Introduction: How to Make a Sumo Bot (Science Olympiad 2011 Rules)
This Sumo Bot was the Century High School, from Rochester, Minnesota, Science Olympiad Team's entry into the State Competition on March 5, 2011. Although we didn't do so well (25th out of 32 teams), I still decided to showcase my hard work, and to provide tips for other people.
Here's a brief overview of the competition:
Science Olympiad is a team-based science competition with events ranging from so-called "study events" to "lab events" to the menacing "build events." Sumo Bots is one of these "build events." Sumo Bots consists of two robots specifically designed to push the other robot out of a "Sumo Ring."
I"m entering it into the 13-18 NRW Contest Category.
Step 1: A Not-So-Brief Overview
Now for the extended overview of Science Olympiad, and specifically, the Sumo Bots competition:
Science Olympiad is, as I stated previously, a team-based science competition. Competitions include Invitationals hosted by schools around the state, Regionals, State, and Nationals. According to the Science Olympiad National website, soinc.org , Science Olympiad has been around for 27 years, and "has led a revolution in science education." Teams, for Division C (high school division), are made up of 15 members, who participate in multiple events, usually with different partners for each event. Events range from "lab events", such as Chemistry Lab and Forensics, to "study events", such as Ornithology and Fossils, to "build events", such as Mission Possible and Sumo Bots.
That wasn't too bad, was it?
Now for the exhaustive description of the Sumo Bots event (or rather, the event rules sheets).
The main points of the sheet are the "Construction Overview" and the "Competition" sections. The images highlight the restrictions on the construction and some parts of competition. Essentially, the competition consists of two robots trying to push the other robot out of the ring. Should one robot leave on its own, it will have five seconds to re-enter without forfeiting. Robots cannot deliberately stall for 15 seconds, but it is up to the judges to determine the definition of stalling.
Step 2: Inspiration
Being a sixteen year old junior in high school, I didn't have much experience with RC, so I needed enormous amounts of help. Some of the greatest inspiration for every Science Olympiad event (including Sumo Bots) came from the Science Olympiad Wiki, at scioly.org . The forums linked me to www.geekshavefeelings.com for inspiration. The author of Geeks Have Feelings constructed two previous Sumo Bots, and posted pictures, videos, and general descriptions and tips on the design. His design, Harpy I, was the main source of inspiration here, along with the general robotic and RC guidance of Mr. Bart McCoy and the local hobby store owner.
Step 3: Materials
Our team gave us a budget of $100 for Sumo Bots. Sadly, that budget was not kept, as we spent roughly $200 on the project, but we financed it through "private investment," the parents of the four of us assigned to this project.
Electronic Components:
Qty. Part
1 GWS 4-Channel RC Transmitter/Receiver Combo
2 Tazer 15T Forward/Reverse Electronic Speed Control
2 GWS EPS-350C (RC Airplane power system motors)
2 Spare wire connectors for Airplane Motors (taken from broken airplane batteries)
1 Kyosho Plug #14 Wires
1 Tamiya Plug #14 Wires (set of two)
1 Package of 2 Foam Racing Tires
1 7.2 V NiMH RC Battery
4 AA Batteries
Building Materials:
Pine Wood Scraps
1 Large Zip Tie
Scrap 1/4" Thick Plexiglass
Small Wood Screws
Random Nails (or other form of weight)
Package of 4 Locking Nuts
Tools:
Peak Battery Charger
Soldering Gun
Needlenose Pliers
Philips Screwdriver
Table Saw
Miter Box
Coarse Sandpaper
Electric Drill
Wire Cutter
Wire Stripper
Socket Wrench
Step 4: WARNING!!
The following steps use the GWS airplane motors. However, after taking this robot to State competition (the first time it was unveiled), I lost both of my first two matches for two reasons, both of which come from the motors. In the first round, I lost because the airplane motors had very little torque, especially compared to my opponent. The second problem arose in the second match. I lost the second match because the motors go too fast, even for lock nuts, so the left lock nut came off, forcing the robot to try to drive and win using only the right wheel. Needless to say, this isn't a great tactic, and it failed for me, even though, in my opinion, my robot was "stalling." So be forewarned, do not use airplane motors, unless you are willing to work with the gears themselves, instead of purchasing a pre-made airplane gearbox. According to the forums on scioly.org, a better method would have been salvaging "broken" electric screwdriver motors.
Step 5: Soldering
In order for the ESCs to control the motors, they must be able to connect to each other.
