Introduction: How to Properly Mix and Pour Concrete
This instructable is a lesson in my free Concrete Class. To enroll, click here.
Making anything out of concrete requires you to mix the dry concrete with water in order to start the chemical reaction that allows the concrete to cure. In this lesson, you'll learn how to properly mix and pour concrete.
Though mixing concrete might seem straightforward it's actually the easiest part to get wrong. In this short lesson we'll cover best practices for mixing and pouring concrete to achieve the best results, along with additives that can change the properties of your concrete mix.
Step 1: What's Happening
As described in the Intro Lesson of the Concrete Class, when water is mixed with Portland cement to form a paste a chemical reaction starts called hydration, this will harden the slurry into a solid over a few hours.
The hydration reaction transforms the Portland cement into crystals that weave into adjacent crystals and form a dense interlocking lattice. With the right amount of water this reaction makes very strong concrete - too much or too little water will weaken concrete.
Hydration process is slow, taking concrete a full 28 days to reach it's full strength potential. Luckily, concrete is hard after about a day and can be safely handled without damaging the surface after 48 hours.
Step 2: Setup
Before mixing any concrete make sure you're all set up to pour immediately after mixing. This might seem obvious, and even though concrete takes a while to set up you don't want to be fumbling around when working with either wet or dry concrete.
Designate your work area and make sure you have enough room to mix and pour. Also get your water beforehand, I like to reuse the large plastic soda bottles as they have screw cap that can seal the water in case I knock the bottle over.
Make sure you have your dust mask, eye protection, and gloves on before starting any mixing.
Step 3: Mixing in Water
The amount of water added to concrete is called the water/cement ratio. Though adding more water to the concrete will make it easier to mix, pour, and work with, it actually lowers the concrete strength of the concrete when cured. This is because the hydration creates interlocking crystals and the more water in the mix the further apart the crystals are. Inversely, the lower the water/cement ratio the stronger the concrete as the hydration crystals are close together and can fully knit together, creating very dense and strong concrete.
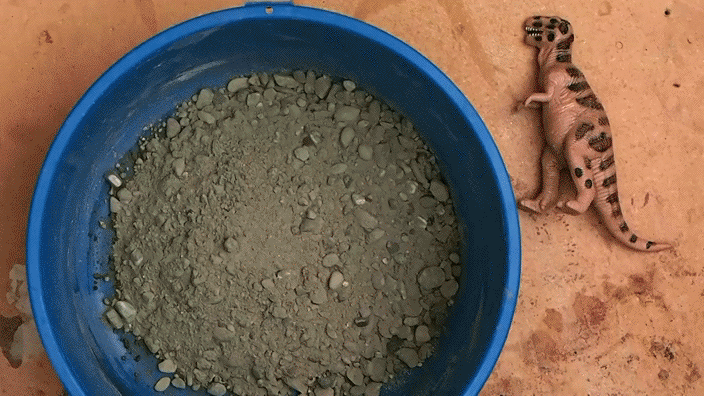
Start by adding dry concrete mix into a sturdy plastic bucket and make a small well in the middle. Add enough water to make the mix wet enough to ensure good hydration, but not so wet that the concrete mix becomes soupy. If you've over-poured water just add more dry mix and incorporate it until you achieve a good mix.
After getting the right water to cement ratio you can start incorporating color and other additives to change how the concrete looks and behaves.
Step 4: Color + Additives
If concrete wasn't amazing enough already, there's loads of things you can add to the mix to achieve different properties.
COLOR APPLICATION
Adding color to your concrete can be a great way to accent your piece and really make it stand out, or have it blend in with the surroundings. Concrete dye is usually found in powder form and added to the concrete mix while it's being prepared, whereas stains are usually liquid and are brushed on to the concrete after it's poured and cured.
DYE
Dye usually comes in a powder and is available in almost every color imaginable, colors and concentrations can be experimented with to get some really interesting results. Care needs to be taken when adding dye to concrete to ensure consistency in the coloring, especially when making multiple batches. Weighing powders is probably the easiest way to ensure a uniform color throughout your concrete.
