Introduction: Leather Flask
Show ye olde style, while saving the earth by stopping the use of disposable waterbottles. Carry, the flask...
The flask is quite the fashion piece these days, just wait, soon ye'll see ye olde Lady Gaga wearing it... And nothing else... >barf<
Anyway, it's quite cool, and gets a lot of comments wherever you take it. So, jump on the train and make one yourself. This flask holds 3 cups of water (*or, 663 ml, or 23.4 fl oz) or if you prefer it can hold 23.4 fl oz of whiskey...
P.S. A note I forgot to add earlier. At first, the water stored in it for long amounts of time may get a leatherish/beeswax flavor to it. It isn't too bad, and it diminishes with use. When I make one I like to fill with water, let it set for several hours, and empty then repeat. this repeated for a few days will diminish much of the flavor. (I personally kind of like it, but some people don't).
Step 1: Tools and Supplies
Tools
- Sharp knife
- contact cement
- marking tool (I use a fine tip sharpie)
- two sewing needles
- overstiching wheel (for marking sewing points)
- edge beveler
- drill or drill press with small bit (I use 3/32" but one size smaller might be better)
- Optional - leather tooling tools (make it look cool!)
-
pattern
Supplies
- Heavy Veg Tanned leather (I believe mine was 10-11 oz)
- False sinew
- beeswax
- paracord (I use it for a shoulder strap)
- a wine cork
- lentils (or small beans, or something like that, you just need something to hold the shape for it)
Step 2: Trace and Cut
Take your pattern (my dad helped me lay mine out in auutocad, and I printed it then glued it to a piece of cardboard which I cut to shape). Trace it onto the rough side of the leather, and cut it out. Then take the ONE cutout, lay it smooth side up on the rough side of leather, and trace it. This way even if you cut it wrong, the second side will fit.
Image notes still aren't working, so I'll add important things down here.
Pic 2 - you can see a scratched out line, that was from a tracing I decided not to use
pic 3 - thats a pic of a hole in the leather that made me decide not to use the first tracing
Pic 10 - thats the design I use. You can copy it and size it how you want.
Step 3: Tooling
This is instructable isn't about leather tooling (different one) so I'm not showing how I do it on this one. Decide what you want, and tool it, but do it deeply, the leather will be stretched later, and it could wash out light tooling.
I decided to go for a celtic knot on the front, and I stamped my logo on the back (sorry, I forgot to get a pic of the logo after stamping it)
Pic 1 - partially tooled celtic knot
pic 2 - the finished knot
pic 3 - larger pic of the finished knot
Step 4: Mark the Cork Area
this is important, you want the cork to fit nicely, so you need to do it right. Mark where you want to sew up to around the cork with this method. Take a strip of leather, wrap it around the cork, mark where it meets itself, and mark the middle of that distance. This way you have half the circumference of the cork. this is the distance you want it on your flask. Go ahead and also mark out the area you'll leave flat as well.
Step 5: Glue
take your contact cement, and glue a 1/4" around the outside, as well as the areas at the top you want to remain flat. Let them sit (apart) till the glue is nbearly dry to the touch. CAREFULLY stick them together, this stuff is tenacious, so be careful until it's in the right place. go ahead and take your mallet and tap the areas that got glued, you want them to stick together nicely.
After the glue is dry go ahead and use the overstiching wheel and mark the line around the flask to be sewn. Make sure to get the outside of the areas you want flat also. (sorry, forgot to get pics of this, but you'll see some of the marks the wheel makes in the next step).
Step 6: Drill
Using the marks made by the overstiching wheel, drill a hole through each one. As you can see I clamp a board under the flask, that way the drill bit doesn't go into my drill press table. After the drilling is done, go ahead and chuck up a 80 grit flapwheel drum, use this to smooth out the edges and make them all even. Now, walk back to the house, realize you need to drill the big holes for the strap, and walk back to the barn. Go ahead and drill the large holes now.
Step 7: Sew
I'm using the saddle stich here. Basically I take a long length of the sinew, put a needle on both sides, insert it into the first hole, pull it till it's centered, then feed both needles through the next hole (both goin different directions). Then do that on the next hole. keep going till you his the end. Go here for better instructions (start at step 8) the stuff before that we've already done). Make sure when you do this to pull it TIGHT, you want this to last forever. Also, I like to slightly dampen the leather when sewing, that way the sinew gets pulled into the leather and doesn't show as much, just makes it look nicer.
When you’re done sewing go ahead and run an edge beveller along the edge on both sides (front and back). You can do it before sewing, but I just did it after.
Step 8: "poof" It
This is where you make it poofy. Now, I didn't get as many pics of this as I'd like, but oh well.
Soak the flask in warm water, you want it good and pliable. go ahead and make sure the cork fits (if it doesn't you can sand the cork down some to make it fit, mine fit perfectly now, but I had to sand it down some). Now, blow into it a little to poof it out some, and start filling it with the lentils or whatever you decided to use. Take a wooden spoon or dowel, and start pushing out the sides, and ramming down the lentils. You want to fit in as many as possible. When you can't ram in any more, and it's as poofy as you can get it, fill it up to the top, and push the cork in. Let it dry with the cork in it (so it forms around the cork perfectly) overnight.