To get the electronics to work together, two "conversion" wires must be made:
Strip the ends of the two "Airplane Wire Connectors" and slide back the plastic covering on the ESCs motor-controlling wires.
Match red-red and black-black.
Crimp the metal covering to hold the wires in place.
Solder the wires together, one "Airplane Wire Connector" to one ESC. (In order to keep separate the wires while working, I used clothespins and wire clips to prop up the wires.)
Slide the plastic covers back over the connection, to protect them.
In order for each ESC to receive power, it must be hooked up to the battery independently. This is achieved by wiring the battery to the ESCs in parallel, so both ESCs receive the full 7.2V. To do this:
Strip the ends of all the replacement/extension #14 wires.
Match all three red wires together and twist the stripped ends together.
Clip the ends and thoroughly solder the wires together, to create a strong connection.
Repeat, using the black wires instead of the red wires.
Step 6: Wheels
Time to attach the wheels:
Remove "propeller caps" from motor axles by pulling straight off.
Remove nuts and washer from motor shaft.
Screw on one lock nut all the way to the end of the thread on the shaft, so that the central plastic piece is towards the motor.
Replace washer against locking nut.
Slide wheel onto shaft so the "hub cap" side is in, towards the motor (opposite of the first pictures).
Attach second lock nut so that the central plastic piece is pointing away from the motor.
Tighten the outside lock nut so the wheel rotates with the axle. To do this, use finger to prevent gear from rotating, and tighten lock nut with the socket wrench.
The pictures are flipped because I took the pictures before taking a test run, during which the nuts came off, so I had to buy lock nuts.
Step 7: Making the Base
Cut one sheet of Plexiglass 6.5" by 6" using a table saw for the base of the robot.
Along each 6.5", cut two 1/2" slots into the Plexiglass using the table saw, 1.5" from one 6" side. These slots allow the gearboxes on the motors to rest better in the Plexiglass.
Cut a 6.5" square rod of pine with the table saw to fit into the gearbox square holes. The rod should be roughly 1 cm by 1 cm wide, but should be a snug fit into the square openings.
Make sure everything fits together cleanly and completely.
Remove protective sticker from Plexiglass.
Drill two holes, one through each gearbox plastic, through the wood, into the Plexiglass (on the first picture where it says "Drill hole here")
Line everything up and secure into place with two screws from the bottom through the Plexiglass first, the through the wood and plastic.
Step 8: Attach Back and Battery Support
Cut a 2.5" by 6.5" strip of Plexiglass to attach as a back with a table saw.
Using the hand held scroll saw, cut a 1" by .5" slot into the strip, 2.75" in from each end of the 6.5" side.
Cut two 2" by 2" Plexiglass squares with a table saw and a miter box.
Cut two 6.5" strips of pine, like the one attaching the motors together, to screw the Plexiglass pieces together with.
Place one strip of pine on the base behind the motors, and drill two holes up through the base Plexiglass and through the new strip of pine.
Remove strip of pine and place on bottom 6.5" edge of the newly cut 2.5" by 6.5" strip of Plexiglass.
Drill two holes through the pine into the Plexiglass.
Secure with two screws through the Plexiglass and the wood.
Place second strip of pine 1" from bottom of Plexiglass strip. (roughly 5/8" gap between the two pine strips)
Drill two holes through the pine into the Plexiglass.
Remove second piece of pine to attach 2" square Plexiglass pieces to.
Place a 2" square piece of Plexiglass on each end of the pine, pointing out the same direction.
The edge of the Plexiglass should line up with the edge of the wood with the holes drilled through it.
Drill two holes through each square Plexiglass into the wood, being careful not to hit the already drilled holes perpendicular to the new holes.
Secure the square pieces of Plexiglass to the pine with four screws total.
Secure pine with square Plexiglass pieces onto the back piece, with the square pieces on top of the pine.
Secure the pine to the back piece with two screws.
Secure the back piece to the base with two screws through the base to the bottom pine strip.
Step 9: Front Ramp Supports
Cut a 3.5" strip of pine using the table saw.
Using the miter box, rotate the blade to a 30 degree angle and cut off a 30 degree triangle that is 2" wide.
Rotate the miter box back to zero degrees, and cut another 30 degree triangle, 2" wide.
Cut a strip of pine that is 6.5" by .5" by 3/8".
Place the strip of pine on the 2" side of the triangle, so that the top of the strip is .5" down from the top of the triangle and the .5" edge and the edge of the triangle are lined up.
