Introduction: Hack a TowerPro Micro Servo to Spin 360 / Continuous Rotation
Hey guys! Since I've got my servos, I've had two that I set aside for hacking. So, coming to my favorite website for help, I was sorely disappointed when I couldn't seem to find any instructables on how to mod a micro servo. After viewing a few, I went to my workbench and got to work. I was very surprised when I opened up my micro servo and found it to be slightly different then the bigger servos. So, I decided I would make a guide on how to hack into your servo! So what are we waiting for? Lets get started.
But then you ask, doesn't this defeat the whole purpose of a servo? Well, no. We just utilize the gearbox, so that we can use this motor as a drive motor for a robot. So now, let's really get started!
Step 1: Ingredients:
Ingredients needed: (no, not food ingredients unfortunately)
- Rotary tool or a utility knife
- Very small screwdriver (phillips)
- Soldering pencil* and solder
- Wire snips
- Needle noes pliers
- 2x 2.2k resistors
- Helping Hands (AKA 3rd hand) BTW check out this awesome instructable on making helping hands. Thanks rstraugh!
&
- 10 minutes
Step 2: Disassembly
First remove any servo arms, legs, and limbs from the servo.
Then, using a very small screwdriver, unscrew the four screws on the bottom of the servo. Be very careful not to lose these.
Watch the video for the disassembly of the gears. The top main gear my be hard in coming off. You can see I had a little trouble getting it off in the video.
Step 3: That 5k Potentiometer
Now we are going to turn our focus on the 5k pot. Here is were it's different from the bigger servos. The shaft of the pot is also the shaft on which the gears sit on. So, we cannot get rid of the potentiometer, but we must keep it.
That being said, we must unsolder the 5k variable potentiometer, and solder on 2 [2.2K] resistors. Unsolder the wires on both ends, off of the PCB and potentiometer. Save these wires for a later project.
Take two 2.2K resistors and and bend the top leads over. Then, using the helping hands secure them like you see in the picture. Now solder these two top ends together. Get them as close to each other as you possible can. There should be two leads in the middle. Since this would make it harder to solder bend this wire up and cut it off. You should now have 3 leads.
Solder this new resistor to the PCB as shown in the last picture. Upon request, I made a horrible video of me soldering these on. It's not the best, but at least it held. For instructions on soldering. . .
Noahw and his amazing instructable https://www.instructables.com/id/How-to-solder/
&
CuriousInventor.com https://www.instructables.com/id/How-to-Solder-Videos%3a-Why-is-soldering-difficult-s/
Now we must remove the collar that stops the potentiometer from spinning 360. Note, you may need to use needle nose pliers to peel off this plastic. In my case, I had already broken the collar when I was trying to get the gears out. See the video, and see what needs to happen. There also might be a metal stop like my other servo had. Your smart, just figure out how to allow the potentiometer to spin freely, but keeping it intact.
Finally, we need to put the potentiometer back into its original place. But first, we need to bend the leads over them selves inward, so that it won't be in our way later on. Bend the leads over, the put back in it's spot. Make sure it's sitting properly on the plastic. See pictures.
Step 4: Chop Time
Step 5: Putting It All Back Together
The first video shows stuffing the board back in, and the second is the gears. In the first I was at an awkward angle becuase of the camera, so I couldn't close the case all the way. You get the Idea.
Step 6: Code
Here is a link to some test code. Just hook up the ground and power of the servo to the Arduino 5v and GND, then hook up the yellow or orange PWM control wire to pin 9 on Arduino. Copy and paste this code into the program, upload, and see if if works!
I hope this helps you guys out with your servos. Check out Make Magazine's page on servos.
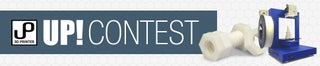
Participated in the
UP! Contest