Pic 10 - the spoons I use. One is a thin store bought wooden spoon, it's good for pushing out the sides with it. The second is a thicker spoon I tried to carve years ago, it's not a good spoon, but it rams the lentils really well.
Pic 11 - closeup of the thick spoon for ramming.
Step 9: Empty
After a night of drying make sure that the flask is an even light tan. It needs to be completly dry before you move on. When it's dry go ahead and take out the cork, and pour the lenitls out. Next take some small bolts, nuts, or the like. put them in and and cover the top and shake like the dickens. pour them and the unstuck lentils. Do this several times. Now you take a long piece of stiff wire (i use clotheshanger) bend at little curl at the end, and run it all around the inside of the flask. Take a flashlight and look inside it and try to spot any more stuck lentils. Repeat the steps until all stuck lentils are gone.
Last pic - lentils that came out after the first shaking.
Step 10: Wax
this is the most important, and the most difficult step. Your goal is to get molten beeswax to soak into the leather. If you have a large amount of clean beeswax (I'm talking around 5 pounds) and a large pot to melt in, then you can just dip the flask in and soak it for a little. Unfortunately I don't have that much wax or a big enogh container. So, what I do is melt a bunch of wax, dip the flask in it, turn it over, and dip the other side. The wax will just cover it in a thick coat, not soak in. So we need to convince it to soak in. preheat your oven to 170 (NO MORE! You'll cook your leather and turn it shrivily if you do). Take a board of wood, drill a hole and insert a peg around 3-4" long. Sit board on a cookie sheet, and cover with foil (if this is your moms cookie sheet and you don't want to die). Go back to the flask that has a thick coating of wax, scrape off most of it and just toss it into the thing of wax. Now sit it on the board (over the peg) and put it in the oven. After 30 minutes or so (check it every 5 minutes, I have ruined 2 out of 5 this way, you have to be very careful) the wax should be melting off and soaking in. Once all the wax is gone, you should have a nice sheen left on it. Take it out, shake it to make sure there isn't any more wax inside that needs to come out. and wipe the outside with a paper towel, really rub it good, it'll take away the sheen, but you want it to.
Whew, that was long, read over it and make sure you have it all down. Once the waxing is done, perform a water test. fill it with water and see if it leaks. Mine leaked quite well form the seam on the bottom, so I have to seal the seam. Go to step 11 for this. If it doesn't leak, skip step 11.
image note: the last photo is what happens if the leather gets too hot. Don't let it get too hot.
Step 11: Sealing the Seam
If it failed the leak test then you need to seal the seam better, to do this we melt a 1/4 cup or so of beeswax. Pour the beeswax into the flask, and turn it along the axis, that way the wax runs along the seam turn till it starts to pour out, then turn it the other way till it pours out. Dump out any remaining molten wax. It should have sealed it well by now. Fill with water and sit in a quite spot for several hours. If it leaks at all then repeat this step and test again.
Step 12: Strap
go ahead and put on the strap. I've seen it done several ways and with different materials. But I like black paracord, it looks nice, and you can do different things with it. To match the celtic knot I went ahead and took three long strands of paracord and did a basic braid. Then I threaded it through the first hole on the backside. then through the next hole. That way the knot is on the back. decide how long you want it, and then do the same on the other side at the length you want it.
The next and last step is to make a cool looking stopper. Continue on.
Step 13: The Stopper, Pt1
Now, I like to add something to my corks to make them look nice. Take a piece of cedar, use a draw knife to cut it down to a little bigger than the cork, and cut off a piece as long as you want. Take the wood and the cork, drill a hole partly into each, fill them with epoxy and inserting the pin first, clamp them together. Sometimes for added strength I'll take a smaller drill bit and drill little divots around the pin.Those will fill with epoxy and make little epoxy pins. Also, for oily woods, I like to wipe the wood down with acetone before epoxying.
Step 14: Shaping the Stopper
Well, theres not much to say here. Just follow the photos. Once it gets to the finishing stage, I hand sand the wood to 600 grit, and then I "whisker" it. Whiskering is a method I learned from Alan Longmire, basically, when you have finesanded the wood you dampen it in water and let it dry, this raises the grain, now you rub it with a fine steel wool. This removes the "whiskers" and gives it a fine finish. Next I rub in boiled linseed oil, let it cure and repeat twice, then I finish it by rubbing in thinned down polyurethane. I also like to add a small pull string through the hole I drilled earlier.
Step 15: Use and Care
Okay, I have only ever used mine for water, but if you were to use something else it should be fine as long as you wash it with warm water when you're done. It is NOT dishwasher safe, do not use it for hot drinks, the beeswax could start to soften and leak. If you leave it in a hot car in the 120 degree weather, it might soften, I'm not sure as it hasn't happened to me. If it does soften at all, be very careful not to mess it up, and fill it with some cool water to harden it again. That's about it, wash immedietly when using something other than water, as mold on the inside would be extremly difficult to remove. One last note, I have never gotten the stopper seal to be perfectly waterproof, when they were in use, they were either carried or hung, so it didn't matter. So, when you make or buy one, the stopper might leak slightly, that is expected. If it doesn't, then good job.
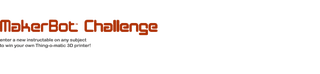
Second Prize in the
MakerBot Challenge