Introduction: HomeMade DC Electric Motor and D Cell Battery Holder
My Name is Marcus Knowles and I am a manufacturing teacher at Arts and Technology High School in Marysville, WA. Our class is called Penguin Manufacturing and this is a lesson I teach in our robotics class. Our advanced manufacturing students help make the parts and kits for that class. We are working to create kits to sell and use as a fundraiser for our program. The kits will end up costing about $13 and we may get a Kickstarter campaign going to help with some supplies. I will update the Instructable if that happens.
There are many improvement ideas and we would love to hear your ideas and changes to this plan. Current research and development includes possible injection molded parts and 3 arms on the armature. We have prototypes that have been made on our MakerBot 3D printer, and CNC router but the Kickstarter would help pay for an injection molder or Laser cutter.
The current tools needed to make the parts are:
Table Saw
Chop Saw
Micrometers
Drill Press
Oxy/Fuel Brazing
Engine Lathe (not needed to drill the holes in the dowels, but we have one, so it is easy)
Misc. hand tools
Please check out our program at www.penguinmanufacturing.com
Cheers,
Marcus Knowles
Step 1: The 2 D Cell Battery Holder
The Blueprint Scans have all of the specs so you can make all of the parts yourself.
Again, I am a High School Manufacturing instructor and am working with students to start packaging these as kits for sale at some point
The battery holder is made up of:
3/4 wood,
1/4 plywood,
2 brass brads
rubber bands
16G wire
Step 2: The Motor Housing
Please read the scanned blueprints for specs so you can make the parts.
The trick here is to glue the magnets on correctly. Two of the images and the expanded view blueprint show how the magnets must be aligned. The magnet walls should be able to sandwich when closed together. This also aids in the glueing of the magnets as the clamp force for the glue is the magnets themselves. Let them sit for a few minutes and then glue the housing together. Rubber bands or tape work well enough for clamps.
Parts include:
1/4 plywood
3/4 wood
2- 1/2 x 1/16 rare earth magnets
some two part epoxy
Some rubber bands to clamp
Step 3: The Armature
Ok, so there are a few tricks on this step.
Making the armature is easy when you want 100 of them, but a pain for just one. We use 6" of 1/8 welding rod and braze on 2 small bolts. We made a jig out of fire brick to hold the pieces in place to braze. There are bound to be other ways to do this (glue may work, or JB weld).
Winding the armature has a trick. You have to not change the direction of your wrappings as you cross over the motor shaft. If you over/under, continue on the other side. The way I explain it to the students is to pretend that the center motor shaft isn't even there and continue winding the same way. There is a decent drawing of this in the exploded view blueprint.
I tell the students that the prettier the winds, the more balanced the motor will spin, but there are so many variables in this thing that I have no proof of this. The armature in the picture has only half the required windings, but I got it to spin anyways.
Make sure there are tails on both ends and clean off the tails with sandpaper or a lighter. I prefer the sandpaper as it doesn't heat up the remaining wire.
We bought some 1/2 copper tape from amazon. ours is conductive backed, but it is not required as we attach the tails on top. Then electrical tape them down. We use Kaptan tape for our electrical tape, but regular E tape is fine.
Notice the orientation of the the copper tape to the arms.
Step 4: The DC Motor Assembly
This is the working motor. Now there is a bit of fiddling to do with the wires and how the touch the commutator, but when you get them right, the motor can zing pretty good. A 2 arm armature rarely starts itself, but I will get around to adding a step that will show you a 3 arm setup. I'll include a picture of our prototype.
We have learned to add a paperclip on the armature walls to help hold down the armature. It can get kinda bouncy and hard to spin start.
Step 5: Changes and Alterations
There are a few changes that we are making and problems we still have with the motor.
We have prototyped the CNC carved motor housing and Battery Holder. I believe that is the only way we will make them from here on out. For the CNC we have a 24x24 Multicam Router. We use Vectric Aspire 4.0.
We still have problems with the brushes wires keeping constant contact with the commutator and we are still making the jig to be able to braze the three arm armatures.
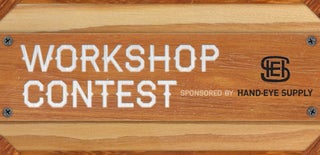
Participated in the
Workshop Contest