design your own. I use a program called AKU. Using this you can create designs pretty quickly. For wooden boards you need to create slices every 150mm that define your ribs. The central spine is the side profile. The outline is your final planshape. Think of it as a fishbone with a spine and ribs that you then build the decks and rails around.
I then use a program called hollow board template maker that generates a PDF of the spine, ribs and outline. Print out at full size and using spray mount stick onto 4mm plywood.
The whole build thread is here: also, with lots of cool surfboard projects
http://www.grainsurf.com/forum/viewtopic.php?f=11&t=5532
Step 2: Cut the Frame
I use a bandsaw to cut out all the frame parts, then dry fit it together. As the design fits onto a 1200x2400mm sheet you can get the frame and the whole bottom deck out of one piece of ply. Sit the frame onto the bottom deck and draw on the rib and spine positions. This is your guide for where a bead of PU glue will go. For this build I used little blocks of balsa wood that keep the frame straight and the ribs 90deg to the spine.
Step 3: Glue the Frame to the Plywood
I made a clamping frame using 3x2 timber, threaded bar and some nuts and penny washers. You'll see how it works but the idea is the board is clamped every 200mm between two strips of ply that can be adjusted to fit the top and bottom rocker of the board using the threaded bar and some nuts.
Bead the PU glue onto the bottom deck, fit the frame and clamp in place.
Time taken so far about three hours - relax till tomorrow while the PU glue cures.
Next add the chine strip - 6x6mm stripwood. This glues into place into notches cut on the rib ends and gives you the outline shape. I'll add the rail strips next, but first some hardware considerations.
Step 4: Fin Box Support
At the tail of the board I add some scrap foam floor insulation blocks. These form support for the finbox and the leash plug when they get holes routered in place and glued in later on. There is also a vent to fit to the frame - for this I use a brass insert pressed into a wooden block then glued to the spine to fit flush with the underside of the deck. As the board is hollow, the air inside can expand and burst the board on a hot day. Using a vent means you can equalise the pressure so the board doesn't suck air in or blow! The vent will be sealed up with a brass bolt and rubber washer.
Step 5: Cut and Glue the Deck
Next I cut the strips for the top deck. These need to be 6mm thick and ideally longer than the board so no scarfing needed. I used some reclaimed western red cedar and pine. The nail stains will look good. The strips can be edge glued using titebond 3 and masking tape. I glue up in twos and threes - no need to do the whole deck in one piece.
Step 6: Rail Strips
Cut some 6x6mm and 6x12mm strips - these get glued to the ends of the ribs to form the rails using any clamping method you can use. Like the drainpipe clamps? Cut an inch off a drainpipe, cut a slot and you have a clamp. I have a box of about 40. You need a lot of clamps for rails. Glue up one strip at a time, using a plane to bevel the strips and taper at the ends. PU glue helps full any gaps you have.
Step 7: Top Deck
Now we add the deck, a strip or two at a time. You need to trim each deck panel to fit against the rails using bandsaw and plane. Glue using PU and don't forget about the vent!
Step 8: Ready for Final Shaping
Once you have it all glued up and cured its ready for shaping. The deck strips take about four or five days to shape and glue. Reckon on an hour or so per panel plus overnight cure time. Now comes a lot of sanding - I use a belt sander and take care to work evenly around the board. Step back and eyeball regularly to keep it symmetrical. Measure, look and measure. This is also the time when you realise the board rattles and you can't find you pencil.
Step 9: Seal the Top
Here's where it gets a little crazy. I seal the top deck using resin research epoxy having masked out the rails. I'm going to do a Mexican blanket resin job on the bottom (crappy ply) and leave the wood exposed on top. This is where the colour of the grain POPs and you see what you have. The positive negative stripes have come out well.
Step 10: Glassing
I have my design worked out and taped to the wall. I add a layer of 4oz fibre glass weave to the bottom and tape in place. The top is masked out. Next I mix up the pigments and resin batches. I'm using polyester resin so add 5ml pigment into 100ml resin and mix well. Do not add catalyst yet! Put gloves, respirator and goggles on, get your squeegee ready and catalyse the first colour. Pour across on bands, then choose the next colour and repeat.
Step 11:
Step 12: Glass the Top
Trim the rail laps with a very sharp blade when the resin loses its tack but is not fully cured. Leave overnight to cure then glass the top. I've added my pinlines (vinyl car stripes from eBay and they are self adhesive) and logo laser printed onto rice paper and laid under the glass. Leave to cure then gloss coat both sides. Polyester resin again but adding wax in styrene so it cures smooth and non tacky. You'll see I already fitted the leash plug and sealed up level with plasticine before glassing - you can open these up afterwards with a Dremel.
Step 13: Pinline and Finbox
Add the pinline before the gloss then router out the finbox slot. The finbox gets glued in with a paste if fibreglass and resin. For the leash plug use a forstner bit and glue in the same way.
Now just the sanded finish to do - wet and dry paper from #400 right up to #1500 and we're done.
Step 14: Done
Step 15: Here's Some Others
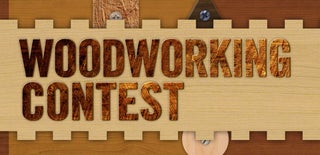
Runner Up in the
Woodworking Contest