Introduction: How to Make a Liner Lock Folding Knife
I've posted an instructable about making a fixed blade knife. It'll be useful to read that first, because in this instructable, I will not go over those steps again, but merely focus upon the nuances involved with creating a folding knife. A link can be found here: https://www.instructables.com/id/Knife-Making/
This instructable is intended to be able to be read by those who are not familiar with knives, but I may use some unfamiliar terms by accident. If I do, please ask.
Disclaimer: I'm not responsible for any injuries(likely) or deaths(unlikely) that may occur as a result of your attempt to follow this instructable, nor am I responsible for what you do with the information you have obtained from this instructable, nor what you do with the knife you have made. Follow your local laws at all times!
Unfortunately, I get caught up with the work sometimes, and forget to take pictures. Thus, I will be using several different models to demonstrate the steps. All the parts are the same, and the instructions to build them are the same, but just be prepared for a sudden change in the knives shown.
This project is somewhat difficult, and requires familiarity with basic tools, as well as quite a bit of time. However, the price is decently cheap, and not counting the tools, only costs me around $25 per knife.
I'm going to try to get this instructable out first, since I can't find another instructable of this type, and then fill in with extra pictures. Any questions are welcome!
Step 1: What Is a Liner Lock?
Feel free to skip this step if you know what a liner lock knife is. This step is just to familiarize those who do not know, and also give an overview of what we will be making.
The liner lock was invented by Michael Walker, who altered the electrician's knife to create this folding knife, with a ball bearing as its detent. The lock, when made correctly, is very strong, and also allows for wear.
The main parts of the lock are the stop pin, pivot, and the liner lock itself. When closed, a detent built into the lock holds the blade closed. A liner lock works because a spring in the side of the handle (usually titanium) is in the path of the blade and keeps the blade open until the spring is pushed over to the side. If one is right handed, when the knife is cutting edge up, the liner lock would be built into the left side, and will spring towards the right. Pictures will do the rest of this talking.
Terms to know:
Lock- what keeps the blade open (in this case, the titanium spring)
Stop Pin- What keeps the blade from traveling too far when opened and closed.
Pivot- What attaches the blade to the handle, and what allows the blade pivots on.
Backspacer- A chunk of material located near the end of the handle (opposite the blade). This is just a pillar of support the same width as the blade and the washers.
Scales- The handle materials. G10 is a really good material to start with- it's strong and easy to machine, although a mask must be worn to protect against the glass fiber it will release. Micarta is a less hazardous material.
Pins- What holds the knife together. In the picture below, these are the two silver ones located near the blade, and the two brass ones towards the end.
Step 2: Designing
A liner lock knife is easy to design. A good liner lock knife though, is harder. Also, I find that I never follow my designs exactly, but a good design is essential to make sure the parts come together. I suggest using inkscape for the drawings, although if your hands are good, drawing works as well. One advantage to inkscape is that when you rotate, you can set the pivot point to the actual pivot on the knife, thus allowing you to have some sort of a virtual model of your knife, and watch it swing open and closed.
Blade design depends on your uses and the knife. If you are just starting, I would try a small simple knife. The smaller size would take less time since there is less steel to grind, and the first knife would probably not be perfect. For me, my first knife had a lock that traveled too far over, or had little room for wear, as well as a broken detent (the ball broke). For my second knife, the lock up was perfect, but the detent was too weak. My 3rd and 4th folders, that I am currently making, have perfect detents and have just been sent off to be heat treated. Point is, making knives takes patience and time. I find it a very nice hobby with the reward of a new knife, custom made to suit my hand, that will fulfill my exact purpose, and costs less than $30 for something the market would charge a lot more for.
The bare needs for design: The blade, handle, pivot, stop pin (or something that holds the blade open and closed), lock, detent ball and detent hole in the blade.
Also, when the blade is being closed, you want to make sure it will cover the detent ball the entire time. That way, there will only be one initial resistance when closing the blade due to the detent. Afterwards, the detent can ride on the blade the entire time. Otherwise, when closing, there will be a series of bumps as the detent is pushed out by the blade, then comes back in, and is pushed out again.
Either way though, once you're done with your design, a prototype cut out of cardboard and a thumbtack is suggested.
I added some ideas below for examples.
