Introduction: I Love Papercrete
Papercrete?? What’s that??
That’s the response I always get when I’m describing my favorite building material. Not surprising since it occupies a spot in that backwater known as ‘alternative building materials’. Papercrete is just what it sounds like actually. It’s concrete made with paper. I tell people to think of it as industrial paper mache. It’s inexpensive to make, amazingly sturdy, lightweight and insulating.
I didn't invent it but I have played with it quite a bit over the past several years. In this Instructable I'm going to go over a little of the history behind it, exactly what it is and how to make and use it. By the time we're done you'll love it too!
Step 1: A Brief History of Papercrete
Papercrete was originally patented in the 20's. The patent lapsed because it was too easy to make on your own and the patent holder wasn't able to make any money off it. It really came into it's own as a building material in the 80's. Eric Patterson and Mike McCain are widely credited with independently inventing (rediscovering) it and actively developing techniques and machinery for working with it.
I discovered papercrete in the late nineties. I used to own a magazine distribution company that specialized in small press and unusual magazines. One of the titles we carried had an article about people who were recycling newspapers and building with papercrete down in southern New Mexico. It was a total off the grid hippie dome sort of scene. The domes weren't my thing but I was captivated by the material and the process of making it. I saved a copy of that magazine and told everyone I knew about it.
It was especially appealing to me because of all the waste involved in magazine distribution. All the unsold magazines would be returned to me and I would have to pay to have them hauled away for recycling. Turning them into building blocks would have been a perfect solution. Unfortunately at the time I didn't have a place to experiment with building projects so eventually the papercrete article went into storage and the idea went on the back burner.
My biggest obstacle was the mixer. To make papercrete you have to be able to grind up paper… lots of paper. In order to do so you need a mixer capable of shredding paper. A regular cement mixer won’t shred the paper it will just stir it around. Luckily for me, Mike McCain had already invented an ingenious papercrete mixer that you tow behind a truck. You just throw everything in and drive slowly for about a mile. When you’re done you have papercrete slurry ready to be cast into something.
Step 2: So....What Is This Stuff Anyways???
Well, like I said in the intro papercrete is basically concrete made with paper. The process consists of adding a certain ratio of paper and / or cardboard to water and then adding portland cement. The mixture is then stirred with a blade to re-pulp the paper and mix everything together. When it is properly mixed it becomes a slurry that has the consistency of lumpy oatmeal. This slurry can be poured into forms and cast into shapes such as blocks or beams or dome sections. You use the same stuff as a mortar to glue the blocks together. It can also be used as a plaster to make a smooth finish coat on the inside and outside of a structure.
Papercrete has an R value of 2 per inch so a 12" wall has an R value of 24. Not bad..
It’s sturdy but lightweight- A block only weighs a few pounds but can hold up a car!
It’s weatherproof- I’ve had blocks out in the elements for 4 years and they haven’t changed at all. It does absorb water like a sponge so if they are going to be used for walls they need to be protected from moisture. Similar to wood they will decompose if buried underground so they need to be up on a raised foundation.
It’s a really easy material to make- As long as you stick to the rough proportions of water, paper and cement you’ll end up with a usable product. I can make 45 blocks by myself in two hours.
It's easy to work with- You can use regular woodworking tools to cut or drill holes in papercrete blocks.
It’s green- Totally overused term these days, I know, but I use all of our paper trash for the year and then quite a bit more. It’s fun to go to the recycling center and see their faces when I ask for paper rather than dropping it off. Now we even grind up all of our plastic trash in a paper shredder and mix it right in! Making papercrete turns nearly all of our household trash into building materials.
It’s cheap- It costs about a quarter to make a 8″ x 12″ x 5″ high block.
Are you sold? Itching to start making blocks? First, we have to make that mixer...
Step 3: Papercrete Mixer
The McCain mixer is sheer genius in its backyard engineering brilliance and simplicity. It consists of a trailer made from a truck rear axle with a stock tank mounted on it. The axle is rotated up 90 degrees so that the end where the drive-shaft would normally attach is sticking up through the bottom of the tank. A lawn mower blade is mounted on the differential stub so that as the trailer is towed it turns the lawnmower blade creating a giant blender.
