Introduction: Improve an Inexpensive Scroll Saw - Add Knobs!
This instructable will show you how to improve an inexpensive scroll saw. This type of scroll saw typically accepts blades with pins, but comes with adapters for pinless blades, which are more commonly used. Specifically, I obtained this scroll saw from harbor freight tools, which I think is a great place for hobby tools.
Although you can purchase knobs, they are typically very expensive. For me, a #10-32 screw costs $0.09 versus a knob which costs $2.80 which I found at a local Ace Hardware store. I will show you how I made my own knobs for less.
Step 1: Original Adapter
For reference, this is the original adapter. To use pinless blades, the blade must be inserted between two adapters and tightened with a hex-wrench. When there is no tension on the blade, it does not stay on the scroll saw body and falls off, since tension holds the adapter to the scroll saw.
Step 2: Drill and Mark
Find and drill a piece of wood. The holes should be far enough apart, to prevent the knobs that will be created from interfering with one another. A drill press should be used to make a straight hole. A compass should be used to draw circles around the drilled holes for the knobs.
Step 3: Wax and Level
In this step, wax the wood. I used a candle and applied it quickly to create friction. Level it using a razor blade; this will fill in and even the surface. Most importantly, it will prevent the epoxy used to make the knobs from sticking.
Step 4: Measure, Clean, and Ready
The depth of the screws should be measured so that they extend out of the wood, and so that there is a small gap between the head and the wood. This will allow the epoxy to completely surround the head. Dept is indicated by how far the screw extends out of the wood. Lastly, the screws should be cleaned with acetone and pulled out somewhat to allow for the epoxy to be put underneath the head.
Step 5: Form Knobs
In this step, form the knobs using epoxy putty. You can use any type of epoxy putty you'd like. Although I purchased some J-B Weld brand epoxy, I actually ended up using some very old Oatley brand epoxy. The most important thing is to consider the mixing time and cure time. In my case, this was one minute and three minutes.
Once the epoxy is mixed, take two halves and shove it underneath the screw head. Next, screw the head in deeper and cover the head with epoxy. Using a razor blade, form a square and use the arcs of the circle that was drawn as guides for the square. Allow an appropriate amount of time for the epoxy to cure.
Note: Epoxy uses BPA so you may want to wear gloves and coat the finished knobs in paste wax when done.
Step 6: Sand Knobs
You'll need to sand the bottom of the knobs so that they form a level surface to accept the blade. To do so, twist out the knobs (once cured) barely exposing the ends of the encapsulated screws. Sand this by placing sand paper onto a level surface and moving back and forth. Once done, the knobs are ready for use.
Step 7: Repeat With Hex Screws
There isn't much point in putting a knob on either side, to reuse the screws that are provided. Sand the ends like before to create a level surface.
Step 8: Cut Rubber and Assemble
In this step, cut some rubber squares. This will prevent the adapter from falling off the scroll saw without any tension on the blade. Use a knob and hex screw for each adapter. Altogether, this will allow for easier blade removal and should make sawing inside wood or plastic much easier.
Step 9: Side Port
For some reason, the side port uses regular philips screws rather than knobs. For easier access to change the blade and to clean, the other two knobs are used. One of the holes was not completely taped, so I had to finish it.
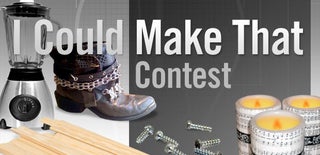
Participated in the
I Could Make That Contest
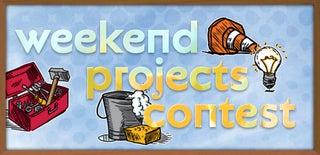
Participated in the
Weekend Projects Contest