Introduction: How to Make a Bookshelf Mountain!
My girlfriend has a lot of books. A lot of hardback books. A mountain of books. Our apartment has exactly zero shelves. But there is sixteen feet of clear wall space that a bookcase can go up against and none of the shop bought laminate versions appealed. So these are my plans to make an appropriate bookshelf. The entire project cost $220 for all the materials.
Step 1: Tools and Materials
Tools:
Safety glasses
Circular saw / table saw / jigsaw / cross-cut hand saw
Power drill
Hand sander
Work bench
Wood drill bit
Angle drill guide
3/8” dowel centres
Clamps
Measuring square
Measuring tape
Materials:
5x - 8’ lengths of 1 x 10 softwood
14x - 6’ lengths of 1 x 10 softwood
132x - 3/8” x 2” hardwood dowels
24x - 2½” x ½” corner braces
4x - 2” corner brackets
4x - 4” straight braces
Wood stain and protection of choice
Wood glue
Wood screws
Another option instead of solid Spruce/Pine/Fir is to use a good quality ¾” thick plywood. An 4’x8’ board ripped into 1’x8’ boards by the store could be slightly cheaper in price if you don’t mind seeing the plywood edge.
Step 2: The Design
I opted for a slightly unusual design in a mountain-like shape. The left side is a set of straight bookshelves in decreasing lengths with one of the shelves shorter in height to receive DVDs. The right side is a set of various sized compartments for books, tall things or other such knick-knacks. Each shelf is 12” tall except the bottom level which is 18” tall. The T-section sticks out 4’ from the shelf and 2½’ high and helps divide the room into sitting room and a study area. The SketchUp design shows how the boards sit and are arranged.
Step 3: Get Cutting
Remember the words of the guru Norm Abram:
“Before we use any power tools, let’s talk about shop safety. Remember to read, understand and follow all the safety rules that come with your power tools. Knowing how to use your tools properly will greatly reduce the risk of injury. And remember that there’s no greater safety rule than to wear these *points to face* safety glasses.”
I didn’t have a table saw or a router for this project, so there are no dados or mortise & tenon joints. The boards are connected with dowels set into the ends and some corner braces on the back side to support the external corners and prevent the entire construction from racking.
I planned out the cuts by hand as I couldn’t find a good board calculator. Having the 3D model is useful for pulling dimensions for the cutting which already take board thicknesses into account. I used a circular saw to do all the cross-cuts to cut the boards to length. 49 cuts in total. To help speed things up, I made a sled that my saw rides in to make perpendicular cuts with my mark out line.
The boards were the cheapest you can find from a big box store so careful selection of the straightest and least cupped boards were pulled from the piles. Arrange the boards so that the best side is visible. And take care to label the boards with their length after cutting. The cutting list should give you all the pieces for the plan.
Step 4: Get Drilling
I bought a discounted drilling guide for $11 to help me drill the holes for the dowels as close to 90° in the ends of the boards. It also provided me with stops for drilling depth. Majority of the holes are 1” in from the edge of the board. Vertical pieces have the hole in the end grain 1 3/8” deep, horizontal pieces are 5/8” deep. Clamp the board down and secure two scrap pieces on either side to provide more surface for the drill guide to rest upon. If you have proper dowel centres, drill the 3/8” hole in the end grain of the vertical pieces first and offer them up to the horizontal pieces with the drill centres in place to mark where the corresponding holes will be.
I didn’t have drill centres so cut the heads off of two screws to leave the thread and point, covered the thread with masking tape to fit my 5mm pilot hole. The pilot hole is drilled so that only the tip of the screw protrudes and when lined up with the mating plank, will put two marks that I can centre my holes with. This ensures that my dowels will always fit together and line up. If you can measure and drill perfectly accurately, then this is not required, but it is rarely perfect so this provides a best case scenario.
Whereas the outer vertical boards have dowels and braces to connect them, the internal vertical pieces between the shelves on the left side have no dowels or fixings at all. These pieces simply float like book ends between the shelves and can be placed and shifted according to the shelf’s needs. The weight of books will keep the boards in place and I recommend not having a span of shelf longer than 3 feet, lest a particularly heavy encyclopaedia snap the shelf in half.
With the holes drilled, drop the dowels with a bit of wood glue into the end grain holes (i.e. the dowels are in line with the boards). This facilitates the bookcase to deconstruct into flat, easily transportable pieces.
Step 5: Assemble!
With the pieces cut, drilled and dowels inserted, do a dry fit of all the pieces to ensure it fits together in the right order. With the dry fit complete, take time to label the back side of the boards to aid in assembly later. I labelled the boards “V” for vertical and “H” for horizontal and then numbered from the floor up and left to right. This gives each piece a unique designation. At the intersection of each piece, write the piece it connects to on the ends to give a specific position and order. Place corner braces on the external corners (i.e. the outer most intersections around the perimeter) on the back side to prevent racking.
Step 6: Disassemble!
After you’re done admiring your shelves, you could stop there and be satisfied. However, the soft wood is unprotected and will dent and mark and take on water without some sort of protection. I opted for a dark stain and polyurethane finish to add some depth and substance to the relatively thin shelves. Take the shelves apart and place them back side down onto some scrap wood cleats to raise it off the floor and allow better access.
Step 7: Stain Away
I detailed my staining method in another Instructable (Introduction to wood staining) with more detailed instructions. I used Minwax Bombay Mahogany Stain & Poly in one applied with a folded piece of t-shirt cotton with the grain. The first coat is dry overnight and then sanded back with 80 grit paper and an electric sander to remove the stain from the high levels of the grain and make it pop. I then applied another coat of Bombay Mahogany mixed with Minwax Ebony stain in a 5 parts Mahogany to 1 part Ebony to darken the stain. This is applied to the boards to give more depth to the colour and give the wood a more aged appearance.
As a note, the Bombay Mahogany was not the expected colour on application and required the Ebony stain mixed in to get the desired colour. They call this the finishing stage, but it easily took the same amount of time as the woodworking, if not more.
Step 8: All in the Details
With the stain dry, I chamfered all the edges of the boards with a plane and utility knife to leave approximately a 3/16” (2mm) chamfer. Where there were intersections, I left the edge square so the pieces joined together flush and continued the chamfer on the other side. This left a nice lighter coloured line around all the pieces which helped give more depth than just one shade of colour.
Step 9:
Join all the pieces back together in the order you’ve hopefully marked. The T-section that sticks out is also joined by dowels at the intersection but also has flat connecting plates screwed on the underside to keep them joined. There is also a corner bracket on the outermost vertical panel to keep it aligned with the other pieces.
Step 10: Security
As the entire unit is over 16’ long and 6.5’ high, it needs to be anchored to the wall to prevent falling over and trapping any small plants or children. Use the 3 remaining corner brackets screwed to the underside of a shelf and then to a wall stud.
Wall studs are commonly found on one side of a power outlet. Knock on each side to hear a solid noise instead of a hollow noise. The edge of the 2x4 stud will be to the outlet. Measure 16” from this point to find the next stud, and 16” again to find the next. You can drill a small hole in the wall and ½” in should be the wood of the stud. Secure the bracket with at least a 2” screw. In some older buildings, the studs may be 24” apart if you can’t find it.
Step 11: Actually Finished!
With the shelving secure, you can admire your alternative shelving solution and put all your books and pieces on display. Behold your mountain of books! I was a little concerned about weight distribution with the offset shelves, but it is all holding up very well with the immense mass of books.
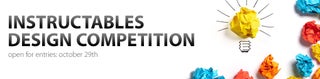
Participated in the
Instructables Design Competition