I built my own McCain mixer a few years ago and it’s worked really well for me. I’m going to go over my build here knowing full well that it would take an intrepid soul to actually go ahead and build one of these but hey, maybe you'll get inspired. (I lost my !@%$&# photos from building my mixer so we’re going freehand from here people!)
First I gathered up my materials which included:
A four foot diameter metal stock tank
A full sheet of 3/4″ plywood
Metal beams
The rear end from a Land Rover (I think I have the classiest trailer in town)
A trailer hitch
The rubber inner tube from a large truck tire
A couple hinges
A lawnmower blade
A small can of bondo
A tube of silicone and liquid nails
Assorted nuts and bolts and some wood screws
The first step was to assemble the trailer. I needed a contraption that could securely carry several hundred gallons of water. I used galvanized I-beams that were way heavier duty than I needed to build the trailer with, but hey, they were pretty cheap at the scrap yard and about the length I needed already. I welded them together along with the rear end from a Land Rover to create the framework. Once I welded on a trailer hitch from Pep Boys I had a trailer. You can get the idea from the first illustration.
Next, I cut the plywood sheet in half and glued and screwed the two halves together to make an inch and a half thick platform to hold the stock tank. I cut a hole in it where the end of the differential would stick through. I cut the plywood to fit snugly around the differential so that it would be relatively easy to seal later. After that, I cut a hole in the stock tank as well so that it sat on top of the platform and fit over the differential too. Once everything was aligned I drilled through the tank, plywood and trailer rails and bolted everything together.
In order to get the papercrete out of the mixer I needed a drain. I took the tank off and cut a hole that was the circumference of the truck inner tube. I cut a third of the inner tube off and slid it through the hole in the plywood and secured it with a couple screws. It looks like an elephant’s trunk sticking out of the bottom! I cut a matching hole in the stock tank but made the hole an inch smaller so that I could cut tabs and bend them down to secure the tank over the drain. I bolted everything together and sealed the joint between the differential and the tank with bondo. I also made a flap under the trailer to hold the drain shut. All that remained was to attach the lawnmower blade to the differential and I had a mixer.
How long did it take?
I took my time acquiring parts over a few months and then once I got started building it took me the better part of a couple of weekends to construct it.
How much did it cost?
I scrounged as much as I could. I got the rear end from a mechanic that I knew. I bought the metal for the trailer from the scrap yard so it only cost about $35. The trailer hitch was another $20 and the stock tank was about $175. Maybe another $20 for bondo, bolts, glue and silicone. So a total of about $250.
What you do different next time?
I would re-design the drain so it was easier to use and make it larger to let the mix out better. I also need to put a couple of chains on by the hitch in case something bad ever happens and the trailer comes off.
OK , that's cool and all but I want to try making a few blocks before I commit to making a contraption like that.
No problem. just use a plaster mixer on a heavy duty(1/2") drill in a 5 gallon bucket for a test run.
Next up we’ll go over actually making a batch of papercrete and casting it into blocks.
Step 4: Making Papercrete Blocks
Making blocks is super easy. After mixing up a batch you just cast it into forms.
Tools
Papercrete mixer
Block molds- mine are made from 2x6's and scrap siding
Bathroom scale- for measuring out the paper
Shovel
Materials
Water
Paper (used of course)
Shredded plastic (if you want)
95 lb bag of cement (cement not concrete- no rocks or sand in the mix)
Process
1. Set out your molds. You will need enough flat space to drive over them and pull your truck and the mixer in all the way in front of the molds.
2. Fill the mixer 3/4 full with water. I just eyeball it.
3. Put in the paper/plastic. I use about 75 lbs.
4. Add the bag of cement. You don’t need to open it, just toss it in.
5. Cover the mixer securely. This is very important. Just think of what happens when you have a blender top malfunction and multiply it by 100… I use a canvas tarp with a cargo strap.
6. Drive slowly- 5-10 mph for one mile. The mixer will chop up the paper into a pulp and mix it with the water and cement.
7. Empty the slurry into the molds. If you got the mix right you should be able to open the drain, fill some blocks, close it, pull forwards a bit, repeat. If the papercrete is too thick you've got some shoveling to do. The type of material you are using can make a difference too. Cardboard makes for a thicker, chunkier mix where newspaper is finer and smoother. Sometimes I use a plunger to force it through too. A lot of poop jokes get made here. Let your imagination run wild. I get about 45 blocks per batch.