From left to right: natural concrete color, black dye, brown dye, white dye.
You can mix dyes to create new colors, or choose a lighter concrete bagged mix to create a cleaner base for the dye to show through. In the above example dyes were added to standard countertop concrete mix to achieve the colors.
Remember that dye is a pigment and will stain anything it comes into contact with. Always wear gloves when handling, and make sure not to get any in your eyes or breathe it in.
STAIN
Where dyes are added to the concrete as it's being mixed, stains are applied after the concrete has cured. The advantage of this is that stains can be brushed on, or applied with an artistic touch to only apply color to specific areas. There are just as many stain colors are there are dyes, but the look is slightly different. Dyes penetrate all the way through the concrete as it's being mixed in, stains can have a translucent effect and a softer appearance in color.
Before committing to either dye or stain, it's wise to preform some tests to ensure the color you are looking for.
ADDITIVES
Introducing additives to the concrete mix can affect the performance and set times for concrete, but really should only be used if the circumstances require it (no need to mess with ordinary concrete, it's already pretty great stuff!).
We won't be using any additives in this class, but it's good to know they exist and under what circumstances they should be used.
ACCELERATORS / RETARDERS
Accelerators reduce the set time and allow early strength for concrete. This is great for applications where you need to concrete to set up quick, like in colder weather where you don't want to wait around and heat an area just to set your concrete pour.
Retarding agents slow down the curing process, and are often used in hot temperatures to delay the set time. Retarders can also be used if your job is complicated and you want additional work time for the concrete.
OTHER CONCRETE ADDITIVES
There are a few more concrete additives, but they are typically for specialized applications and aren't really used outside of the construction world. However, just so you know:
AIR ENTRAINING
Air Entraining additives trap tiny air bubbles inside the concrete. This is useful for concrete that will be exposed to freezing, as any water in the concrete will expand into the small air bubbles instead of cracking the concrete.
WATER REDUCING
Like the name suggests, this additive will reduce the amount of water needed in the concrete mix. As we'll learn in the next lesson, less water in the concrete yields a stronger cured product, and too much water can make the concrete weak. (more on the water/cement ratio in the next lesson)
Water reducing additives typically allow 5%-10% less water to be used in the mix, which results in an even stronger concrete.
SUPERPLASTICIZERS
This additive allows the concrete to flow very easily for a short period of time, with little to no vibration and compaction needed. Depending on your application you may not want a fluid mix.
Of course all these additives cost money and are mostly used in construction applications. However, after this class maybe you can see some advantages of using additives and may want to try them out. Share your results with additives with the rest of the class!
Step 5: Reinforcement
You might be wondering why you would ever use reinforcement since concrete is already so strong. While concrete is strong it's really only strong in compression, when force is being applied in a crushing motion, like when you're standing on a sidewalk. But concrete is weak in tensions, when a stretching force is applied, like across long spans like bridges where a load in the top of an unsupported section can cause tension on the underside.
Compression and tension forces on a beam. Image modified and used under CC BY-SA 3.0
To make concrete able to withstand the tensile force another component is added to the concrete when it's wet to take the stretching force. For almost all larger applications this material is steel, which has a very high tensile strength. Steel is a great choice for concrete reinforcement as it can be easily shaped, is widely available, and has very high tensile strength.
Once encased in concrete the steel is sealed from air and water, meaning it won't rust and degrade. However, if the concrete cracks or if the reinforcement is placed too close to the surface of the concrete there's a chance water can enter and corrode the steel. When working in concert, steel and concrete are a very robust building material that can withstand a lot of dynamic loads, you can see this on any large construction site where the building and floor slabs are all poured concrete.
Through steel is a great pair for concrete reinforcement it's not the only one. An alternative are short fiberglass fibers. The advantage to fiberglass over steel is that while steel needs to be laid out in a grid-like pattern in the concrete the fiberglass has the advantage of having small rods facing in every direction and fully mixed into the concrete, allowing tensile strength in any direction without having to make a steel skeleton first.
