Introduction: How to Make a Wooden 6" Bench-Vise
I have a great little vise. I use it a ton (pun not intended)! The only problem with it is that it's tiny-- It opens to a little more than 1.5"
I wanted to buy a bigger vise (for my birthday), but the prices are INSANE!
As a "maker", I don't think it makes sense to pay $100 to $500+ on a vise, when it's basically a big chunk of metal and a bolt. I know that I'm not the only one that thinks that.
I decided to build my own 6" (~16cm), with free reclaimed wood, and less than $5 worth of hardware.
Did you know that if this Instructable gets 150,000 views, and 5% of the people that would see it would build the vise, it would mean that this Instructable saved ~MILLION DOLLARS!!! Share, Share, Share!
*Pssst! Make sure to check out my top comment (in the comment's section) for a chance of winning several free PRO memberships to Instructables!
Step 1: The Plan
Back in April, I tried to build a vise, but it didn't really work out like what I wanted. You can see that vise here.
This vise is bigger, stronger, can fit in a small Drill-Press, is easier and faster to use, and many more.
While I don't have Sketchup Plans (I still haven't learned how to use it) for this vise, you can see the pictures above for the plans, along with fully detailed instructions in the next steps. If you need any more help, feel free to contact me in the comment section below.
Also, if you want to build your own vise, but am not really fond of my design, I recommend seeing this collection of homemade vises, which many different DIY designs.
Let's get started!
Step 2: What You'll Need:
Hardware & Materials:
- European Beech Wood (The dimensions are written later in the Instructable)
- 3/8"X29cm Threaded Rod (I bought it at a hardware store for less than $5)
- 2 Pieces of 290X8mm Metal Rod
- 2 Washers
- 16mm Hardwood Dowel
- 2mm Metal Rod
- Plywood
- 2 Screws
- Paper Towels
Chemicals & Adhesives:
Tools (+Attachments):
- Abrasive Dremel Cutting Bit
- Homemade Hot-Glue Mallet
- Vise (the small one)
- Drill-Bits: 1, 2, 8, 9, 10 , 19mm Spade Bit , 27mm Holesaw
- Hammer
- Clamps
- Sandpaper: 200 Grit
- Steel Wool
- Paintbrush
- 7mm Chisel
- Caliper
- Tape Measurer
- Speed Square
- Screwdriver
Electric/Power Tools:
- Drill
- Drill-Press
- 6-in-1 Woodworking Machine (It contains the Mini Bench-Grinder)
- Dremel
- Circular-Saw
------------------------------------------------------------------------------------------
Recommended Safety Equipment: Earmuffs, Respirator, Safety Goggles
Cost (for me): <$5
Difficulty: Fairly Hard
Approximate Time: 5 Hours (It took me more10 because I didn't have written Instructions...)
Step 3: Cut Wood to Size (& Glue for Making the Final Size)
Since this is made from reclaimed wood, I thought there would be no point in making two different steps, for cutting, and then gluing, to the final size. For example, if this was made from a 2X4, the base wouldn't have been made from two different parts. Makes sense? :)
I started by measuring and marking cutting all of the European Beech Wood parts with my Drill-Powered Circular Saw.
After that, I glued them together with wood glue, and clamped them together while they dried. For the actual build, I had to split this steps into several parts, because I didn't have enough clamps.
Here are the dimensions in centimeters:
3.5 X 4.5 X 7cm of European Beech Wood
2 Pieces of 5 X 9 X 7cm of European Beech Wood
32.5 X 9 X 2.5 of European Beech Wood
Step 4: Drill Holes for the Front & Back Jaws
I aligned and clamped both of the 5 X 9 X 7cm pieces one on top of another. Make sure they are totally aligned before you drill, this is REALLY important!
I drilled a 10mm hole in over the middle part of the first block, and then drilled two 8mm holes for the metal rods.
After I drilled them, I used my Drill-Press, again, to slightly widen the holes so the rods could slide better.
Step 5: Chisel Holes for the Hex-nut
The nut is going to fit inside the back jaw, like my first homemade vise, I decided to chisel out the holes. This works really well!
I first traced the outline of the nut over the hole, after that, I used a sharp chisel to chisel out the hole, and then hammered it in.
Unlike my first vise, I used one hex-nut, and made it a tighter fit, instead of using Epoxy.
Step 6: Glue the Rods
I mixed up some 2 part Epoxy, and glue the rods inside of the holes that were previously drilled in the first jaw.
Since this a tight fit, make sure that you apply a lot of Epoxy.
Step 7: Glue the Front Jaw
Glue the front jaw to the base with some wood glue. If you want to turn this into a Bar-Clamp, you won't need to do this ;)
I clamped the joint until the glue dried.
Step 8: Make the Handle
I started by drilling a 9mm hole in the tip of the 3.5 X 4.5 X 7cm piece, and when I made sure that the rod fit snuggly inside, I drilled a 2mm hole through the wood and the rod. This will help strengthen the bond.
After that, I quickly mixed up some new Epoxy (stronger), and pushed the rod inside. Don't forget to add the 2mm strengthening rod!
After after about an hour, I came back, and drilled a 19mm hole through the piece of wood for the handle.
To finish it off, I drilled a 27mm hole in some hard plywood, drilled two small holes in each end of the handle, and screwed them in.
I let everything cure for a few hours inside the holes of my second Homemade wooden vise ;)
Step 9: Sand Everything
Since this is reclaimed wood, a small part was actually sanded and finished, the most, however, was not.
I started by sanding the wood with steel wool, and then finished it with 200 grit sandpaper.
Step 10: Cut & Grind Off the Rods
The rods were a bit longer than I wanted, so I cut part of them off. I'll use the leftover piece for a future vise.
I also used my mini Bench Grinder to remove some of the sharp edges. Handheld this time!
Step 11: Varnish
I applied a coat of varnish.
2 Hours later, I came back. I sanded the whole vise again, and applied another coat of varnish.
I hope this will make it waterproof.
Step 12: Grease the Rods
Greasing the rods- I've said it a lot, and I'll say it again.
This lowered the amount of friction probably to a fifth. I suppose I'll have to do this again every once in awhile...
Step 13: Use It!
Congrats! You've built your own Wooden Bench-Vise!
I don't need to explain how useful this will be. You'll see this in MANY more of my upcoming Instructables!
-----------------------------------------------------------------------------------
Don't forget to Follow me on Instructables, I have over 80 Instructables that I'm sure you'd like!
DON'T BE SHY! Liked it? Let me know! Didn't like it? Let me know why!
If you liked the Instructable, please consider clicking the orange vote button (in the top right corner), and sharing it on social media. At no cost for you, this supports my projects, Instructables, and me, since DIY isn't always cheap :)
I read and answer ALL comments, so make sure to leave your suggestions, upgrades and improvements in the comments below!
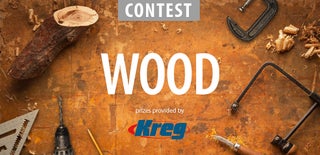
Participated in the
Wood Contest 2016
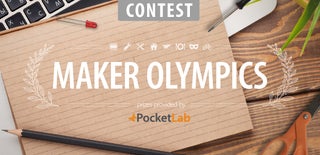
Participated in the
Maker Olympics Contest 2016
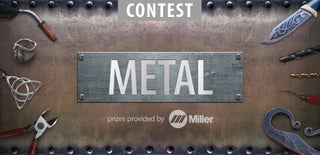
Participated in the
Metal Contest 2016