Step 3: What You Need
Tools:
-Drill+Drill guide/Drill Press
-Good Drill Bits (I used 1/8" and #53)
-Ball Peen Hammer
-Files (Round and flat)
-Hacksaw (With metal cutting blades. I use Lansky)
-Expo Marker
-Sharpie
Materials:
-Blade Steel (1084 can be heat treated with a fire. I have moved on to D2 and 154CM, and am using Texas Knifemakers to heat treat) (I used a thickness of 1/8")
-Titanium (Around 0.060" Thick, for the liner lock)
-Handles (G10/Micarta suggested)
-Stainless Pins(round rods of metal) (For a stop pin/pivot. Or one can use pre-manufactured pivots and stop pins) (I used 1/8")
-Backspacer Material (thickness must equal your blade's thickness+washers
-Detent Ball (I use 1/16" diameter)
-2 Phosphor Bronze washers (Your choice of thickness, I use 1/32" I believe.)
All of the materials can be purchased from USAknifemakers.com. Other sites include Texasknife.com, knifekits.com, alphaknifesupply.com and more.
Step 4: Cut It Out!
Print the design onto pieces of paper, super glue the paper to your metal and titanium, and then cut out the design. I use a hacksaw with lansky blades. Just somehow, get the design cut out. Nothing too dainty here. Make sure to leave extra space around your lock and stop pin areas on the blade. So wherever the blade touches the handle (the two stop pin contacts- opened and closed, and the lock), leave a bit of extra space- say 1 or 2 mm.
Use a file to finish the blade. At this point, your blade of the knife, the cutting edge, needs to be finished perfectly. The parts of the knife that won't show when the blade is opened can be left somewhat finished. Remember, it is important to leave space around the stop pin contact points and the lock area!
Also, cut out the handle slabs at this point. Make them roughly accurate. The most important part is to have the two holes.
Step 5: Drill the Pivot and Stop Pin Holes
Drilling needs to be precise. I use this drill guide thing, but a drill press would be much better. If you are going to try to do it with just a drill, try to keep it as close to perpendicular as possible, and when you're drilling holes where the same pin would pass through, use the holes as a guide for the next hole to be drilled, that way all your holes can be at the same angle. It won't work well for the pivot, although it can be done. Start with a center punch, and drill through the knife. I use 1/8" pivots and stop pins, thus I drill with a 1/8" bit. Simple. Do not drill the detent right now.
A good bit makes a great difference! My favorite is the Norseman Cobalt bits from USAknifemaker.com. This step sounds really easy, but I had some of the most trouble with this. Drilling a perfectly placed perpendicular (say that three times fast!) holes were difficult for me. Like I said, a drill press would be your best bet.
Also, when drilling for the handles, it helps to make the titanium piece first, and then use that as a template for the handle scales. When you do that, drill a hole and stick a pin through it to help align everything. Then drill the next hole, and then put in another pin.
Step 6: File the Bevels
Basically, file out the edge. You will file at a slant, so that the knife shape is there. I use drawfiling. With the handle in the right hand, push the file towards the base, or tip of the blade. This way it ensures a perfectly flat grind. Then flip the blade over, and do the same.
A trick to find the center of your blade: Color the edge of the knife with a sharpie, and then take a drill bit the same diameter as the thickness of your metal. Scratch a line into the edge by putting the blade and the drill bit on a flat surface, and drawing the blade towards you, against the drill bit. This way, the drill bit will mark a line right down the center of your knife. To double check, flip the blade over, and do the same thing. There should only be one line, but if there are two, this means that there's a small difference between the size of the bit and the blade thickness. This is okay, just know the center is directly between these two lines.
File the blade, and leave around 1/16" of thickness on the edge of your knife. Hint: This is around the thickness of a dime.
Step 7: Fitting the Stop Pin
Now you should have the handles, roughly shaped (or finished, it doesn't really matter), with at least two holes, the stop pin hole, and the pivot hole. The blade should be done, except for extra metal behind the two stop pin contact points, and behind where the lock would touch the knife. Other than that, the blade should be looking good.
It's time for fitting. For these next steps, please take your time. Being too rushed would ruin the knife at this point. Essentially, what's going to happen is trial and error. I usually have a certain pattern depending on how much steel I need to remove. File 5 times, check. File 5 more times, check.
Using a hacksaw, cut out the pivot and the stop pins. You want the length to be equal to the thickness of your overall knife, plus at least 1/4". I usually leave around 1/2", just so it is easier to take the pins out. The fit will be very tight at this point. You can push it in with an extra piece of metal, or use pliers. It doesn't really matter how the pins get in. They'll be put in and taken out quite a bit during these next few steps.
