Introduction: How to Make Foam Armor
Due to a few requests, I have decided to make a fairly detailed tutorial for my foam armor. This is my suit create last year from foam, Its my second suit of armor and I am currently working on my third. For the purpose of ease, I will be showing pictures from both suits to help show how a suit of your own might be made. Here is a list of needed materials for foam armor.
Materials:
-A knife (carpenters or hot knife, or even a scroll-saw)
-Computer with printing capabilities
-Hot glue & Glue gun (I prefer one with low/high temperature setting so that you can quickly join parts and avoid burns)
-Paper, pens, ruler etc.
-Plasti-Dip, and spray paint
-A dremel.....very, very, VERY helpful.
-And of course.....the foam! I typically use EVA foam from three retailers which are all a little different in terms of composition.
Home Depot-> Thinner foam that bends easily, has a diamond pattern on the reverse side.
Lowe's-> Thicker foam that doesn't bend as easily, very durable and has a hatched pattern on the reverse side
Harbor Freight->Thinner foam that bends easily, has a hatched pattern on the reverse side
Now that you have got everything, Lets Begin!
Step 1: File Collection and Printing
All over the internet are 3d models, some in Pepakura form that are craving to be made. If you're not sure what Pepakura is, it is simply a program that takes a 3d model and makes it into a net so that the 2d parts can be printed, and assembled in real life. The viewer program which allows you to also print can be found here: http://www.tamasoft.co.jp/pepakura-en/download/viewer.html The Designer program, which lets you scale the parts to you can be found here: http://www.tamasoft.co.jp/pepakura-en/ If you ever need help printing/scaling/anything with Pepakura, simple search the web (There are tons of tutorials for that) or simply ask me and Id love to help. Once you have the model you want to be foam (Keep in mind that you can find these all over the net by searching say "halo armor Pepakura" If you can't find what you're looking for, it most likely hasn't been made into a 3d model yet.
Ok, once you have the file, open it in the viewer and hit "Print". When all is done, you will have something like a pile of pages filled with polygons. Excellent, these will be your templates to trace on the foam.
Step 2: Template Tracing
Once you have the parts printed on paper, you will need to cut them out with an exacto or scissors. You may cut off the little flaps/tabs as these will not be needed. If you file was not foam-ready, you may need to do some editing to your templates as you go along with this process. It also helps to take pictures of the 3d model from a few angles so that you have a reference as well as the templates. Keep in mind however that cutting out all of the pieces may get confusing, especially if there are many similar ones. I usually cut them out as I need them to stay organized.
After you have the pieces cut out, lay them out on your foam. If you have a symmetrical thing to make, flip the piece over after you trace it so it yields the mirror side. To trace he templates in the neatest and cleanest way, simply use a pen to put a dot on each vertex of the template (where the inner lines meet the edges.) You can then connect them with a ruler for neat, clean, straight lines. For curves you can trace the paper directly, as a that's a little tough to do with a ruler.
In this step, try to keep the parts you trace on the foam close together to save some foam space, you will go through the stuff quickly enough, trust me haha.
Step 3: Part Cutting
With the parts you need traced onto the foam, you are now ready for the cutting step. This step may vary depending on what you are using to cut the foam.
For Hot-knife users: Slowly trace the over the lines you drew on the foam with the knife to cut them out. Remember to go slow but not so slow as to burn the foam.
For a Carpenters Knife: I highly recommend getting one of these. They have snap off blades and cost less than 10 bucks, Probably the most helpful tool exempt the dremel. For this guide the knife over the lines. With this, you can miter your cuts by angling your hand while cutting. This will allow you to make angled connections with foam easier. For curves, do your best. You can always sand them down correctly with the dremel later.
For A scroll saw: This one should be pretty self explanatory. If you have used your scroll-saw before, just trace over the lines you drew on the foam with the blade. Make relief cuts so that you don't get stuck in a maze of lines, otherwise you can always cut your way out.
Now that the parts are cut, dry-fit them together to make sure that there re not overlaps or size differences between pieces that are supposed to connect to each other. Use a knife to trim off the excess and fit the parts nicely.
