Introduction: Home Semiconductor Manufacturing
Hi everyone this is Matt H I am a college student studying Microelectronic Engineering (making computer chips). I wanted to apply what I learned and came up with the idea to make my own cleanroom to test experiments. This instructable covers how to build a cleanroom/cleanbox and preform photolithography, oxide growth, and etching at home. These steps are integral processes to how modern computer chips are made. Due to a limited budget instead of making a whole room into a cleanroom I had the idea of making a glovebox like design with modifications. Also due to limited budget the results are a whole lot larger then modern techniques and I followed a similar approach as did the early pioneers of transistors. This is to be assembled in a spare room or garage where it is dark. Building this should only be attempted if you have knowledge of semiconductor manufacturing and know the proper safety precautions.
Step 1: Building the Cleanroom/cleanbox
Gathering Materials:
The first thing to do is gather the materials for making a miniature cleanroom.
I found a large plastic container from Walmart that already came as waterproof with insulation between the box and the lid.
2. Next I went on ebay and found some HEPA filters which are special filters that filter the air down to particles smaller then 0.3microns. Full scale cleanrooms use large HEPA filters but they are also used in vacuums and air filters. Along with that we need a few small computer fans to blow the air through the filters.
3. Lighting is a very important part of making a cleanroom since photoresist is sensitive to UV light which regular light contains. Yellow light doesn't emit UV so it is used when doing photolithography. Ebay or local hardware stores often sell yellow bug lights that emit only yellow light which is ideal.
4. We also need two chemical gloves which we will be able to use to interact with the materials inside safely.
5. A small plastic lunch box which will be used later for a door.
6. From a local store get some hot glue or silicone to seal the various openings.
---------------------------------------------
Assembly:
1.Once those materials are gathered I suggest following a similar approach as shown in this instructable for how to make the arm openings and a few holes for wires: https://www.instructables.com/id/DIY-Glove-Box/2....
2.Next step is to take the small plastic lunch box container and use a dremel or exactoknife and cut 3 sides of a square into the bottom of the container; this will be used for a small door. Following that cut an opening on the side for a hepa filter and fan, then silicone/hot glue them in. Cut a large enough opening in the side of your large plastic container now where your small plastic lunch box can fit in partially. You want to be able to have it so you can access the flap the you cut from the inside. Next seal up the small box to your large container with hot glue or silicone. What you should end up having then is a flap on the inside of your container where you can open and close it as a door to your cleanroom. Where you can open the lid of the plastic container put an object in, close the lid, and grab it through the flap with your glove inside the box without spoiling the pristine environment.
3. Following that cut an opening either on the top and bottom or either side of your large plastic container for hepa filters and fans. You want the air to flow through the filter, into the container, then back out through another filter. Secure these via hot glue/silicone. There should be a constant small breeze through the container and I recommend leaving the fans on.
4. If you plan on doing photolithography your going to need a heat source around 100C for a soft and hard bake. Best thing I had available for me was a toaster oven. I completely cleaned it out, sealed the door, then cut an opening in the box and used metal tubing to connect it to the large plastic container. Due to the nature of the head I used a heat resistant sealant to seal the openings and made a metal door to the metal tubing so that no heat would flow into the box. I also used a pair or long tweezers to place samples in the toaster oven.
Step 2: Oxide Growth and Diffusion
Supplies:
-Kiln/Furnace must get up to 1000C
Dopant Sourse
Process:
Silicon is a gray color that changes with the amount of oxide grown. Oxide grows on silicon at temps above 1000C and growth can be speed up if steam is supplied. I ran into the problem of particles landing on my samples after extended periods of time. To help prevent that I used some quartz rocks in a stonehendge like fashion with the sample under it to protect it.
Step 3: Photolithography
Supplies:
1. UV light source at least 5mw which can be found on ebay
2. isopropyl alcohol higher concentration if possible
3. UV blocking glasses, found in sears
4. Semiconductor grade photoresist, found on ebay or elsewhere online
5. Paint or Photoshop
Process:
First you need a mask, create a design in photoshop/paint and then from staples have 2 copies made of it. You need it double layered to fully block out the light in certain areas. Note though even with the clear film it does dim down the laser light a bit ~30%.
1. Surface Prep: clean with bottled water and dry.
2. Resist application: Use a PC fan fan or even a blender motor with double sided tape. Stick your sample to it, apply resist and spin for 20-30 seconds. Note that thickness depends on RPM and differs depending on the resist.
3. Softbake: move sample carefully into a heater not over 100C and leave it for around 1 min. This evaporates some of the solvents.
4. Align and expose: To align it I had made a simple stand I would line up the sample and had two rods out of it and would put the mask on top of it using a proximity printing like method. I used a 200mw laser for 0.7s to expose, it all depends on the resist you are using.
5. Development: Developing removes photoresist in the unwanted areas leaving your with your image. To develop the image I used an alkaline developer since I didn't have any TMAH available. This works however it does etch silicon so that has to be kept in mind.
6. Hard Bake: This removes more solvents and light sensitivity which can be useful in etching if small features are required. I had no use for a hard bake since my feature size was so large that it was perfectly fine with a soft bake. If it is needed though that would go for over 100C for several minutes depending on the resist.
7. Inspect: Before you etch a material it is important to check for flaws since if there are flaws you can remove the resist and repeat the process. To inspect I used a small microscope and my own eyes.
8. Etch: Etching removes material where the photoresist has been removed. For etching SiO2 I used a bit of the Whink Rust Stain Remover which contains 2% HF and has an etch rate of ~300A/min. *HF is very dangerous please review the possible hazards before working with it.
9. Resist Removal: To remove the photoresist after it was etched I used isopropyl alcohol.
10. Final Inspection: check to see what your results are.
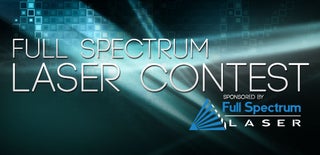
Participated in the
Full Spectrum Laser Contest
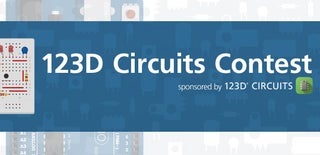
Participated in the
123D Circuits Contest
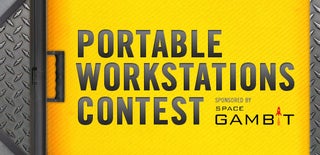
Participated in the
Portable Workstations Contest