Take the titanium liner, and push the two pins. Push the blade in on top of the pivot pin. Now, try to open and close the blade. It's probably not perfect, and in fact, the arc may be prevented due to extra material on the blade. There will be 3 places to file. The top area raises the blade when the knife is opened. The bottom stop pin area will cause the blade to sit deeper in the handle when closed. The last area is in between these two stop pins. If the blade cannot swing open and close, material needs to be removed from the middle in order to allow the blade to swing. Remember to keep the lock area flat.
Sorry for the bad explanations, I'm going to let the pictures finish. I'm going to reference the pictures from here because I think it's easier.
Picture 1(Open blade): Point A is where the stop pin meets the blade. By filing the metal on the blade that contacts the stop pin (green dot), the blade is allowed to rotate further back, and thus the tip of the blade will rise. When you file this one, try to line up the knife as you designed it. A straight spine helps with alignment, but is not necessary in the design.
The orange line represents the parts of the blade that will contact the stop pin when the blade is closing. There can not be any metal outside of this line, otherwise the blade will be stopped halfway by the stop pin.
The light green verticle line is your lock. When removing metal, this line must be kept straight for your lock.
Picture 2: This is the blade closed. Note the backspacer on the right side, with the two holes. The point labeled B is where the blade contacts the stop pin. This will prevent the blade from closing too far. When adjusting this bit, make sure that the blade will not touch the backspacer, nor stick out of the handle.
Because of the relatively small radius of the pivot to stop pin compared to the pivot to tip of the blade, a small change can make a big difference! Remember that metal can be removed, but not put back on. File slowly!
Step 8: Cut Out the Lock!
Sounds simple huh? Essentially, you need to cut an L shape in the titanium. How you do it is up to you. You can drill a hole, and use a jeweler's saw, or use a cut off disk, or a band saw. In my case, I had to use a hacksaw. In order to give the hacksaw blade space to fit, I drilled a series of holes right next to each other, and then opened it up with a file. That gave me the clearance for the hacksaw blade.
Before you start, put the knife together, and open the blade. Mark where the blade tang is. You want to cut the lockbar out with around 1mm overlap with the blade. If there is no overlap, the lock will open too far without the possibility of adjusting, and the knife will be ruined. Don't forget to account for the thickness of the saw!
Start by cutting out the long line, parallel with the open blade. Then cut perpendicular to the open blade.
Now, with your lock bar released, bend the lock bar out by securing the back of the liner, and pushing the lock down. You want to bend it so that if the knife were assembled, the lock is being pushed towards the center. You usually have to push to around 5 inches, but start small. Push it out 1 inch, then 2, and so on. You know the lock has been bent enough when it rests a bit further out than the thickness of the blade.
Also, file the lock bar, and try to match the angle of the blade tang. (8 degrees). It's not necessary, since the lock bar will wear in and match the angle eventually, but having it pre-matched can save the lock bar from wearing in and losing life. In other words, by doing so, you can extend the life of the knife.
Step 9: Optional: Harden the Lock Bar?
This is superstition, and I'm not 100% sure it works. However, I do it anyways, just in case there's a benefit. Basically, I compact the lock, and then "heat treat" it.
This idea came because on one of my knives, I tested the lock by smacking the blade with a hammer. The knife held, but to my surprise, the lock bar had compacted, and thus wore so quickly the blade developed lock rock (where the blade can move a little bit when it's locked.)
Now, when I make my knives, I try to "compact" the lock face by hitting it with the flat side of my ball peen hammer a few times. Nothing ridiculously hard, but just a few good smacks. Going too hard might flake the titanium.
Then, I take a match, and just heat up the face of the lock bar a few times. Again, I'm not sure if this works, but it's just a superstition thing.
Step 10: Fit the Lockbar
EDIPretty much the most critical step. Patience is the key. Don't lose everything because you want to save a few minutes. Do it slow.
Now, a liner lock knife needs space to adjust. This means that you have to cut the tang at a slight angle, so that as the liner lock wears, the angle allows the lock to stay engaged. It's hard to explain, but check out the first picture. Or ask me in the comments.
You want the angle of the tang to be around 8 degrees. Too much, and the lock will slip when any force is applied. Too little, and the blade will not have as much room to adjust.