Step 4: Glueing the Pieces
With all of the parts cut out. You are ready to glue them together. Withe them dry-fitted you should know about where the parts should connect, if not take a look at your 3d model. You also may have noticed that because of the thickness of the foam parts don't exactly fit well. This is because these parts were made to fit together as thick as paper, not foam. You may find that cutting the thickness of the foam off of a connecting edge will help reduce this.
To glue parts, simply put a line of hot glue onto one edge , and place the other on top of it. While the gluing is drying try to make the two faces that are now touching as lined up as possible. This will make the armor look much better in the end. Once the initial glue has dried, flip the two pieces that you were gluing over, and put glue generously on the inside of the joint. This will further hold the parts together. Note: If the glue that you are using is very hot an takes time to dry, make sure to keep holding the pieces together as this step may melt the initial gluing before drying.
Continue gluing parts and strengthening them with glue, Try to keep glue on the inside of joints, and not the outside. You may have to bend the foam pieces to keep the shape of the model, once bent it should stay like that if it is glued to other supporting parts.
Step 5: Final Details
At this point in time, with all of the parts glued together, you should see the 3d model that you saw earlier in Pepakura emerging. If you can find any reference pictures from in-game, in-movie, etc use this for the final details. These will all be done by hand, so I recommend buying some thin craft foam. Use your free-hand skills to cut out pieces that most nearly match you pictures, and glue them onto the foam.
Tips/Tricks:
-If your armor/thing has screws in it, foam has a handy composition that allows you to literally screw them in, They arwe also able to help hold parts together that glue may not hold so well.
-Nylon strapping can be bought for cheap, and can also help hold parts together.
-A Dremel can be used to make fine details in the foam, and sand down edges to miter them.
-Using a hair drying or space heater on the foam heats it up nicely, and makes bending it much easier.
-Remember to use your ingenuity, there is really no correct way to do this! Be original!
-If you see a part of your project that simply can't be made from foam, look around the house! You'd be surprised how easy it is to find the parts you need.
-If you have an airbrush, lightly spraying every foam edge black adds an extremly nice effect to the look of the finished piece.
I will try and keep this section updated as I find new things and as I remember them haha. If you find anything that works good, drop a comment and ill put it in here
Step 6: Painting
Now that you have everything completed, you are ready for the final step; painting. You may have noticed that the foam is not one smooth surface, it is filled with billions of tiny bubbles. If you try to spray paint directly over the bubbles, they will absorb the paint and the finished product will have a dull, grey-(colored) Finnish...bleh! For a smooth glossy surface that wont be eaten by bubbles, buy a can or two of Plasti-Dip spray cans. Its essentially rubber in a can, so it fills the little bubbles mentioned earlier. Two coats over the ENTIRE surface over the foam is plenty.
After the Plasti-Dip Dries, you can now use the spray-paint of your liking. To tape off areas that you don't want painted, use either painters tape or duct tape. Both of these work great.
After this, the choice is yours, you can hand paint things on it, airbrush it, etc. Its yours! Make it yours! :D
Step 7: The Finished Piece
Now that you are done, you can add whatever you want. If you find that you want to add something to it, say you forgot a piece just add it and repaint. Anything extra such as lights, fans, and decals can easily be attached.
Overall:
Remember that there is no correct way to make your armor, especially if it hasn't been made before. takes tips and make up your own, trial and error. For example, i found that you can make the edges of the foam have a "step" if you cut halfway down near an edge from the top, and then meet the cut line from the side. As I said earlier, share your tips! It benefits the entire process.
I sincerely hope that this tutorial helped you. I you have any questions, or if I haven't made a section clear enough, let me know with a comment or PM.
Thanks & Keep building!
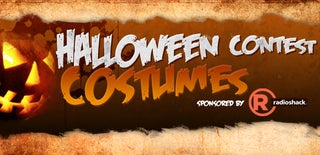
Fourth Prize in the
Halloween Costume Contest
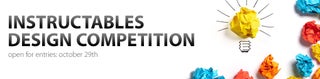
Participated in the
Instructables Design Competition
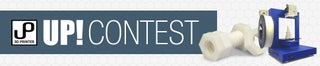
Participated in the
UP! Contest