Drill a hole through the the strip into the triangle, to put a screw through.
If the screw isn't long enough, "countersink" the hole by drilling a hole wider than the head of the screw part way into the strip, to push the screw in farther.
Repeat on the other end of the strip with the other triangle, so both triangles are facing the same direction, but on opposite ends of the strip of pine.
Place the triangles onto the base, and slide the new strip of pine underneath the two square pieces of Plexiglass.
Drill one hole through each square piece and through the strip of pine.
Secure the strip of pine to the two squares of Plexiglass to the strip of pine with two screws.
Flip the base over and drill two holes through the bottom into each pine triangle, and secure with four screws.
Step 10: Connecting the Electronics
Plug the ESC battery connections to each of the battery extension wires.
Wrap electrical tape around the twisted ends of the extension wires.
Bend the battery splitting wires in half, and secure with a zip tie.
Plug the motor wires into the ESC wire connectors.
Slide the single remaining battery connector out the slot in the back.
Slide the ESCs on-off switches and RC connectors also out the slot in the back.
Bend all the wires still on the base of robot underneath the "battery support" squares.
One the wires are bent under and out the back slot, secure the ESCs to the base with the double-sided foam tape that comes with the ESCs, using only one of the big pieces per ESC. Secure them so the back edge of the ESC is 2.75" from the back.
Step 11: Making the Wedge
Cut a 6 3/8" by 11.5" sheet of Plexiglass with a table saw.
Cut one of the 11.5" edges at a 45 degree angle, to make it easier to sand and get closer to zero clearance.
Cut a 5.25" by 1" strip of Plexiglass, used to contain the nails in the front.
Slide the 5.25" by 1" strip onto the base, butting right up against the front edge of the ESC.
Fill the front of the base, between the edge of the base and the strip of Plexiglass with the extra nails, to weigh down the front of the bot.
Place the 6 3/8" by 11.5" Plexiglass sheet on top of the triangles, and drill four holes through the Plexiglass into the wood triangles, 2 per triangle.
Secure the Plexiglass on with four screws, making sure the nails and small Plexiglass sheet are contained within the robot.
Using sandpaper, sand down the bottom of the Plexiglass ramp, to get closer to zero clearance, but keep making sure the ramp sits flat on the surface.
Step 12: Battery and Top of Ramp
Cut two 1 7/8" by 1 7/8" by 5/8" pine squares.
Cut a Plexiglass strip 1.5" by 11.5".
Slide the two squares onto the Plexiglass squares, all the way to outside edge of each square.
Drill one hole through the back piece of Plexiglass into each square, and secure with a screw.
Place the Plexiglass strip on top of the ramp and against the wood squares.
Drill one hole through the Plexiglass into each block.
Secure with two screws.
Set battery into slot, and wrap a zip tie through the back slot and around the battery, to secure it.
Connect the ESC RC wires to the RC receiver, on channels 2 and 3.
Using one of the remaining large pieces of double-sided foam tape, secure the receiver to the top of the battery.
Using the two small pieces of tape, secure the on-off switches to the back piece of Plexiglass.
Connect the battery wire to the extension wire sticking out the back slot.
Step 13: Controller Fixes
Put the 4AA batteries in the controller, and charge the robot's battery.
The controller's reverser should be set as follows:
1-off (down)
2-off (down)
3-on (up)
4-off (down)
You might have to switch the channels of the ESCs if the controller controls the wrong side.
Since the controller is an airplane one, the left joystick "sticks" or stays in one place, because it's typically a throttle. However, this isn't needed for a Sumo Bot, and actually is hard to use, because the tensions are different. To counteract this, I tied two sets of three rubber bands together and looped each set of three over the joystick.
Step 14: Competition Comments
Although I already mentioned this, but here are some final observations and tips.
1. Airplane motors do not work well in land vehicles, because even lock nuts don't stay on well enough. Also, they provide no torque, which in a competition like this, is a horrible idea.
2. Develop a better means of achieving zero clearance.
3. Do not, under any circumstances take off the plastic around the RC receiver. It is meant to stay on and protect it.
4. Remember to charge the battery fully before competition.
5. Get lots of practice handling the robot.
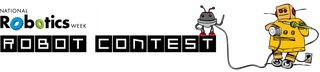
Second Prize in the
National Robotics Week Robot Contest
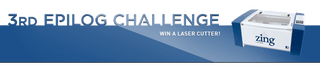
Participated in the
3rd Epilog Challenge