This is why it is so important to have the lock area be flat. Now, all you want to do is just file the tang down until the lock bar fits. Also, to help prevent lock rock, only the last 0.125" of the lock should contact the blade. This means the lock needs to be filed at a slight angle, so the bottom of the lock contacts the blade. By bottom, I mean the area closes to where your fingers would touch. Otherwise, if only the middle portion touches, than lock rock can develop. As the blade wears in, more of the liner lock will contact.
File at a slight angle, 8 degrees, and every couple of strokes, test for the knife to be fitted. It's fitted when the lock can engage the blade and keep it open. I usually aim for at least half of the titanium contacting the blade.
EDIT: thinkpadt30 has brought to my attention that the first picture is too dark. Since it's hard to get a picture of the lock up, I drew one up on inkscape, which should help.
Step 11: Fitting the Detent
I had more trouble with this than I should. The detent is a small ball that keeps the blade closed. The detent rides on the lockbar, and when the blade is opened, is pushed out to the side. Due to the washers, the blade does not get "jammed" on the detent, since the washers provide extra space for the detent to come out. When the blade is closed, the detent, and the liner lock, moves inwards a bit, and the detent ball falls in a depression in the blade, thus keeping the knife closed.
First, determine where the detent ball should go. From the pictures, you can see that the most typical area for the detent ball is at the top left of the lock. However, other places will work as well, and in fact, Emerson knives drills out a separate lock for their detent ball.
Take a small bit, which is just a hair smaller than the detent ball, and drill your hole in the liner lock. If you use a 1/16" detent ball, a #53 drill bit is perfect. Once that's done, take the ball, place it in the hole, then take the phosphor washer, and place it so that the ball is in the center of the washer. Now, take a clamp, or a hammer, and gently press the ball in. Due to the slight size difference, the ball is now press fitted into the liner lock.
The reason for the phosphor bronze washer is simple: Since a liner lock has handles on both sides, the lock cannot move out, or away from the center of the blade. If the detent ball were higher than the washer, than there would be no space for the blade to open, and the lock to move away. Thus, the detent ball can only be as tall as the phosphor washer.
Step 12: Making the Detent Hole
Now, assemble the knife, with the washers. Coat the inside of the blade with a white board marker first. This will allow you to figure out where to drill the detent depression on the blade. Open the blade a few times. The detent ball will push aside the expo marker, and create a little track where it goes.
Now, you want to drill the depression just a bit in front of the end of the detent's track. You want to drill the hole so that the ball is just barely in the hole, so that it tries to move more in the hole, and thus, will keep the blade pushing against the stop pin. If the hole is drilled so that the entire ball sits in the hole, there's going to be a little wiggle in the blade because the ball isn't pressing. So you want to drill the hole so that the slope of the ball is contacting the hole, and exerting pressure to keep the knife closed.
The depression hole doesn't need to be drilled too much, just at least as deep as the height of the ball.
Step 13: Finish Up!
This is just a bunch of little things to finish the knife.
First, heat treat the blade. I usually do the 1084 by myself (other instructable), but for the more complicated heat treats, I send it off to Texas Knifemaker to heat treat it. Right now, I have 2 blades there.
Cut out and shape the scales. They should be the same shape as your titanium piece. Drill the holes (with pins to help alignment), shape it nicely, and polish it up!
Then, make the backspacer. This is just a little piece of material the same thickness as your blade+2 washers. It's purpose is just to be a pillar in the butt of the knife, and make sure the handles don't collapse. Drill holes to align it with the scales, and make sure you file it enough so there is a clearance for the blade when the knife is closed.
Using a ball peen hammer, smush all the pins in. Check out the other instructable if you need help.
Lastly, find a sharpening stone and sharpen the knife. It takes a while with hardened steel, but it is the last step!
Step 14: Enjoy!!!
Thanks for reading this instructable, and enjoy your new knife! I know not a lot of people will go through with such a project due to the amount of time it takes. For me, I make knives as a hobby, and it takes me around 30 hours per knife. I find it rewarding, but each to his own. Either way, I hope to start publishing more instructables, all to do with knives, since I'm a knut (Knife+Nut). Probably going to come out with a stonewashing one soon!
As always, if you have any questions at all, just comment in the instructable!
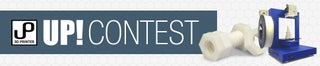
Participated in the
UP! Contest