Another great advantage of fiberglass is that if the concrete ever cracked and there was water ingress the fiberglass can't rust and compromise the concrete like steel could. The idea of these fibers is that they provide tensile strength in all directions, so any cracking that could occur as the concrete shrinks while it's curing are halted by the fiberglass.
These fiberglass fibers can be added straight to the concrete mix. The fibers may be slightly visible when the concrete is cured, so bear that in mind.
Do I Always Use Reinforcement?
It should be stated that you don't have to use reinforcement for your projects. In fact, for smaller craft projects it doesn't make sense at all. However, knowing what reinforcement is and how to include it will be crucial to the capstone project, and of course your next larger concrete venture!
Step 6: Pouring
Pouring concrete is just as important as getting the mix right. The toughest part about pouring concrete is making sure that concrete makes it into all areas of your mold or form.
For small molds you'll need to scoop your concrete mix into the mold and push the concrete into all corners and voids. I've found it helpful to use a thin stick to push the concrete around to ensure coverage in tight spaces.
Though making sure concrete is into all areas of a form, the real magic of making a great concrete casting is vibrating.
Step 7: Vibration
To remove bubbles and to help settle the concrete into the mold or form vibration is used. On construction sites where large concrete slabs are poured they use a powerful corded immersion vibrator, but for our applications anything that agitates the wet concrete will work. This means we can shake and tap our mold, or improvise and use the vibration from power tools to create the agitation we need.
When vibrating your mold you'll start to see the surface become smooth and small bubbles rise. Tapping, or slapping the mold will help with this process, or you can be a little more inventive; I've used a random orbital sander pushed directly on the work surface next to my filled concrete mold to create vibrations, settling the concrete and bringing the bubbles to the surface.
Below is an example of air bubbles caught inside the mold as it was curing, a result of not vibrating after pouring.
Always vibrate your concrete after pouring, ensuring all voids have been filled and as many bubbles have surfaced as possible. If your final mold has bubbles after curing you can sometimes repair the work with some concrete finishing, but that will depend on what your mold is of.
Step 8: Covering Your Work
After pouring you should cover your work as much as feasible to retain moisture as it cures. This is because if water is allowed to evaporate too quickly from the concrete the hydration process will not have enough time to react with the water that was mixed in, leaving your concrete without the proper moisture it needs to successfully complete the hydration process.
Uncovered concrete will still harden, and will likely be fine for most smaller applications, but you may notice that some corners and edges are more brittle. This is especially true in hot or very dry places with low humidity.
During the curing process, when your mold is covered, you can see condensation forming. Without covering, this moisture would have escaped and not been included in the hydration process weakening the concrete.
If you want really strong results you can mist the surface of your concrete every day during the curing process. Since the concrete will be mostly set by that point adding more moisture won't dilute the concrete and can help aid hydration in any parts that didn't receive enough water earlier.
Step 9: Curing
Concrete doesn't dry, it cures. During the curing process concrete begins forming interlocking crystals which create the super strong solid we all know. It takes concrete about an hour to start becoming solid, and will continue to gain strength over the next 24 hours. Even though concrete may be hard to the touch after a day, it doesn't completely reach full strength until 28 days after pouring. The initial hydration reaction is fast, but the complete reaction take days to finish.
The length of curing time can vary widely depending upon the structure or item made out of the concrete, the mix design, the concrete’s temperature and the desired strength at a certain time, to name just a few factors.
So, how will you know when your concrete is ready? A fun trick to see how far along your concrete is in the hydration process is by using a rubber square, you can usually find these in the plumbing section of your local hardware store as they are used as gaskets. Place the rubber square on your concrete and let sit for about 2 hours.
Peel up the rubber gasket and look at the concrete, if there's a dark patch that means there is still moisture in the concrete and the hydration process has not yet finished.
Step 10:
Now that we're familiar with what concrete is and how it works, let's get messy and start making. If you enroll in the class, in the next lesson, we'll apply the theory and make our first concrete project using a simple mold.