8. Remove the molds. I do this right away. I want as much air flow around the blocks as possible to help them dry.
9. Wait a few days for the blocks to dry.
10. Stack the blocks under cover to dry further. I like to wait a couple weeks before using them.
11. Do it again and again until you have several pallets stacked with bricks and your year’s supply of paper trash is gone. That’s 10-15 batches for me.
Once you have a big stack of blocks It's time to build something. I've been putting up little buildings all around our place. Let's take a look at a yurt I built out of papercrete blocks.
Step 5: Building Time!
Finally!! You built the mixer, saved the paper and made the blocks. Now it's the fun time- putting them together to actually make something. My first papercrete project was a permanent yurt. We had purchased a yurt years before and after going through three outer covers in five years it was clear that our climate was just too harsh for a ‘permanent tent’. At the same time, the yurt was so cool that we really didn't want to give it up. What we needed was a weatherproof exterior that would not need to be replaced….ever. The only way to do that (in my twisted mind) was to build a real building and put the yurt inside of it. Then we would have something that would last with all the yurt goodness inside of it. What better material to build a backyard folly with than papercrete?
The first step was digging a trench and casting a foundation for the building. I used a metal stake and a piece of string as a giant compass to scribe a building sized circle in the dirt. After shortening the string to match the inside of the building I drew a second circle. Now I knew exactly where I needed to dig. The foundation was one foot wide and six inches deep. It was filled with (real) concrete and had rebar reinforcing inside of it. I also cast a small front entry stoop at the same time. The foundation didn't need to be too heavy duty since the papercrete is so lightweight.
The door frame from the yurt was attached to the stoop and a ring of cinderblocks were put down as the first course on top of the foundation. The exterior of this initial ring was coated in roofing tar to waterproof it. It will act as a water barrier and keep moisture from wicking up into the papercrete blocks.
Next it was just a matter of stacking and mortaring the blocks together. It was a lot of labor but went pretty fast. I was able to complete the wall ring by myself in just a couple days. I also used the papercrete to start to plaster the inside of the walls. After the walls were up I made a double layered ring of plywood that went all the way around the top. This ring is called a bond beam and it ties all the blocks together at the top so that the weight and pressure of the roof doesn't spread the walls apart. It's screwed into the walls with 6" long screws.
Life intervened and it was two more years before I got back to working on the yurt. It would have been longer but my sister, sick of sleeping on the couch when she visited, started instigating for more yurt progress. I told her “Fine, we’ll work on it next time you’re here.” thinking that would be the end of that. Well, she promptly came out and it was yurt building time again.
Part of the reason I had been procrastinating on the project was that I wasn’t really sure how to build the roof. It needed to be self supporting and not have any columns holding it up because the original yurt structure needs to fit inside of it.. It also needed to be very sturdy. We've gotten three feet of snow in a single storm and the roof needs to be able to handle that as well as our 50-60 mph spring winds.
We started by making a central ring out of a couple layers of plywood that all the rafters would connect to. The ring was about 5 feet in diameter with a large hole in the center for a skylight. Next, we needed some way to hold this ring in the right place to attach the rafters to it. We erected some scaffolding and spent quite a bit of time getting the placement of the ring correct. It needed to be at just the right height and exactly in the center of the building. Oh, and level too. Eventually things got worked out and the yurt is finally weatherproof. It still needs to be finished out but it's coming along.
Step 6: Wrap Up
So there you have it. All the joy and wonder that is papercrete. While it's probably not going to ever make it as a mainstream product, it's perfect as an inexpensive alternative for someone who has more time than money to spend on smaller projects.
It really lends itself to piecemeal progress. Save all your paper trash throughout the year. In the summer make some batches of blocks in the evening after work and soon you have enough inventory to build something. Start a building. Add another room next year. So on and so forth.
Don't limit yourself to buildings either. I use it all the time for raised garden beds. Papercrete can be cast into any form you can imagine too. You could use it to make planters, outdoor benches, sculpture or anything else. Just get your hands dirty with it and I guarantee, a love affair will be born.
Interested in what we're up to lately? Updates happen pretty frequently on Instagram and YouTube.
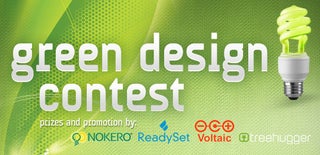
Second Prize in the
Instructables Green Design Contest