Introduction: Homemade Go Kart
Me and a friend got tired of being bored and we don't have money to go out so we decided to build a go kart from scratch using materials we found around the shop. We custom built every single part on this go kart, from the steering to the brakes. This project took 3 days and at a total cost of $0.
Step 1: Materials
What you will need:
Square/Round tubing for frame and support
Seat
Steering wheel
Flat stock
Round rod
Assorted bolts
Step 2: The Frame
We built the frame out of 1" square tubing that has been sitting next to the house for years. We started by researching racing kart frames and came up with a design.
Step 3: The Spindles
To build the spindles you take a piece of 1" flat stock that is 7" long and bend it so you have 2"-3"-2" U shape. Make two of these. Once they are bent, drill a hole the size of the bolt you are using in the top and bottom. Now cut a piece of round tube that is a little bit smaller than the inside height of the spindle. This piece needs to be a snug fit to the bolt your using so the tube will turn freely around the bolt but not so tight that its difficult to rotate. Now for the part that actually rotates, I used 1/2" square tube to make this part. Weld a bolt that is long enough and wide enough to go on the wheels you are using onto the piece of tube that the bolt goes through. At a 90 degree angle to this piece weld another piece of tube that the steering components will attach to.
Step 4: Steering Shaft
The steering shaft is a piece of 1/2" hollow round tube. The length is determined by where you want the steering wheel. we made our shaft about 18" long which is perfect for use cause were both skinny. You will need two industrial washers to hold the shaft in place so the wheels will actually turn instead of the shaft.
Step 5: Steering
We made the steering components out of a solid piece of round stock. We welded the round stock to some tie rod ends and then to a industrial washer. The tie rod end is bolted to a bolt that we welded to the square stock on the spindle. Now you need to make a steering knuckle that the steering shaft welds to. We took a 4" section of 1" square tube and welded two big bolts to opposite sides of the tube and those bolts sit inside the washers that are welded onto the round stock.
Step 6: Front Wheels
We used wheels from old mini bikes for the front and back. Its as simple as sliding the wheel on and bolting it down.
Step 7: Rear Wheels
The axle for the rear wheels is made from the axles from the mini bikes we had. We measured the distance we needed for the wheels and sprockets to clear and cut them. Weld the axle onto the side of the frame.
Step 8: Engine
We used an old 3HP tiller engine to mount on our homemade go kart. We used the original engine mount and welded it to the frame.
Step 9: The Seat and Controls
We used an old seat we found on the side of the house. We cut the legs off and welded it to the frame. We used the brakes from the mini bikes and made a hand brake on the side. For the gas pedal we used the brake lever from one of the mini bikes and welded a support on the front bumper. The brakes are operated by another brake lever from one of the mini bikes and we welded it to a support bar on the side by the seat.
Step 10: Final Product
After building this go kart there are some things that I would have different if I had the material. I would have made the rear axle solid all the way across so it would be stronger. I would have designed the pedal location better, we didn't think about pedals when doing the steering components. Future upgrades include a bigger engine with a clutch and maybe a transmission so we can shift it. I turned out pretty good for being hand built from whatever we could find. We tested it by jumping on it and dropping it and it seems pretty strong. After everything was completed I painted it all black.
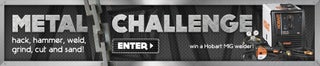
Participated in the
Metal Challenge
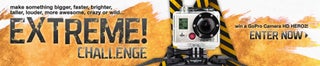
Participated in the
EXTREME! Challenge