Introduction: Leg Vise (Threadless)
I've been getting by with an engineer's bench vise for years now, always watching the catalogs for a sale that will drop this wood vise to a reasonable price. I knew this was never going to happen so I kept looking for alternatives, and instructables delivered, like always.
The one that inspired me was by SlickSqueegie: https://www.instructables.com/id/Shop-mad-bench-vice/ The only obstacle I had was getting a acme threaded rod long enough to do the job. I searched for a while but couldn't get one without paying more than the price of a cheap wood vise (like this one). At some point on this search I had a moment of engineering clarity: I have one of those quick-grip bar clamps , why not use that instead of a screw... so I 'invented' a vise with a low pivot and place for the clamp.
Naturally I had not invented anything, the leg vise has been used at least since the 18th century, see the second picture above. This is a good thing because I could research different styles of leg vises and modify my design.
I've also created a 3D model of this vise, so if you'd like to see it all in more detail you can download it here.
Step 1: Plan / Design
I played with the plan in AutoCAD for a few days. At first I didn't have the slide (I don't know what it should be called, see the picture below to see what I'm talking about). The purpose for the slide is to keep the jaws parallel so that the whole face of the jaw holds the work piece, not just the top or bottom). It is adjustable to accommodate different work pieces.
I've included my dimension sheet in the second photo but this will vary depending on the size or your workbench.
Step 2: Materials, Measure, Mark, & Cut
Materials:
-- I already had the bar clamp, it's 36" which it too big really but it works, 18", or 24" would be more manageable.
-- All the wood I used was 2"x6" / 2"x8" cull lumber from a local hardware store (about 60cents a piece) (in case you don't know, when big box lumber/hardware stores get twisty or split lumber left over (and they get a lot) they cut it in half and sell it cheap).
-- I found the 3/4" galvanized iron pipe (for the pivot and slide pin) in the trash (painted brown for some reason)
-- To hold it all together I used wood screws.
I used the cut sheet (previous step) to cut everything out.
In the photo below I'm testing the fit of the back leg and jaw
Step 3: Slide Box
When the vise is in use there is not really any weight on the slide (it is distributed through the slide pin to the shelf) so this step could be ignored. I built it mainly because this vise was taking up a lot of storage room (my shed is only 12'x10') and the box allowed me to stack things behind the vise and still use it.
The sides of the box are slightly taller than the slide and is positioned directly behind the back legs. I had some plywood (3/4" I think) lying around so I used it as the box top.
Step 4: Slide
I used a scrap, screwed in place, as a spacer for the back of the slide
Step 5: Back Legs
I knocked the back legs into place and screwed them in place at the bottom then screwed the back jaw into the bench top and the top of the back legs (make sure you countersink any screws in the jaw face so that they don't bite into your work piece). The angle iron slot I cut in the back of the back legs was tight enough that I just banged it in afterwards.
Step 6: Front Leg
I then attached the angle iron to the front legs. I did this because the slots I'd cut were a little sloppy, and the front needed to be stiffer. I did this with a single screw in each side. At this point I put the pivot pin in and stared at it for a while, looking for problems. I found a couple but ignored them.
Step 7: Jaws
The front jaw was attached by a (countersunk) screw into each leg. You can see the major problem in the photo below: the jaws don't meet up. You would think that something must have gone wrong in the measuring or cutting process which is why I'm going to blame the drill. I think a drill press might have been more accurate and stopped this... but it isn't a problem because the vise still functions (see the second photo).
Step 8: Fix Front Jaw
I could sleep that night, not with jaws out of alignment, so the next morning I cut the fir from test #1 down to size and planed it to a better fit. The paler wood makes a nice contrast... let's say that I intended to do this.
Step 9: Finished
The final product, well, almost. I'm not totally happy with the back jaw since it doesn't have a square edge. I might fix that one day it works very well (for the cost). The other worry in my little shed was how far out the vise stuck when not in use. In the position shown in the first photo, with the slide and jaws pushed all the way in (in this position the bar clamp can be hung up out of the way) it takes up 5" which isn't too much.
Later I will also add a couple of bench dog holes (if I need them).
The second picture shows the vise with the slide in the max open position (the widest it can go and still keep the jaws parallel): 11 inches. Of course, if you need to go wider you could add some more holes to the slide (and make the slide longer if you needed).
Step 10: Mount for Bench Vise
Now that I won't be using it as often, I built a base for my bench vise to fit in my new leg vise. Now I have a wood vise that's at a nice height for planing, etc, and a metal vise that holds things a bit higher, perfect for cutting pipe and other metal things.
Thanks for reading.
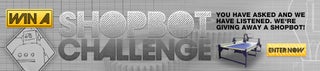
Participated in the
ShopBot Challenge