Introduction: Hoverboard / Hovercraft
This was a project I did a couple of years ago at school. Who ever said coursework had to be boring!
What you need:
- Plywood board about 1.5 x 0.6 m (thickness can vary upon how much you're willing to spend.)
- Plastic sheeting larger than your board, 1.7 x 0.8 m minimum (heavy duty plastic sheet is best, can find at diy stores and garden centres)
- Leaf blower I found the cheapest place to look was eBay. You don't need anything fancy as long as it works! I picked up a 30cc Flymo for £30.
- Duct tape
- Plastic box lid / Long plastic ruler needed for the centre plate
- 90° pipe (this will vary depending on the style of your leaf-blower)
- Screws
- Staples
Tools:
- Jigsaw
- Staple gun
- Scissors
- Screwdriver
- Drill
- File/Sandpaper
Step 1: The Board
1. Cut your plywood board down to the correct size of about 1.5 x 0.6 m. The wider you make it the more stable it will be.
2. Round the edges of your board. This will stop the corners breaking through the plastic. I had mine at a radius of about 10 cm. This just made it easier to fold the plastic sheeting round.
3. Drill / cut out the hole for the plastic tube. The diameter of this hole will vary depending upon the size of the pipe from your blower. However, it does not matter if you make the hole slightly too large as you can increase the outside diameter of your tube by wrapping duct tap around it.
If you chose to get a thinner wood: This is no problem, but your board will probably need strengthening. The easiest way to do this is get two lengths of thicker wood (e.g. 2 x 4 x 70cm) and screw them on either side of the top face of your board, look at picture 3.
Step 2: Engine and Pipe
You now need to make sure that your pipe fits tightly in the outlet in your leaf blower. If it is too loose then you can use layers of duct tape to build up the outer diameter of the 90° pipe. As mentioned previously, the duct tape can also be used to create a snug fit with the hole in the board.
Next you need to place the leaf-blower on the board with the pipe attached and in the board. Now you can mark where the engine will be. Depending on the type of blower you have will determine how you will need to attach it. For this one I used 90° metal brackets screwed into the side of the leaf-blower base and the board. This is the best time to attach any brackets to the board that will hold the engine on as any drilling / screwing will not damage the plastic. However, do not attach the engine yet! This will make attaching the plastic very difficult if you do.
Once everything has been added to hold the engine on make a check over the bottom of the board to make sure there are not screws protruding or open holes through.
Step 3: The Plastic Sheet
This is the tricky bit! You may need a second pair of hands at this point.
1. Place the plastic sheet on the floor. Then align your board with the centre of the plastic.
2. You need to fold the edges of the plastic over the board. Remember: you don't want the plastic to be tight on the base of the board. It's got to inflate! I gave it about an inch of slack.
3. As you fold the edges over you will need to staple them down (roughly where the tape is in picture 2). It's best to use plenty of staples, about one every 5cm.
4. Finally, using your duct tape, cover over all of the edges of the plastic and the staples. This insures that no air escapes from the top and also neatens everything up!
Step 4: Centre Plate
Now you need to make the centre plate. This is best made out of plastic which is roughly the same thickness as a ruler i.e. 2-3 mm.
If you cut a plate out of a piece of plastic the basic dimensions need to be about 90 x 10 cm. The shape shown below is one possible example. Ensure that the edges are smooth. You can either use a file to smooth them down or put duct tape round the edge (duct tape solves everything!)
Another option would be to use 3 x 30cm rulers. The non-shatter ones are the best as they are slightly more flexible. They would need to be attached in line down the centre of the board.
When attaching the plate make sure that it is screwed down in multiple places to insure it gives an even pressure on the plastic. Also, if any of the screws go through the board make sure you file the ends off. You don't want to get cut when riding your board!!
Step 5: Cutting the Holes
As you can see in the picture the exit holes in the plastic are spaced evenly around the base plate. This ensures that there is an even spread of air exiting the plastic. The holes need to be located near to the centre plate.
The main thing to be careful of is that the total combined area of your exit holes is no smaller than the area of the exit hole in the blower. Otherwise you may find that the holes begin to tear.
Step 6: Time to Fly!!
Finally attach your engine, rev her up and away you go!
Try and keep your weight as central as possible!
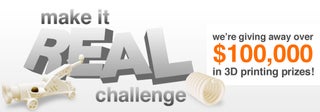
Participated in the
Make It Real Challenge